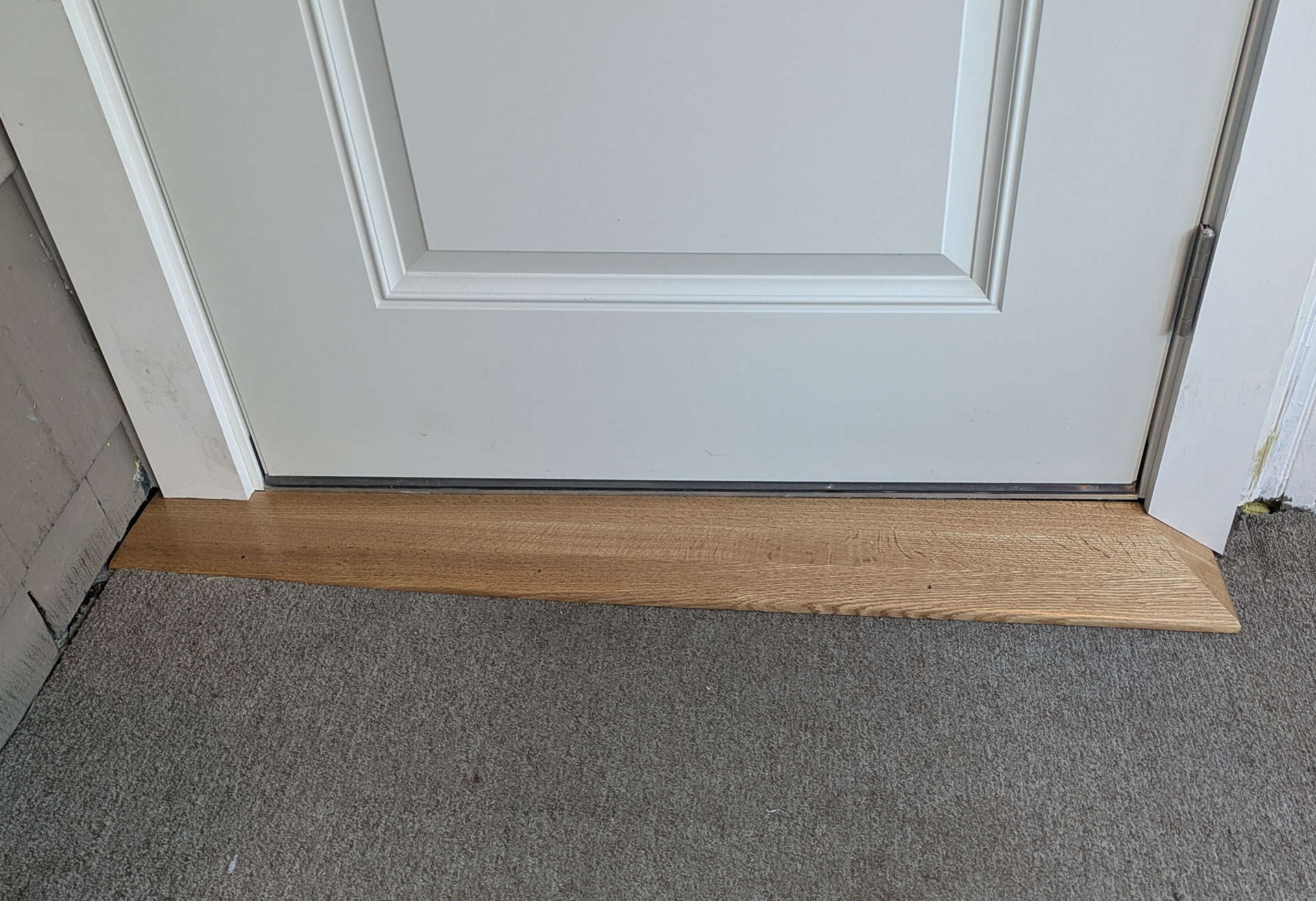
A new oak threshold.
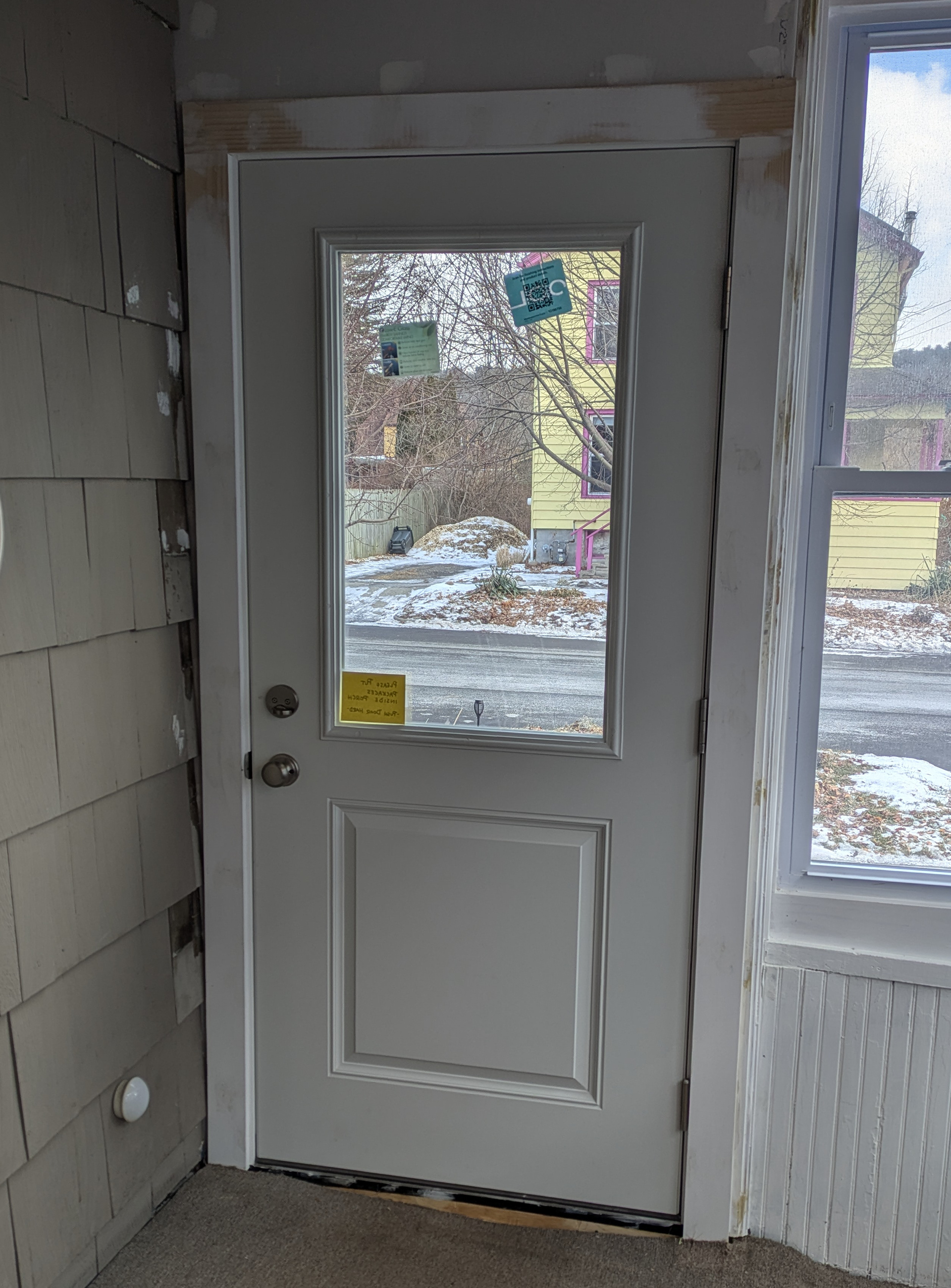
I recently installed a new front door for some folks. The prehung door came with a very thin ADA threshold.
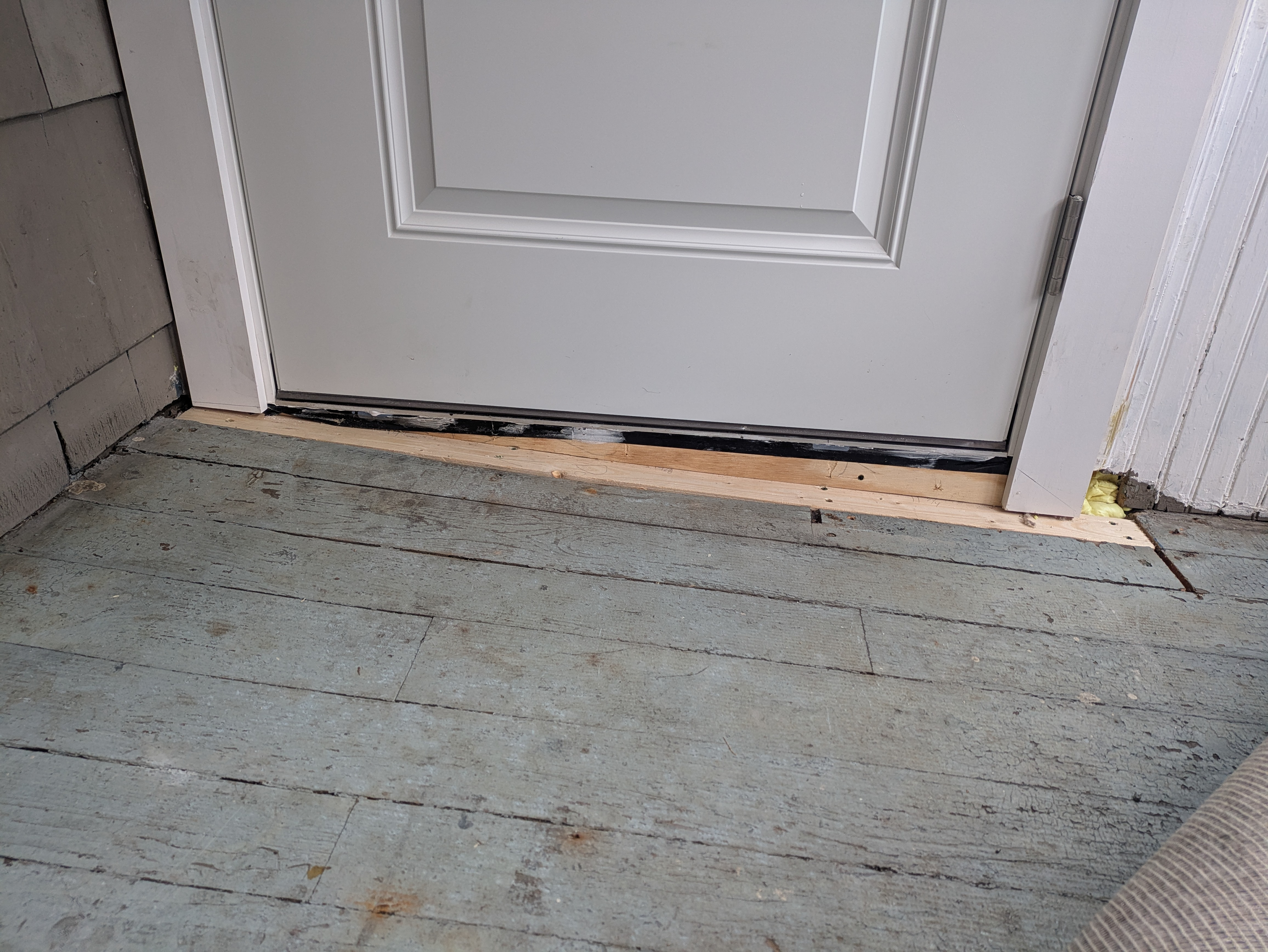
The floor is slanted. There’s about a 2 ½” drop in the floor from one edge of the door opening to the other. I’ll make an interior threshold to serve as a sort of ramp to prevent the level door threshold from being a trip hazard.
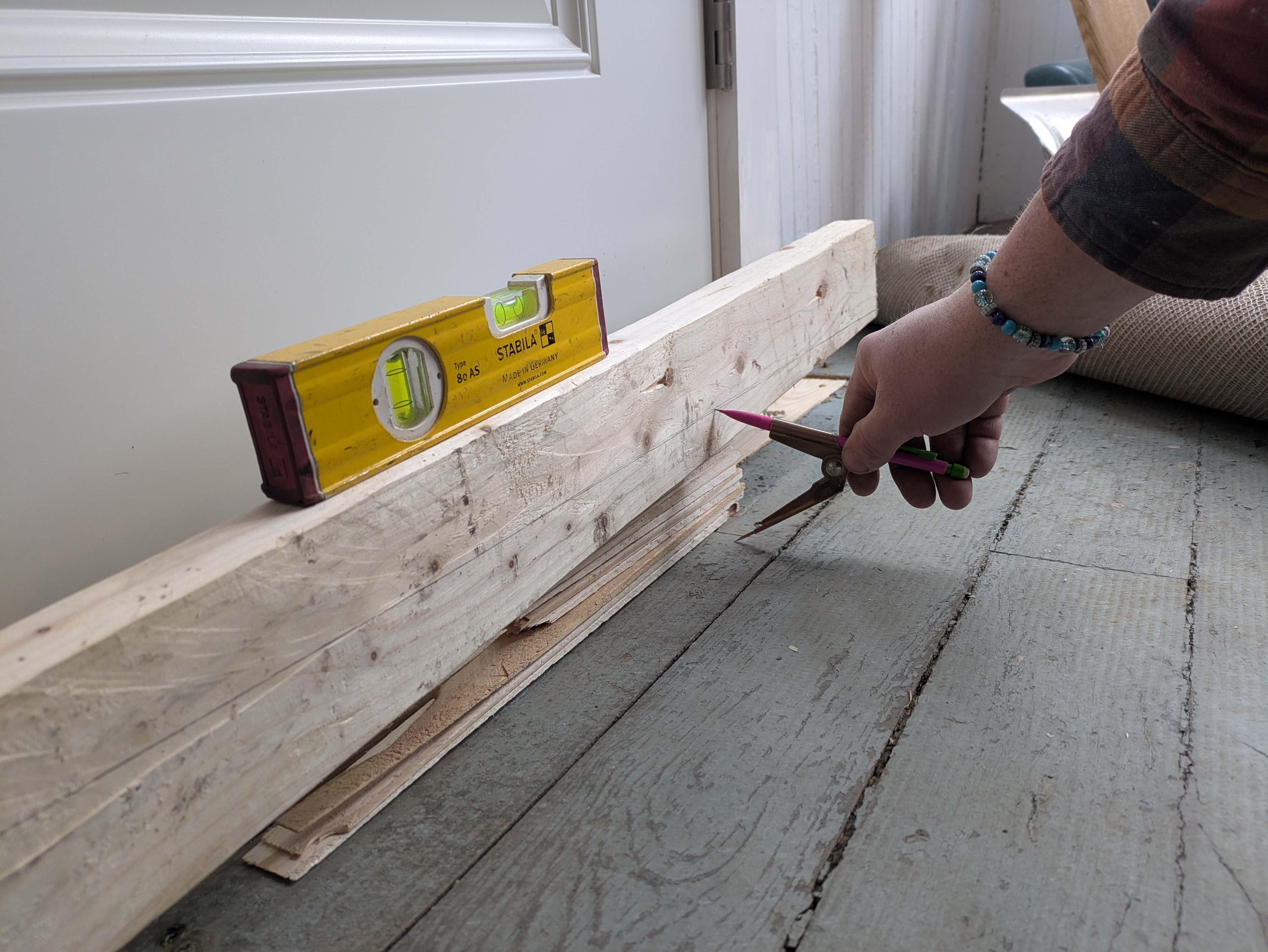
I’m going to make a template from a piece of 2x4 framing lumber that matches the contour of the sagging floor on the bottom and has a flat and level surface on the top with an elevation that comes in just below the ADA threshold. I’ve shimmed the 2x4 level, now I’m scribing the contour of the floor onto the side of the board. I’ll circular saw away the waste and block plane the bottom for a nice fit to the floor.
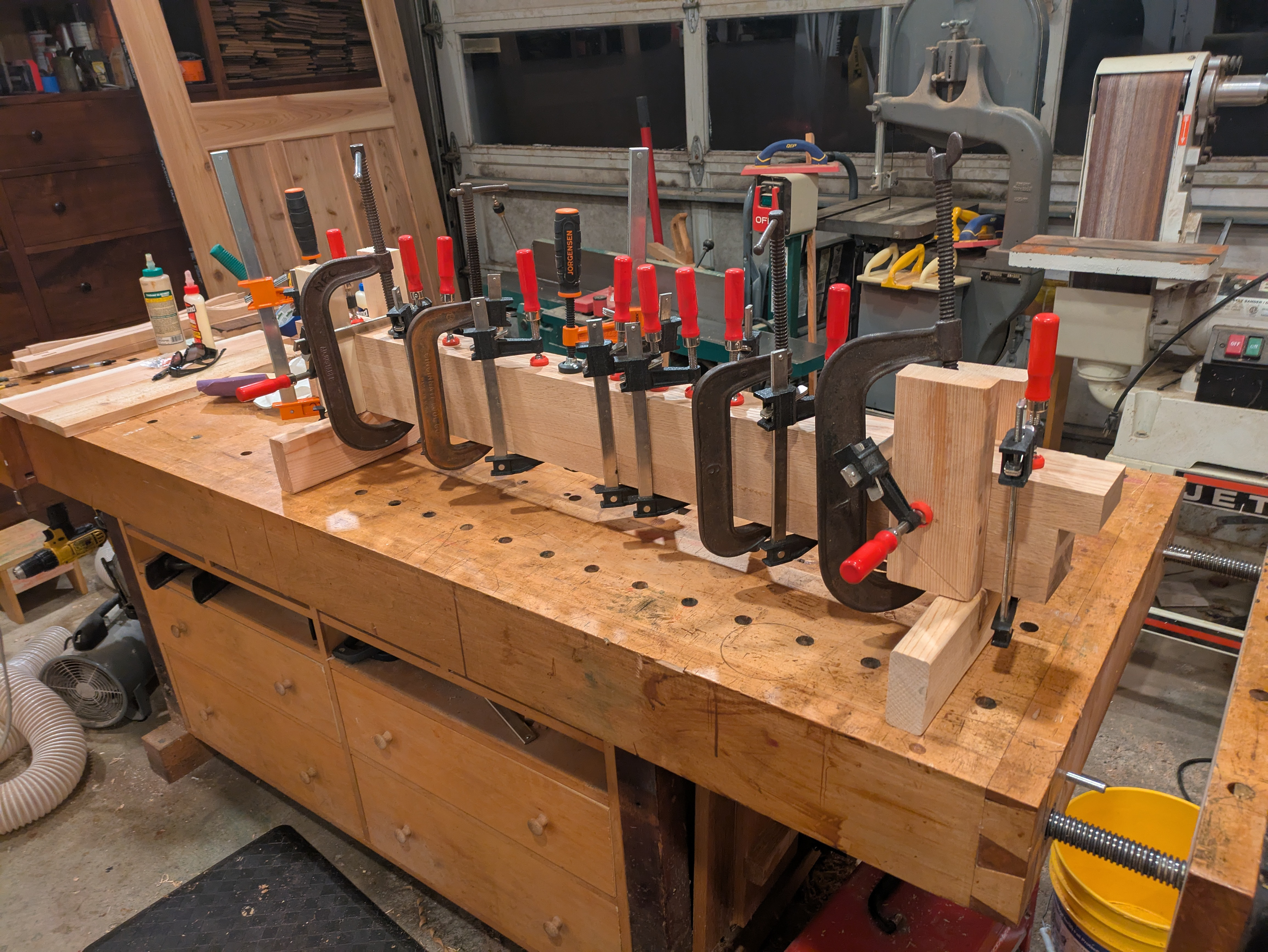
Gluing and clamping a threshold blank from 8/4 red oak. I’m going to make the threshold from a lamination of 3 pieces of about 1 1/2” thick oak that are 3” wide and about 4’ long. The final product will be much more stable than if I were to make such a large threshold from one large piece of wood.
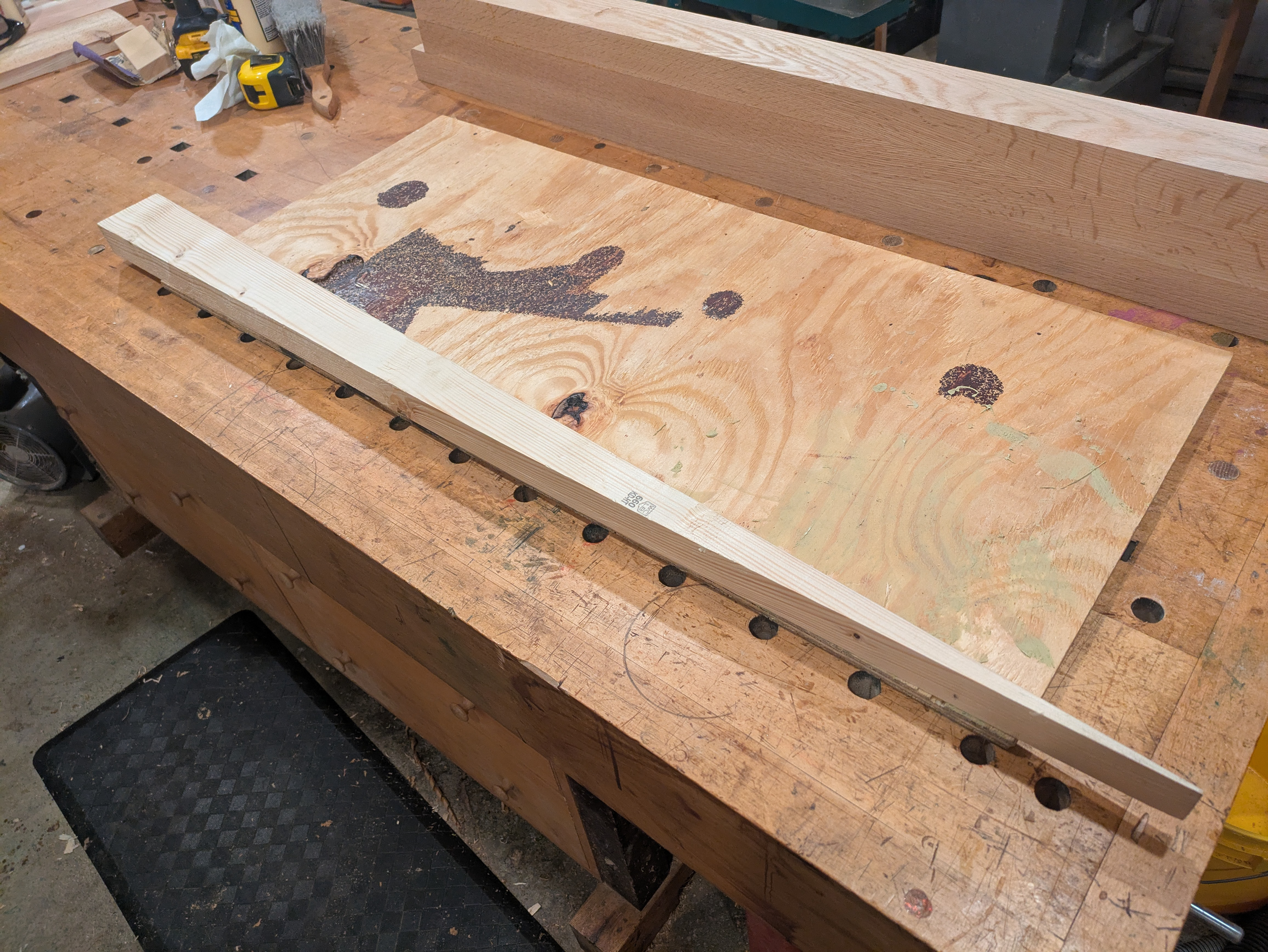
The template is ready to go. I’ve screwed a piece of scrap plywood to the template to keep it from warping.
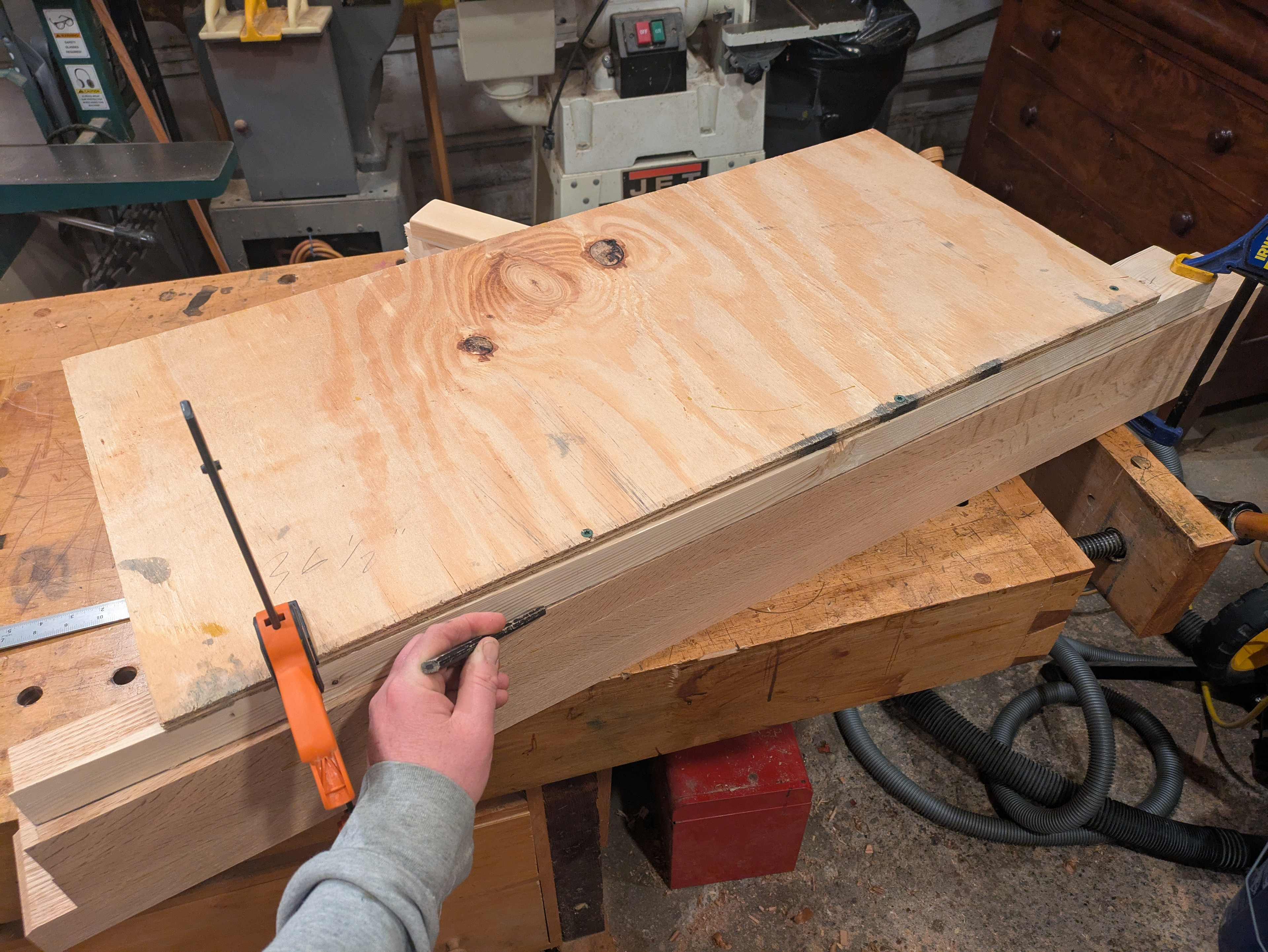
I’m tracing the template onto both sides of the oak threshold blank.
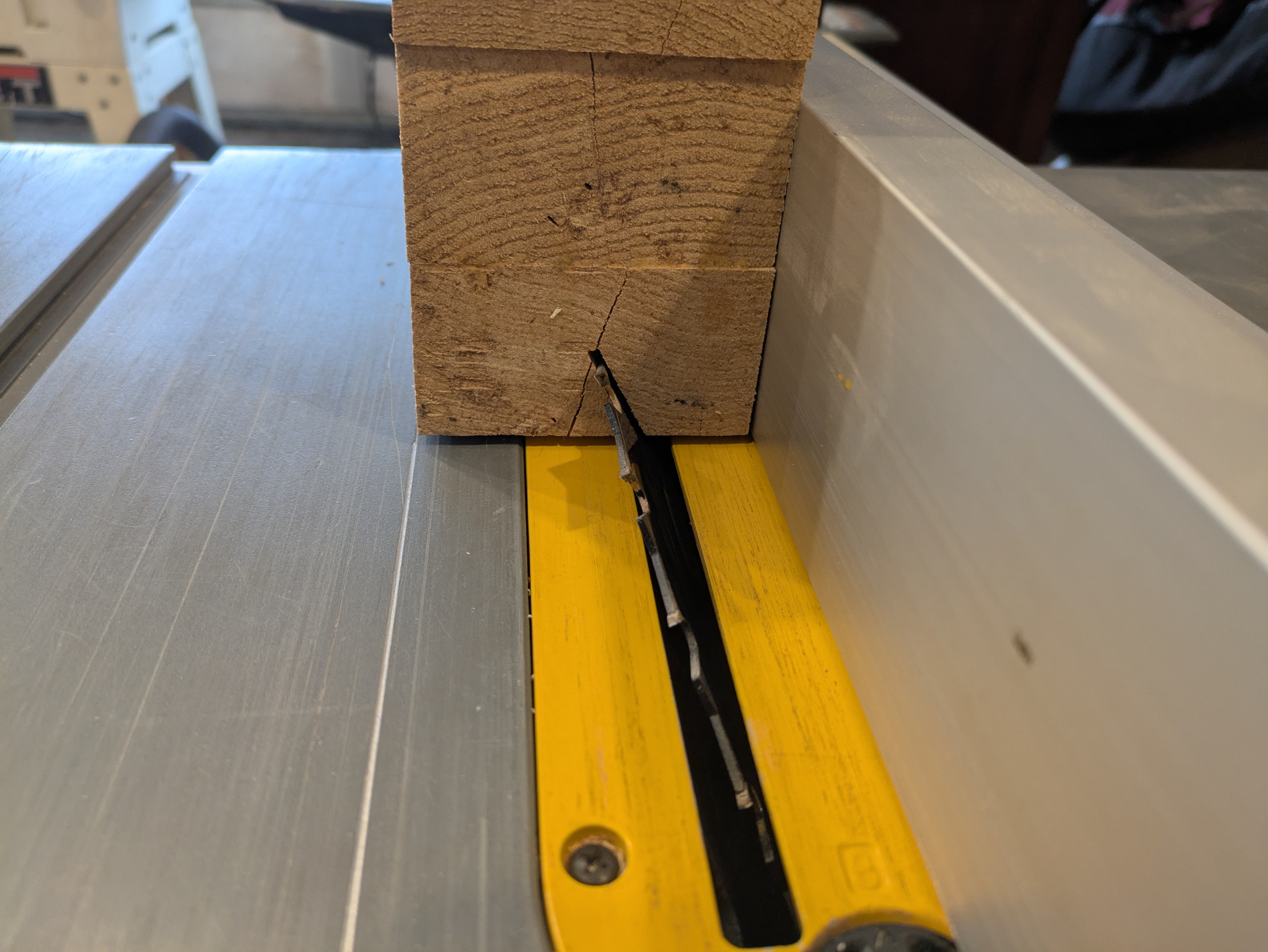
Cutting the bevel of the threshold goes pretty quickly with a few progressively deeper cuts on the table saw. The thin side of the threshold is facing down in this photo.
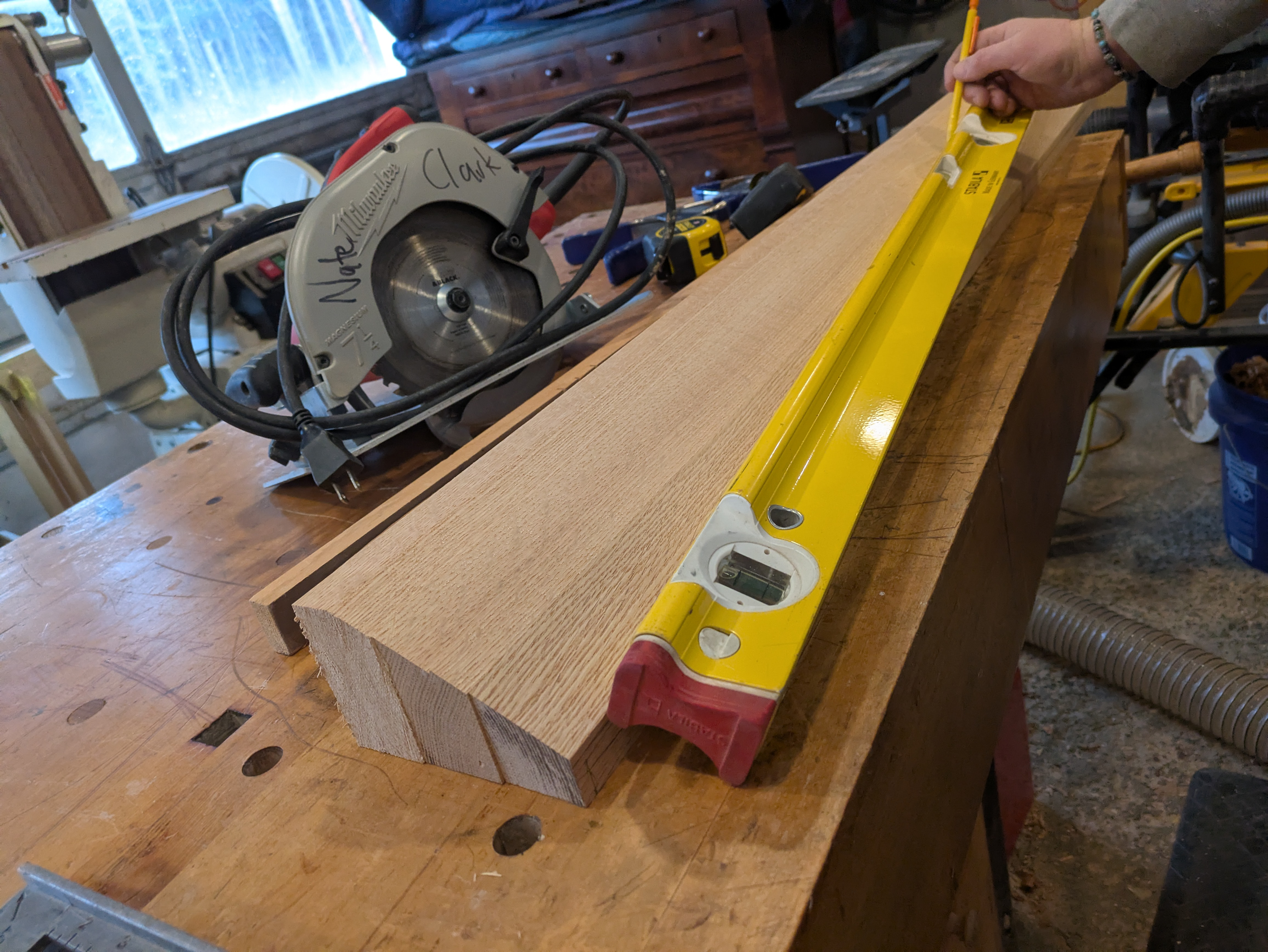
Laying out the center of the curve with a pencil will guide my next cut.
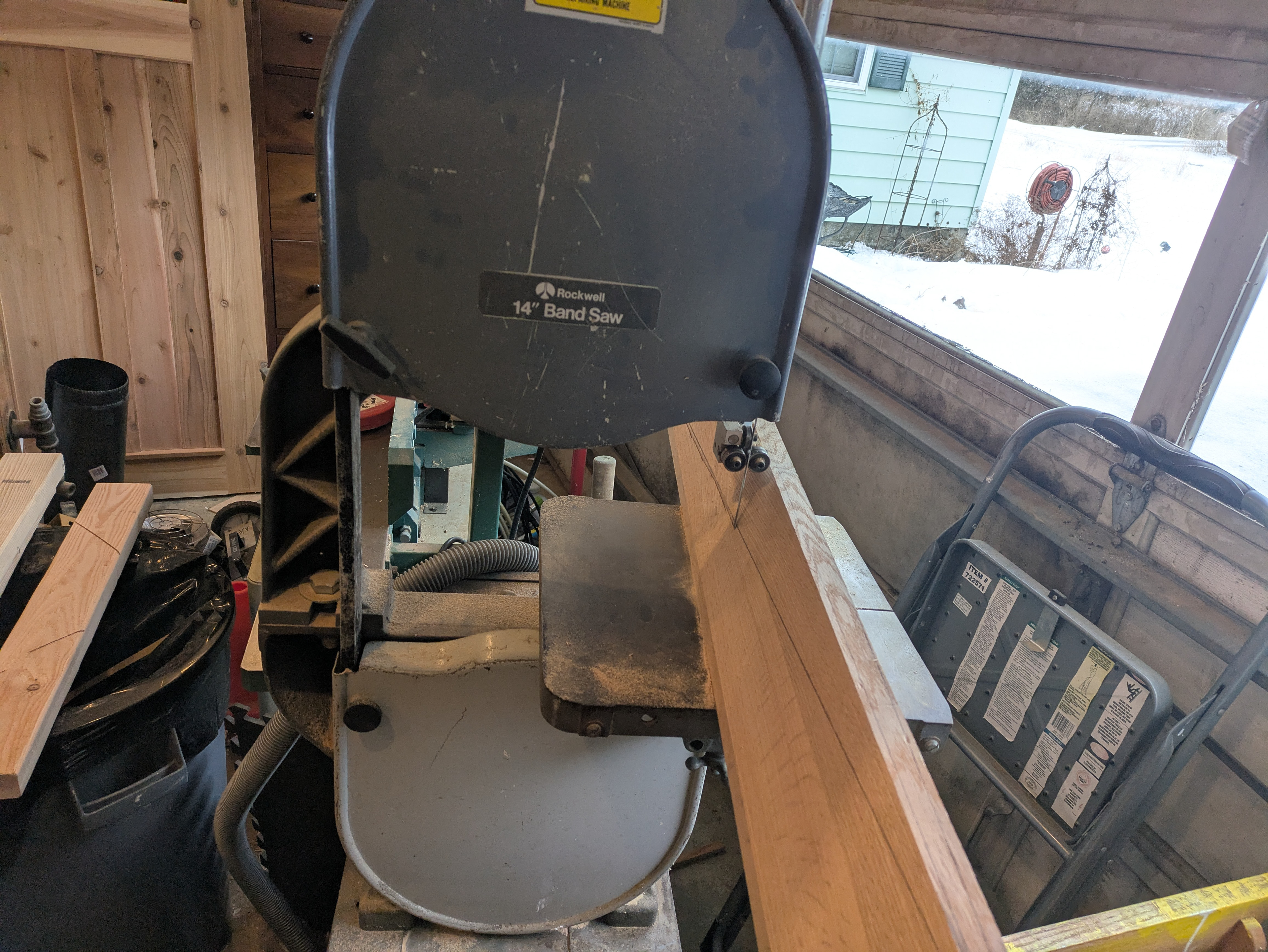
The bandsaw cuts away more waste. I’m following the pencil line that connects the highest point of the threshold with the lowest point of the threshold. In this photo the thick side of the threshold (that will butt up against the door opening) is laying flat on the bed of the bandsaw.

A hand plane helps me sneak up to my layout lines.
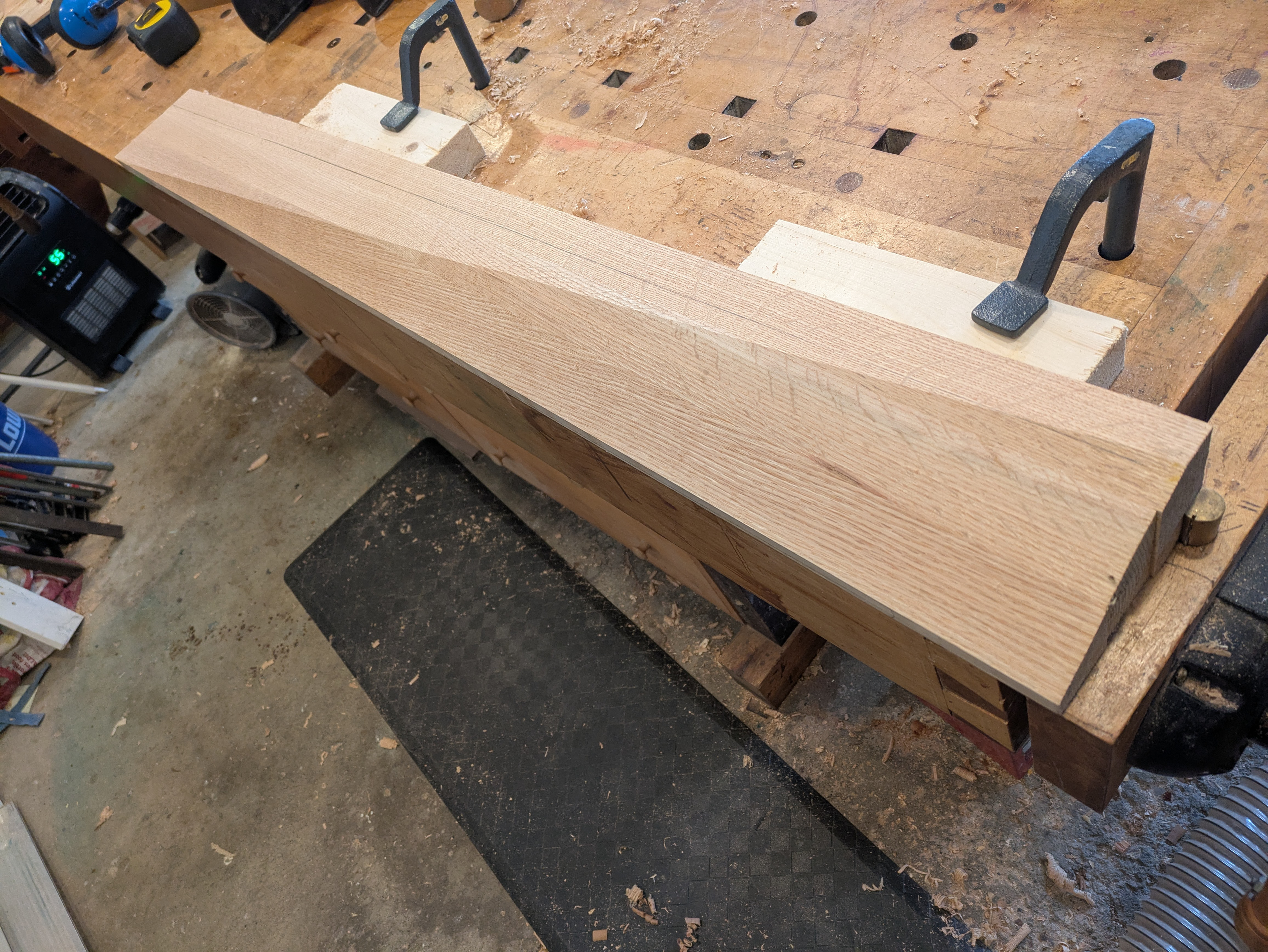
The top of the threshold now has the thin leading edge established as well as the edge that will be against the door that tapers in thickness. My next step will be to remove the waste in the center.
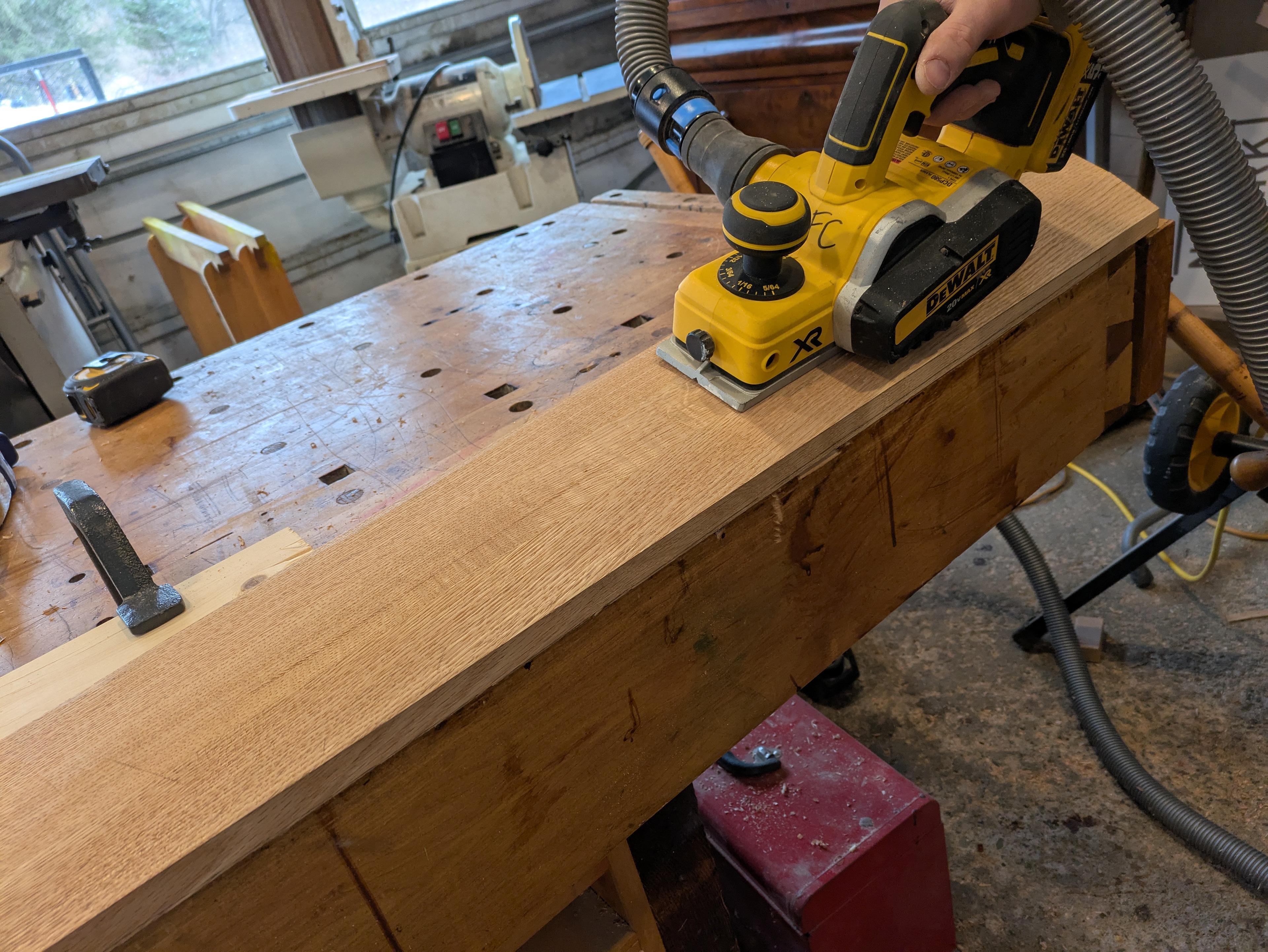
An electric hand planer quickly removes most of the waste. I’ll stop periodically to check my progress with a straightedge laid across the grain. The threshold wants to be flat across the grain and curved along the grain. Next, I’ll clean up the electric planer marks with a smoothing plane.
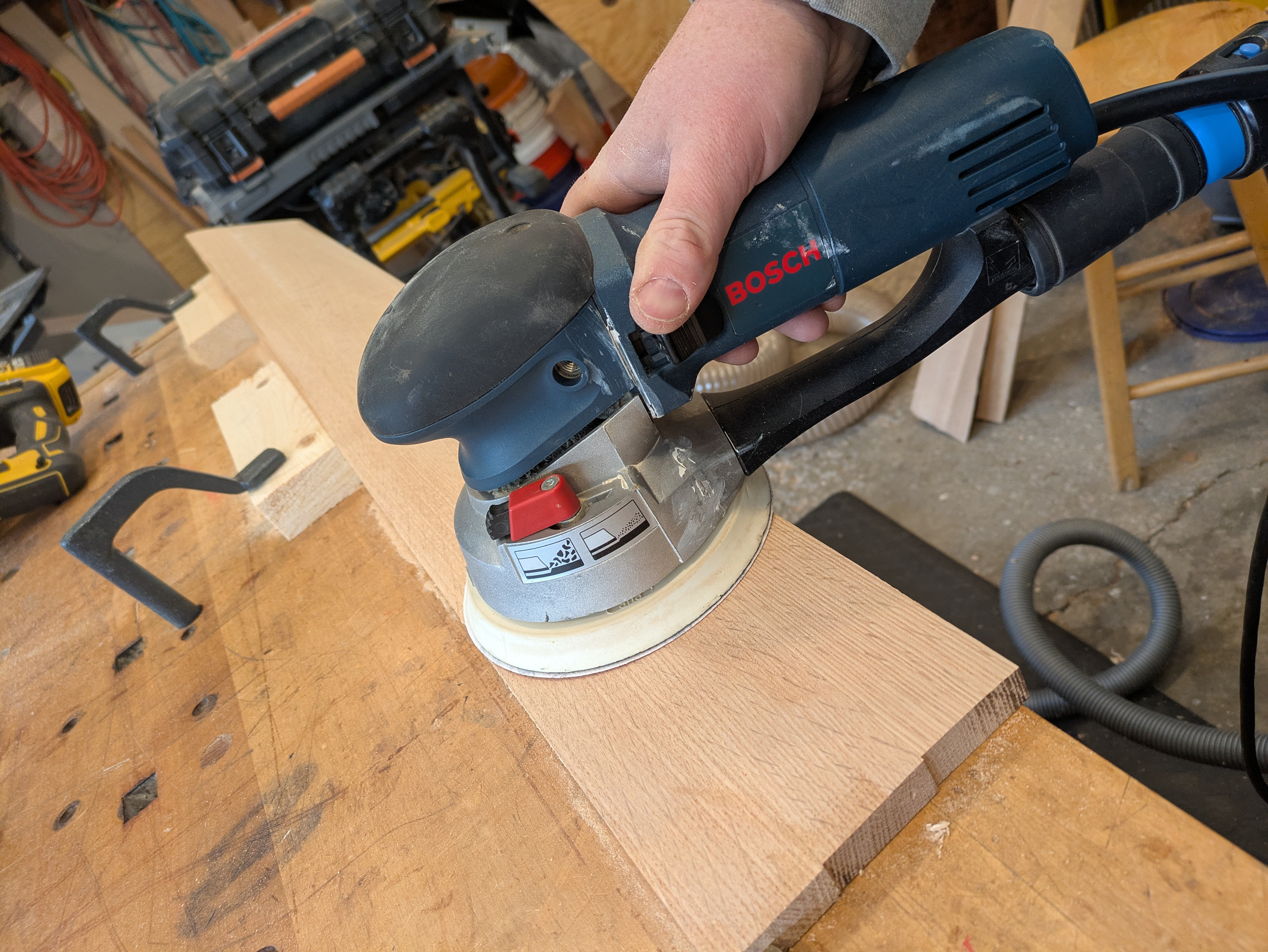
Sanding the planer marks with a large random orbital sander will make for a smooth surface.
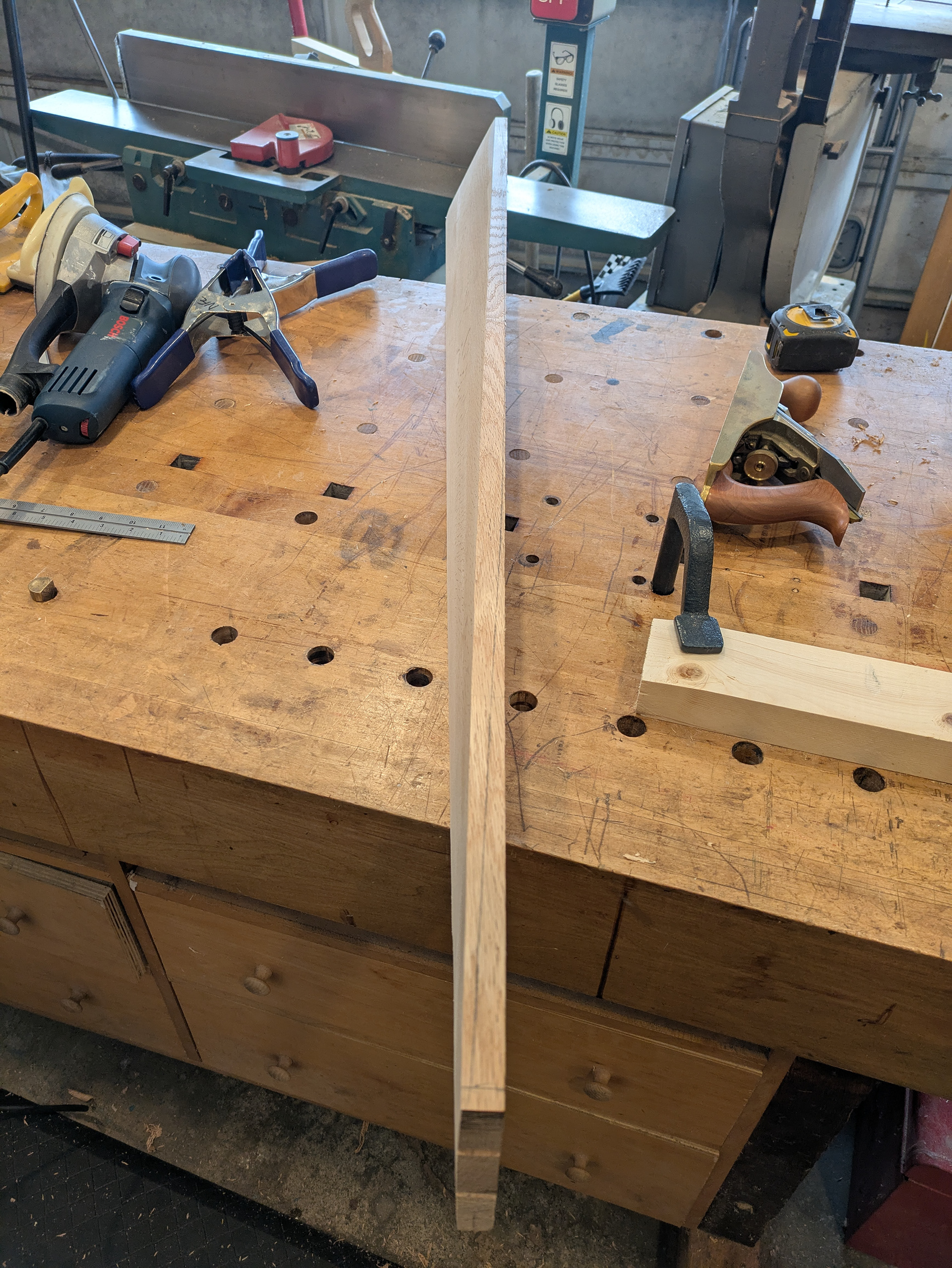
The top of the threshold is just about done. With the threshold standing on it’s back edge on the workbench you can see the prominently twisted profile of the top of the threshold.
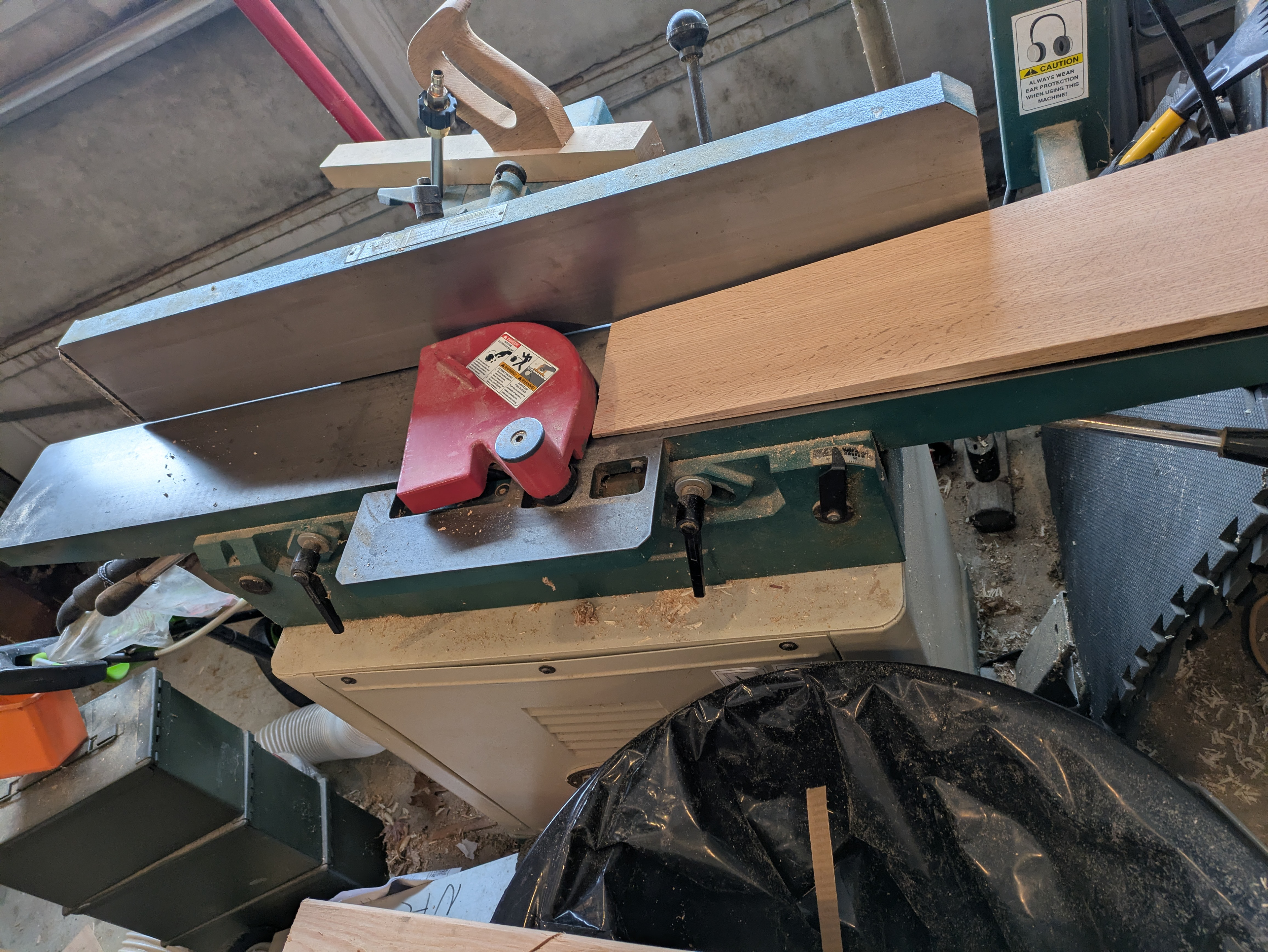
Progressively shallower cuts with the jointer will plane the curved shape of the floor into the bottom of the threshold.
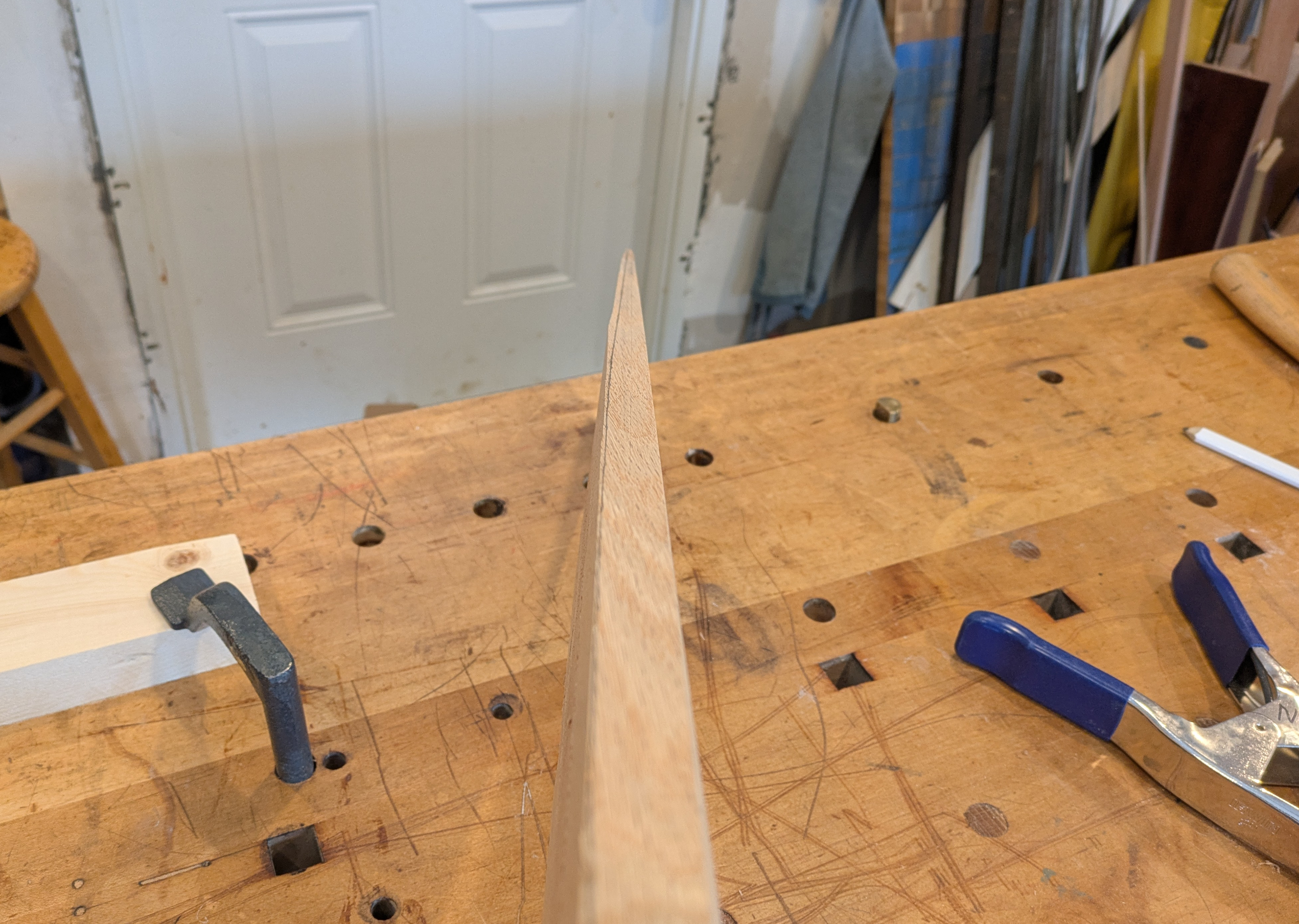
The bottom of the threshold is roughed in. Next I’ll hand plane the bottom of the threshold to the layout lines for a finely-tuned fit.
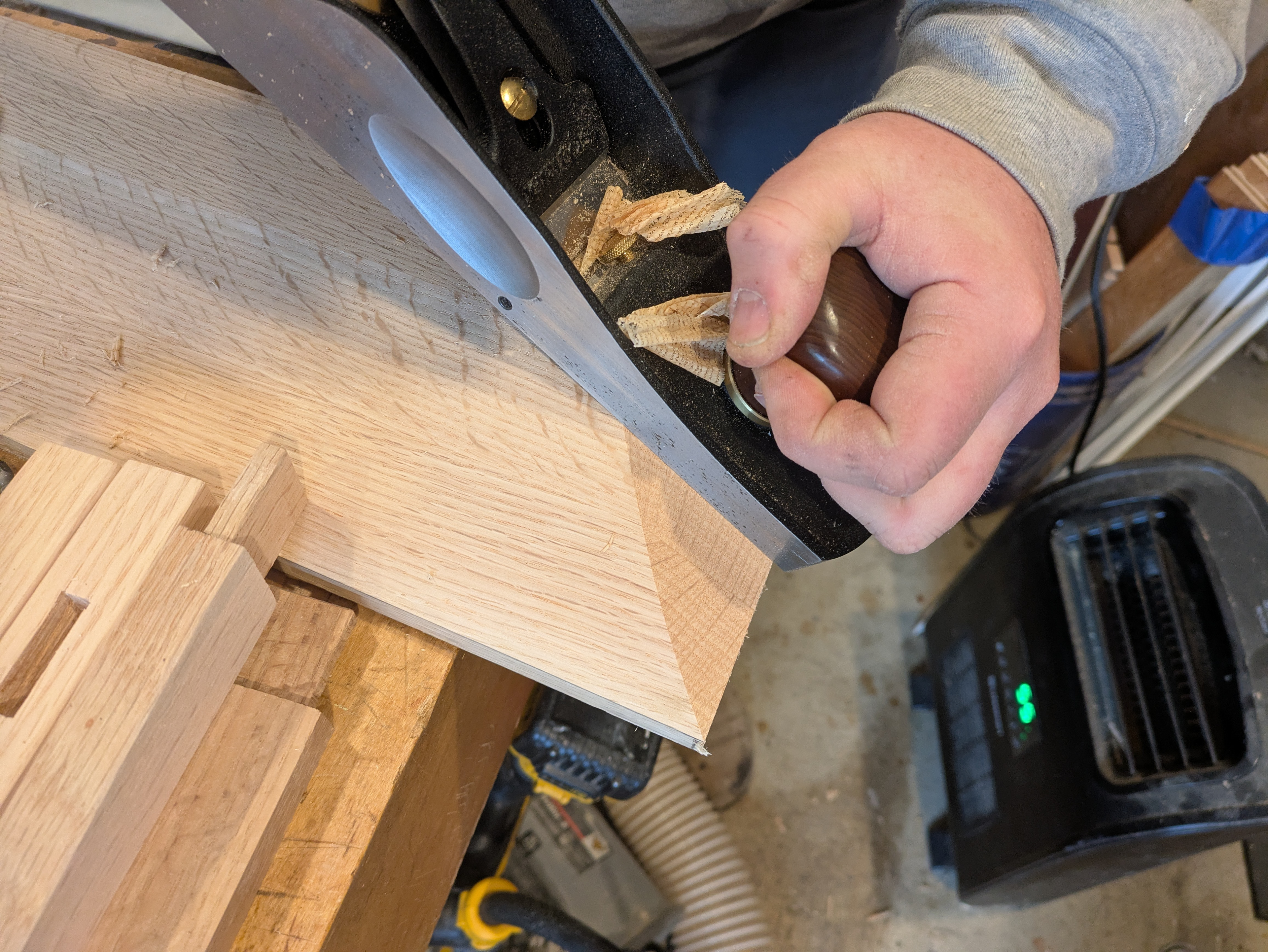
Beveling the edge of the threshold went pretty fast with a tenuous table saw cut. Now I’m cleaning things up with a hand plane. This plane is good for cross grain work as it has an effective cutting angle of 62 degrees.
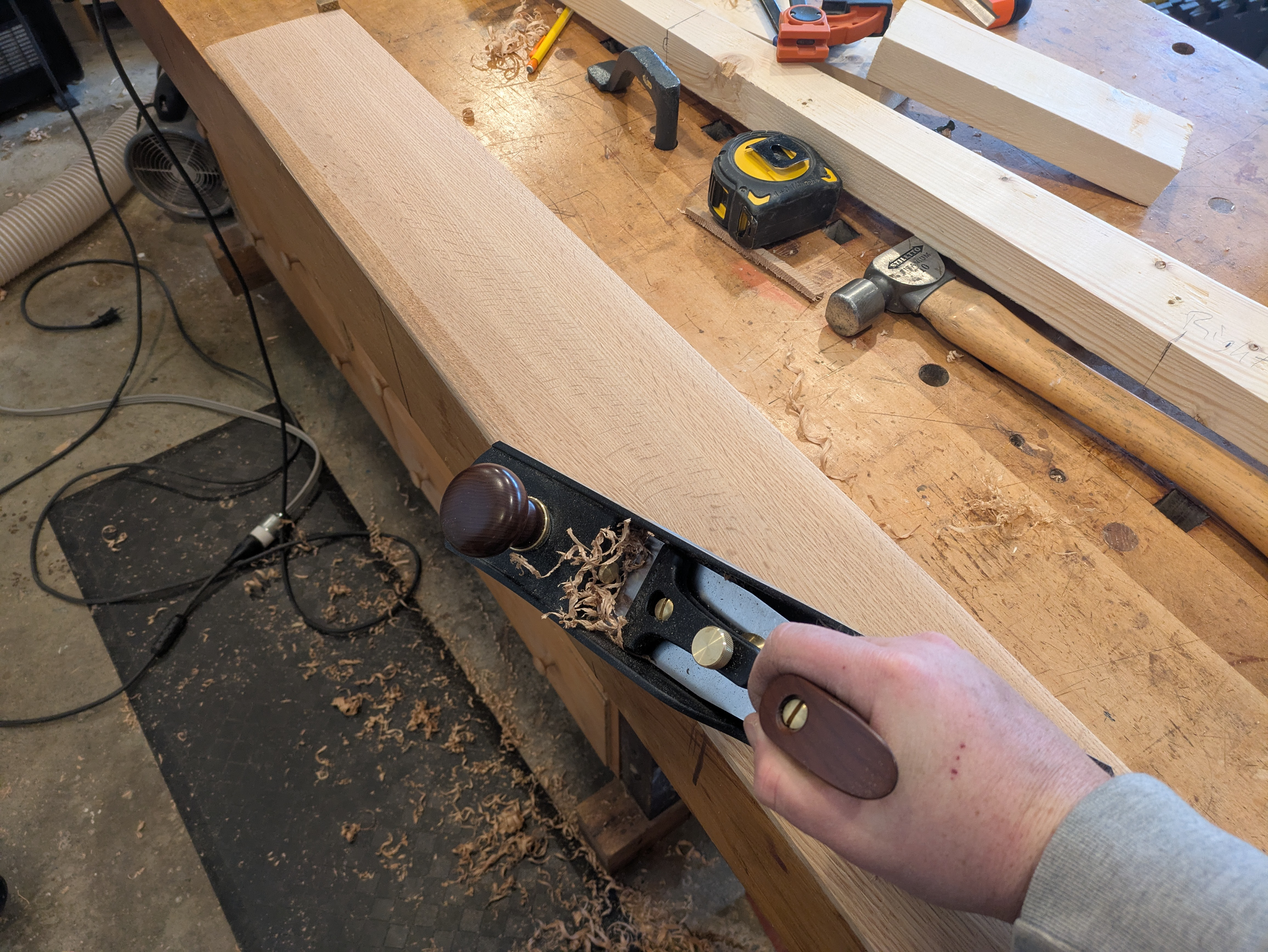
The steeply pitched hand plane does a good job planing tricky quarter sawn oak with the grain as well. I’m rounding over the leading edge and beveled end of the threshold.
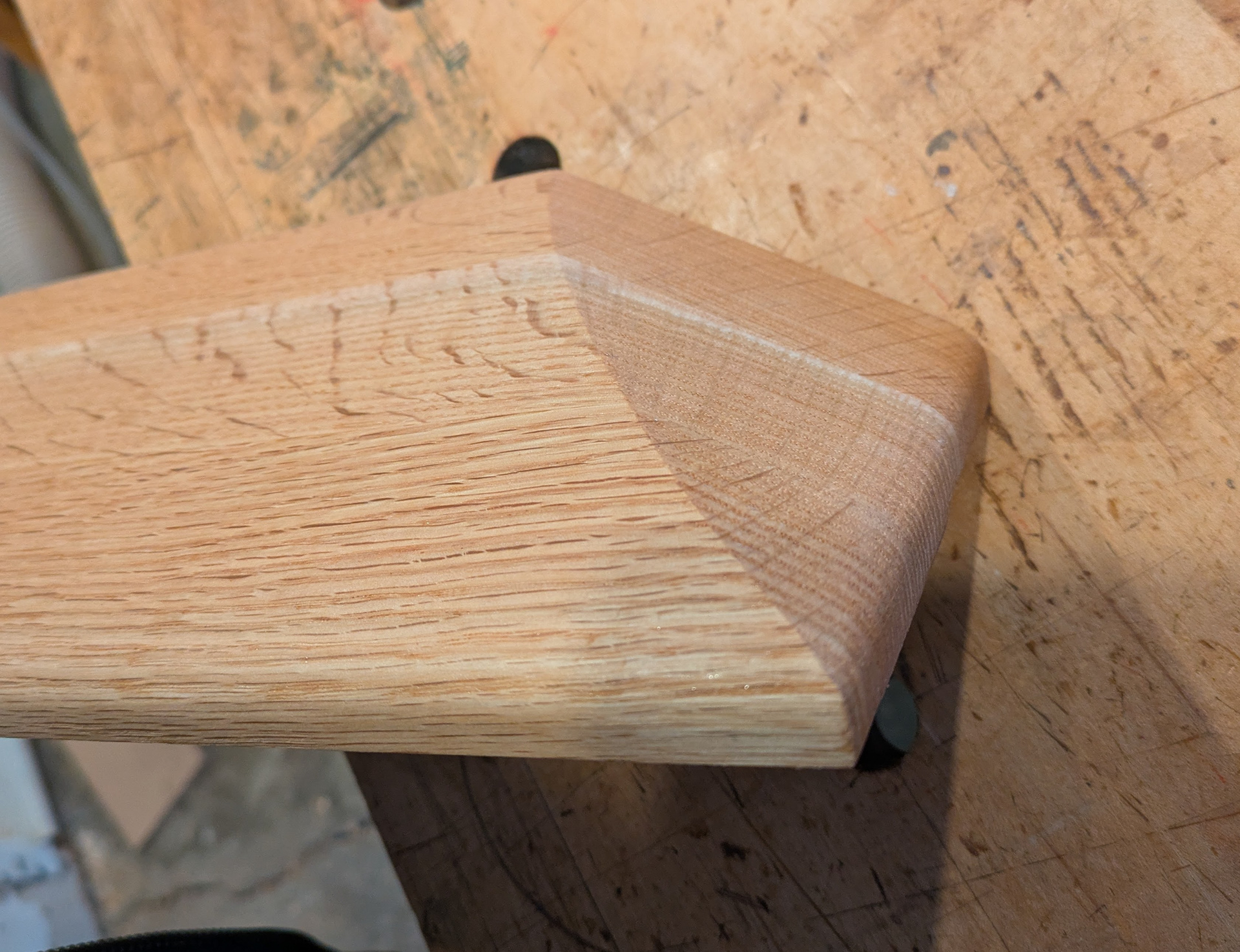
Some final sanding up to 150 grit and the threshold is ready for finishing.
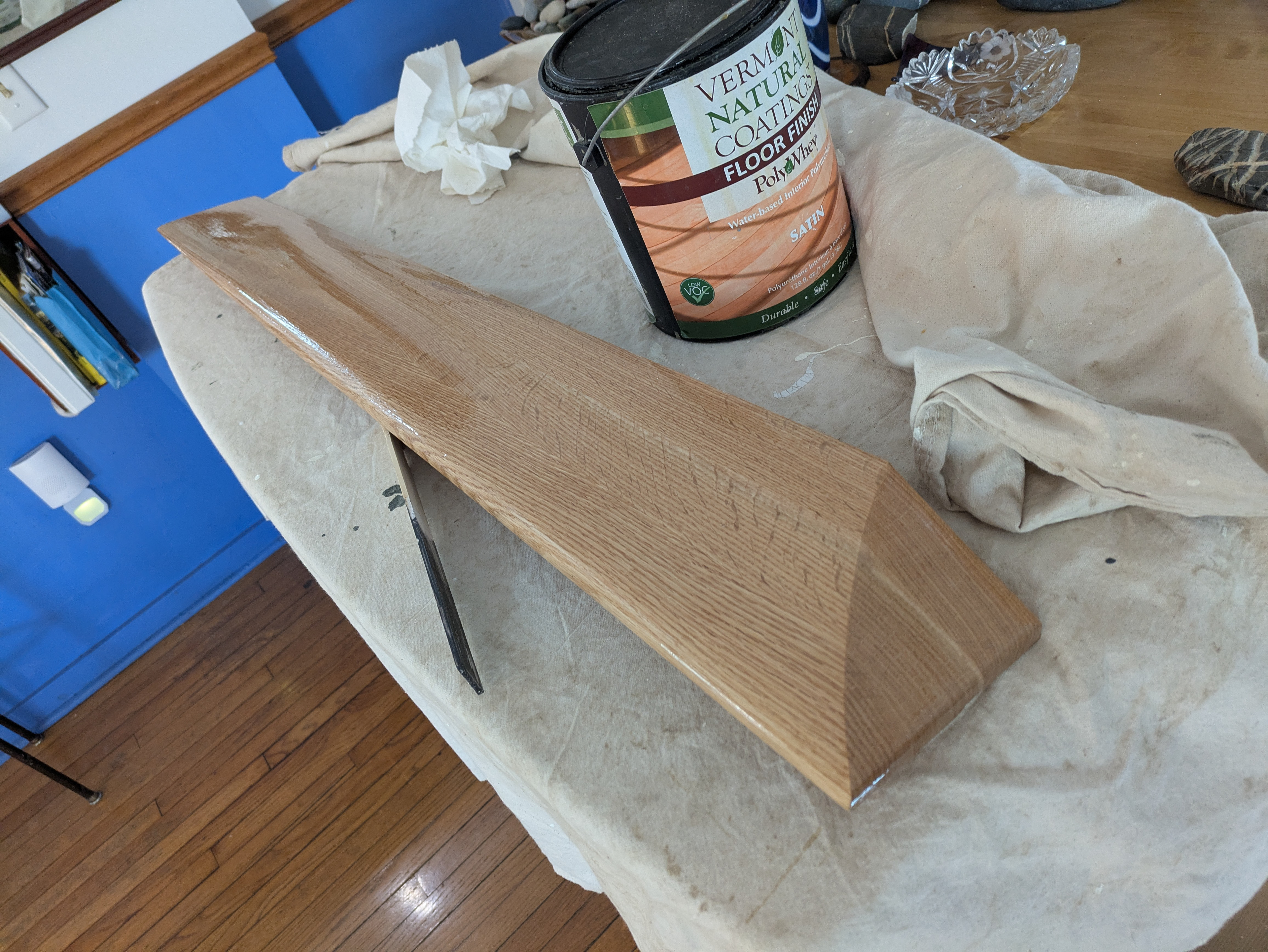
Floor polyurethane is a good choice for a threshold. I sealed the grain with a coat of shellac, then brushed on 3 coats of vermont natural coatings water based polywhey floor polyurethane.
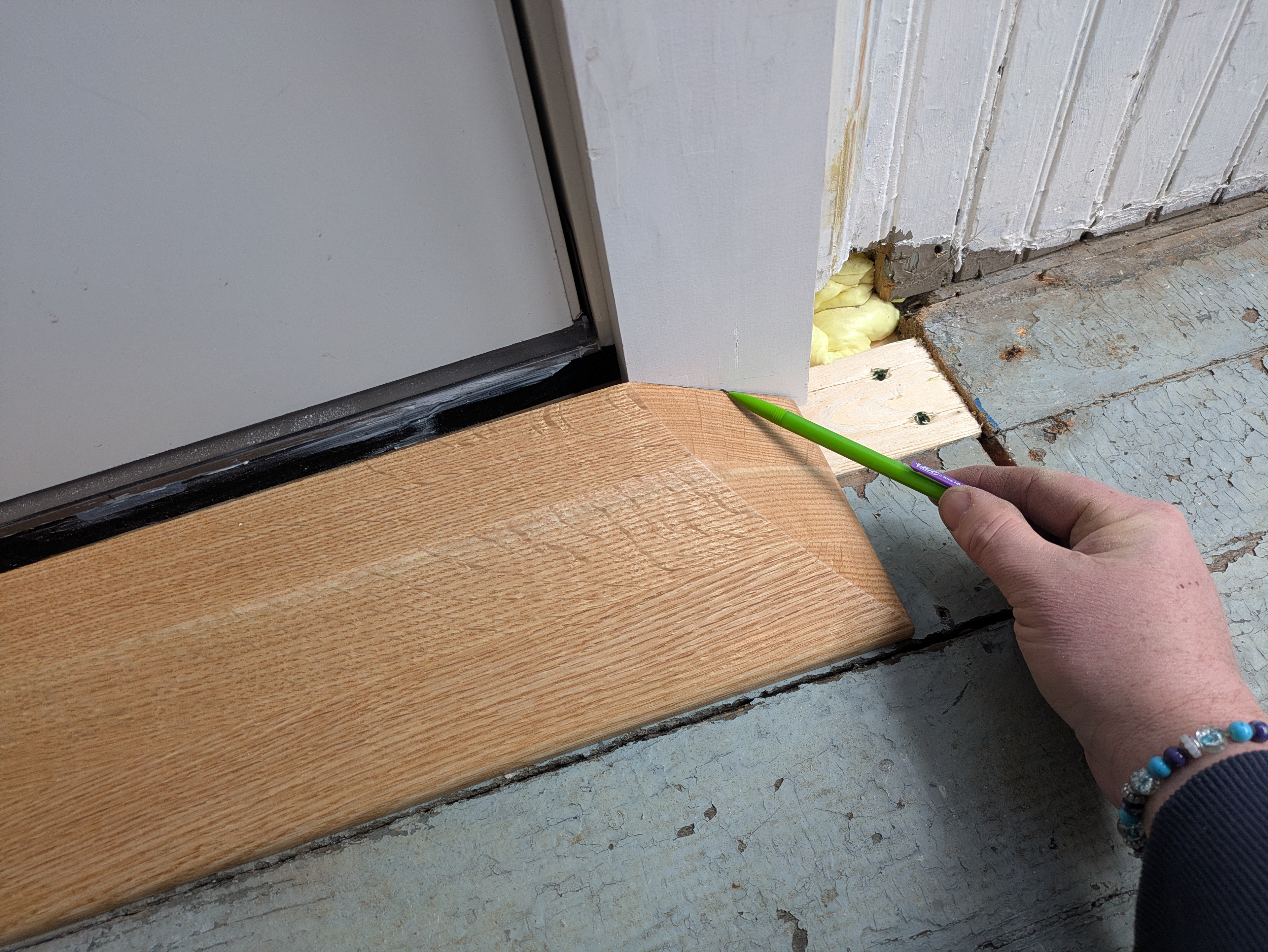
Scribing the threshold into the casing legs will allow me to cut the casing with a buzzy saw for a good fit to the threshold.
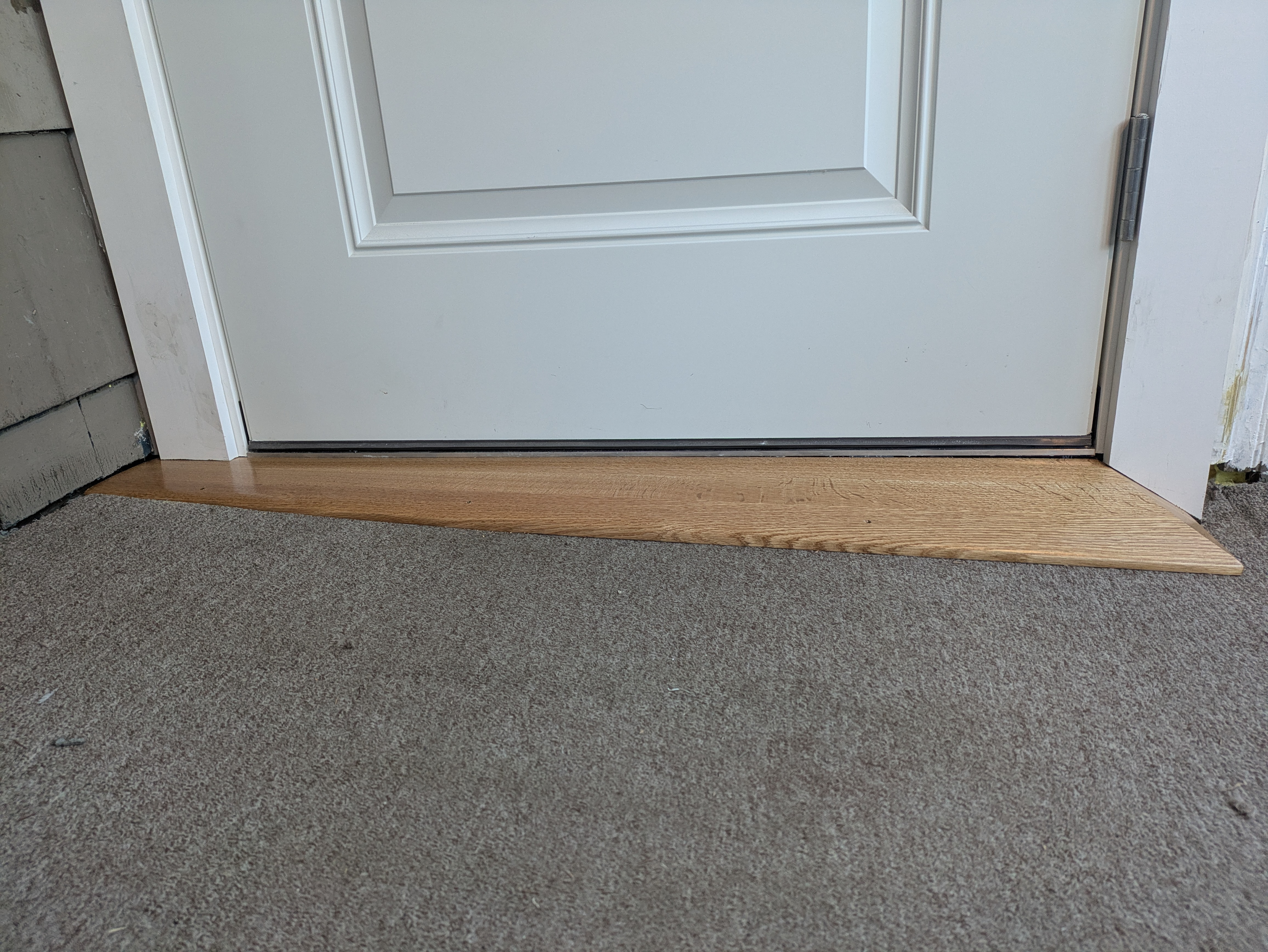
I cut back the carpet from all but the leading edge of the threshold. The threshold is glued to the pine floor boards with PL premium oil based construction adhesive. 3 screws across the leading edge attach the threshold to the floor joists below.
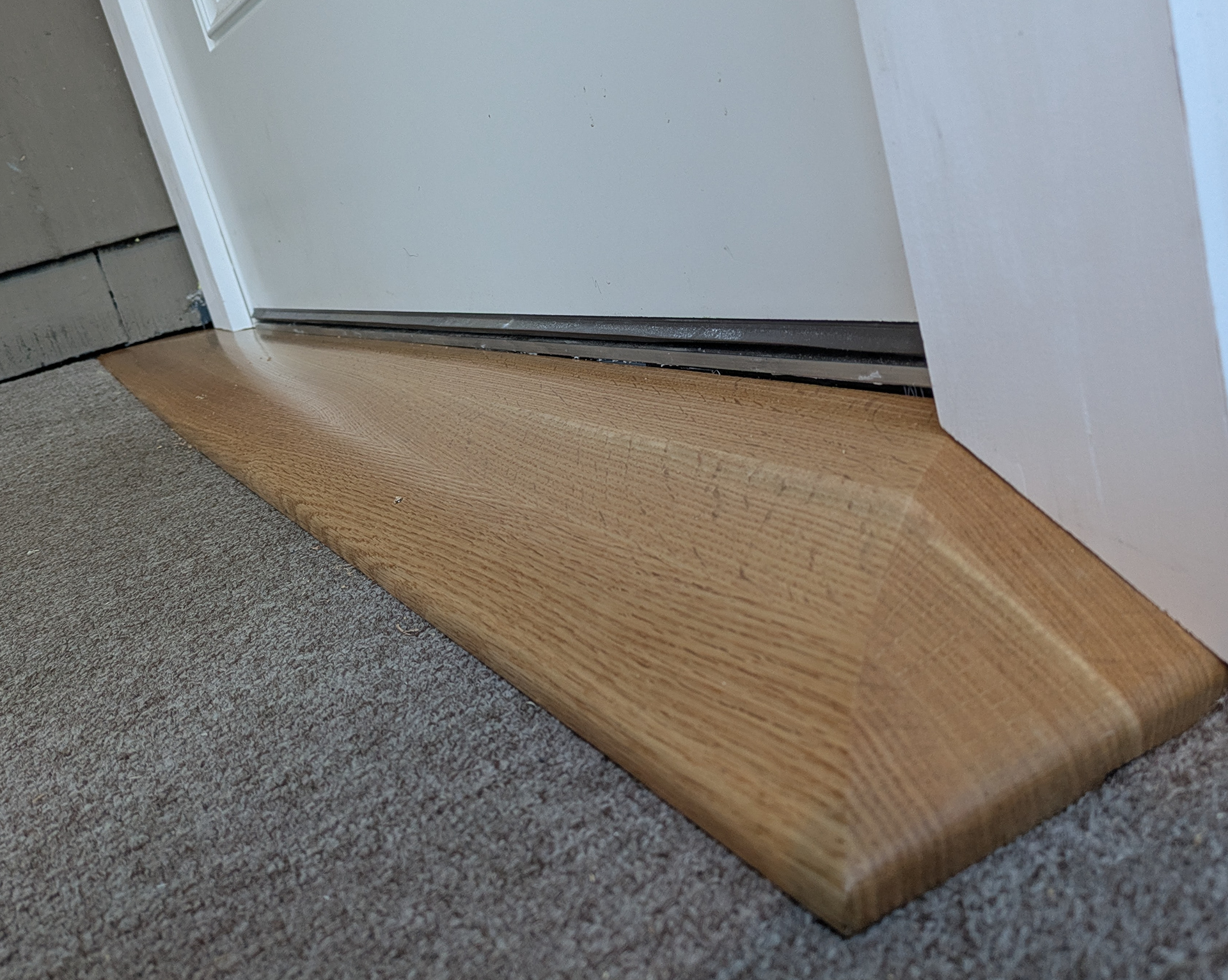
It’s a pretty big step up but this large interior threshold should prevent tripping.

All done. I’ll come back in the Spring to wrap up the spackling and painting in the warmer weather.