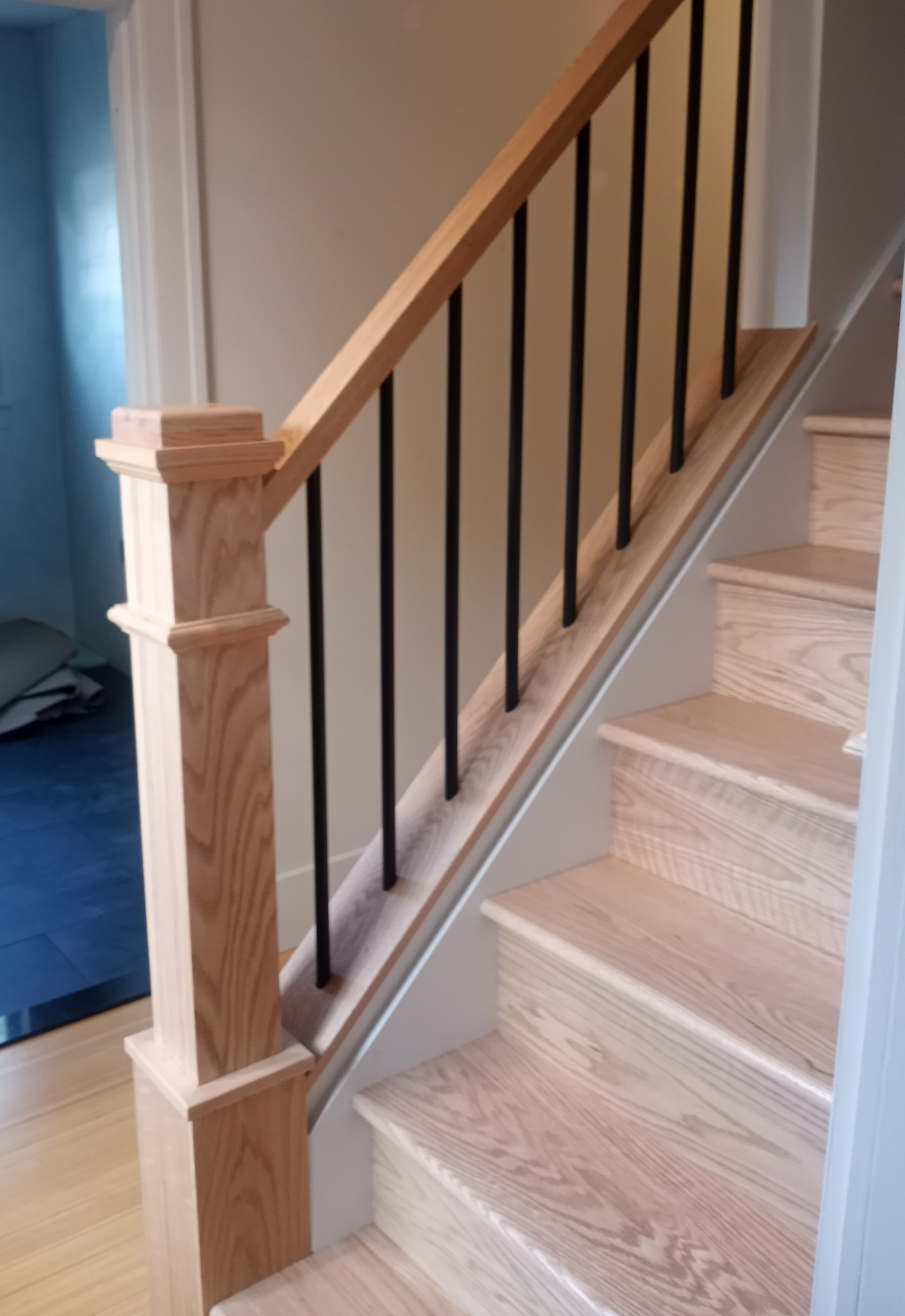
I recently had the opportunity to build a nice set of interior oak stairs for a customer. The design that the customer chose is simple and tasteful.
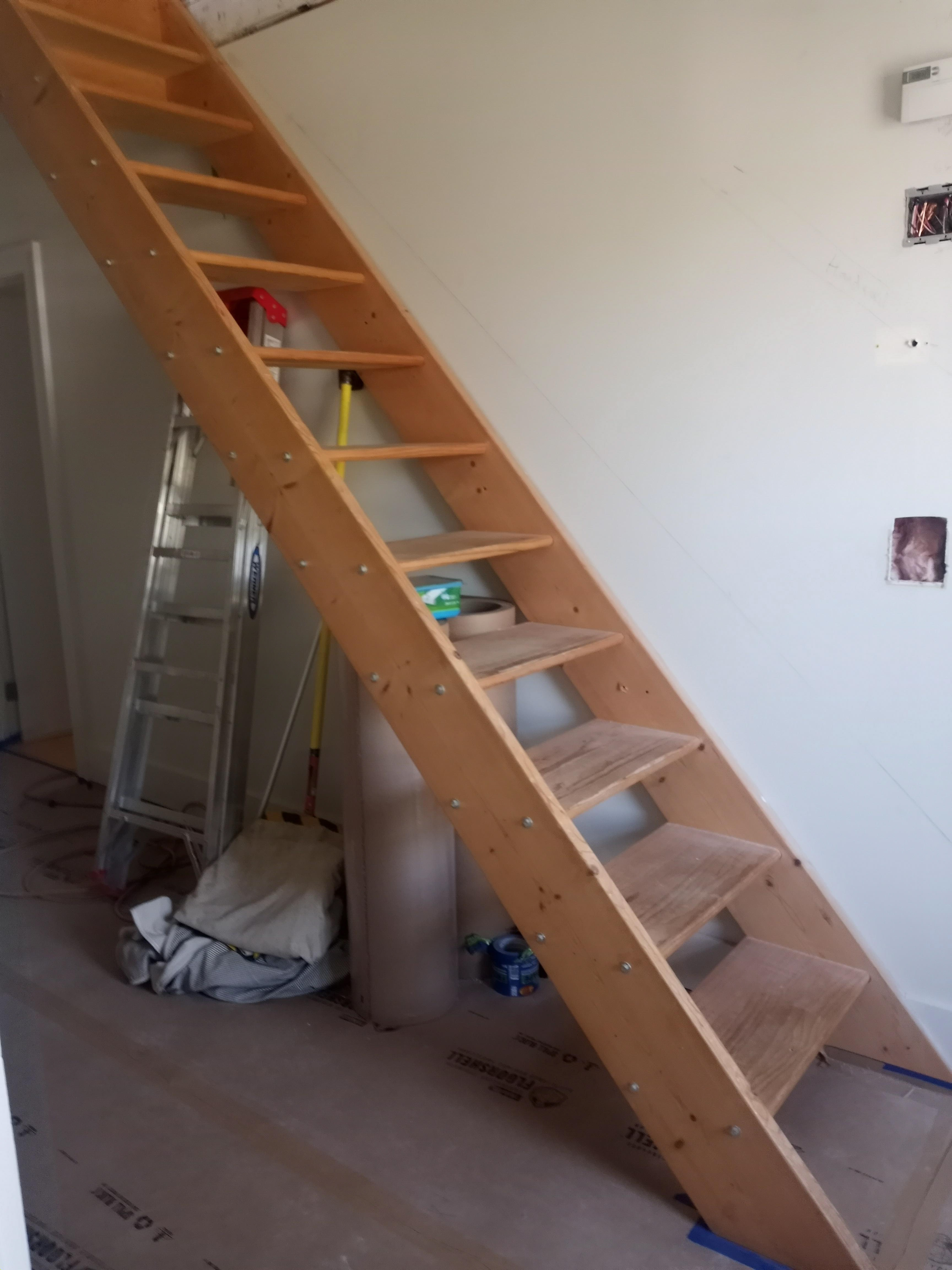
These are the existing stairs. The overall run is too short, the stair case isn't wide enough, there is no balustrade, no handrail and there are no risers. These stairs are unsuitable for the homeowners' growing family.
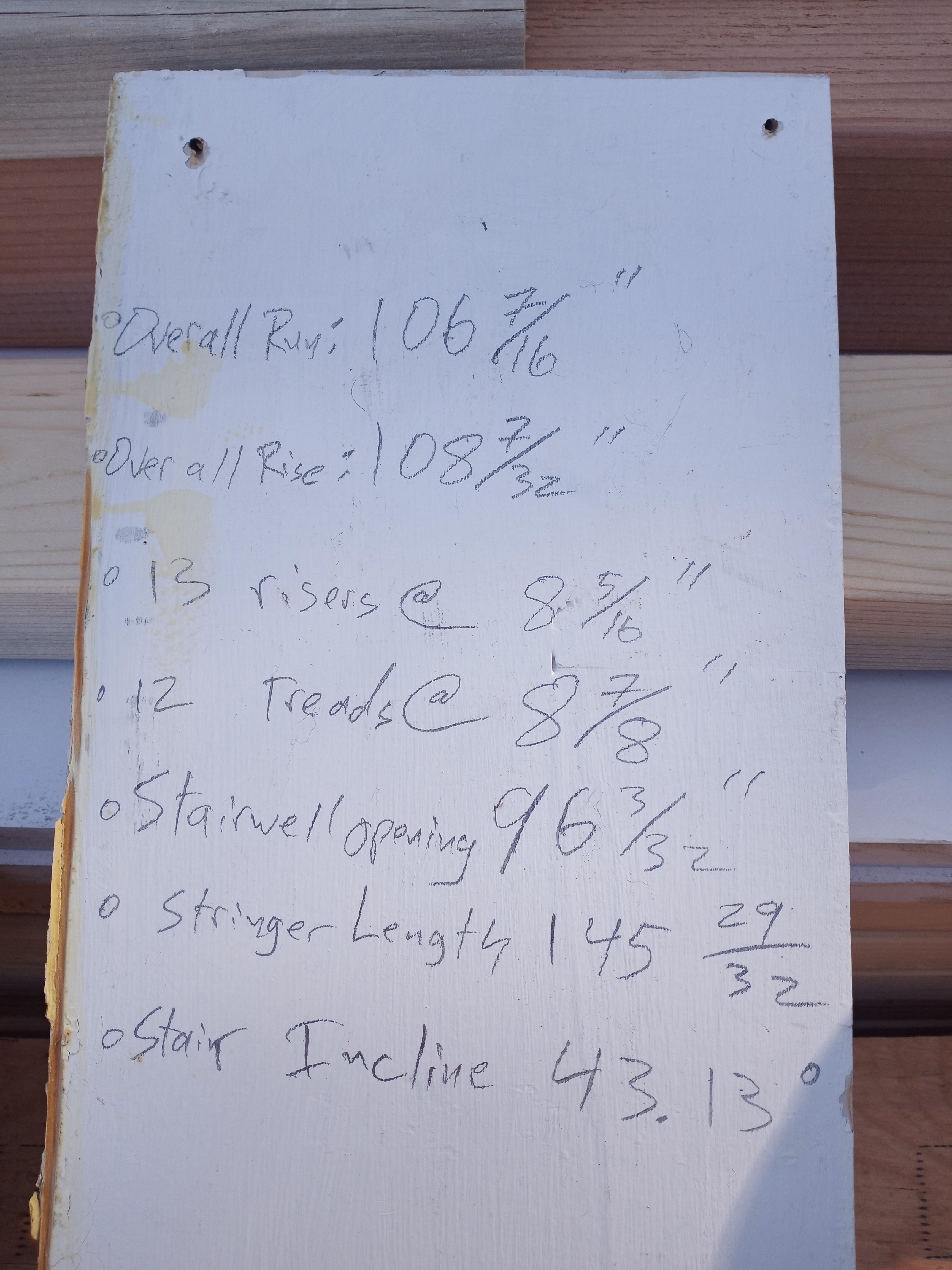
I carefully measured the overall rise and overall run of the space. I punched these numbers into my construction calculator to determine the unit rise (height from the top of one tread to the next) and unit run (depth of a single tread from the face of one riser back to the face of the next riser) and other important information that I'll need to build the new stairs. I wrote this all down on a scrap of wood that I'll hang onto until the project is complete.
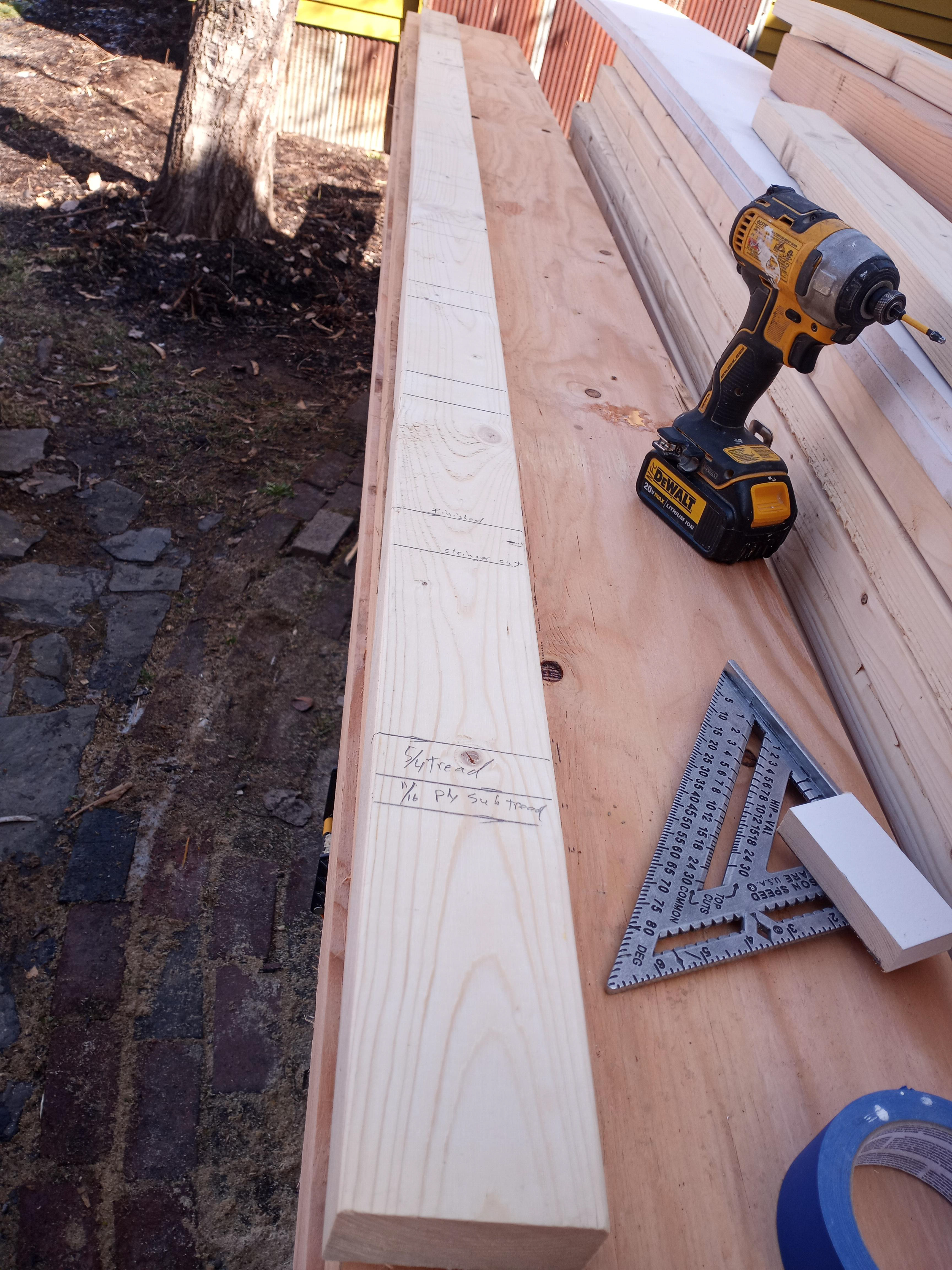
I'm building a story pole with the elevation of the various components of the stairs to check against the actual space. After I label the subtreads, risers and landing tread, I'll stand the pole up in place to be sure that my stairs will end at exactly the elevation that I want them to.
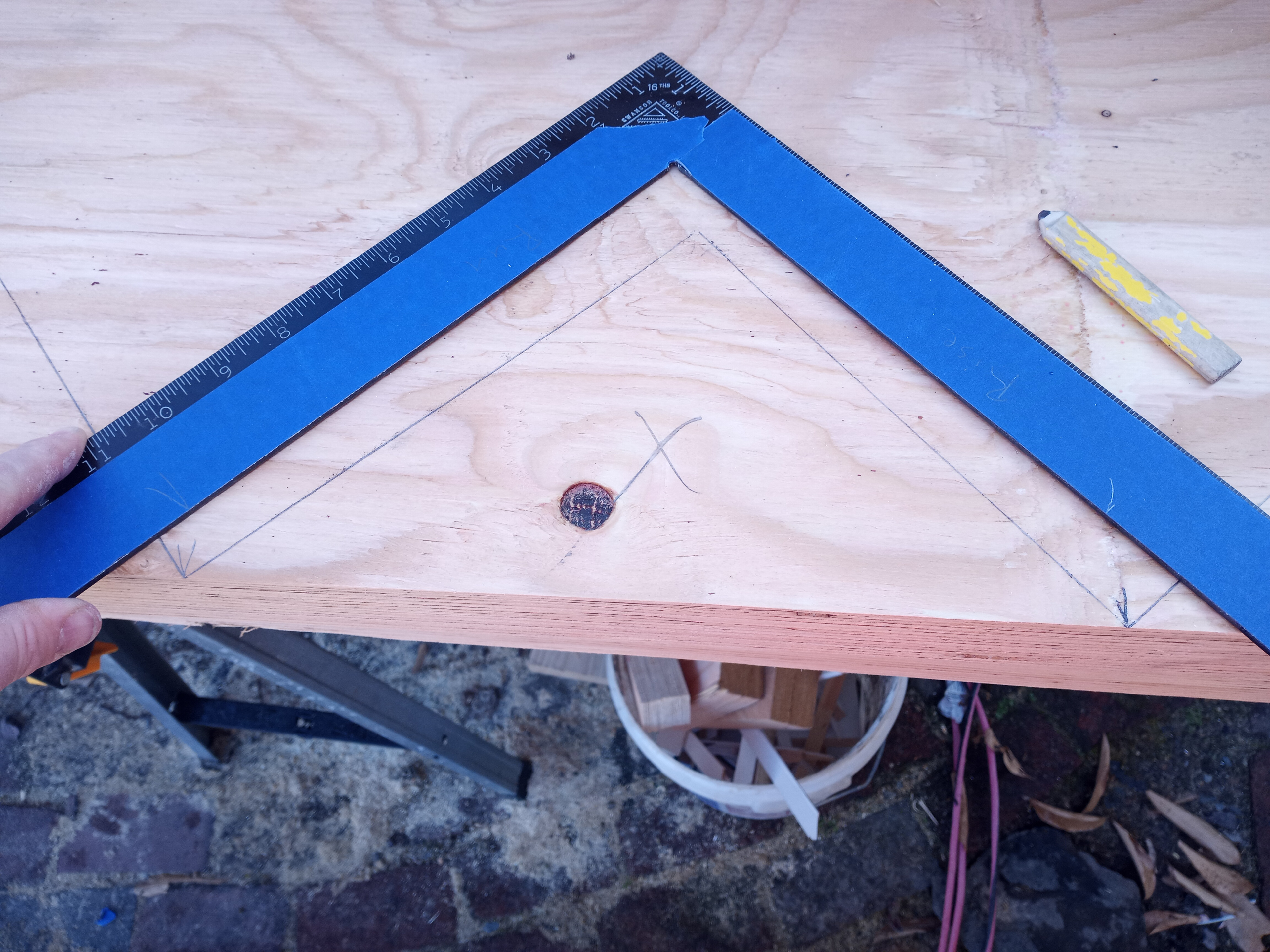
I'm using LVL for stringers because they are stable and more uniform than framing lumber. I'll cut a bunch of right triangle shaped notches out of the stringers so they can support the treads and risers. The direct path From one nosing to the next is the hypotenuse of a triangle. I prefer to layout the hypotenuse of each notch using a tape measure hooked to the end of the stringer. I use a construction calculator to keep adding the hypotenuse to the previous hypotenuse mark on the stringer stock. Now I can align my framing square with the hypotenuse marks in order to avoid accumulating error.
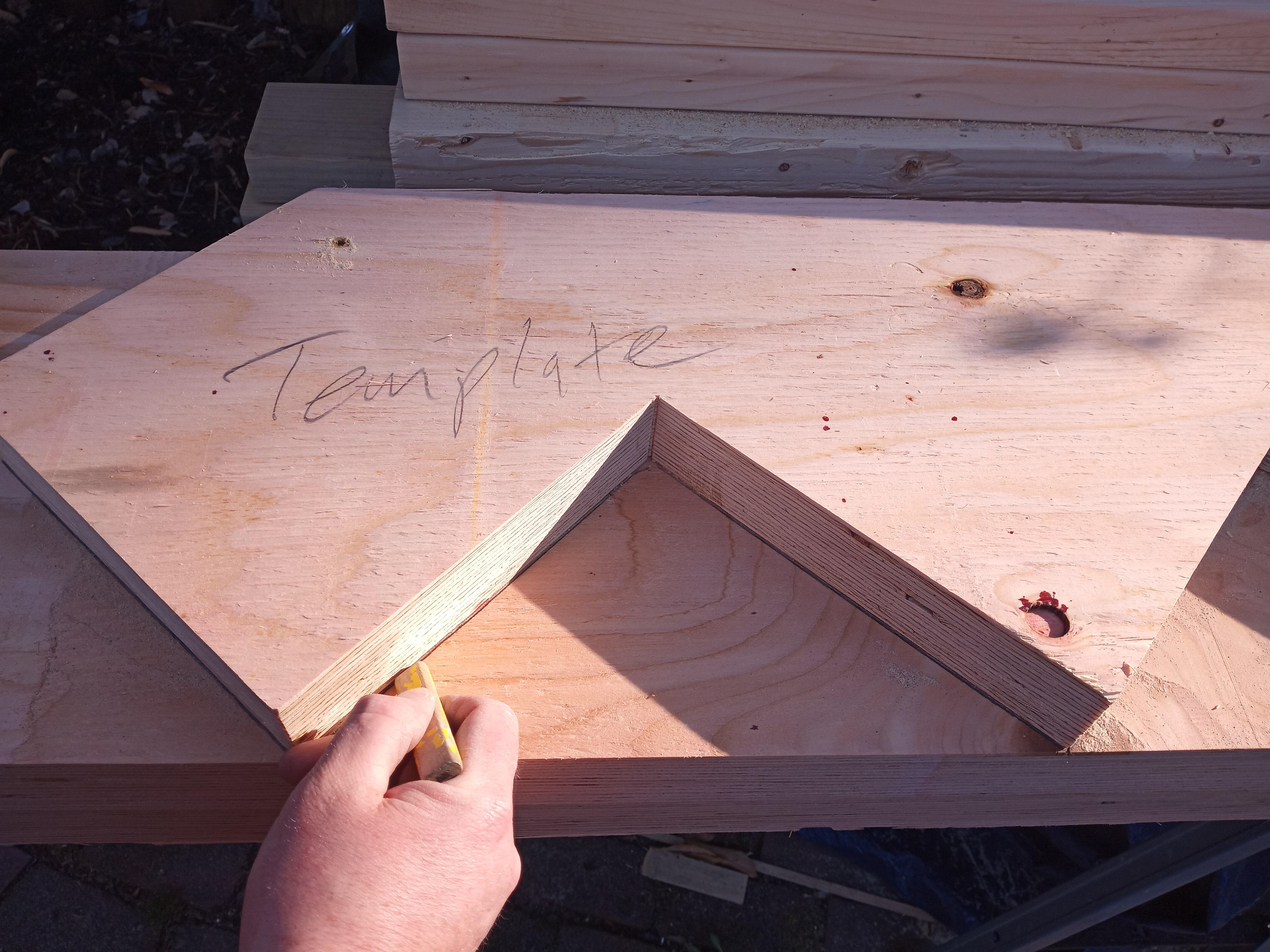
Cutting stringers in the usual fashion is straightforward with a circular saw and jig saw. Since my stringers are site-built I dry fit the first stringer in place to be sure that it's cut correctly with the proper overall run. I'm using the first stringer as a template to layout the remaining stringers.
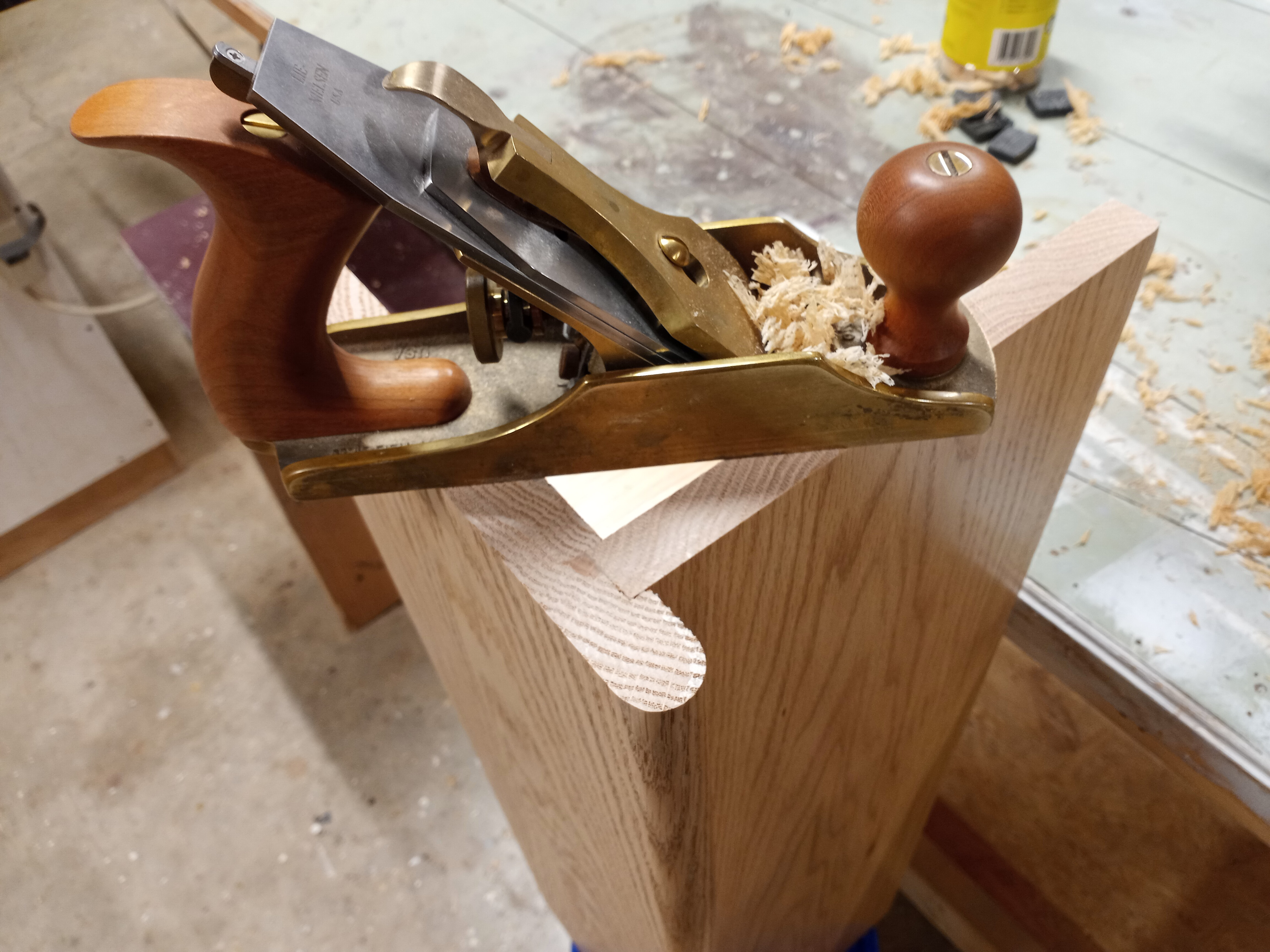
Back at the shop, I've pre-assembled the treads and risers with pocket screws and PL construction adhesive. I cut a dado into the bottom of the treads to help register the risers and create a strong glue joint. A few swipes with a hand plane will flush the endgrain of the tread to that of the riser.
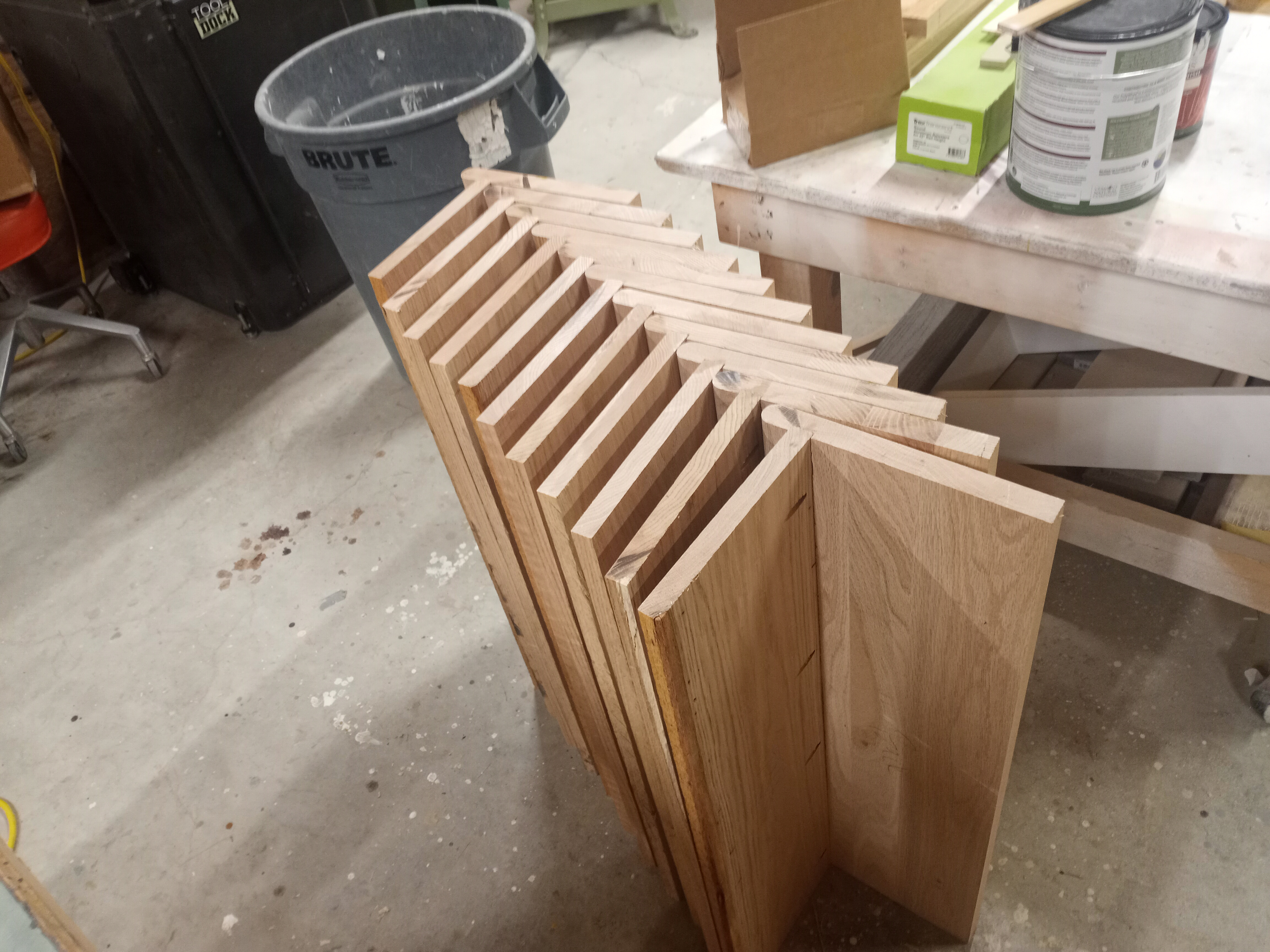
The tread and riser assemblies are ready to transport to the jobsite.
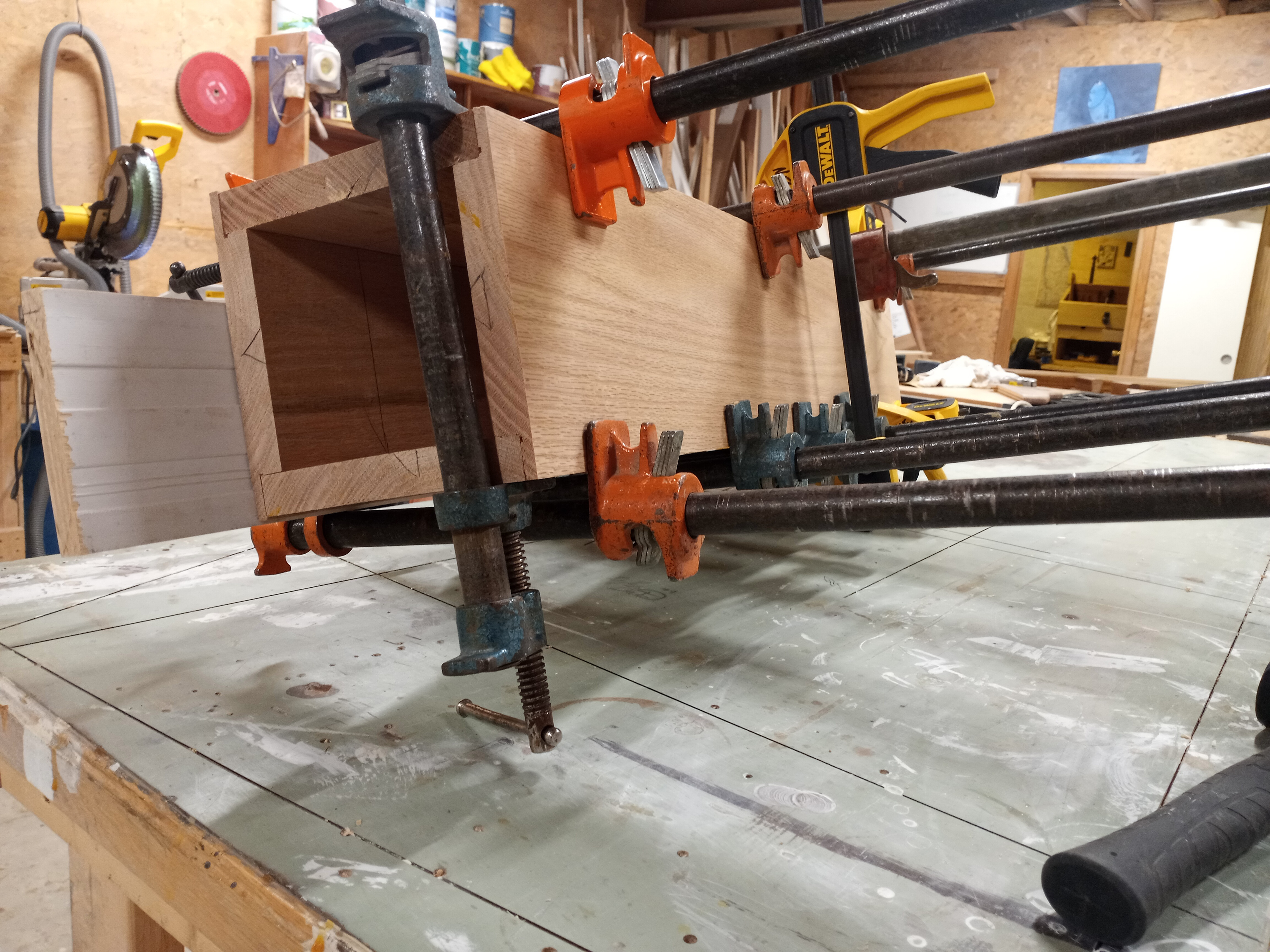
I built a sleeve for the newel post. This will widen the base of the factory made newel post so it can accommodate the thickness of the supporting wall, the baseboard and the skirt board. I used rabbet joints and biscuits for registration and stability. It's important to find balustrade alignment issues before I put saw my to the expensive stair and balustrade components.
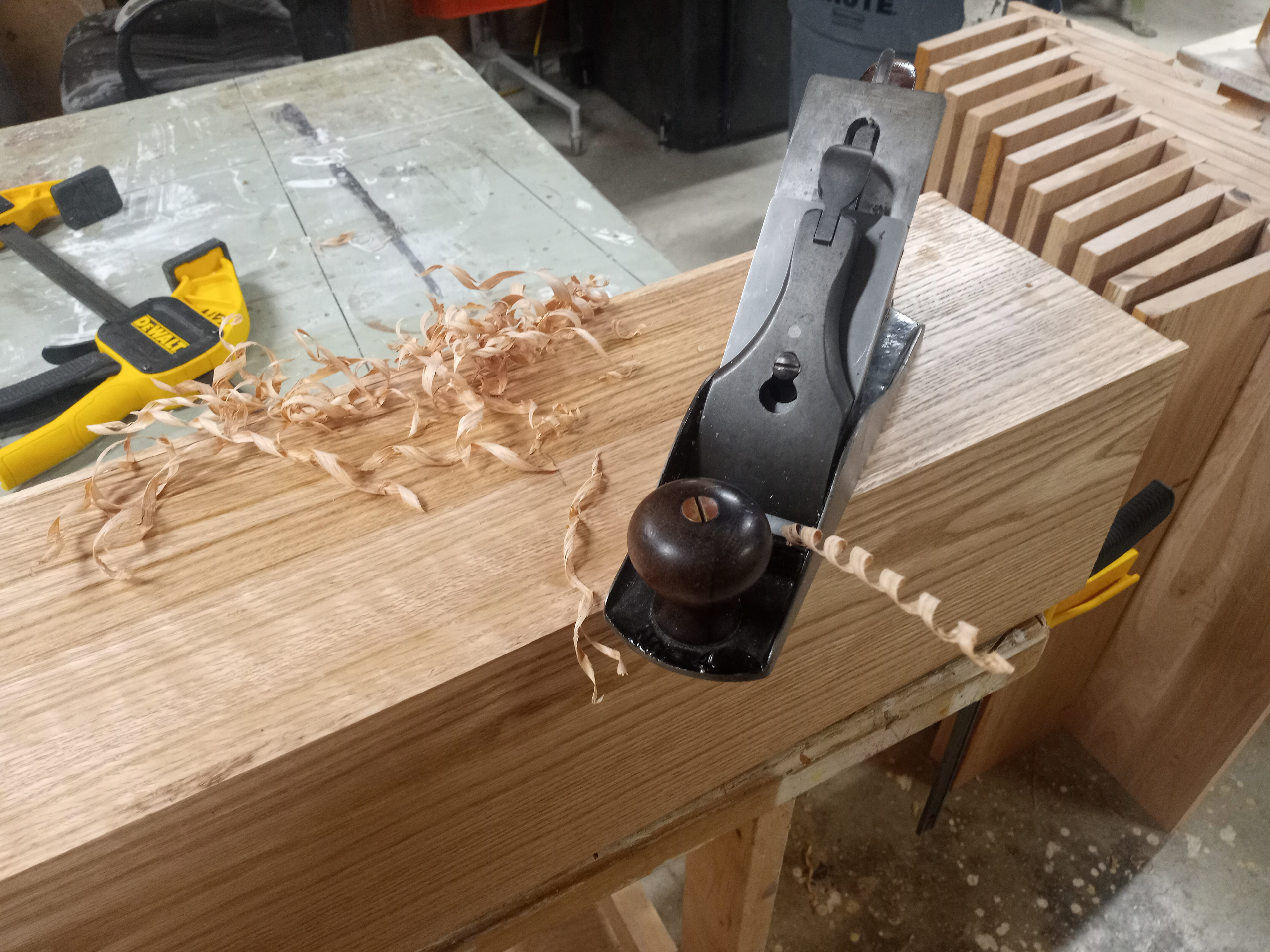
I'm planing the edge of the rabbet flush to the face of the newel post sleeve. I will follow this up with machine sanding to 220 grit. Prefinishing the parts with 2 coats of vermont natural coatings polywhey polyurethane will prevent drywall dust and adhesive from staining the raw oak.
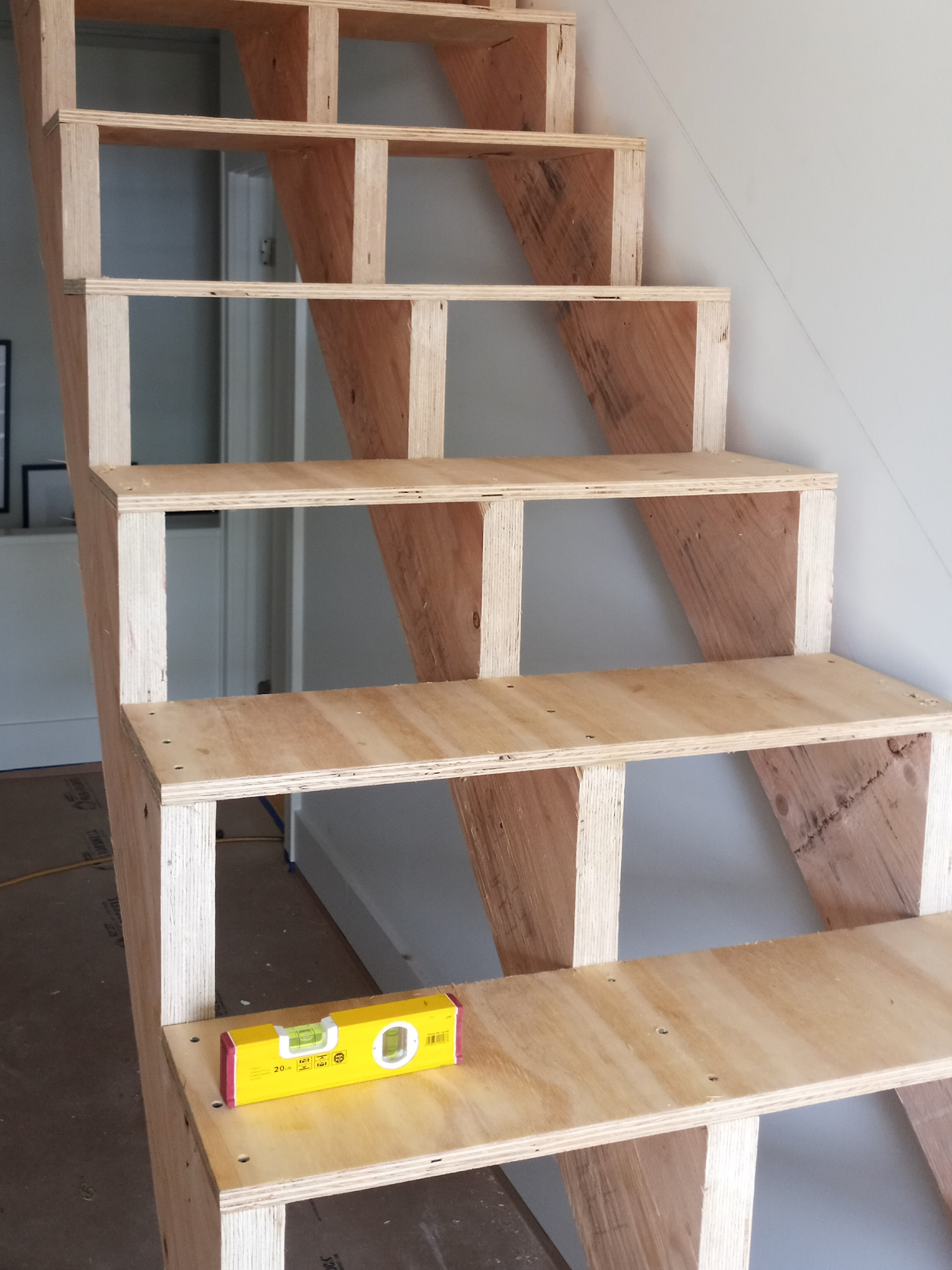
I assembled the framing on the floor. A plywood nailer is blind nailed to the backside of the stringers at the top of the stairs. This nailer is, in turn, fastened to the rim joist of the stairwell. The sub-treads are glued with PL construction adhesive and screwed. High quality plywood subtreads will stiffen the stairs. It's important to check the framing assembly for square.
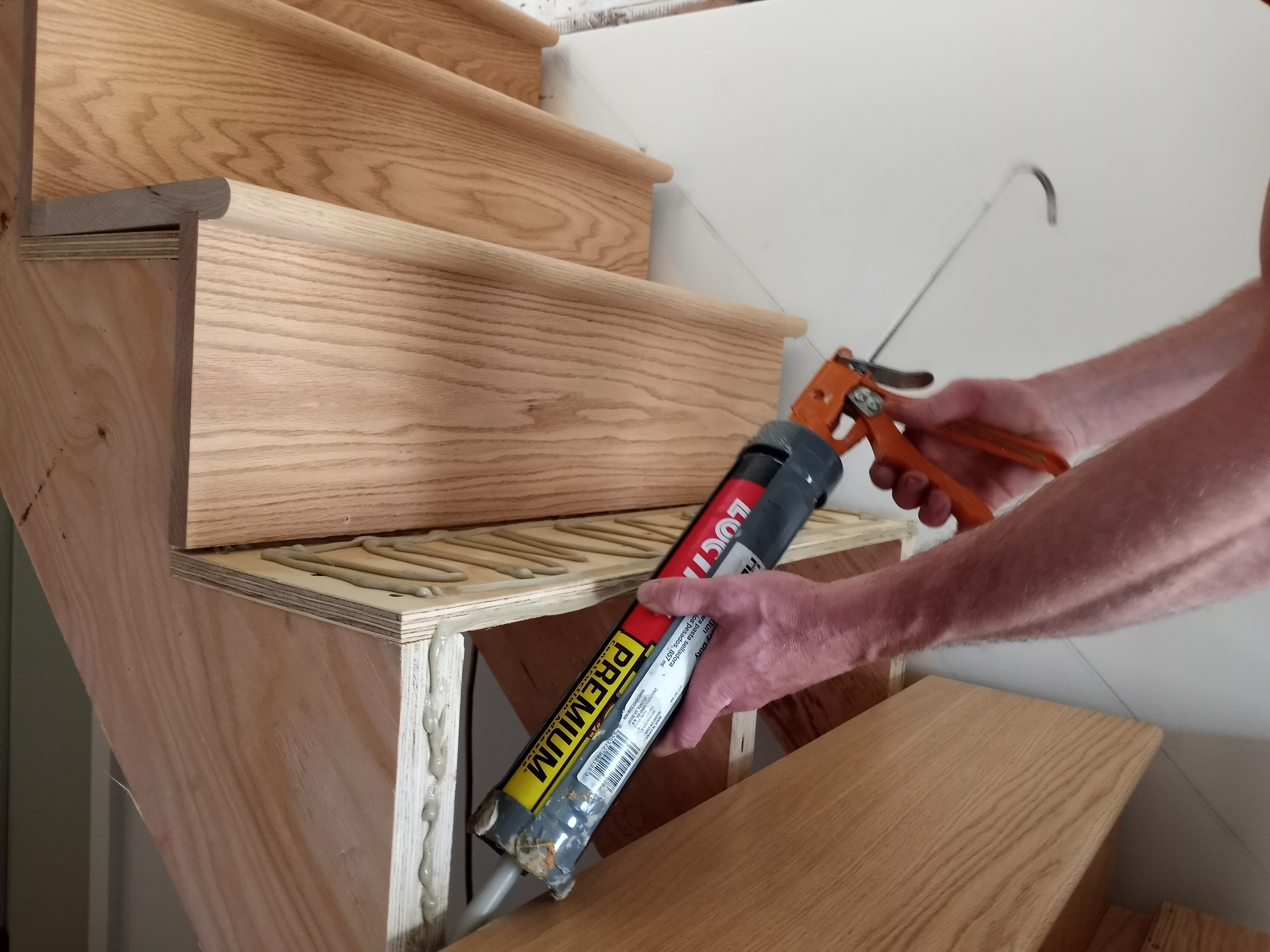
The riser and tread assemblies are glued with PL and blind screwed from below.
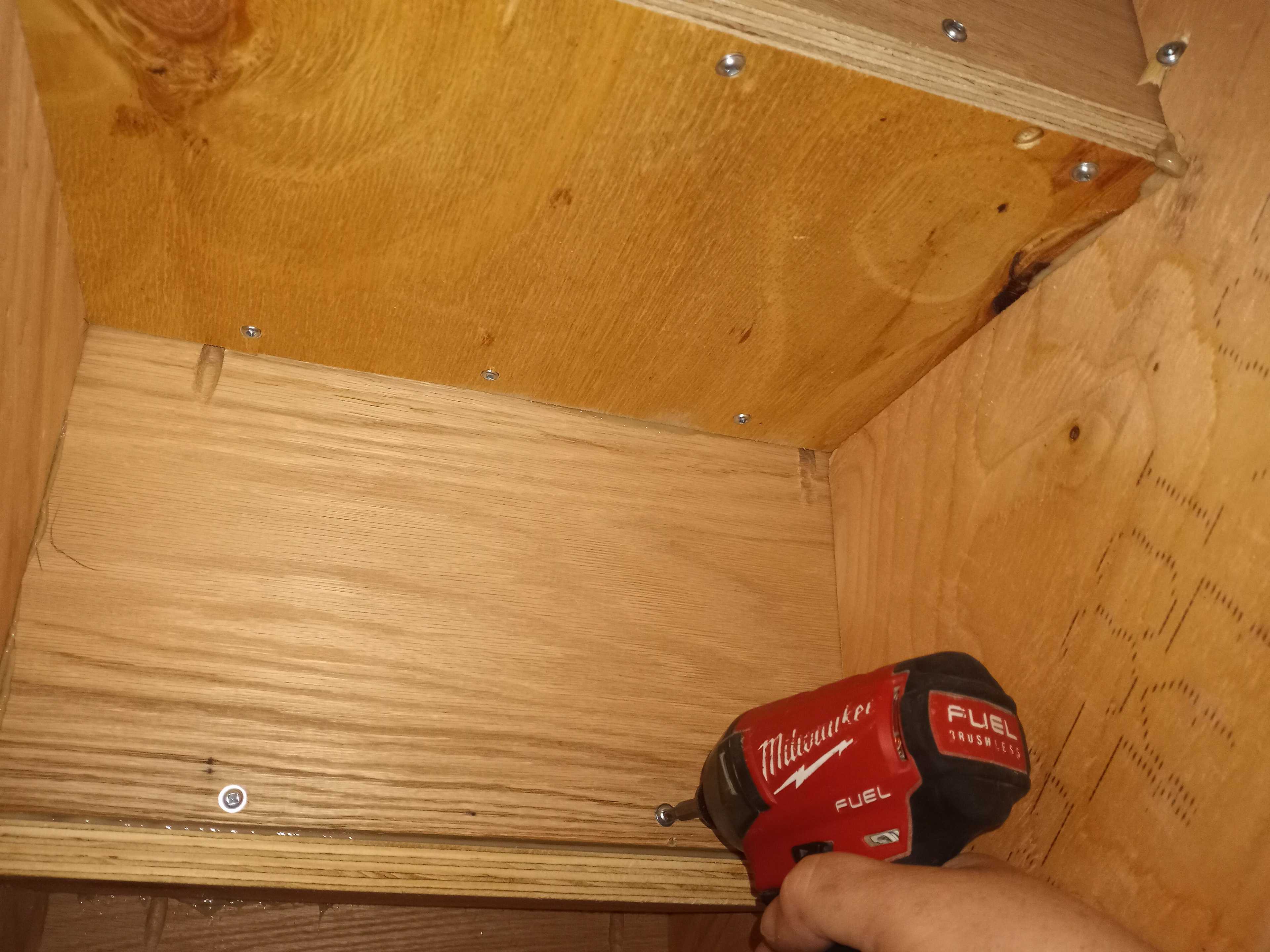
The risers are face screwed to the backside of the tread below. The treads are secured with screws through the sub-treads. The risers are fastened to the stringers with pocket screws toe-nailed through the stringers. Hiding the fasteners in this way will give the completed staircase the traditional look of a housed stringer staircase.
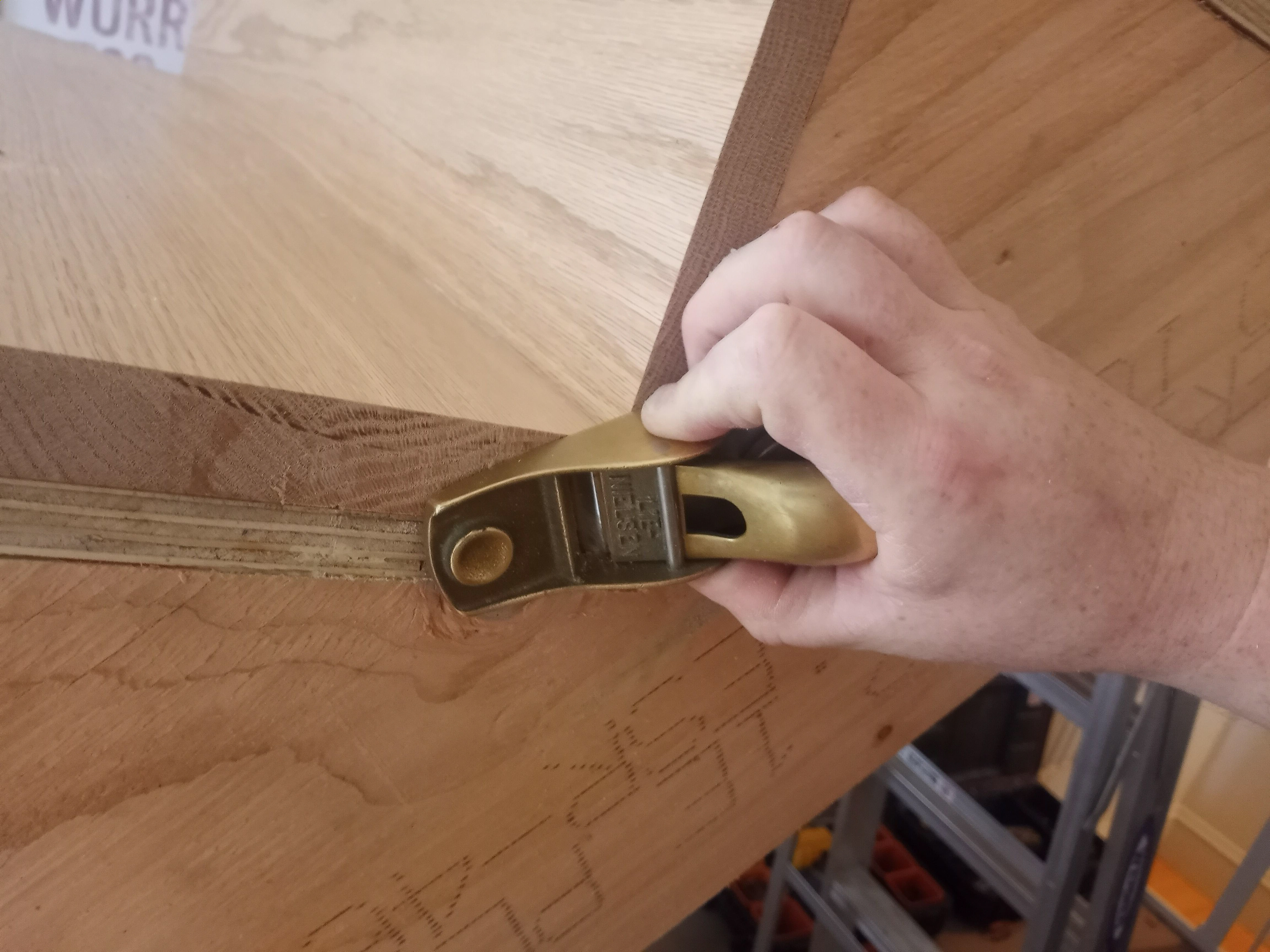
With the treads and risers installed I'm block planing away any misalignment between the tread and riser assemblies. The treads and risers are about 1/4" overall wider than the sub treads. This gives me a little bit of wiggle room to tweak things if the framing isn't perfectly square.
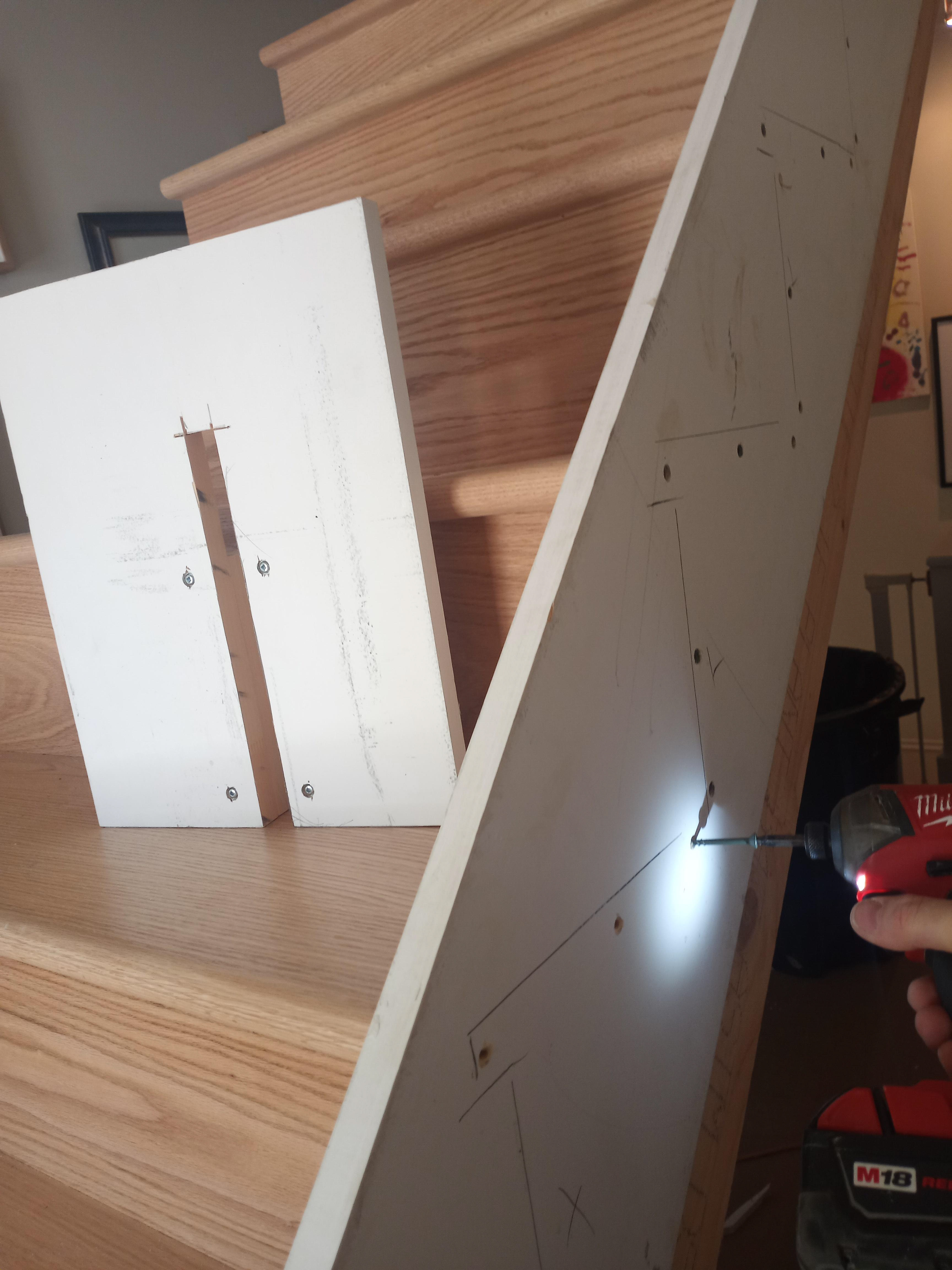
The pants jig allows me to accurately trace the treads and riser locations onto the sides of the skirt boards. This enables me to confidently face screw the skirt boards to the end grain of the treads and risers. To accomplish this I had to drop the stairs down and push them away from the existing wall. Housed stringers aren't in the budget, but face screwing the skirtboard to the treads and risers will achieve the housed stringer look without the added shop time it would take to route housed stringers.
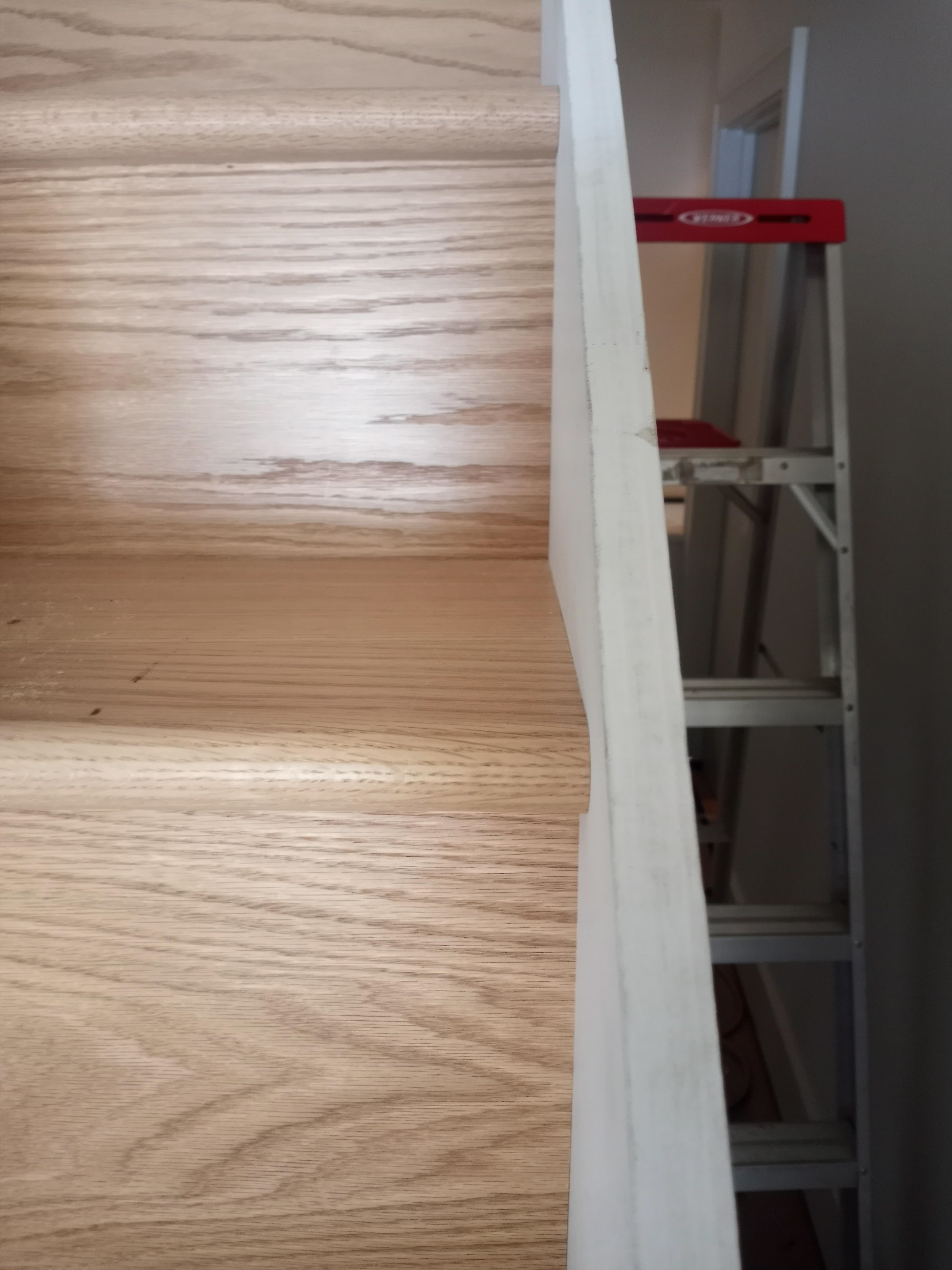
A seamless look.
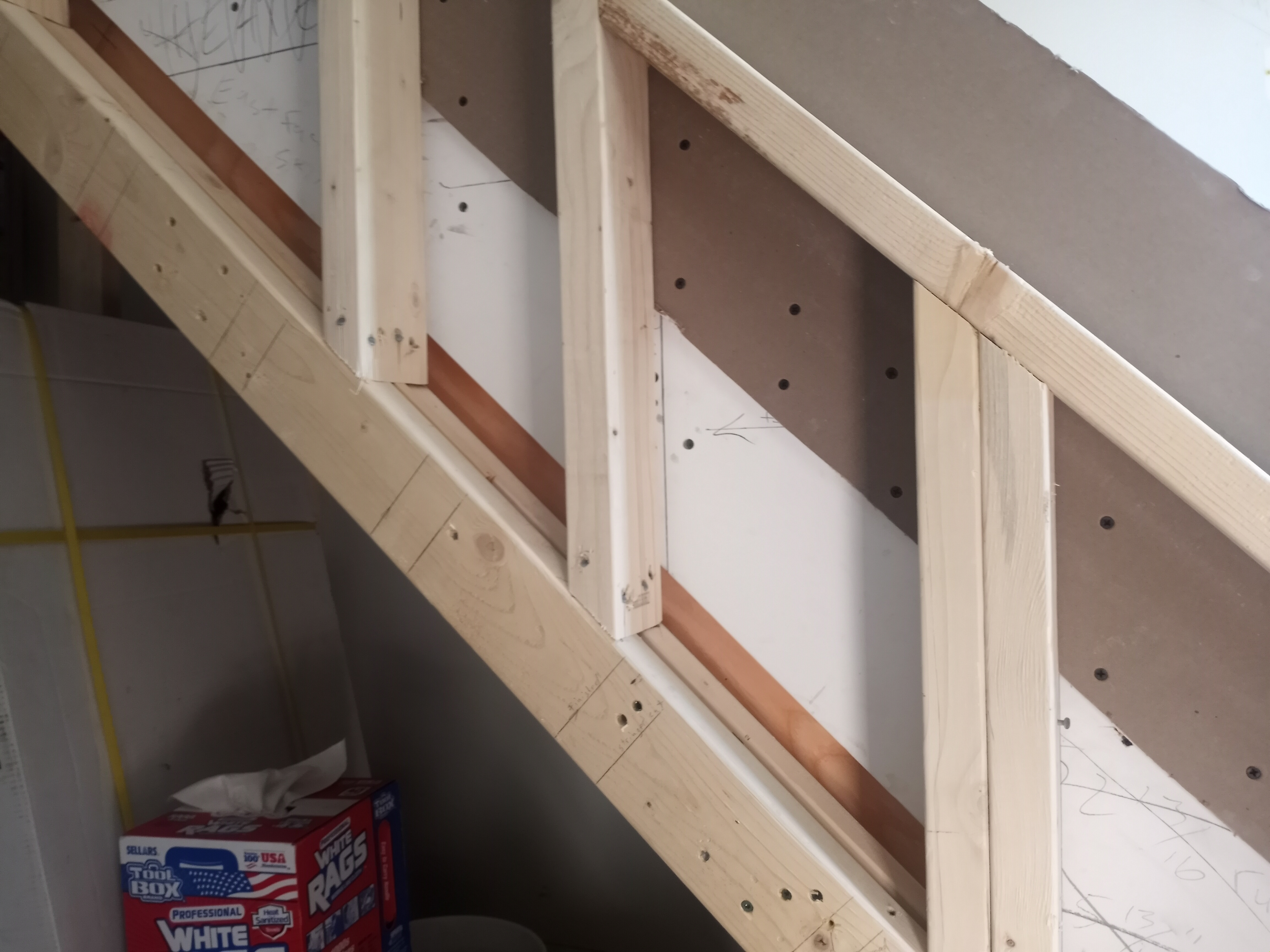
With the stairs installed I proceeded to framing and sheetrocking the supporting walls under the stairs. I've fastened the sheetrock directly to the backside of the skirtboard with 1" screws for a seamless look that will allow me to forgo installing basecap along the top of the skirtboard.
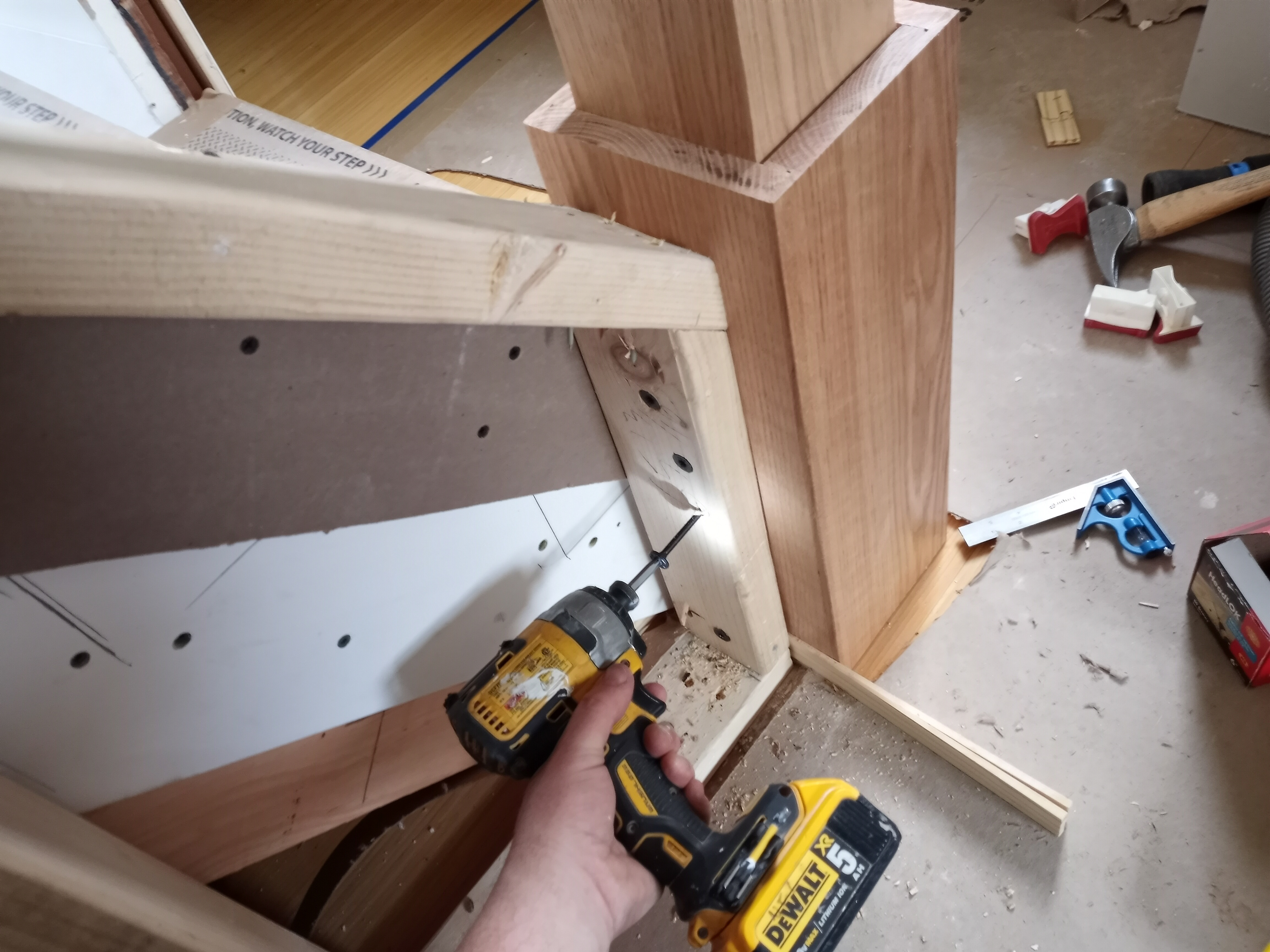
I'm installing the newel post and sleeve with shims and lag screws for a tight and plumb fit.
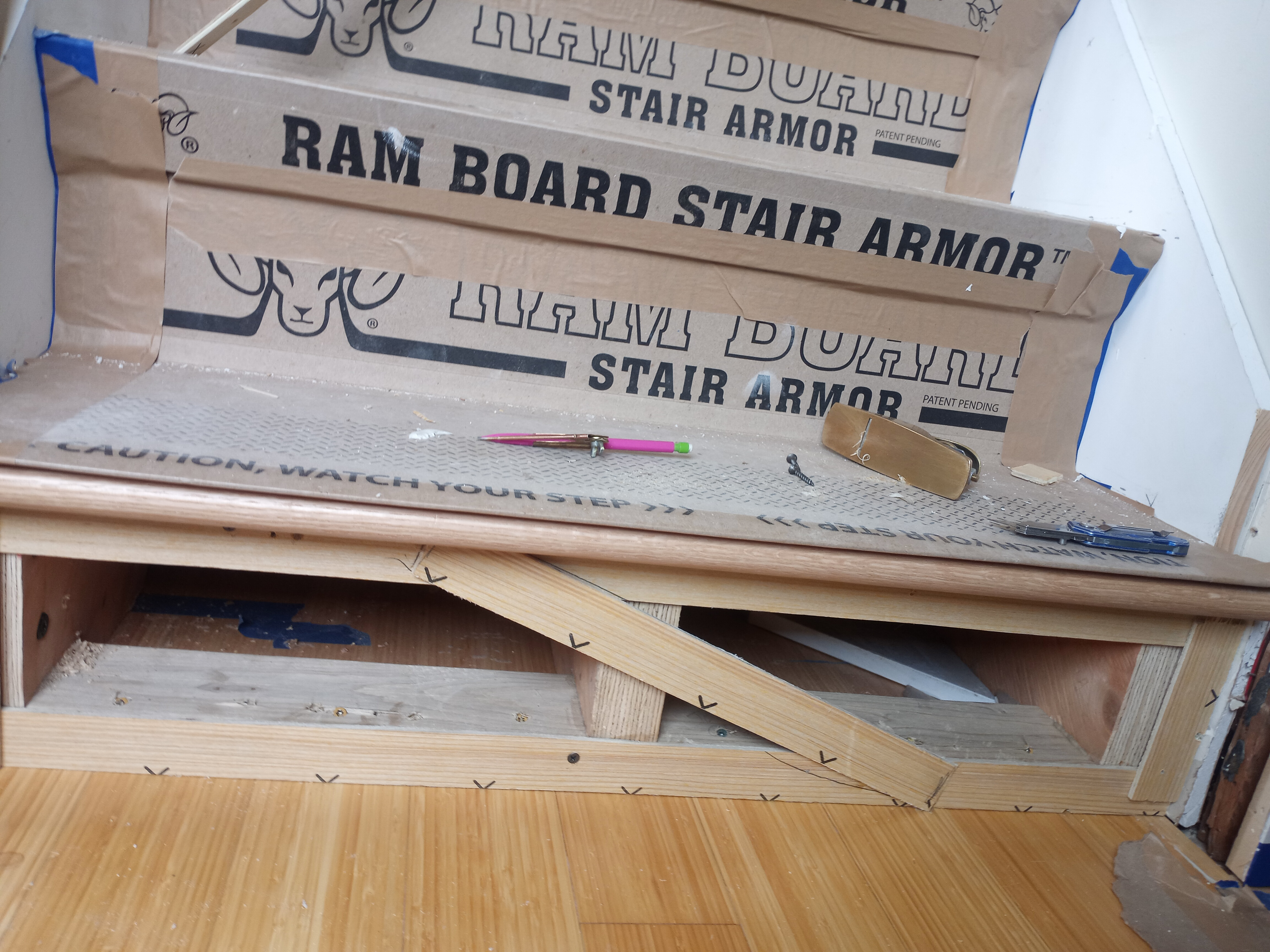
Templating the bottom riser, top riser and landing tread with luan and my hot glue gun ensures a tight fight of those parts.
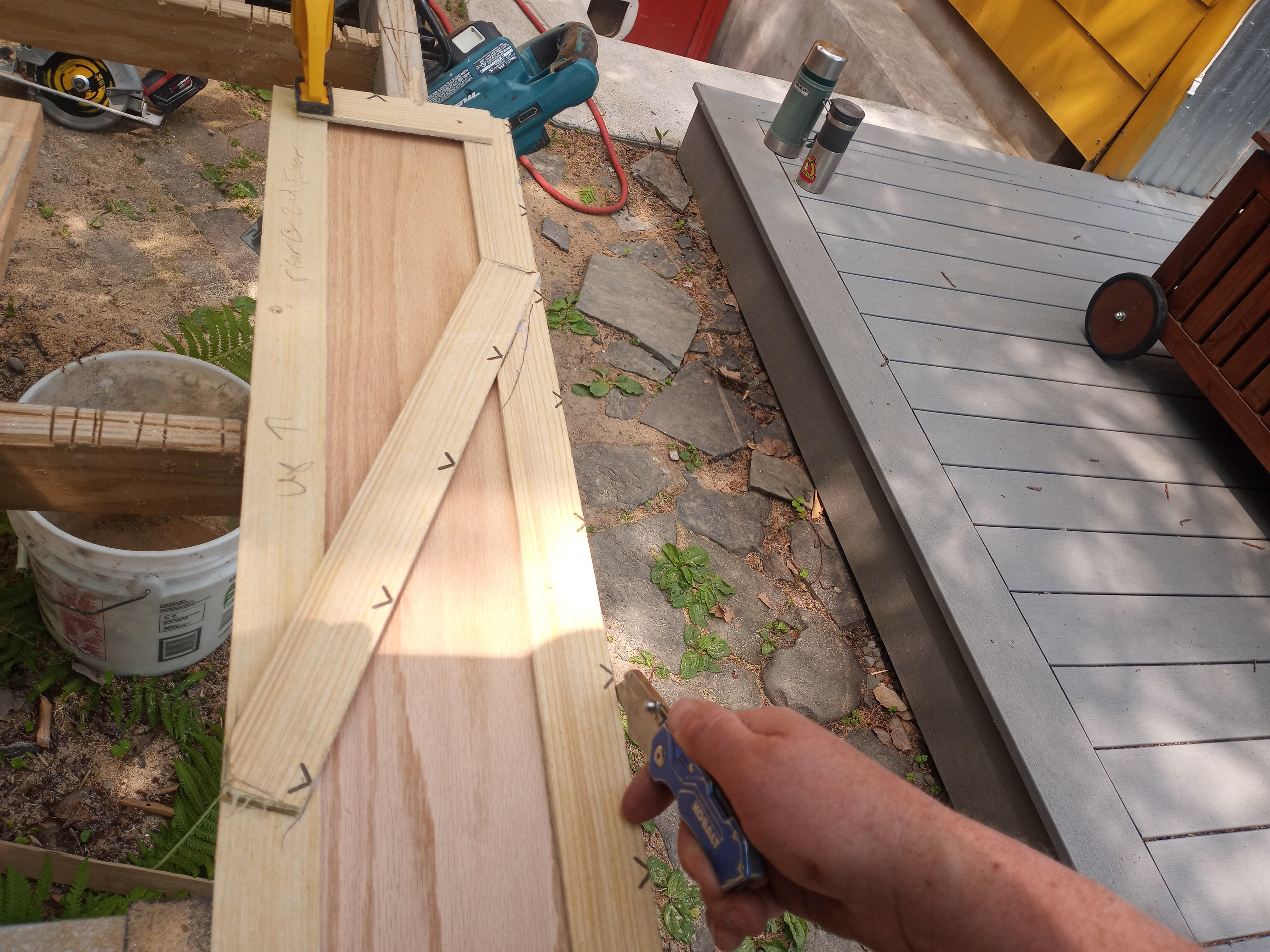
I'm tracing the luan templates onto the oak parts with a utility knife and blue tape for final fitting with the miter saw and block plane.
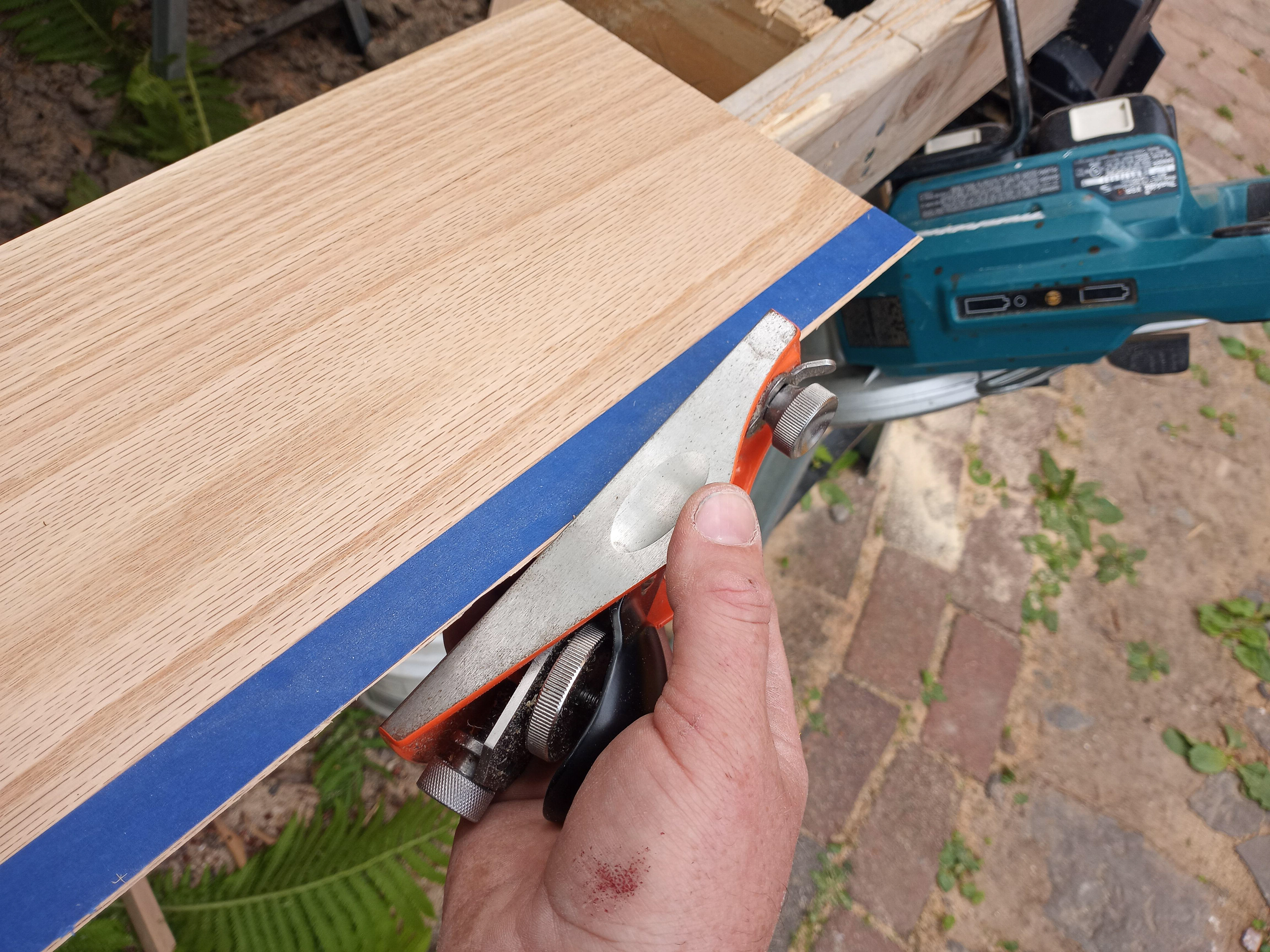
A block plane fits the bottom riser to the wavy floor boards. The blue tape makes it easier to see what I'm doing.
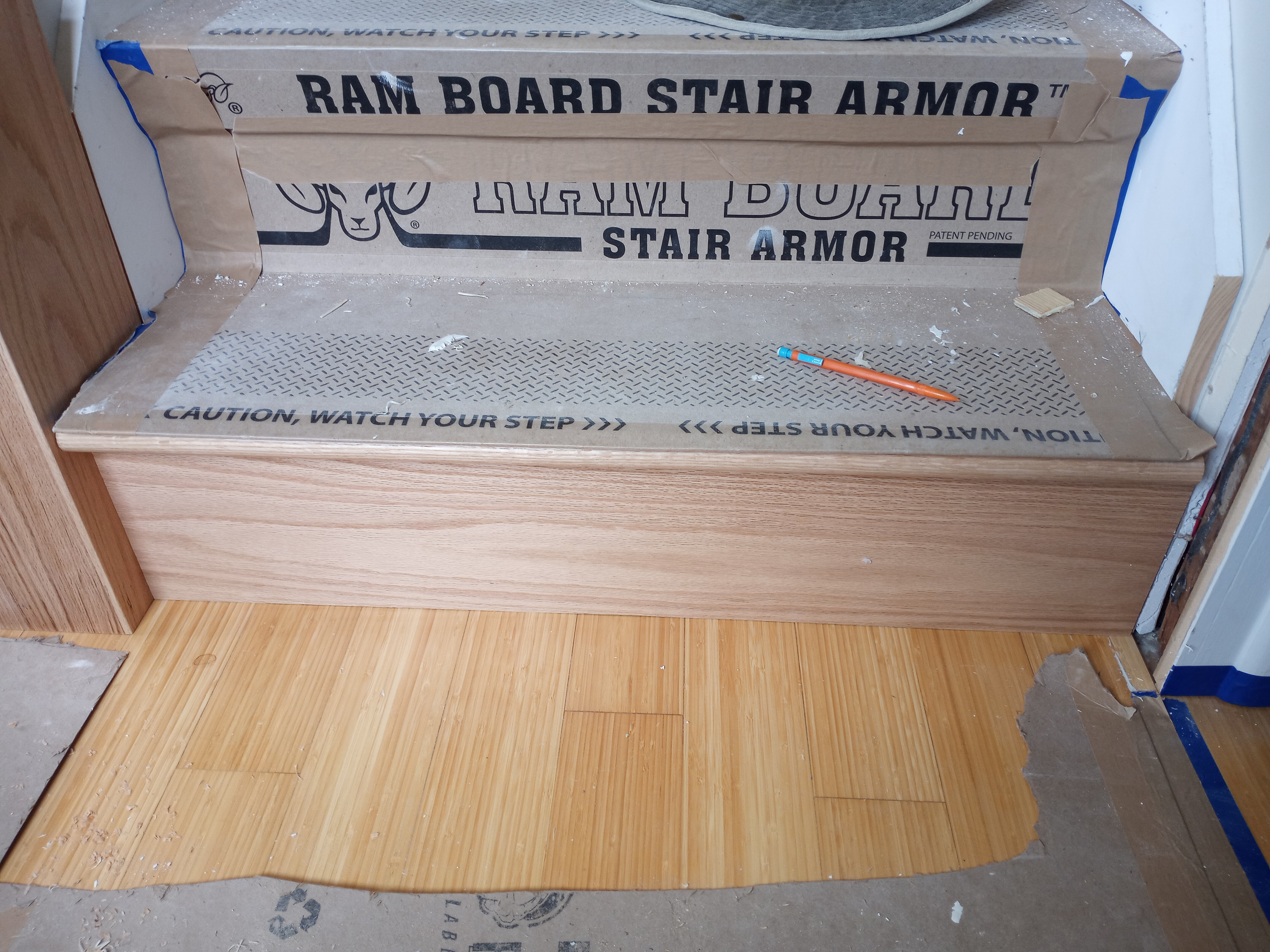
The bottom and top riser fit tightly to the staircase. I've fastened the bottom riser to the stringers from the backside of the staircase. I face-screwed the top riser.
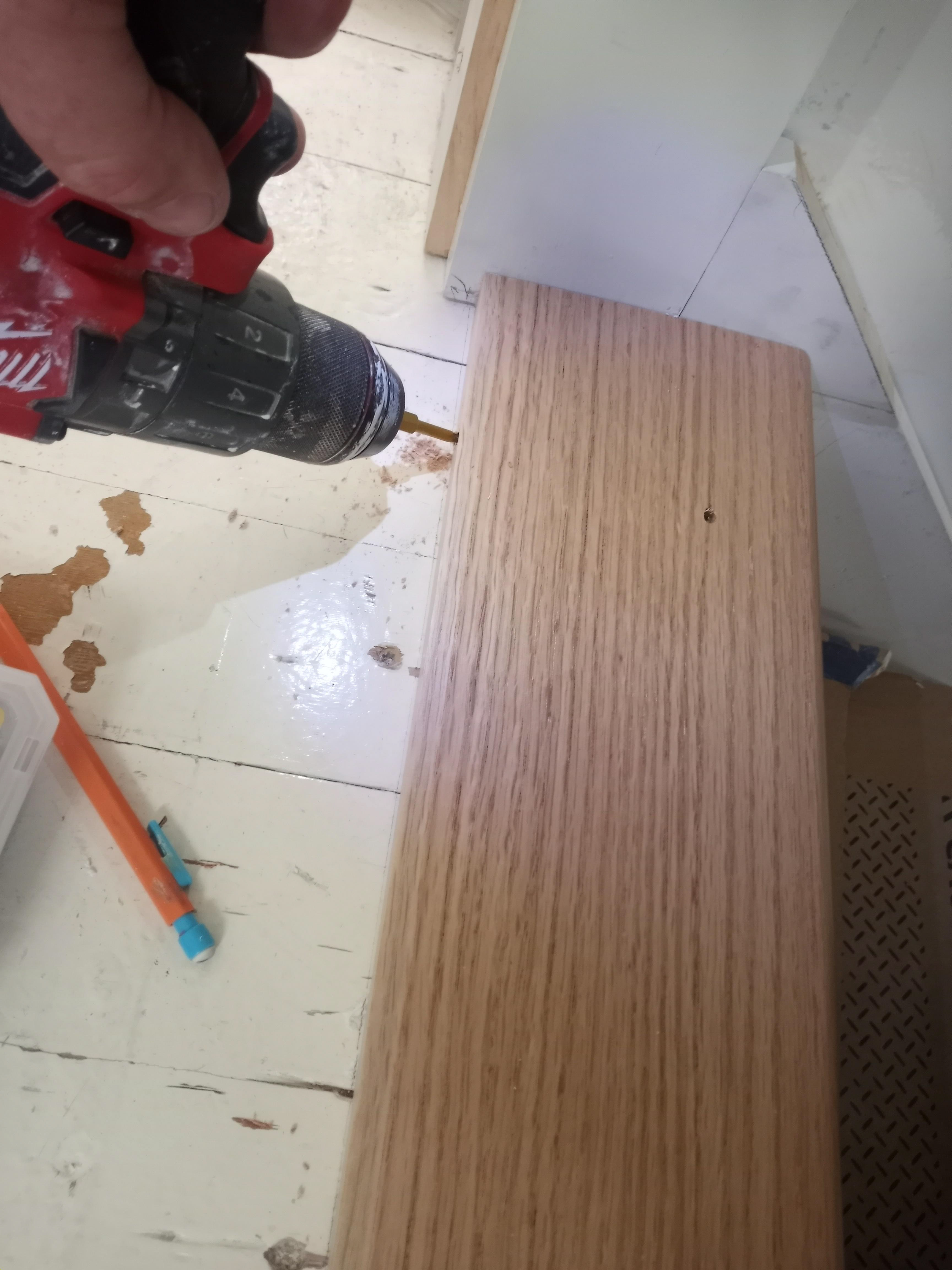
Face screwing/nailing the top riser and landing tread is necessary because I can't access the backside of these components. I did manage to fasten the landing tread in part with hidden toe-nails.
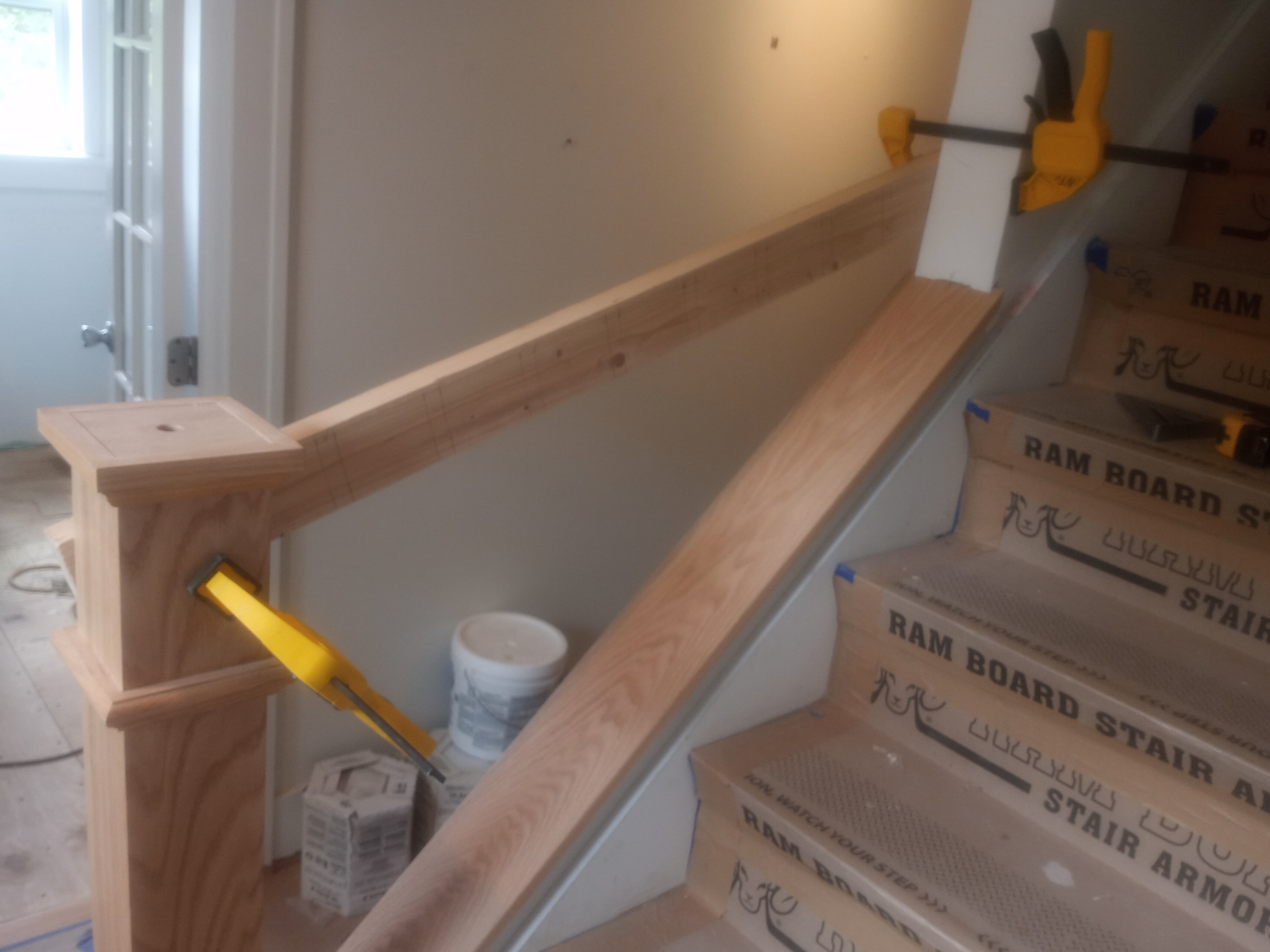
Laying out the rake-wall cap for balusters is straightforward with a story pole. I drew the location of the balusters on a 2x4 assuming 4 3/4" centers. I clamped the story pole to the newel post and the wall at an angle so that the balusters lined up with the newel post and wall. This allows me to layout the baluster locations on the rake-wall cap with a level and pencil using both hands.
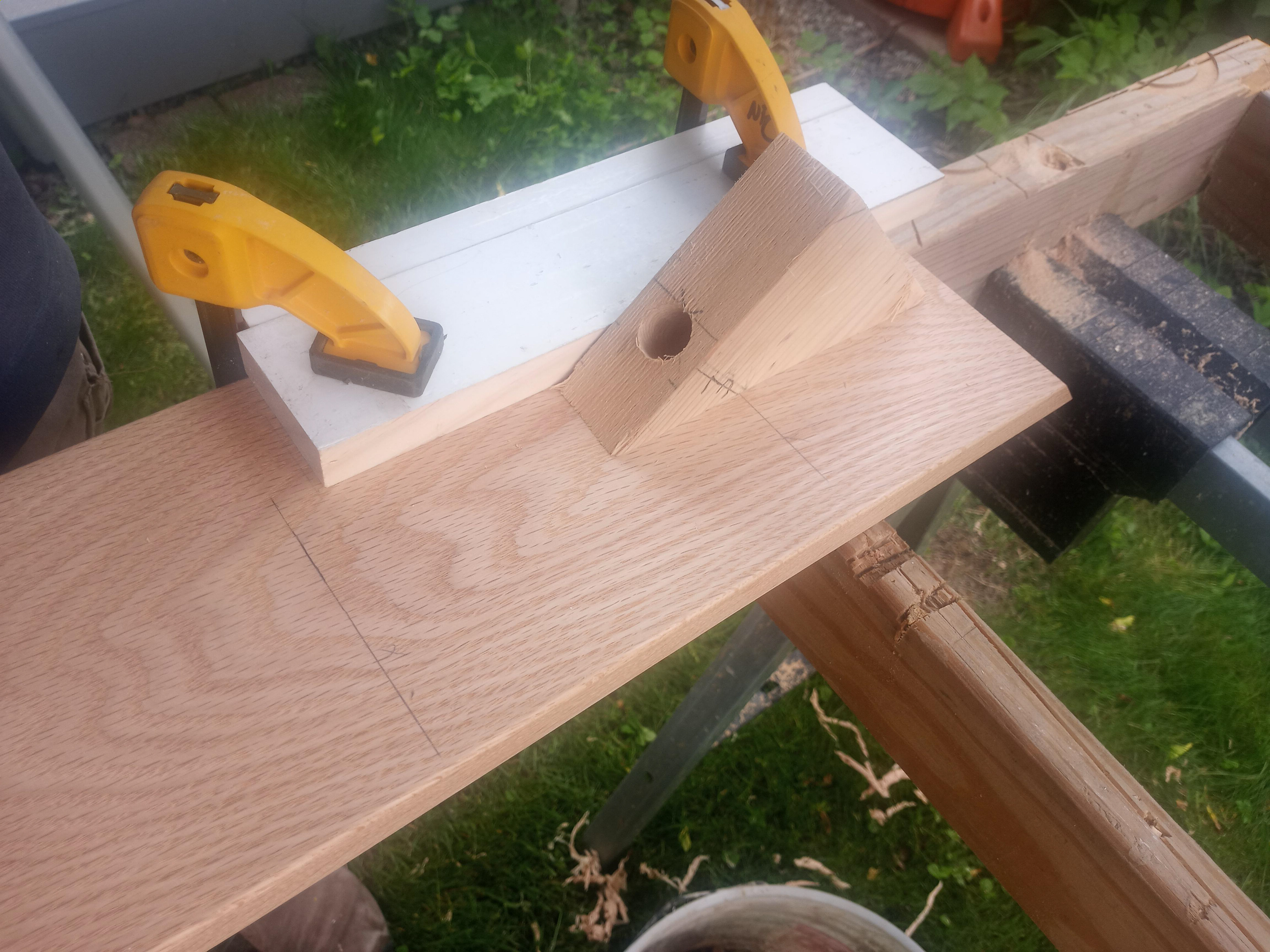
I saved a cutout from the stringer in order to make this drill-guide. There is a spacer and a fence made of 1x pine screwed to the drill guide. This allows me to quickly and easily clamp the drill guide centered on the wall cap.
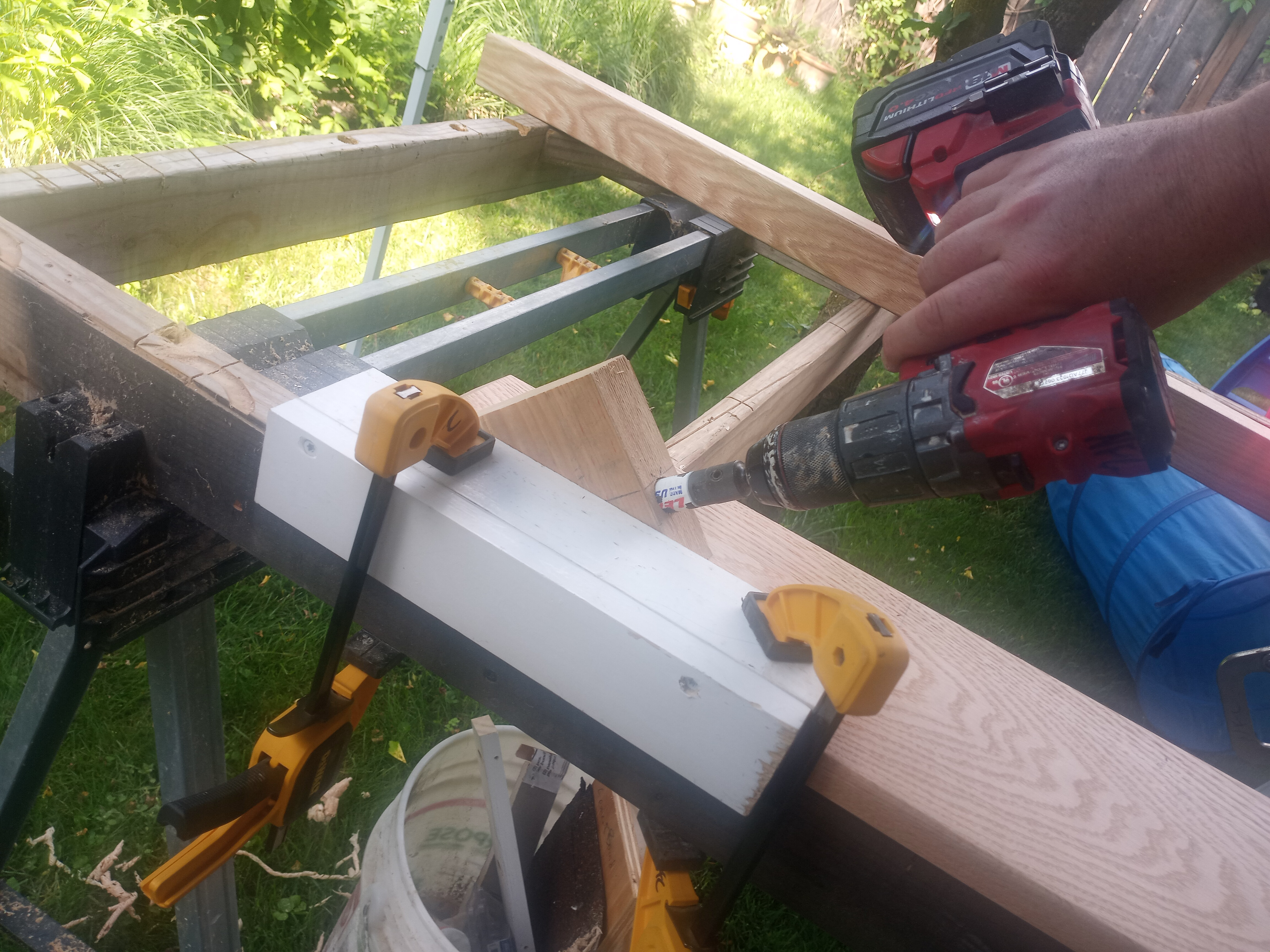
I'm starting the holes with a hole saw which will easily follow the drill guide with tearing out the wood grain. I'll knock out the waste with a chisel.
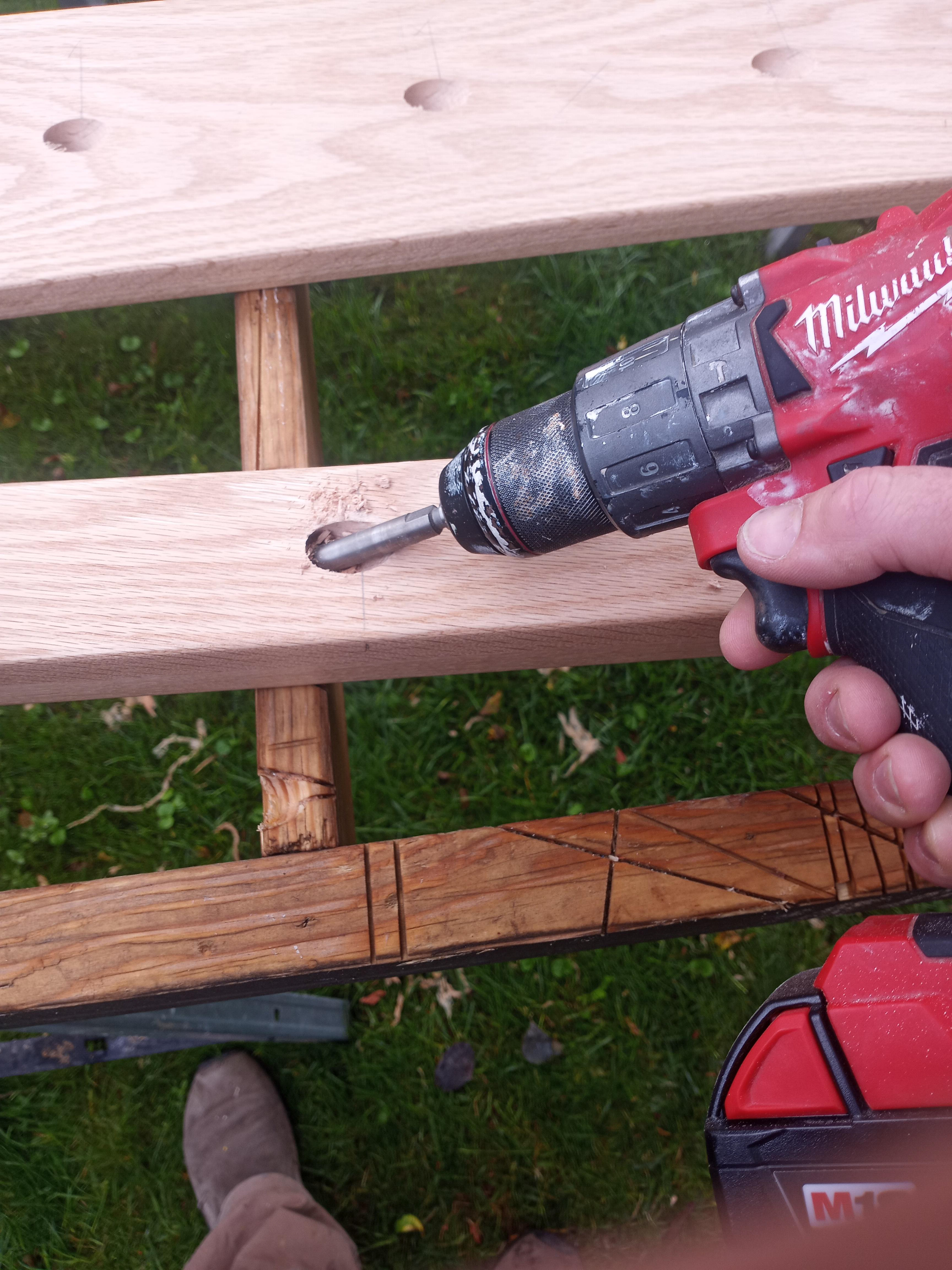
A forsner bit finishes off the holes and leaves them with a flat bottom.
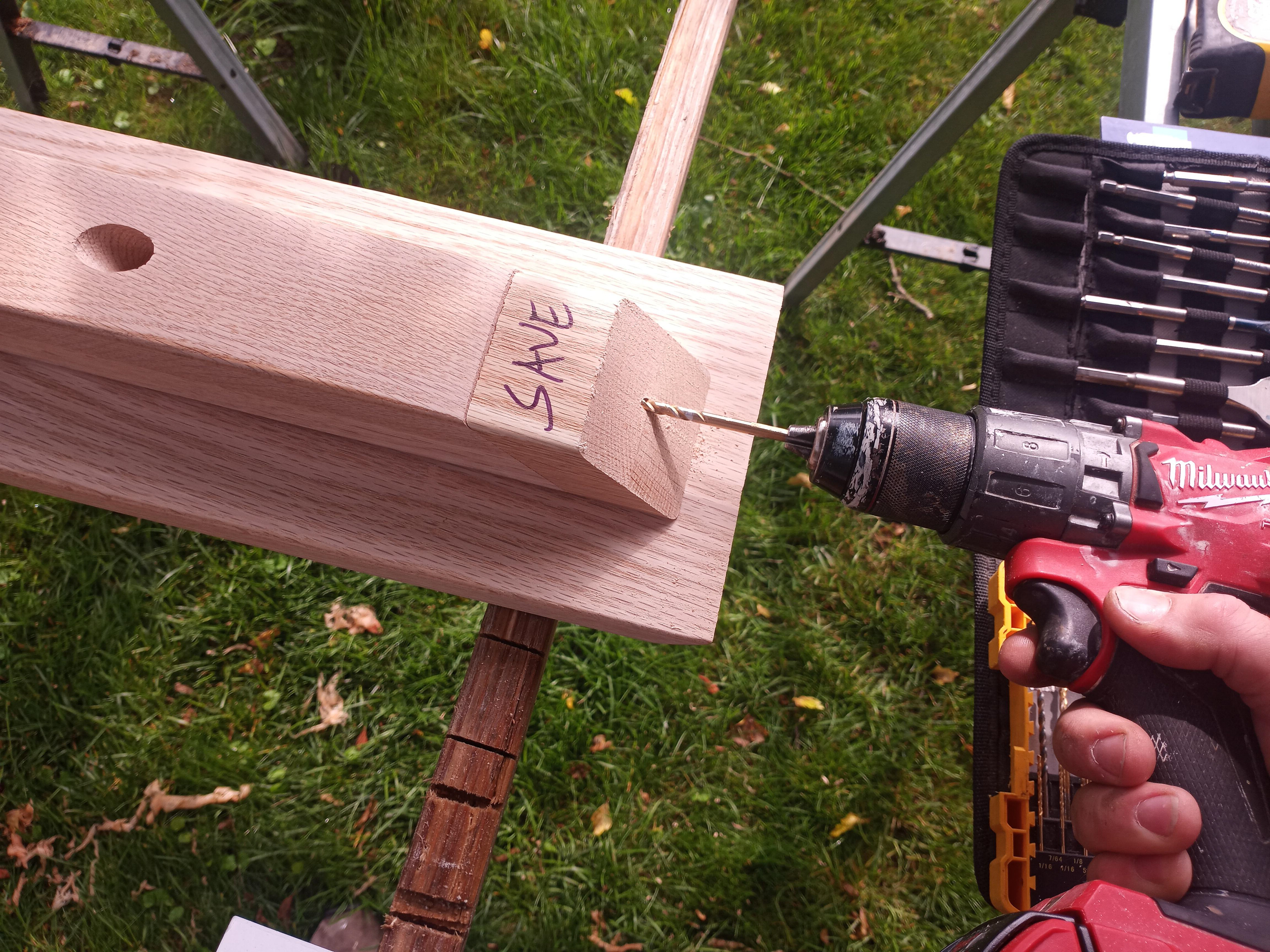
A guide block allows for an easy transfer of the hanger bolt hole in the handrail to the corresponding hole in the newel post.
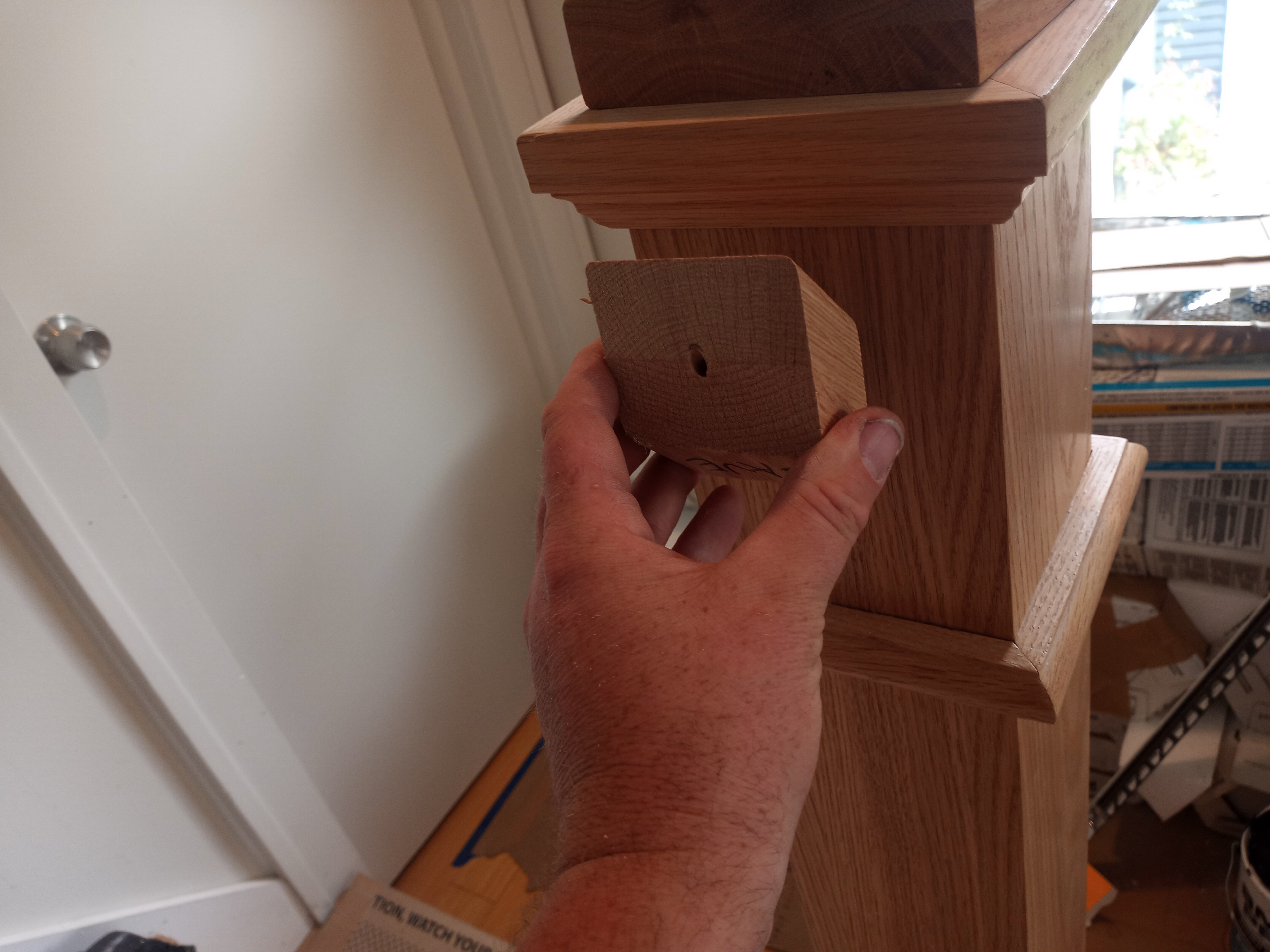
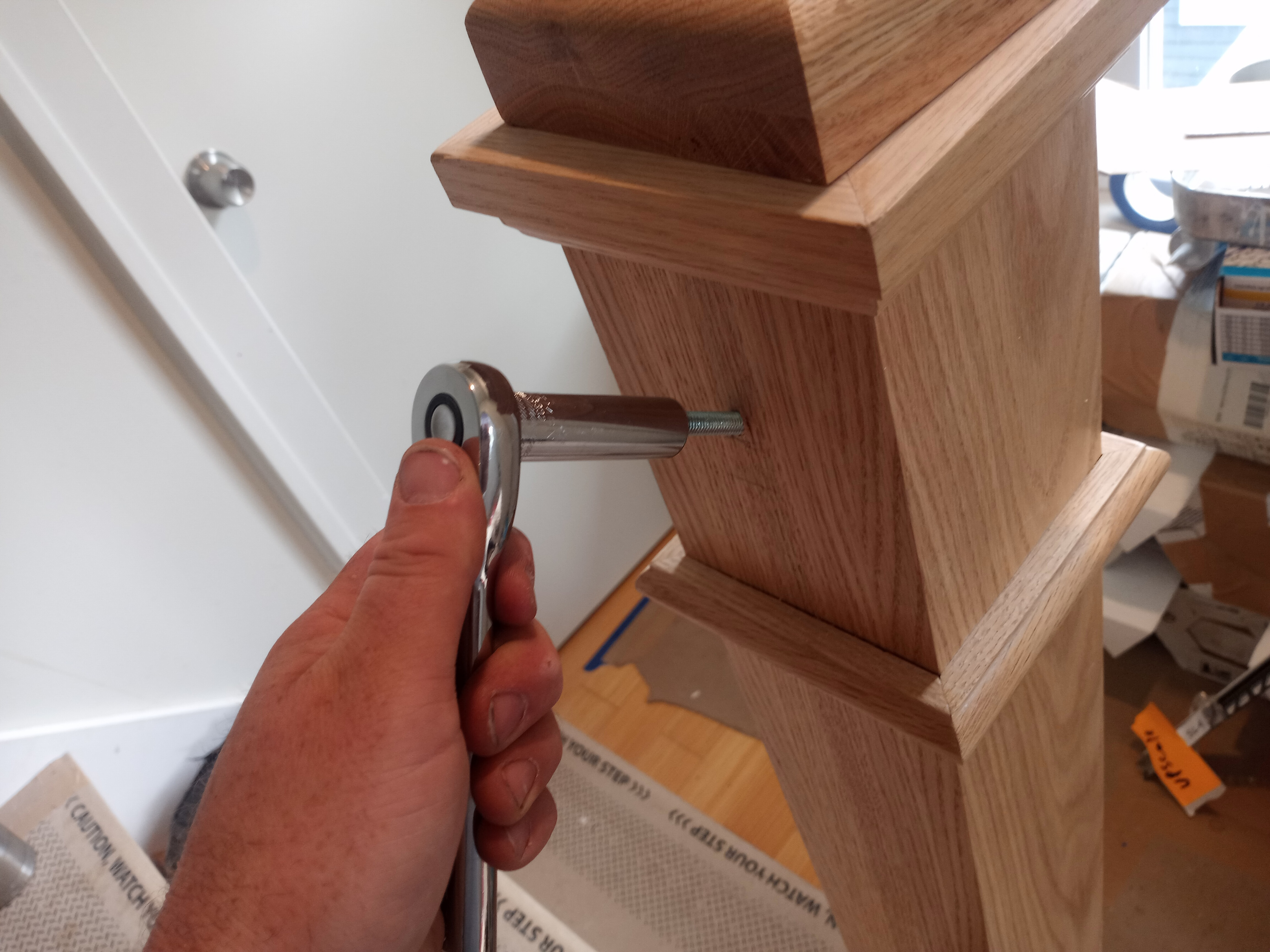
The hanger bolt is essentially a lag screw on the end that I'm driving into the newel post and a bolt end that will receive a hidden nut and washer installed from below the handrail.
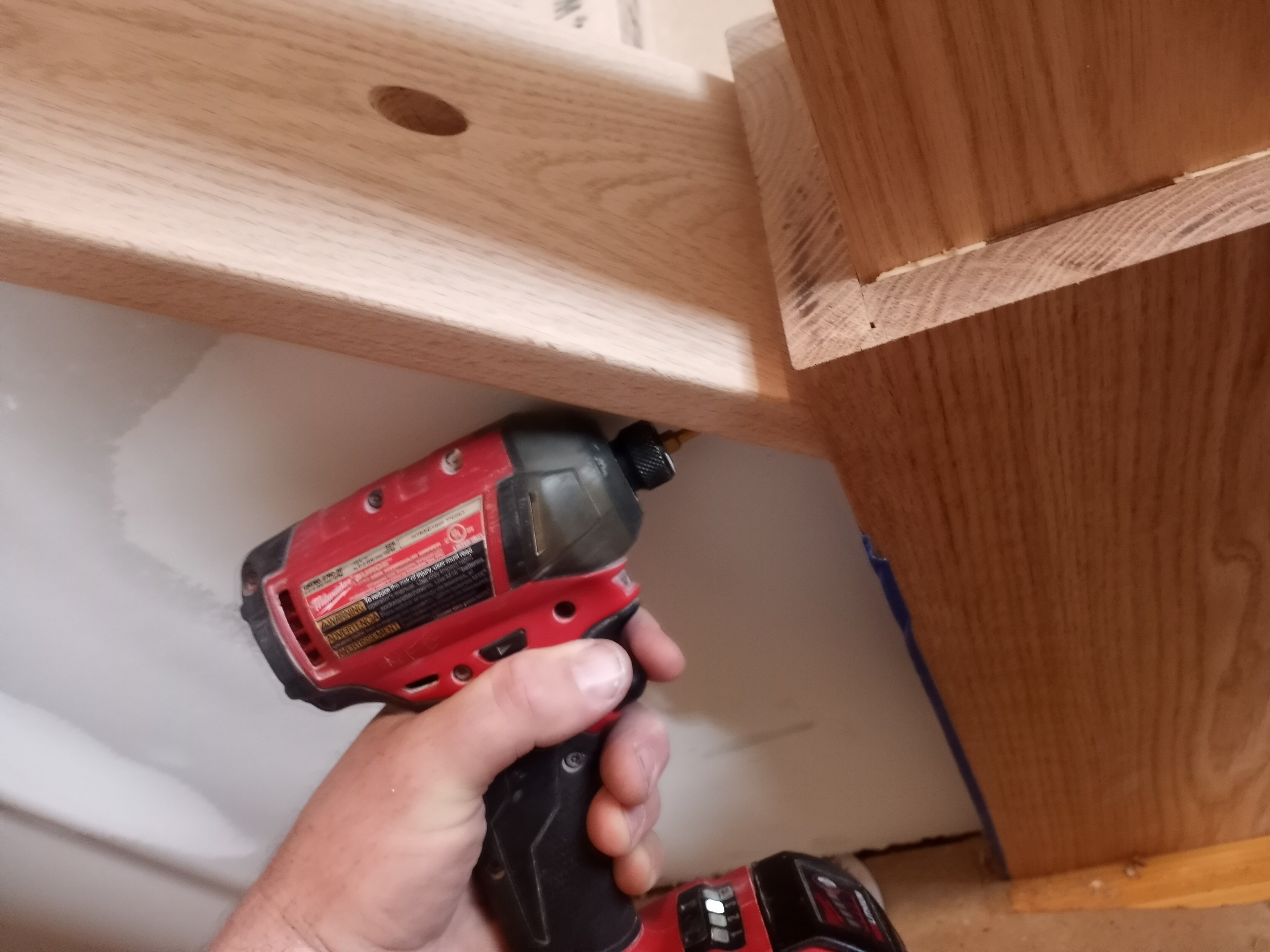
Blind fastening the rake-wall cap is straightforward. I toenailed the wall cap to the newal post from below.
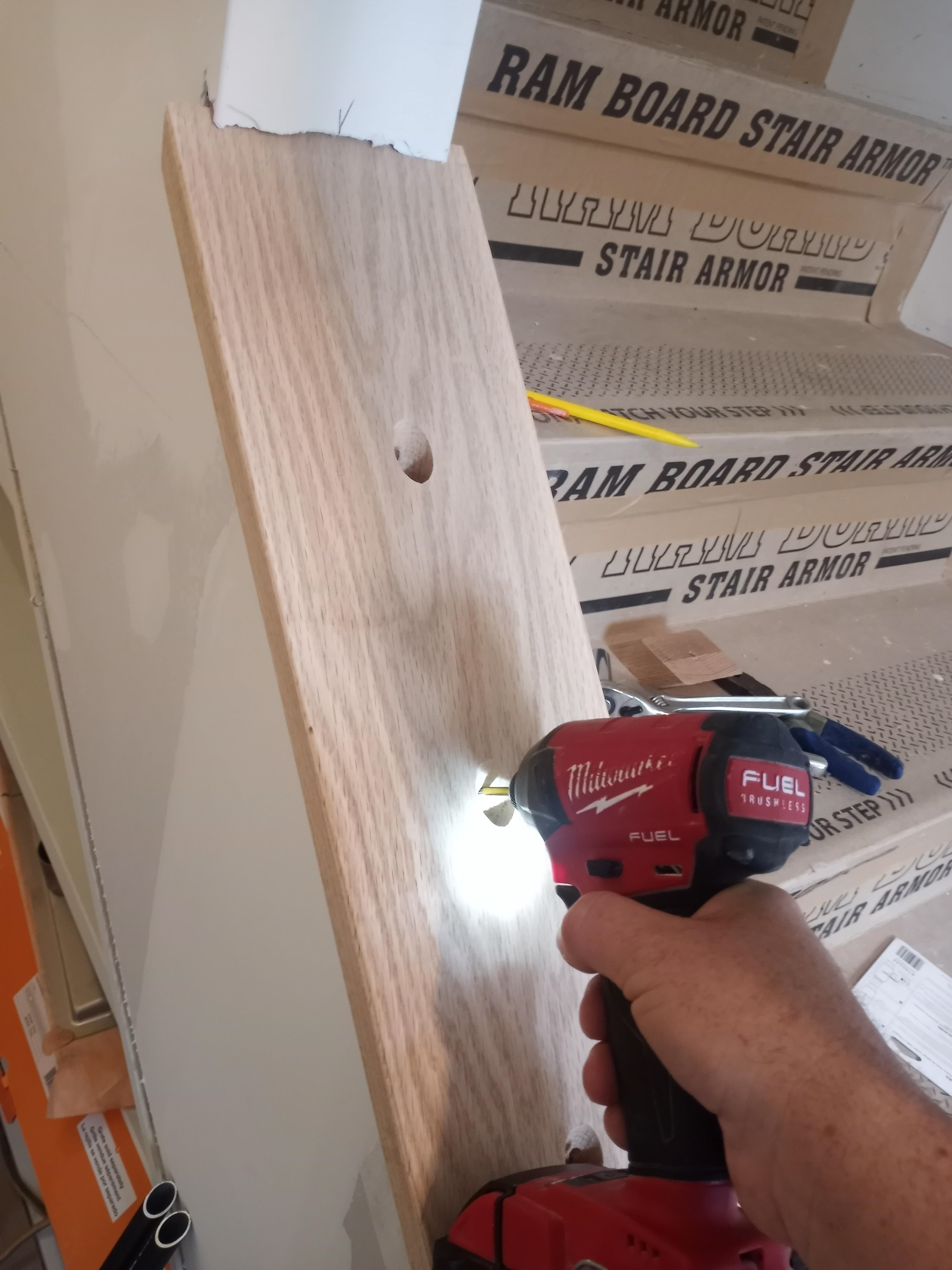
Blind screwing the wall cap to the framing through the backside of the baluster holes will hold the oak flat to the framing.
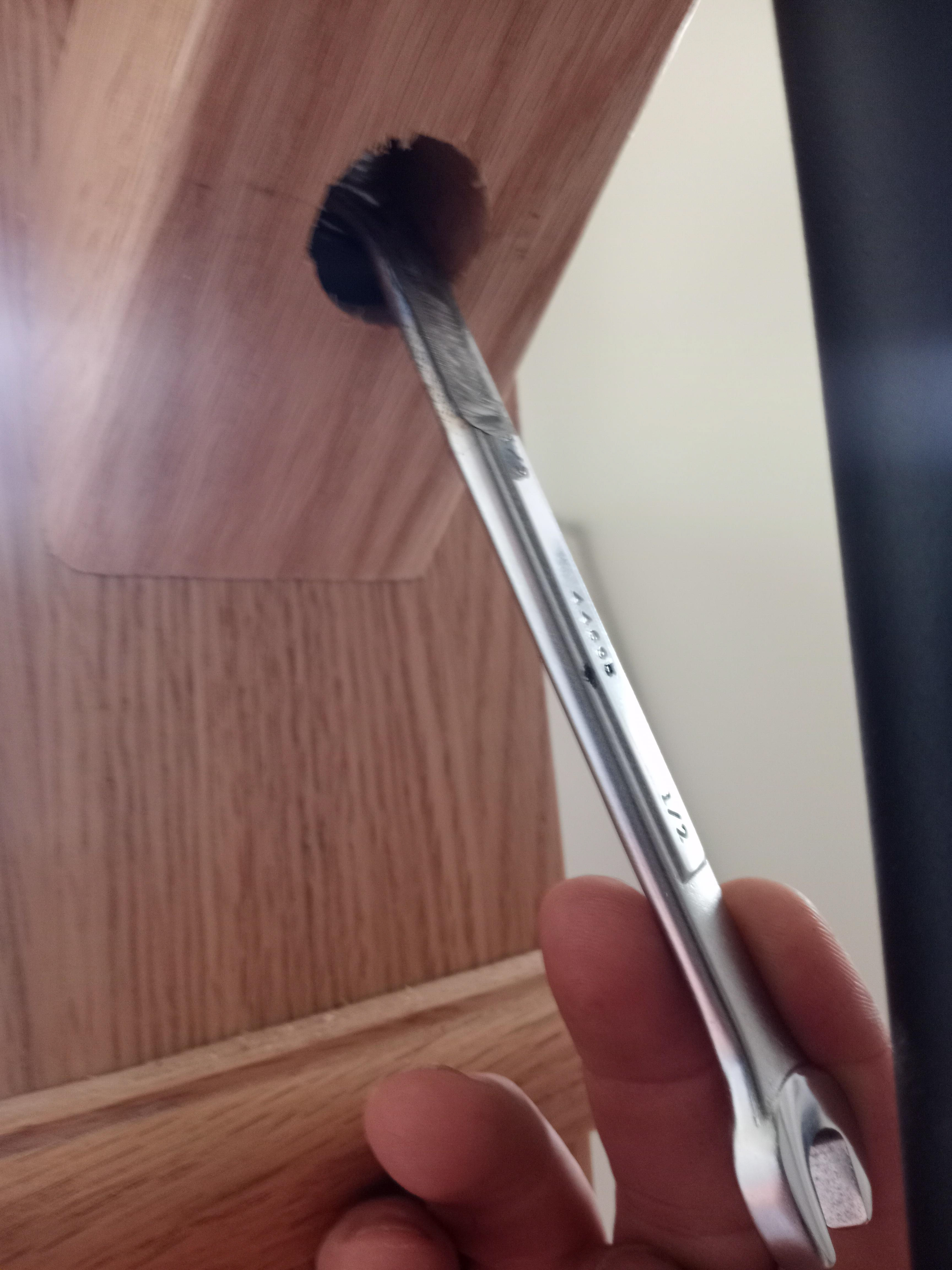
I attached the handrail to the newel post with the hanger bolt. I'll toenail and plug the handrail to the wall from above. I'll also plug the hole that I'm using to tighten the nut on the hanger bolt.
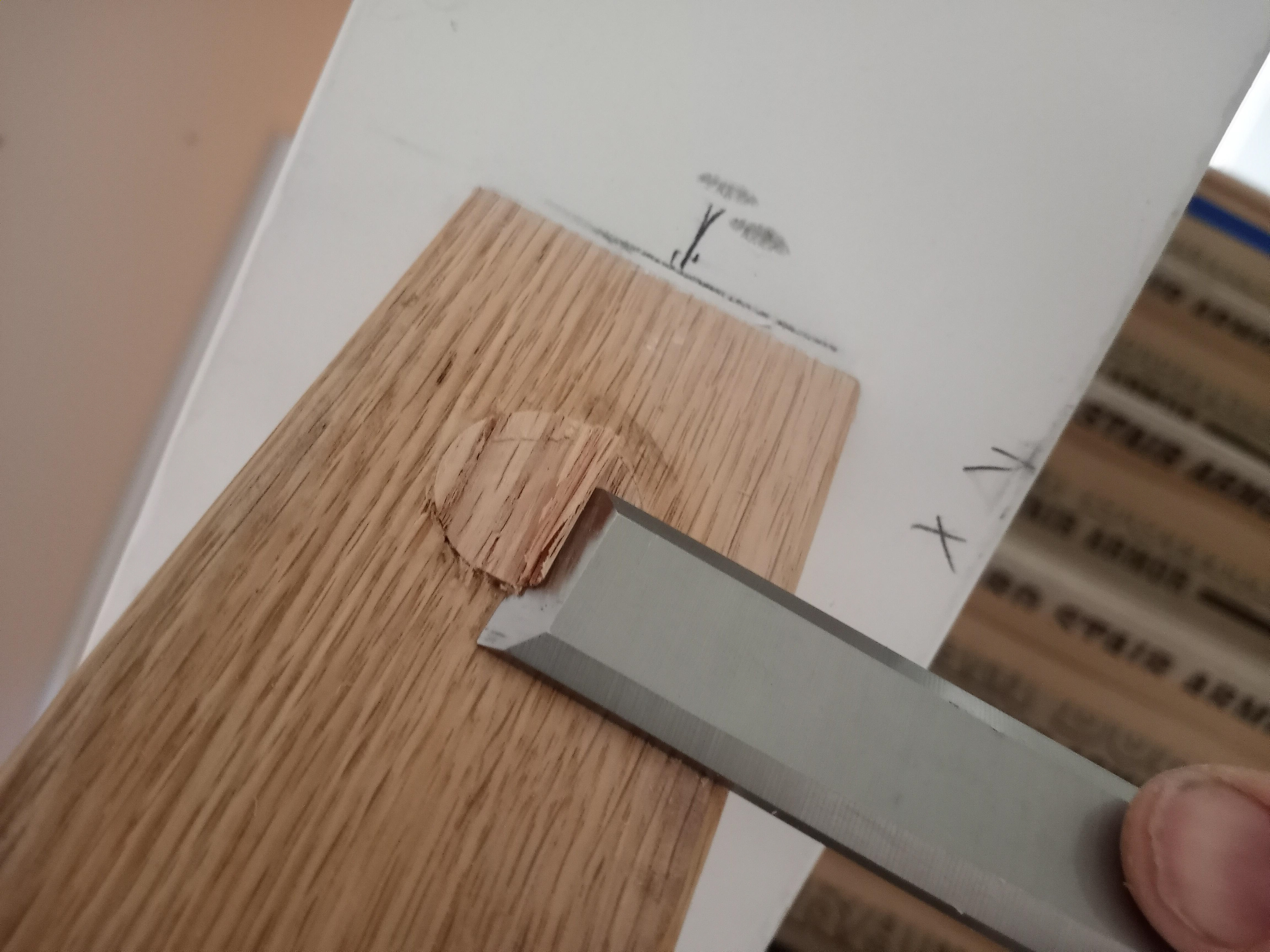
I trimmed the plugs flush with a sharp chisel.
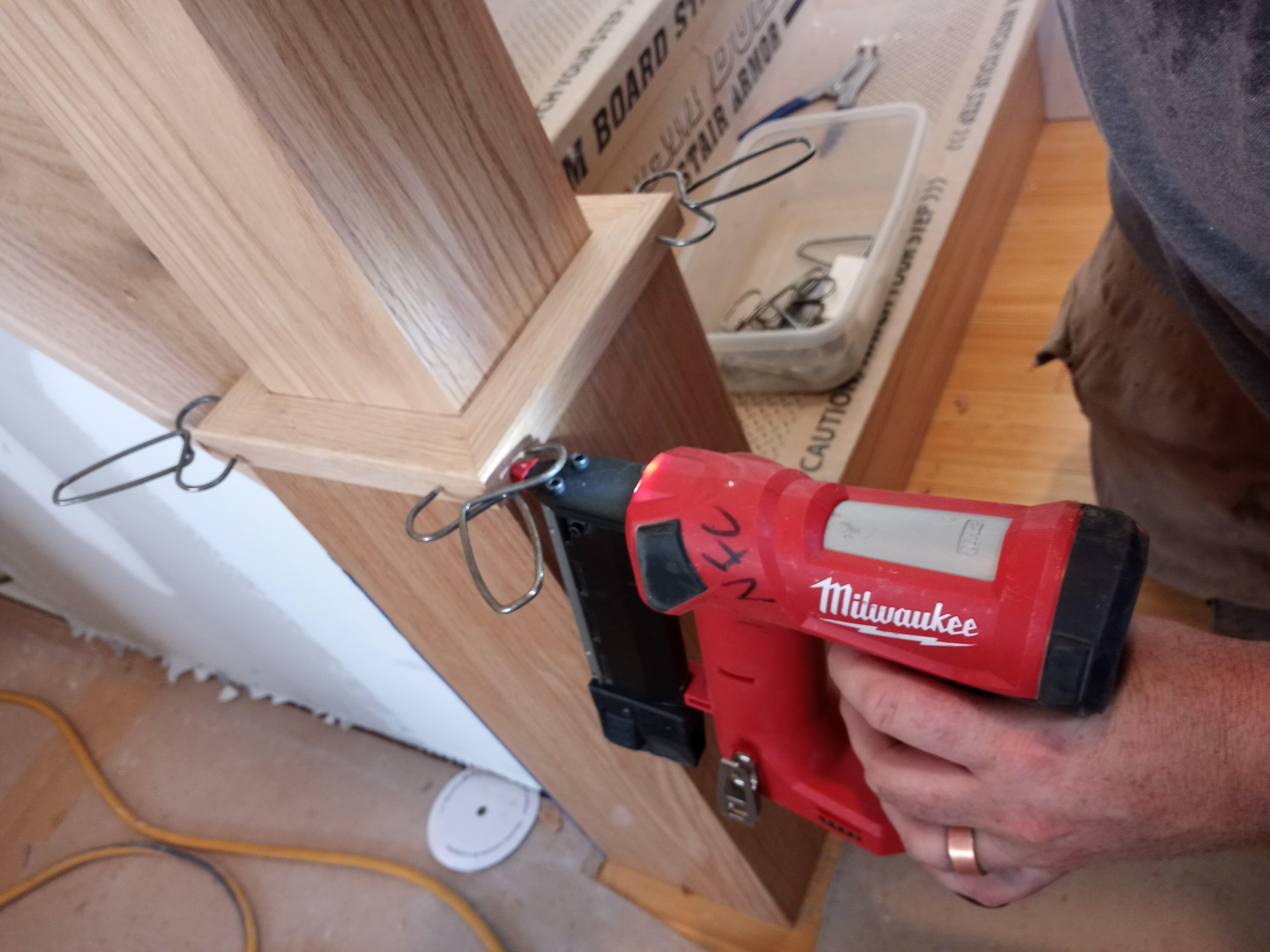
The finishing touches include pin nailing some little custom trim pieces to the newel at the top of the sleeve, floating out the existing wavy wall to hide the gap between the stringer and the sheetrock, filling some fastener holes, cutting and installing a graspable handrail. I'll leave it to the painter to apply the final coat of polyurethane.
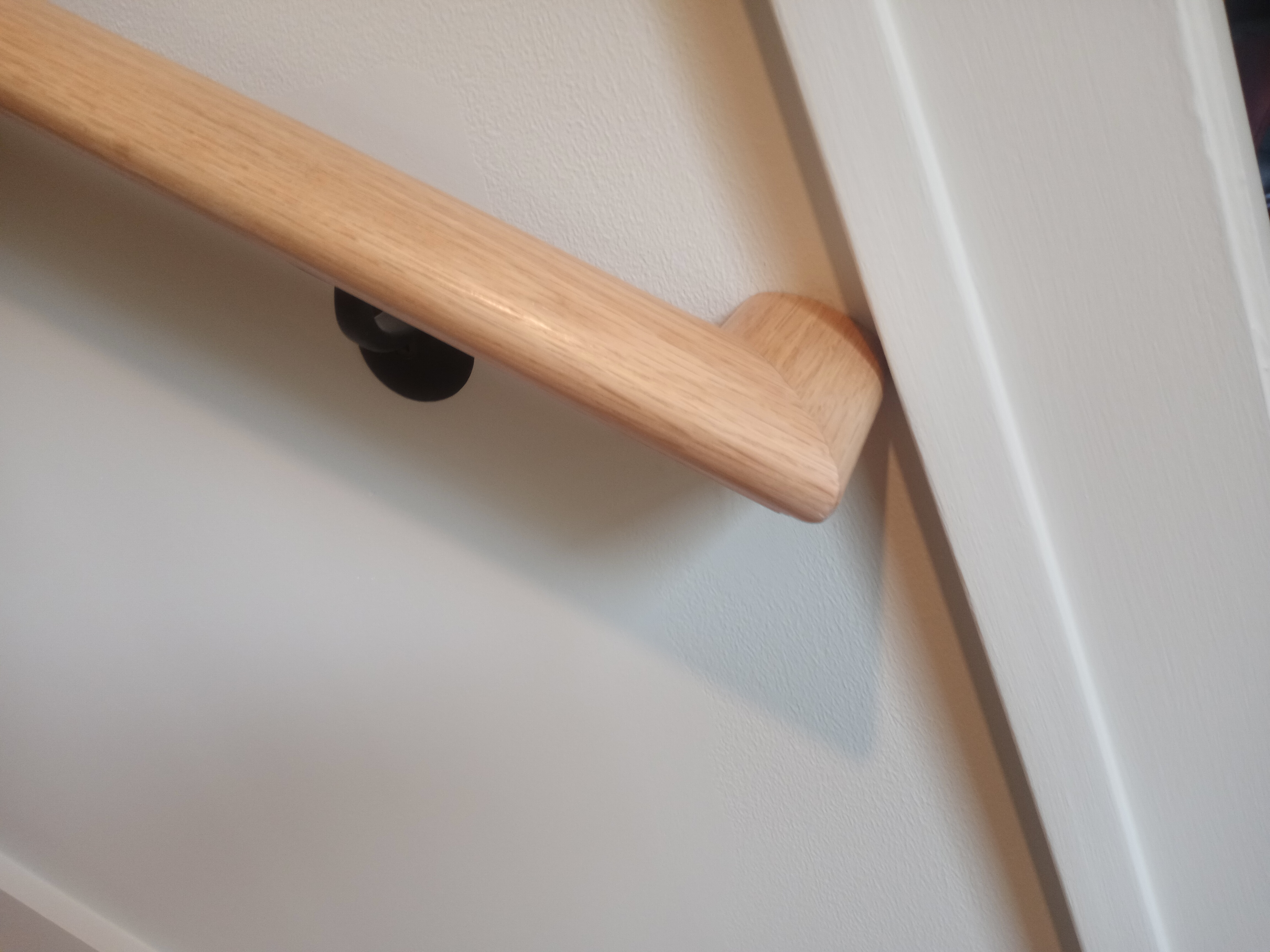
I used the domino jointer and some glue to return the handrail to the wall.
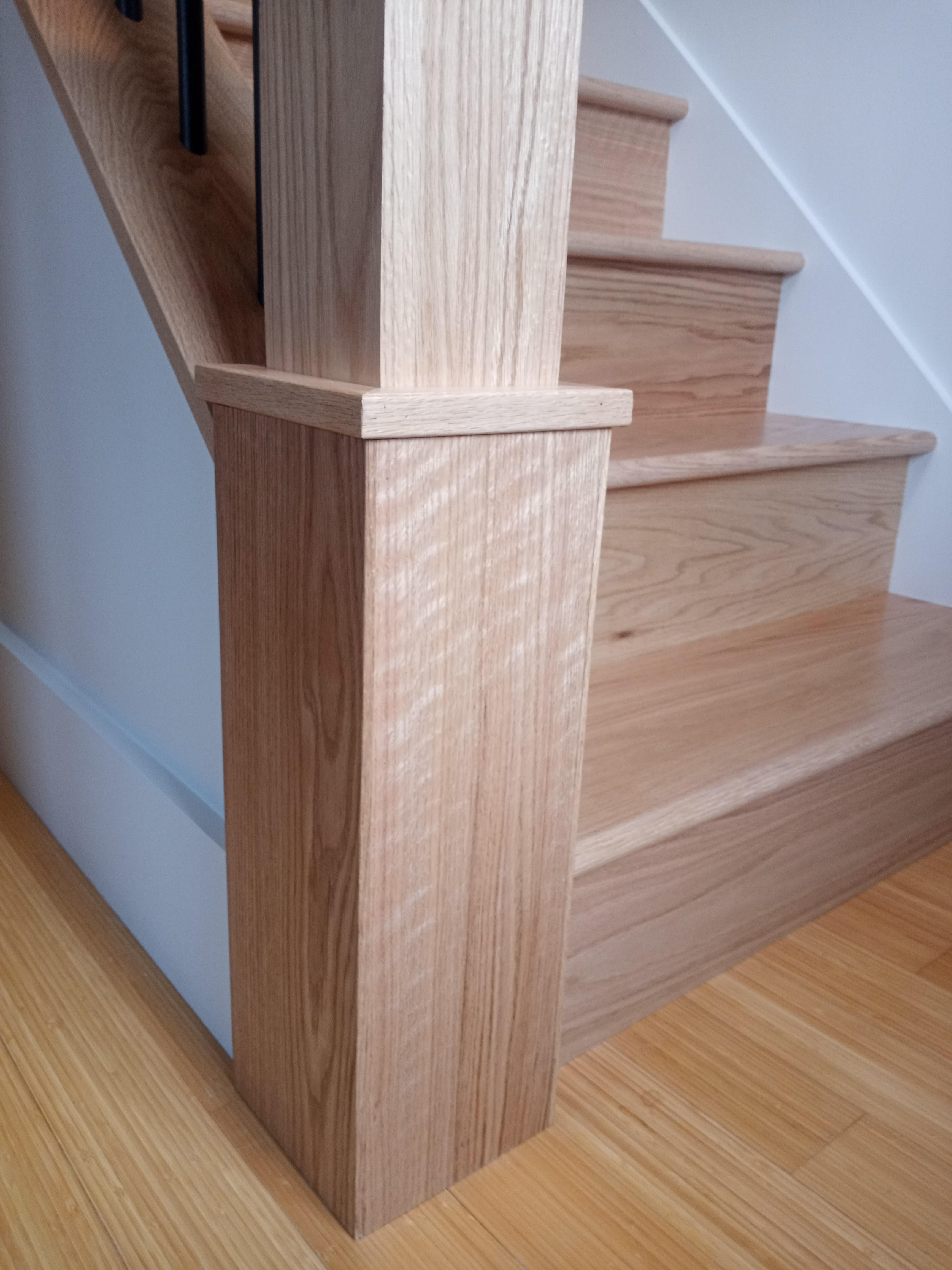
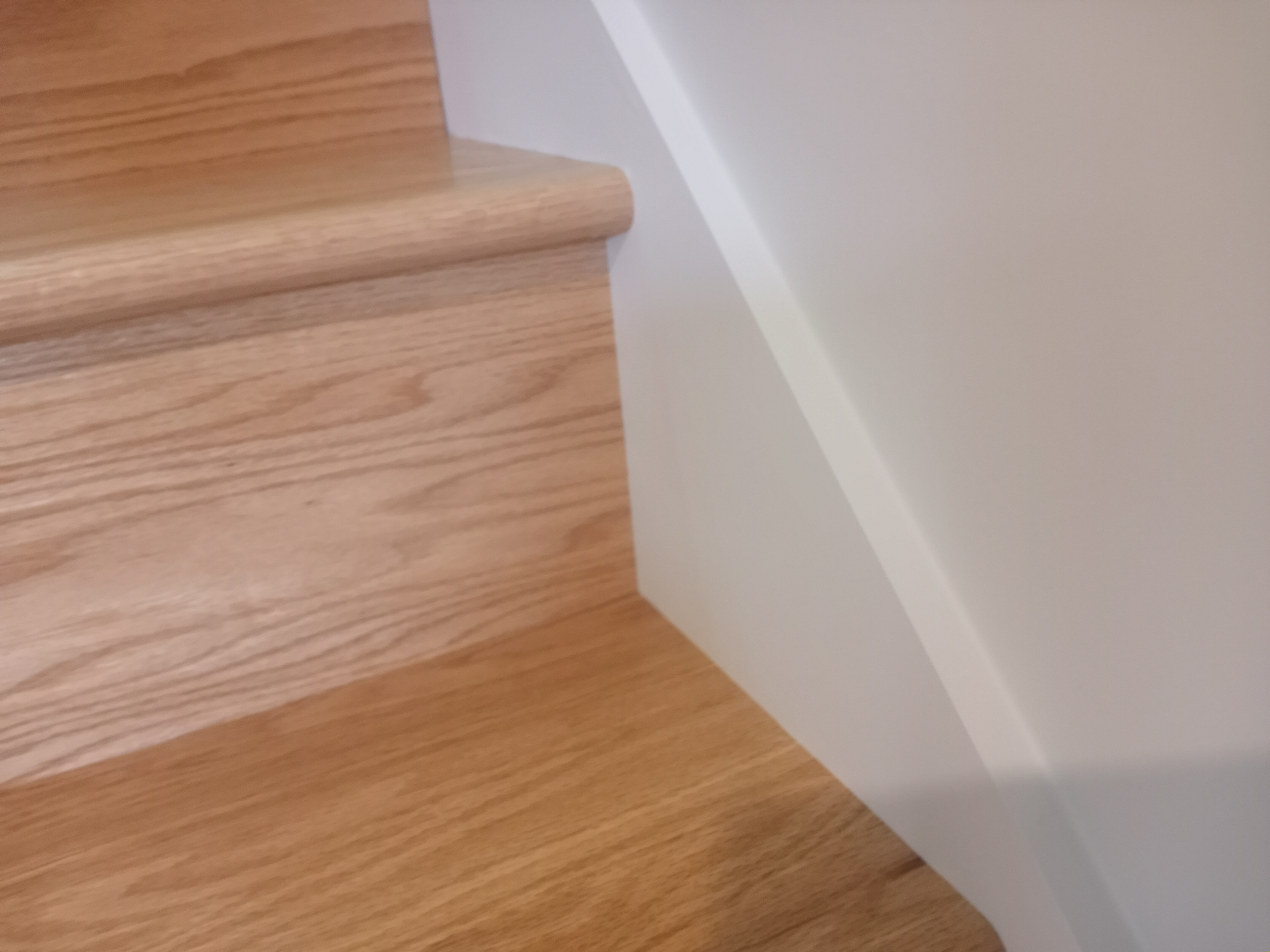
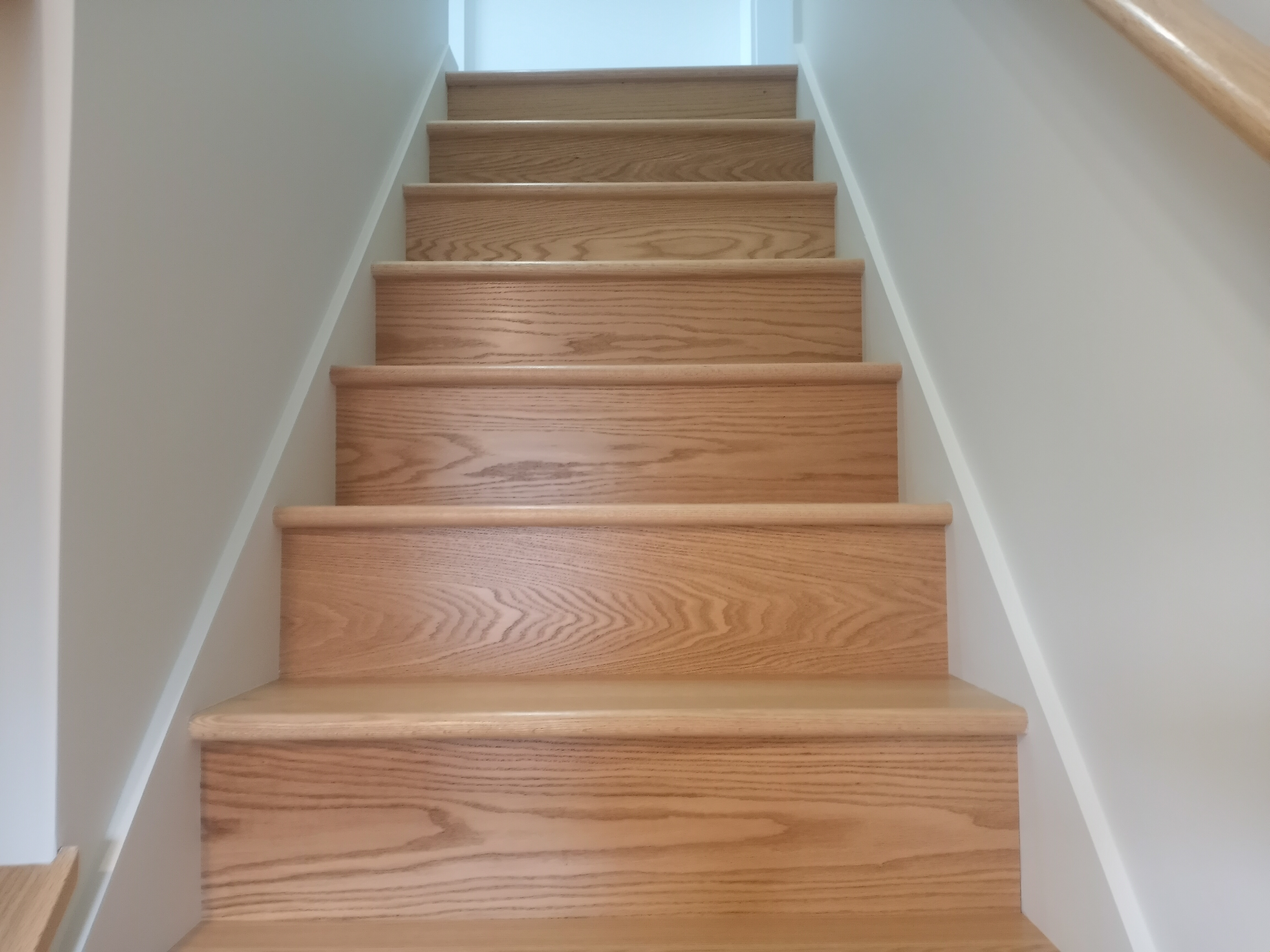
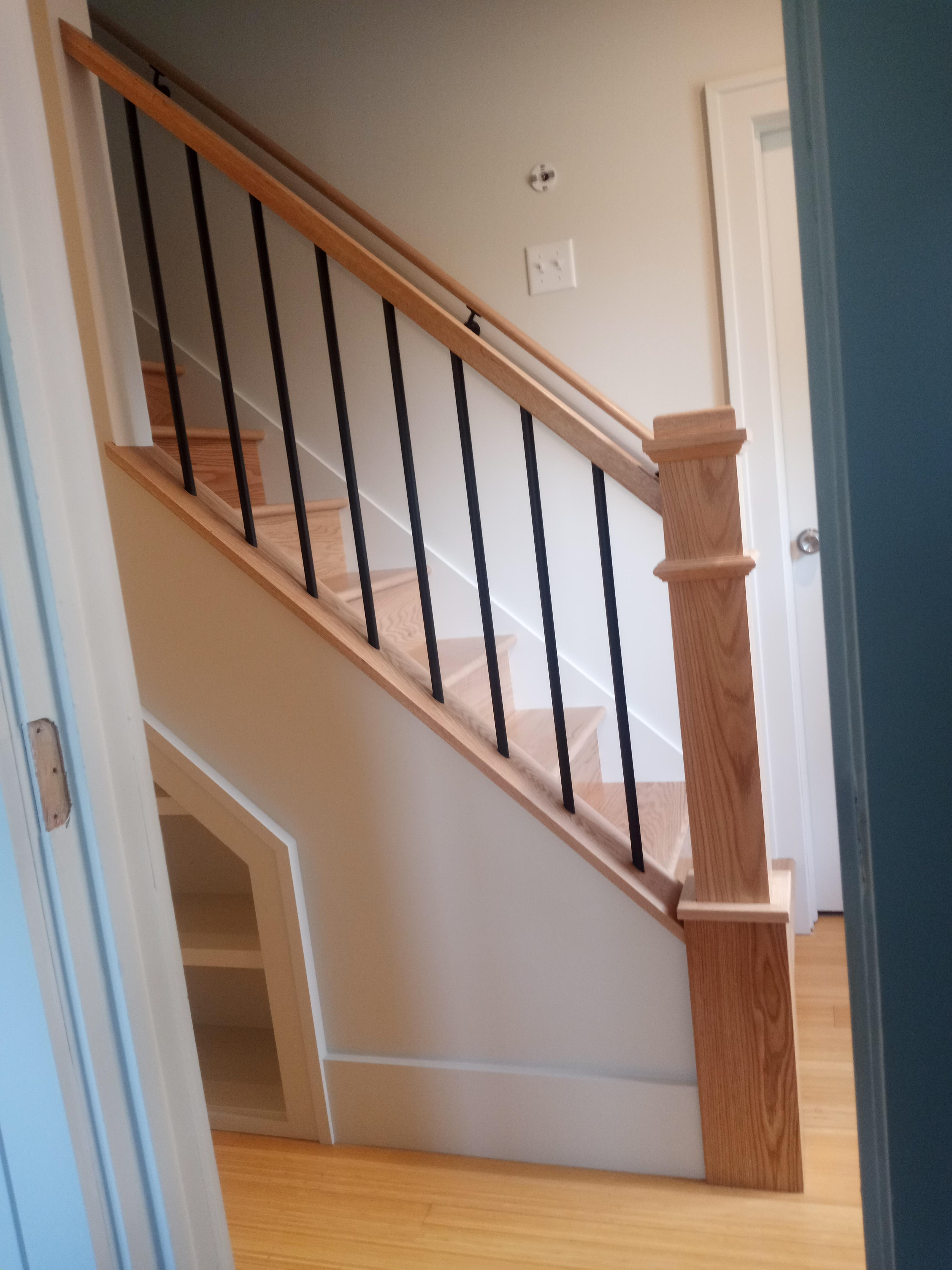
All done. This was a fun project!