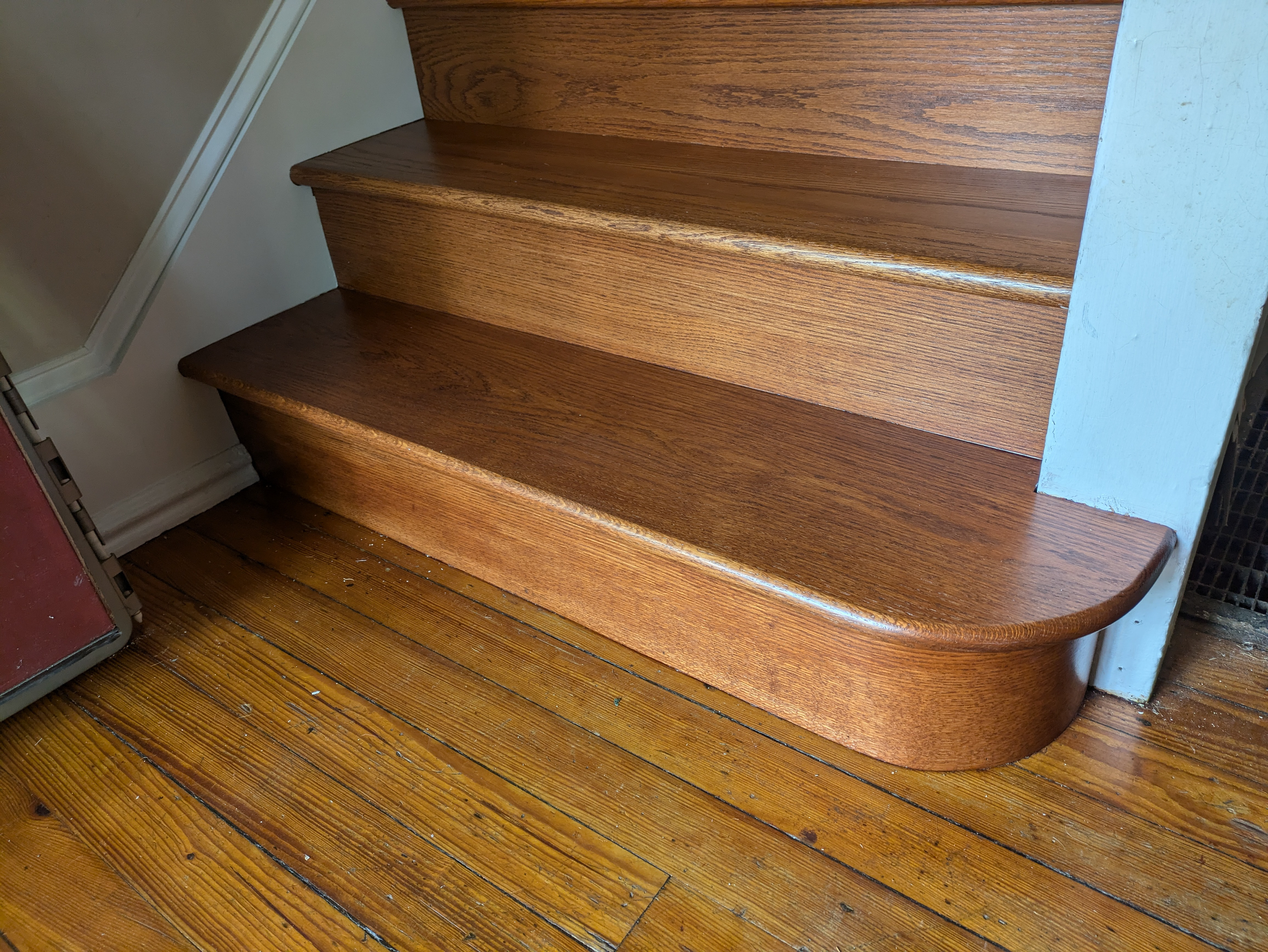
Building this curved riser and tread for a staircase that I recently rebuilt was a fun project. The wood is red oak and the stain is color #76 from the RTM line of stains by general finishes.
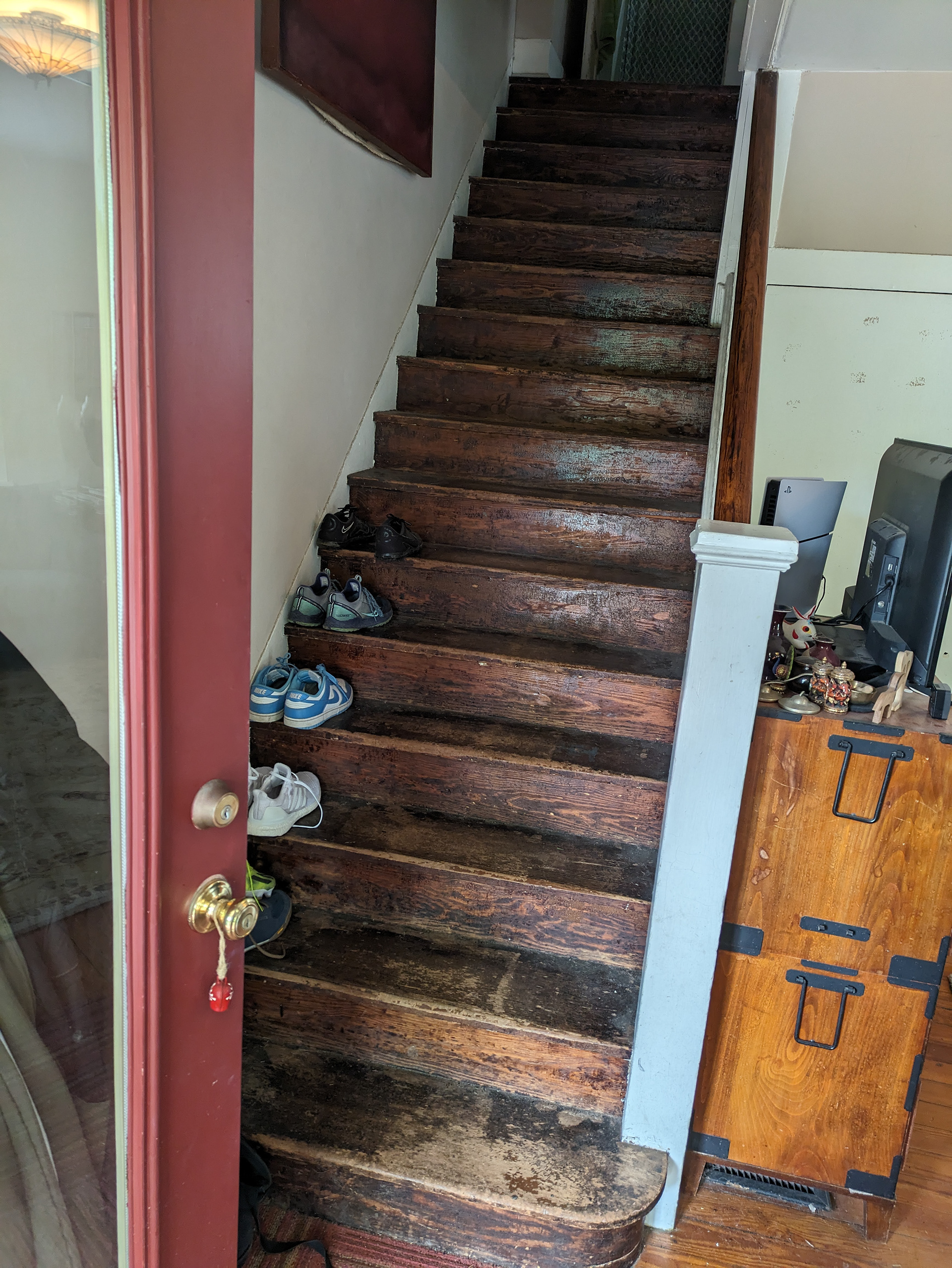
These old stairs are structurally sound but cosmetically pretty worn and very squeeky to walk on. I'll shore them up and install new stair components on top of the existing steps. This will allow me to not demo lead painted woodworking/plaster and we can keep the cool existing balustrade and newel post. The unit rise from the top step to the nosing on the 2nd floor is 5/8" greater than the unit rise from step to step. This means that adding treads on top of the existing ones will make the top step walk the same as the rest of the staircase.
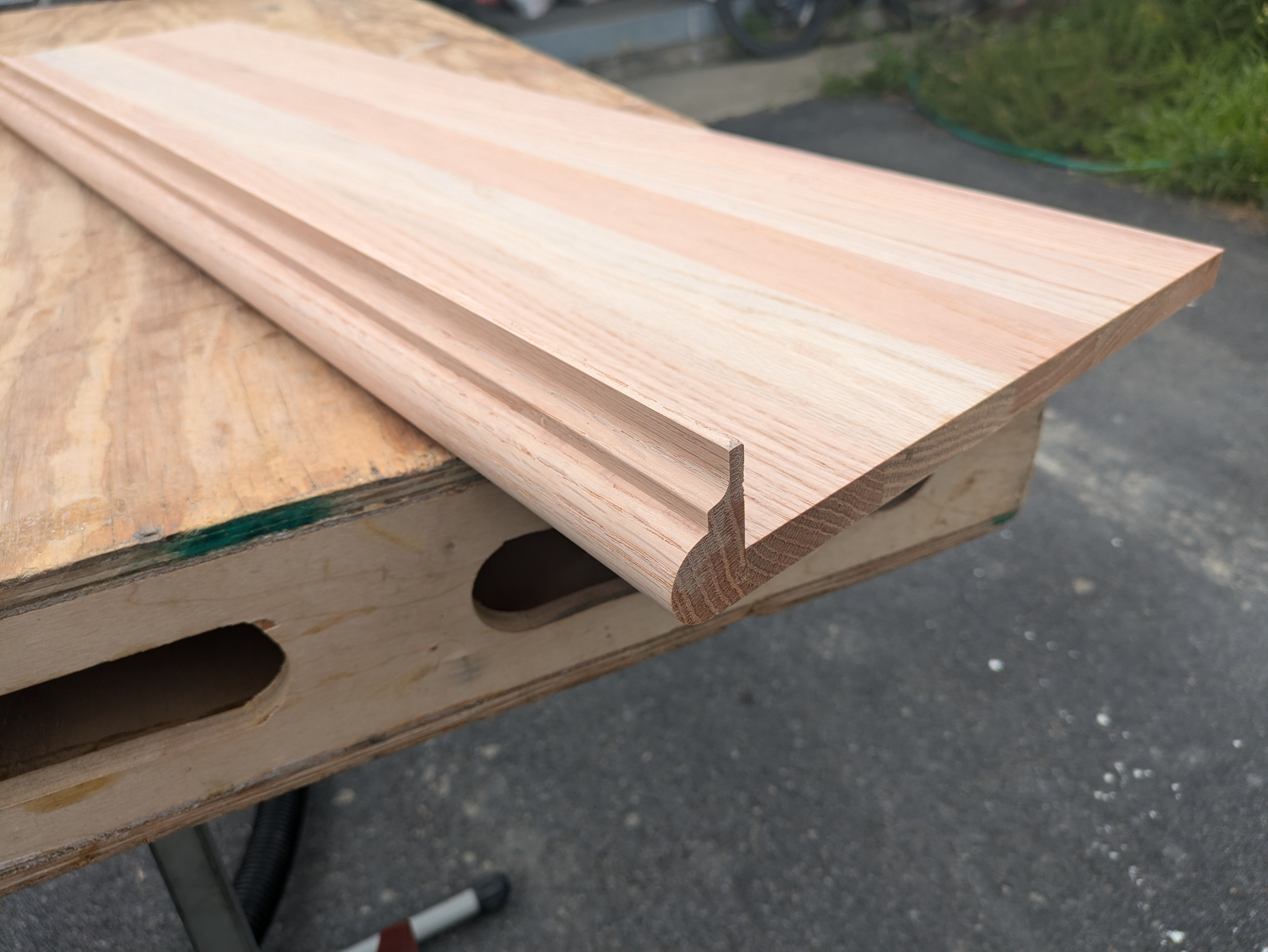
This is a retro-tread. At 5/8" thick it's thinner than a typical 1" thick stair tread. It also has a built in Scotia/cove molding. The 5/8" thickness will have less of an impact on the unit rise of the first step to the floor than would a full 1" thick tread.
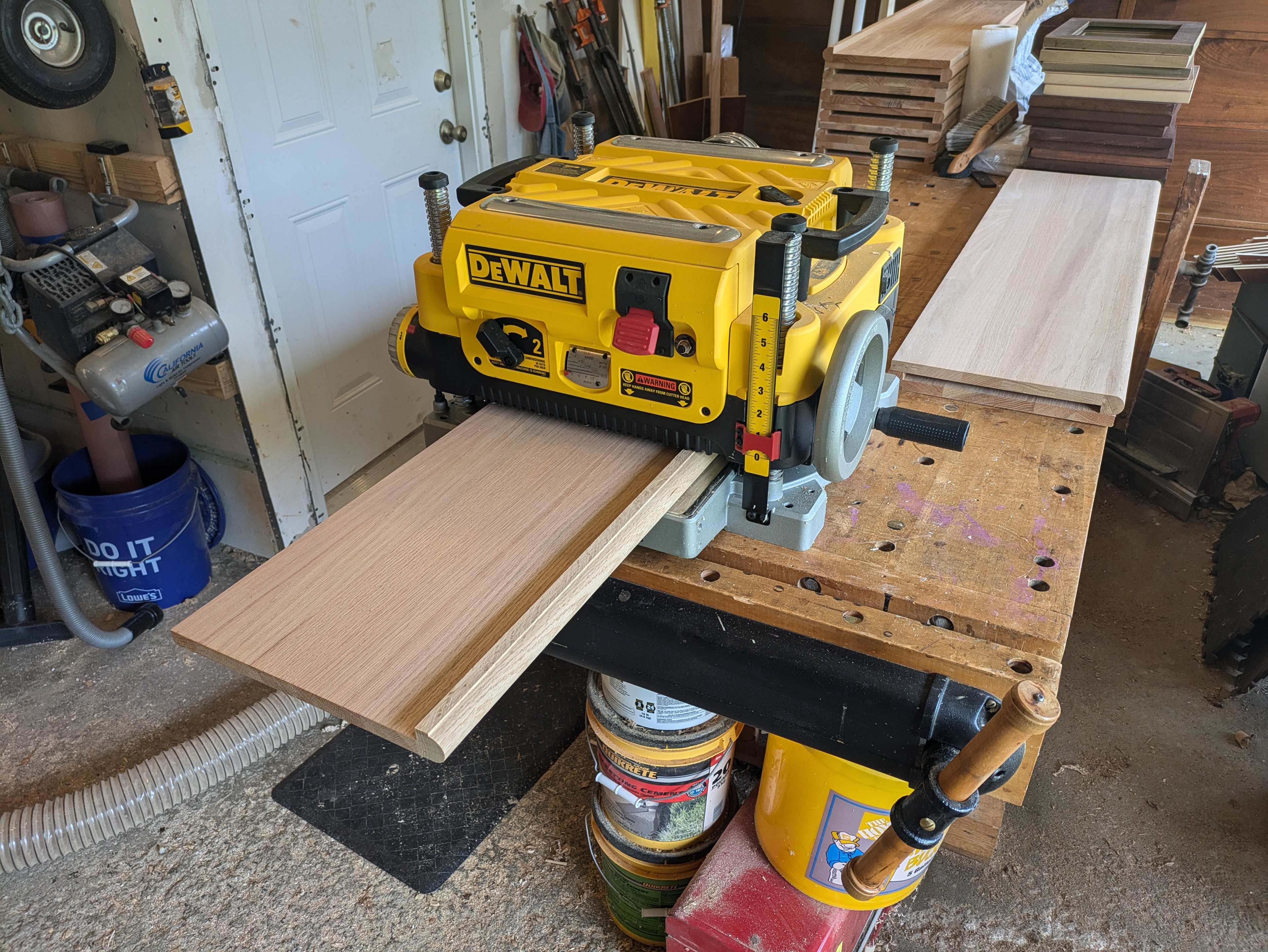
The existing stair treads don't have a Scotia molding so the new treads won't either. I sawed them off with the table saw. Now I'm running them through the thickness planer.
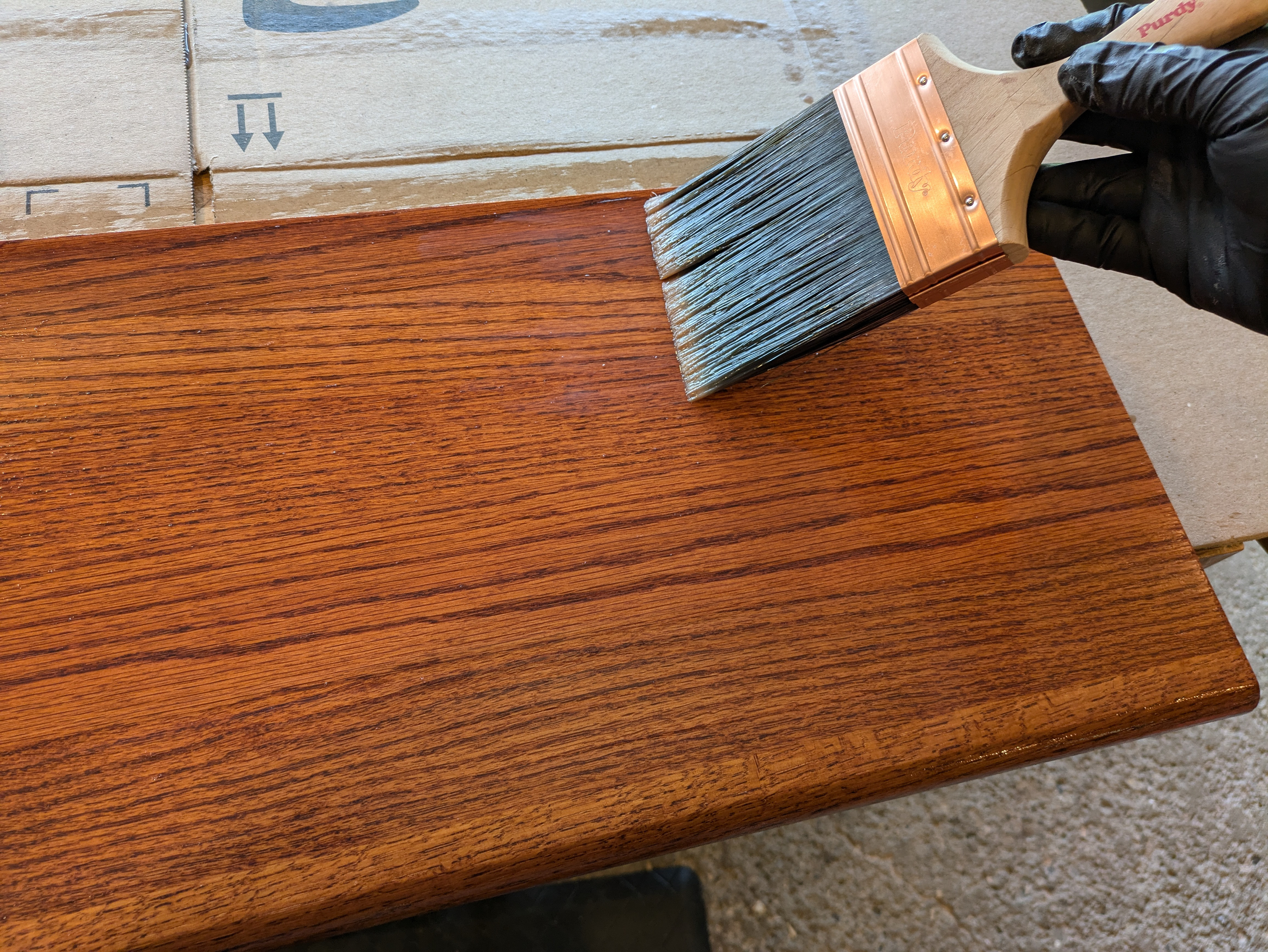
I machine sanded the treads up to 150 grit with a large random orbital sander. I raised the grain with water then hand sanded the parts with 220 grit. I applied a water based stain from general finishes RTM system. Now I'm brushing the parts with polywhey floor polyurethane in satin. I'll apply 3 coats then sand them smooth with 400 grit sandpaper.
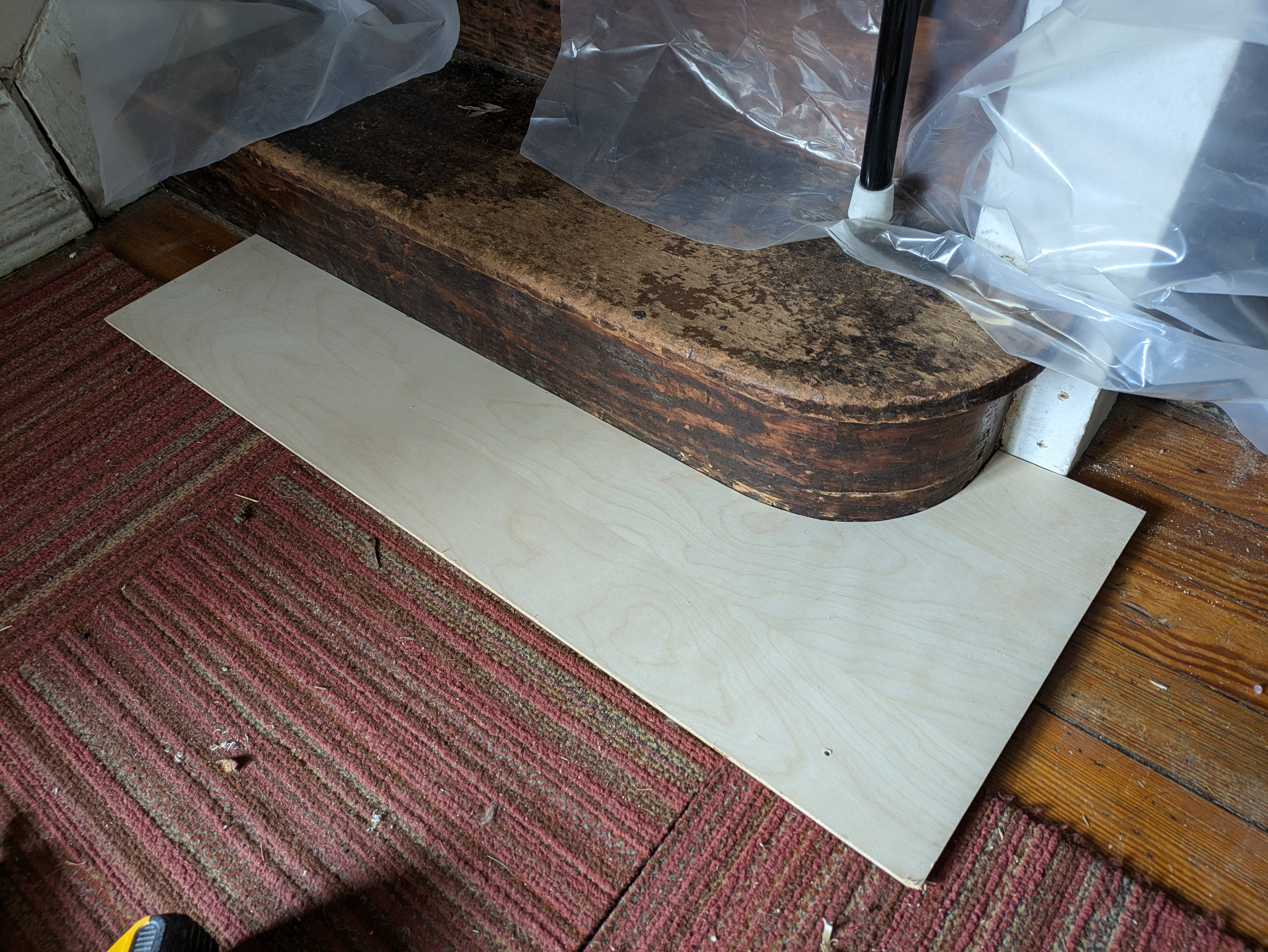
I created a tracing template for the curve of the existing riser. I'll take this to my home shop and use it to create a bending form for the new riser.
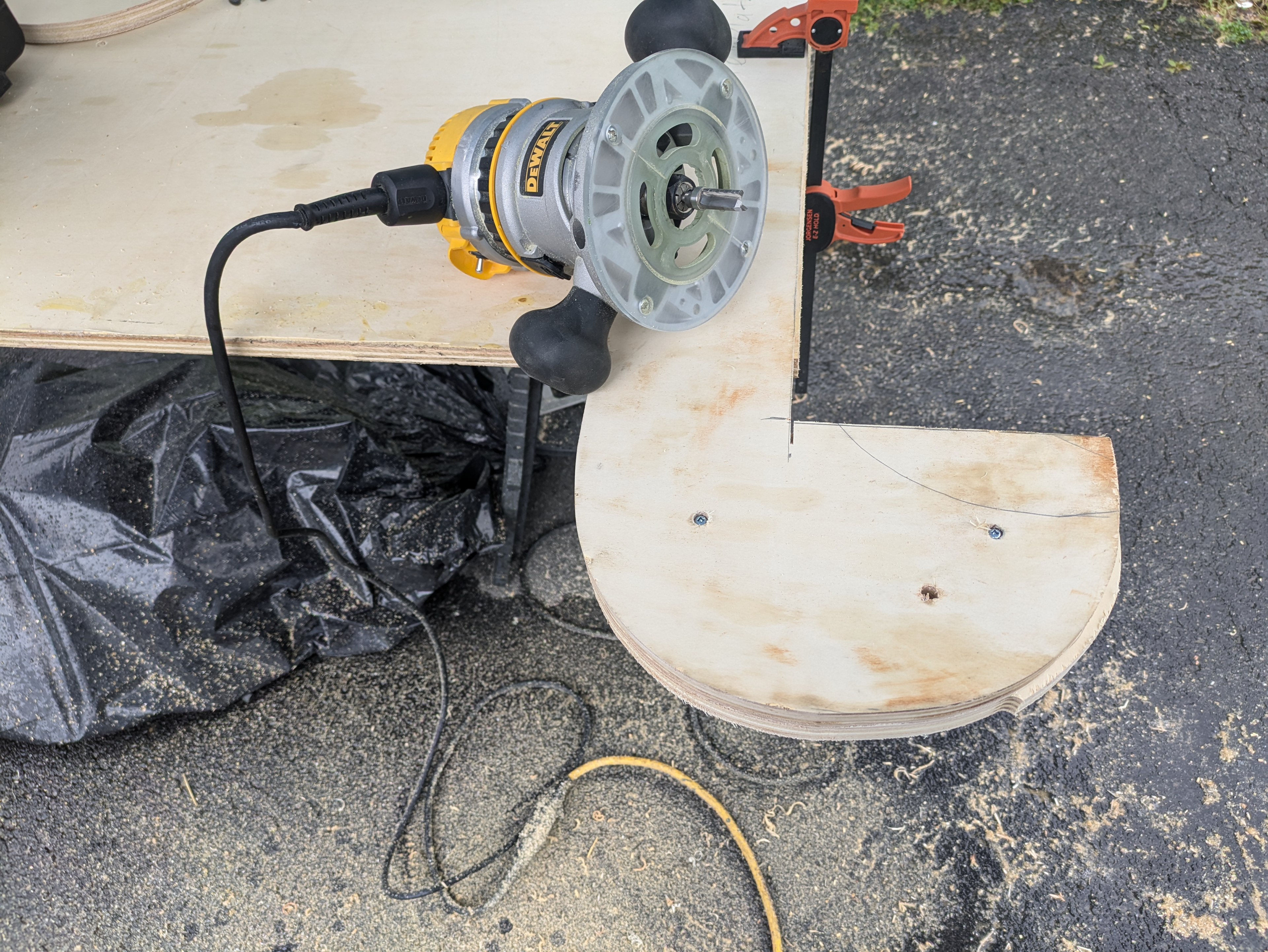
I used the tracing template to create a routing template using a jigsaw and large disc sander. Now I'm using that routing template to make more pieces of plywood to match. I'll glue them together to create a form for bending the new riser.
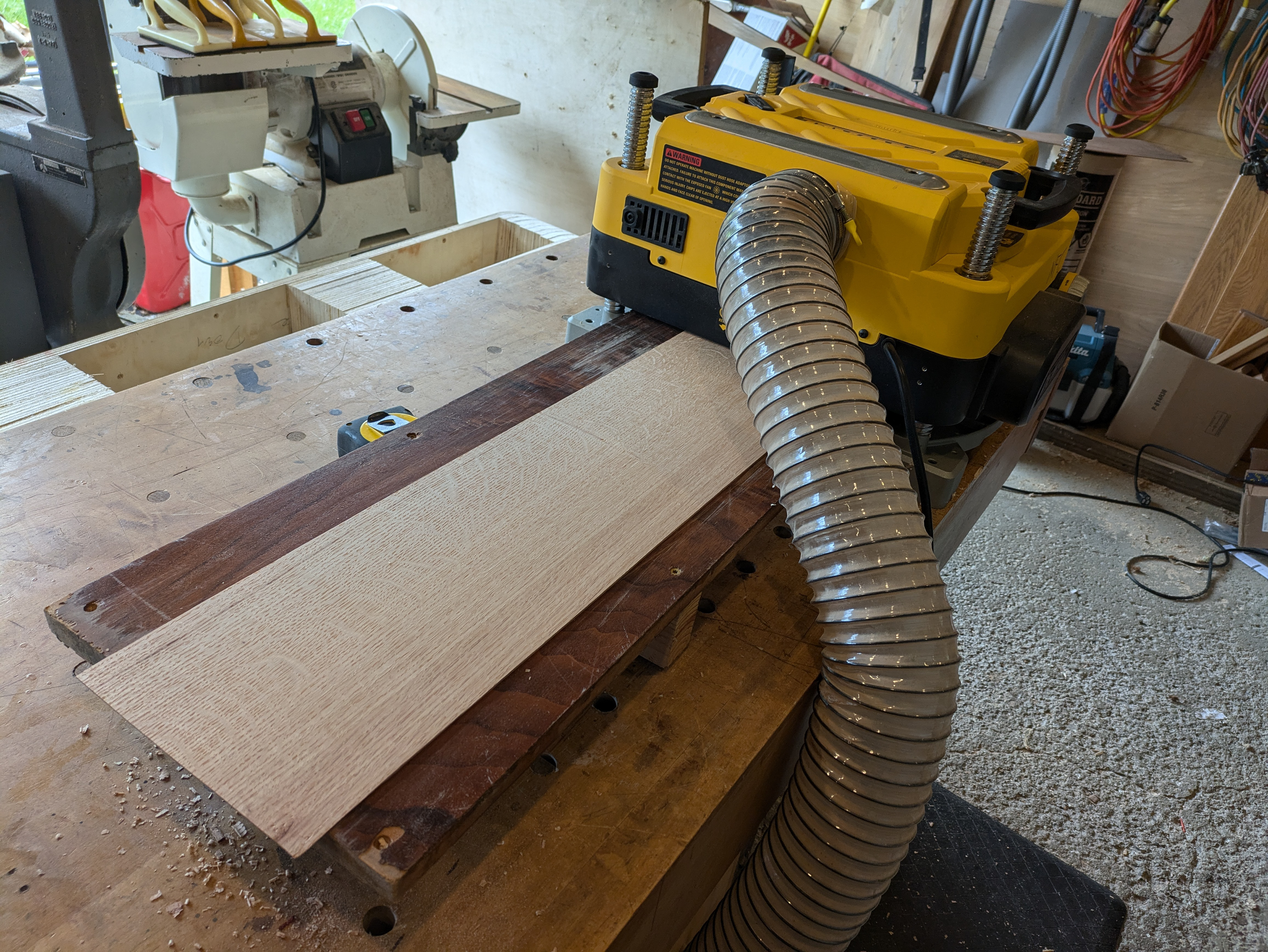
I'm using the thickness planer to plane 2 pieces of quarter sawn red oak to about 1/8" thick. I'll also plane down a couple pieces of rift sawn douglas fir. These pieces will make the laminations I'll use to build the riser.
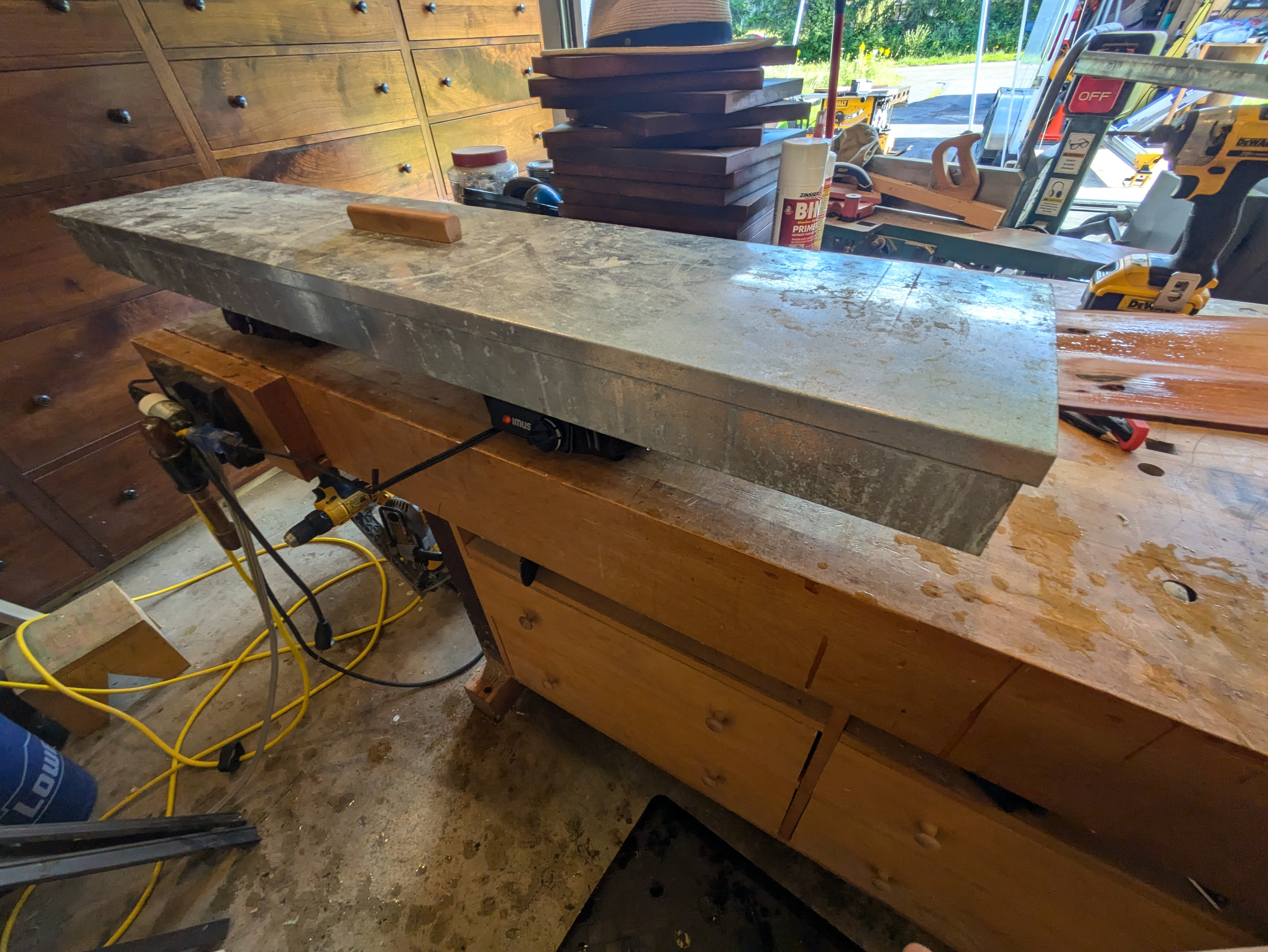
I'm soaking the laminations in hot water. This is the pan I use for making shaker oval boxes. Hot plates bring the water to a near boiling temperature.
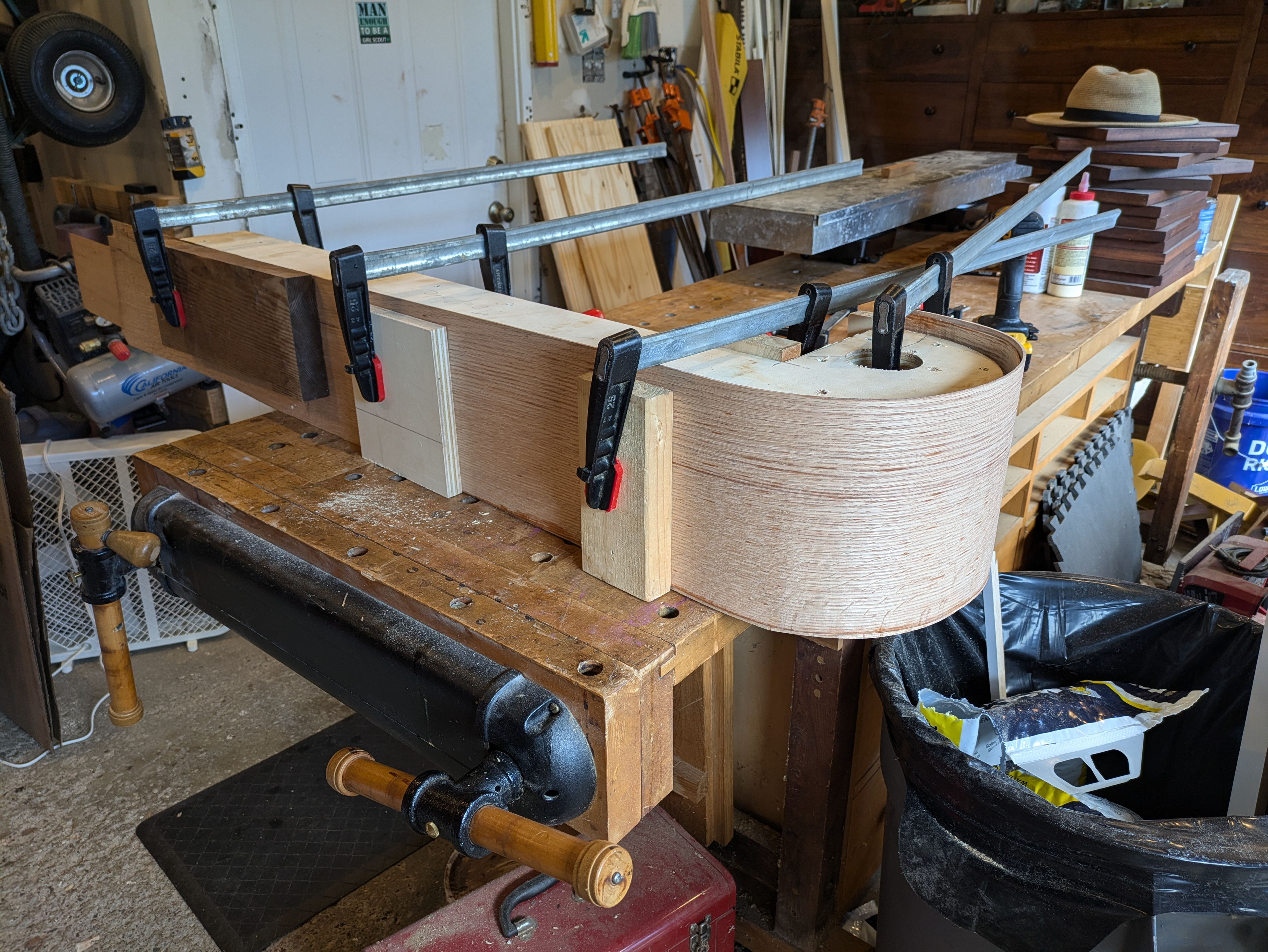
I've bent the laminations around the form. I'll leave them clamped to dry out.
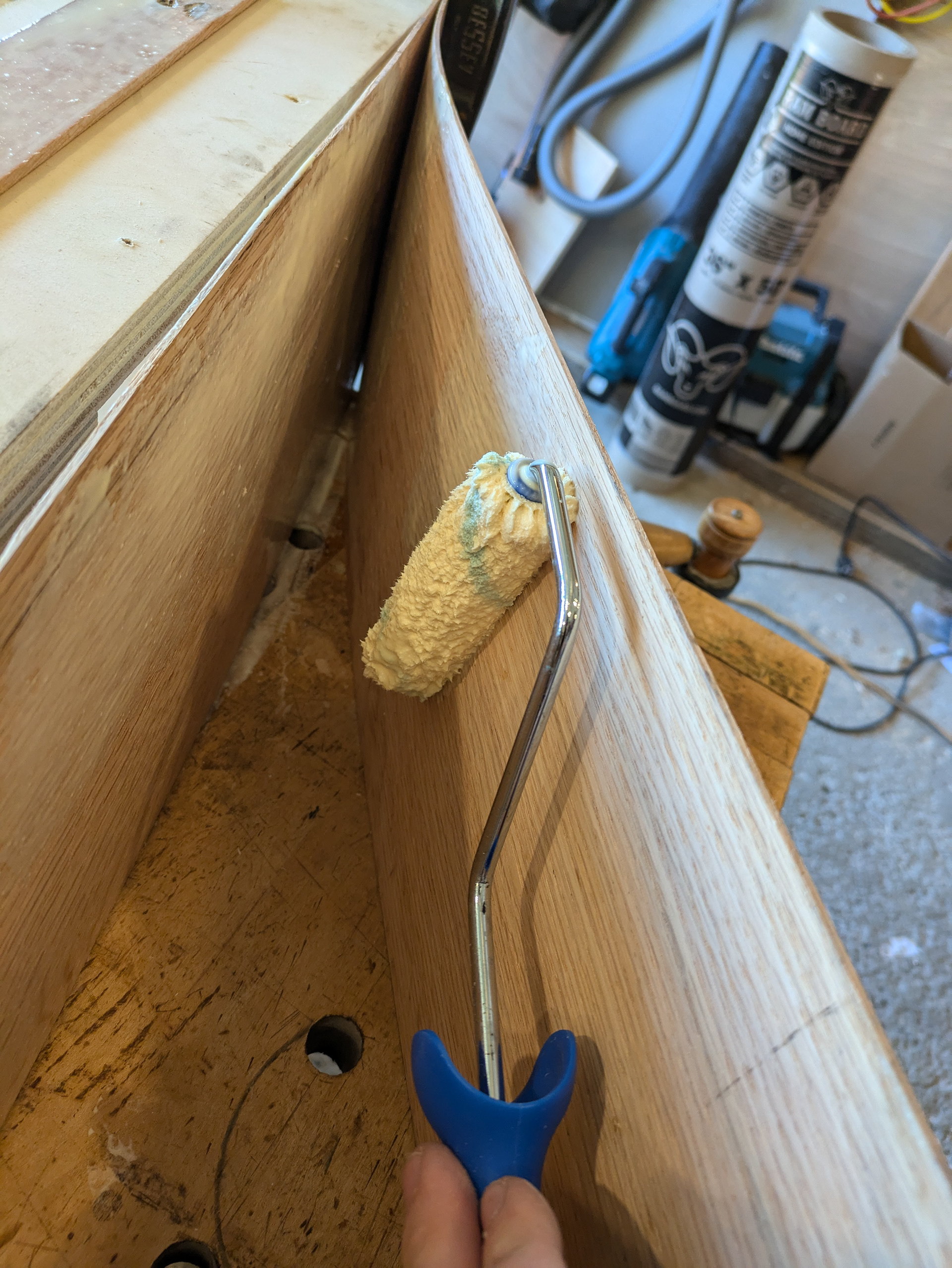
I'm gluing the laminations together with tite-bond using a small paint roller. I'll clamp the riser laminations together and leave them alone for a couple of weeks while I canoe with my family in the mountains.
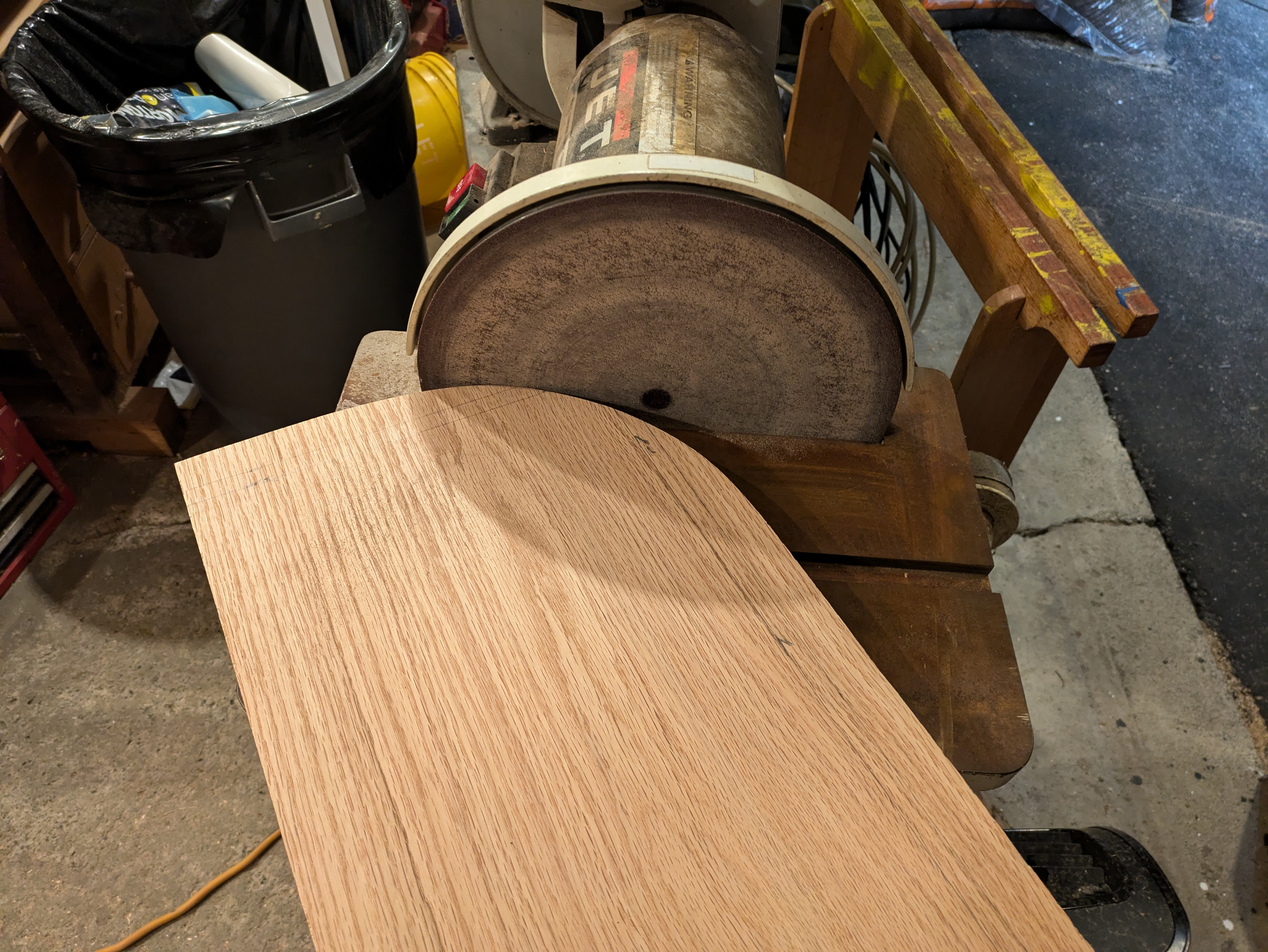
It's been a couple of weeks, now I'm back in the shop making stairs parts. I used the template to layout the curve on the riser. I used a jigsaw to cut the curve. Now I'm using the disc sander to square the edge and remove the saw marks. I'll cut it to final length and rip it to finished width onsite.
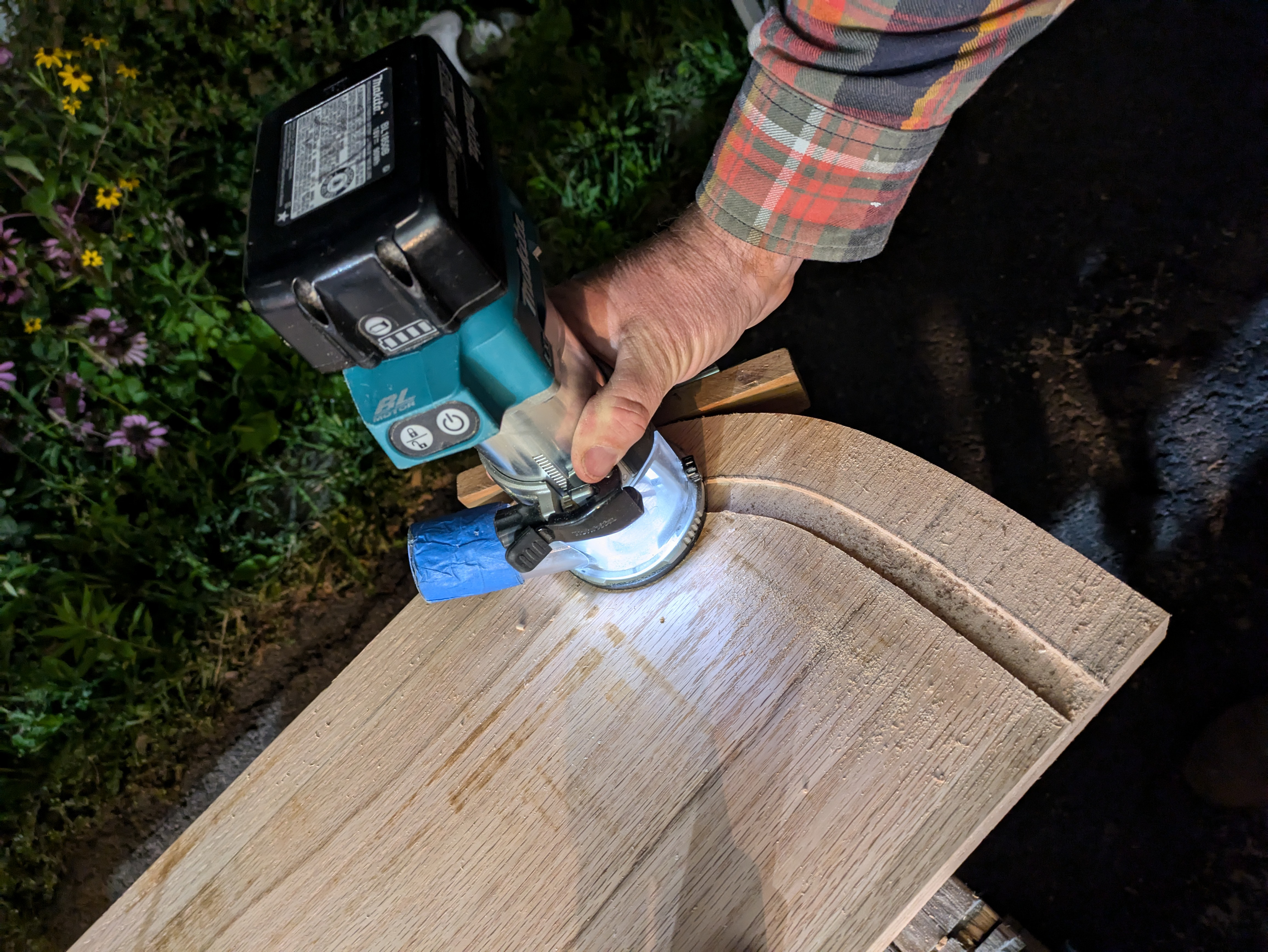
I'm establishing the curved edge of the rabbit with a router and edge guide. On a re-tread job the treads are typically thinner than usual with a rabbited nosing.
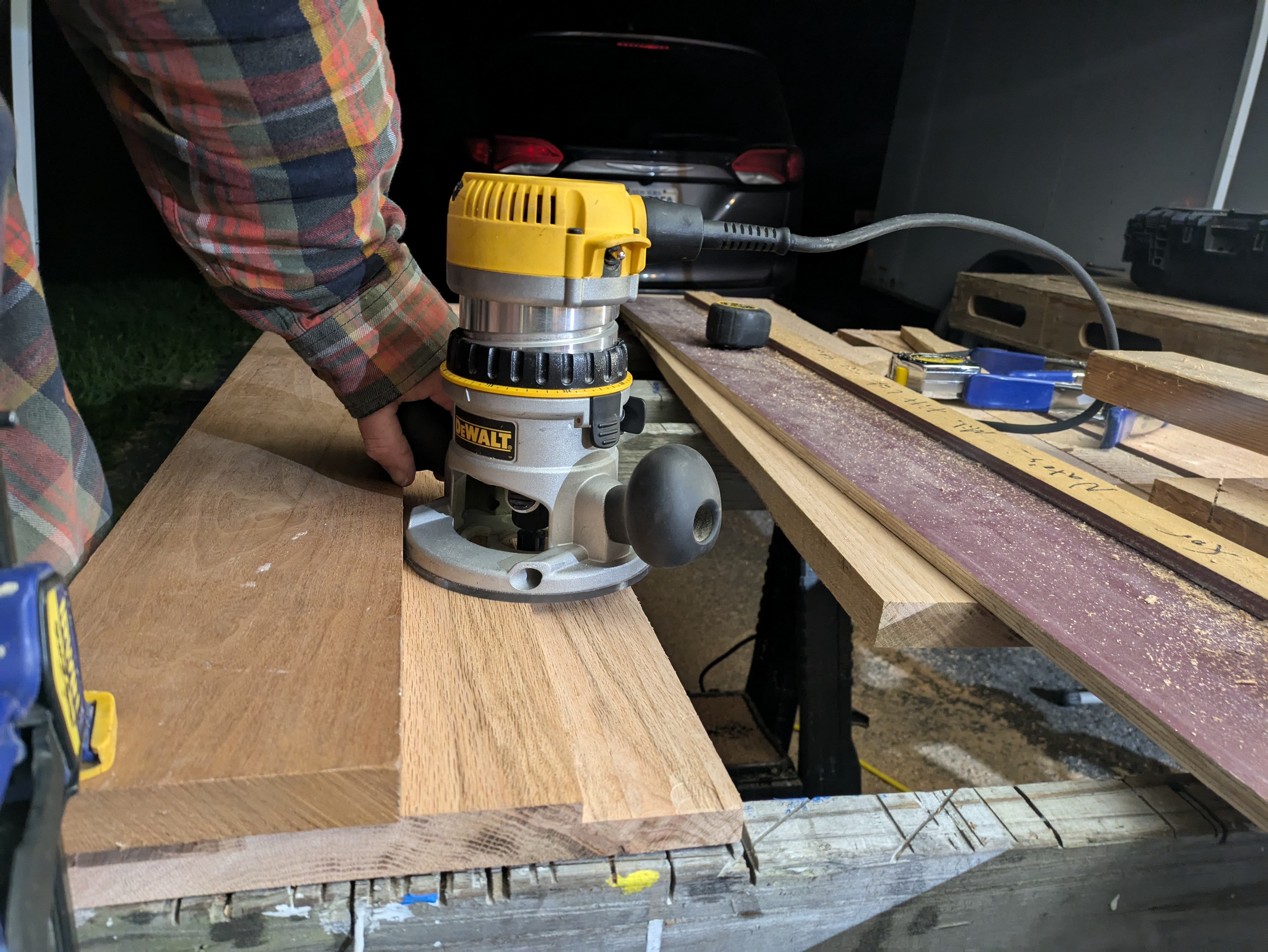
A bunch of passes with a router will thin out all but the nosing of the tread. When I'm done with this step, I'll use the router to round over the nosing.
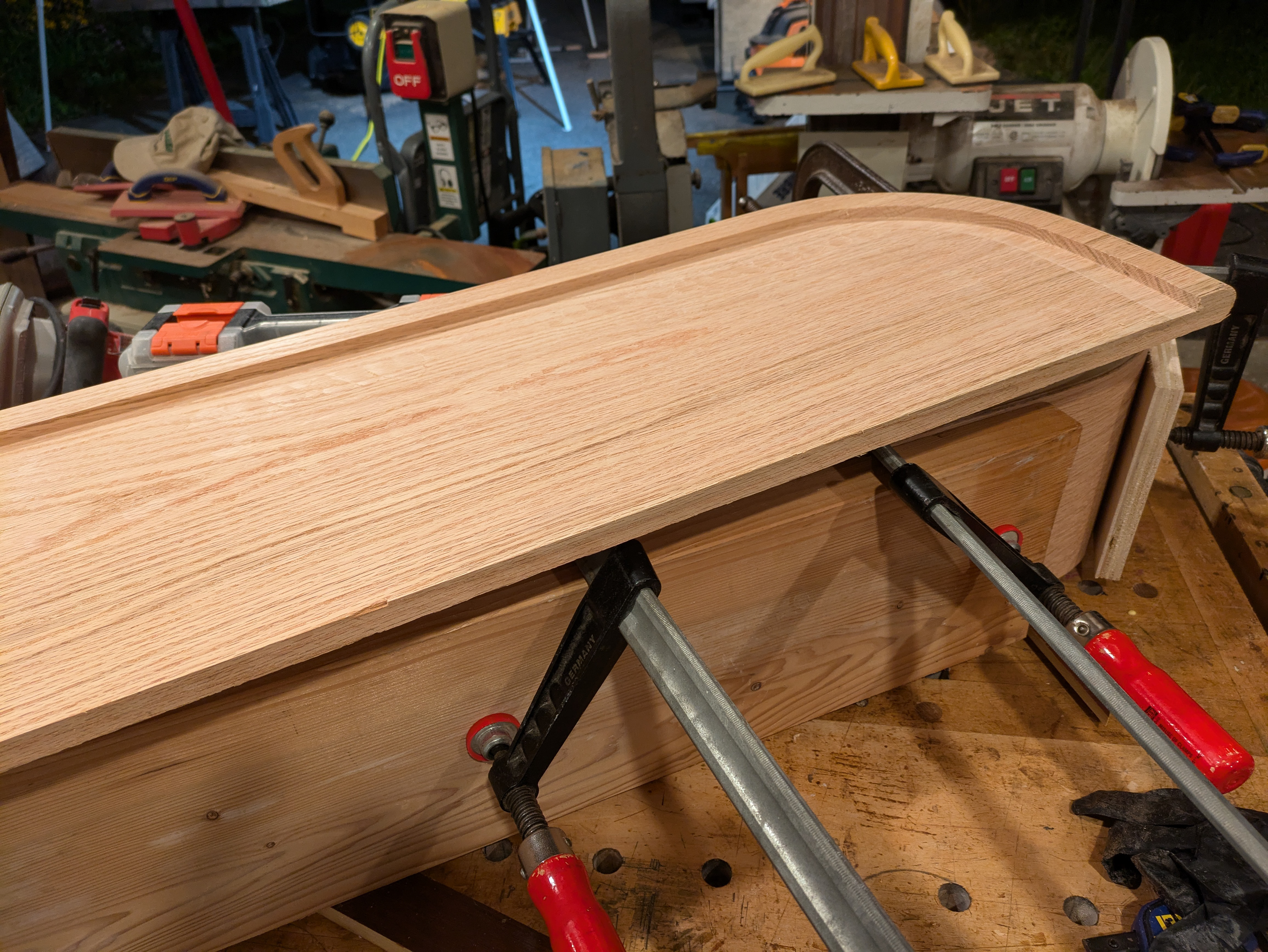
The tread is ready for sanding. This is the bottom of the tread.
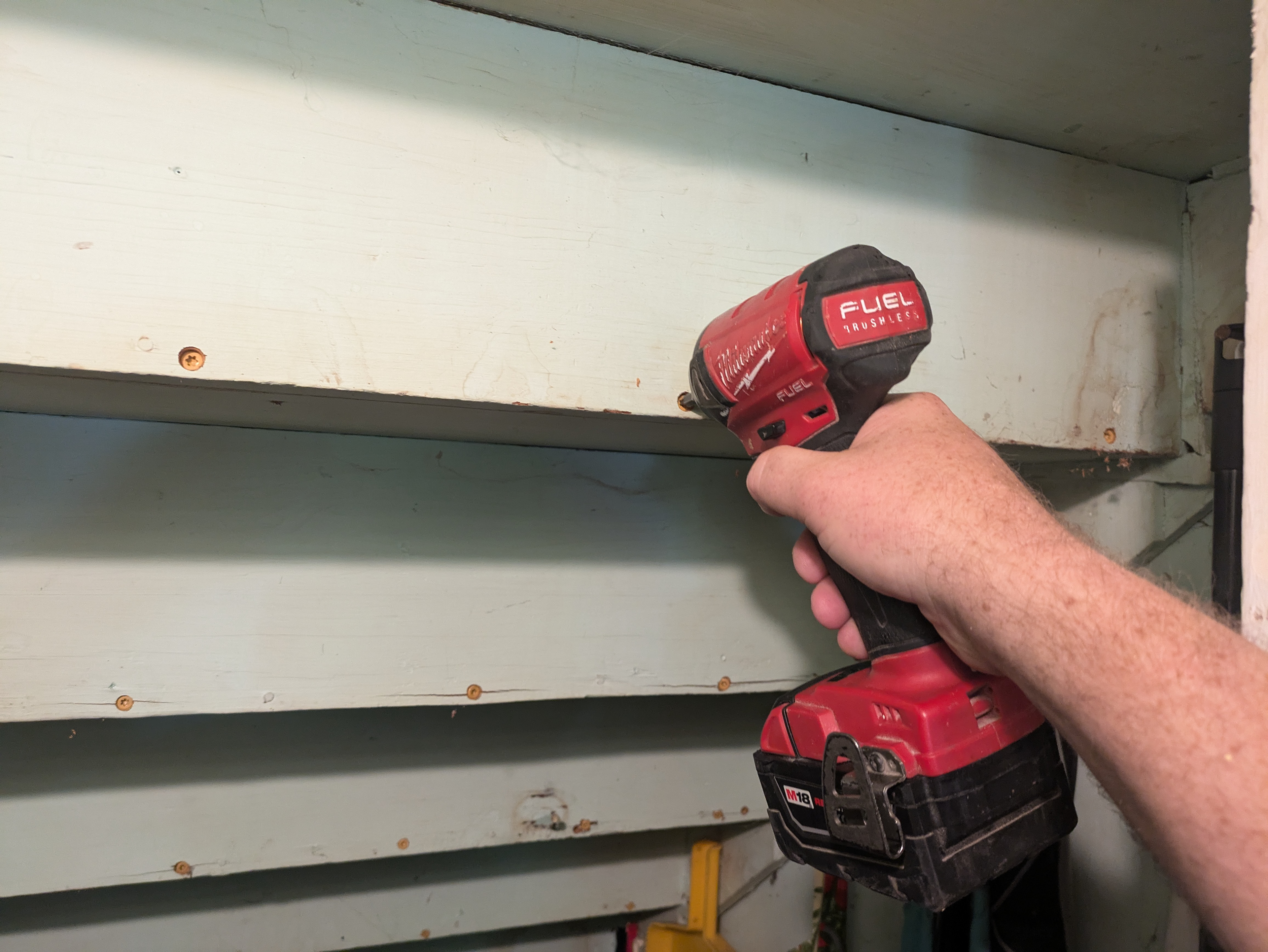
I'm onsite now. The original staircase is very squeaky. I'm fastening through the back of the risers into the treads with framing screws in order to tighten up the old stairs.
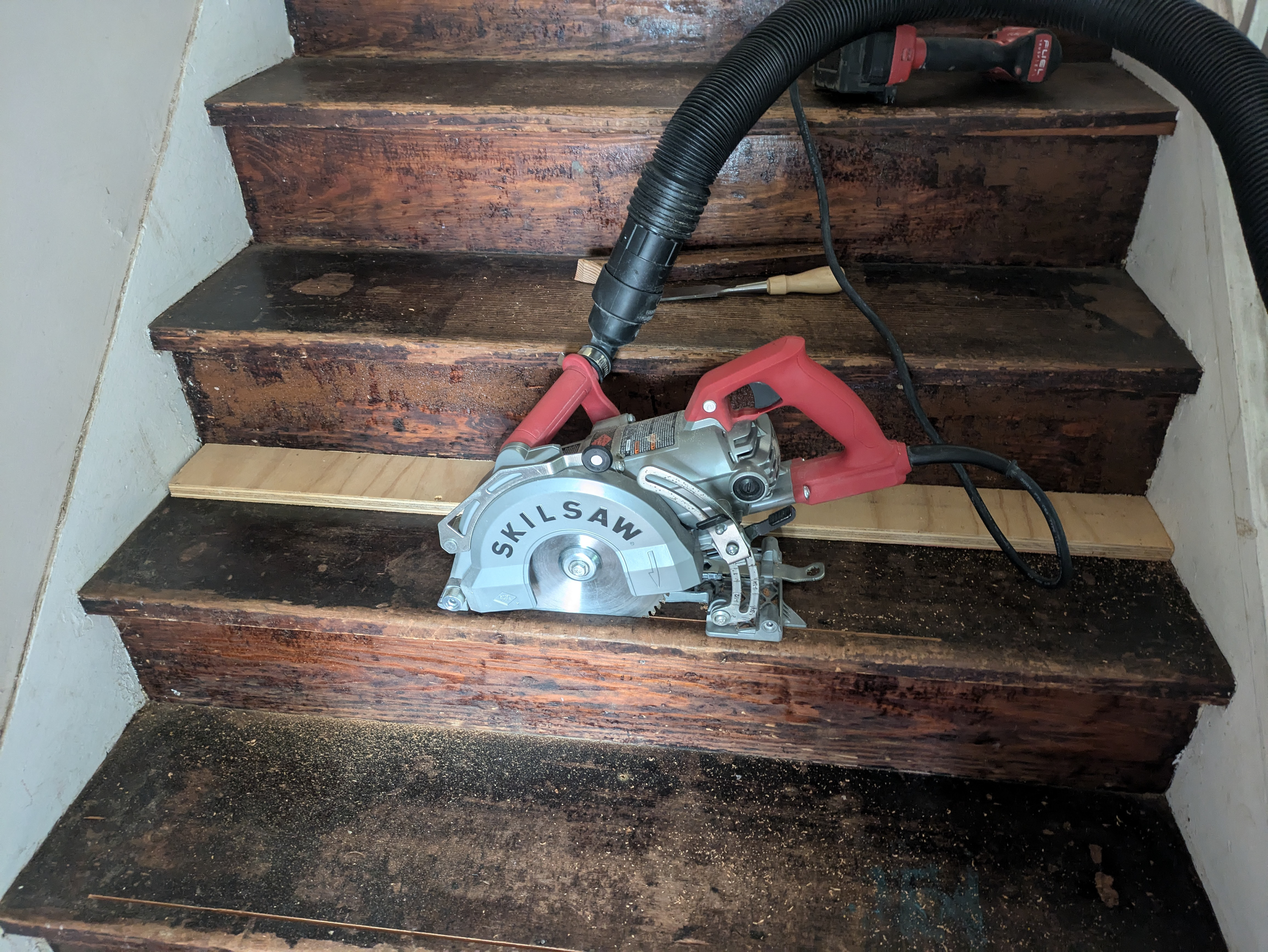
A circular saw rip cuts most of the nosing free from the original treads. I've put a wood cutting blade on my concrete medusaw and removed the wheels. This saw has very good dust collection when I hook it up to my shop vac. A plywood spacer guides the saw so that I consistently cut each nosing a whisker back over the riser below.
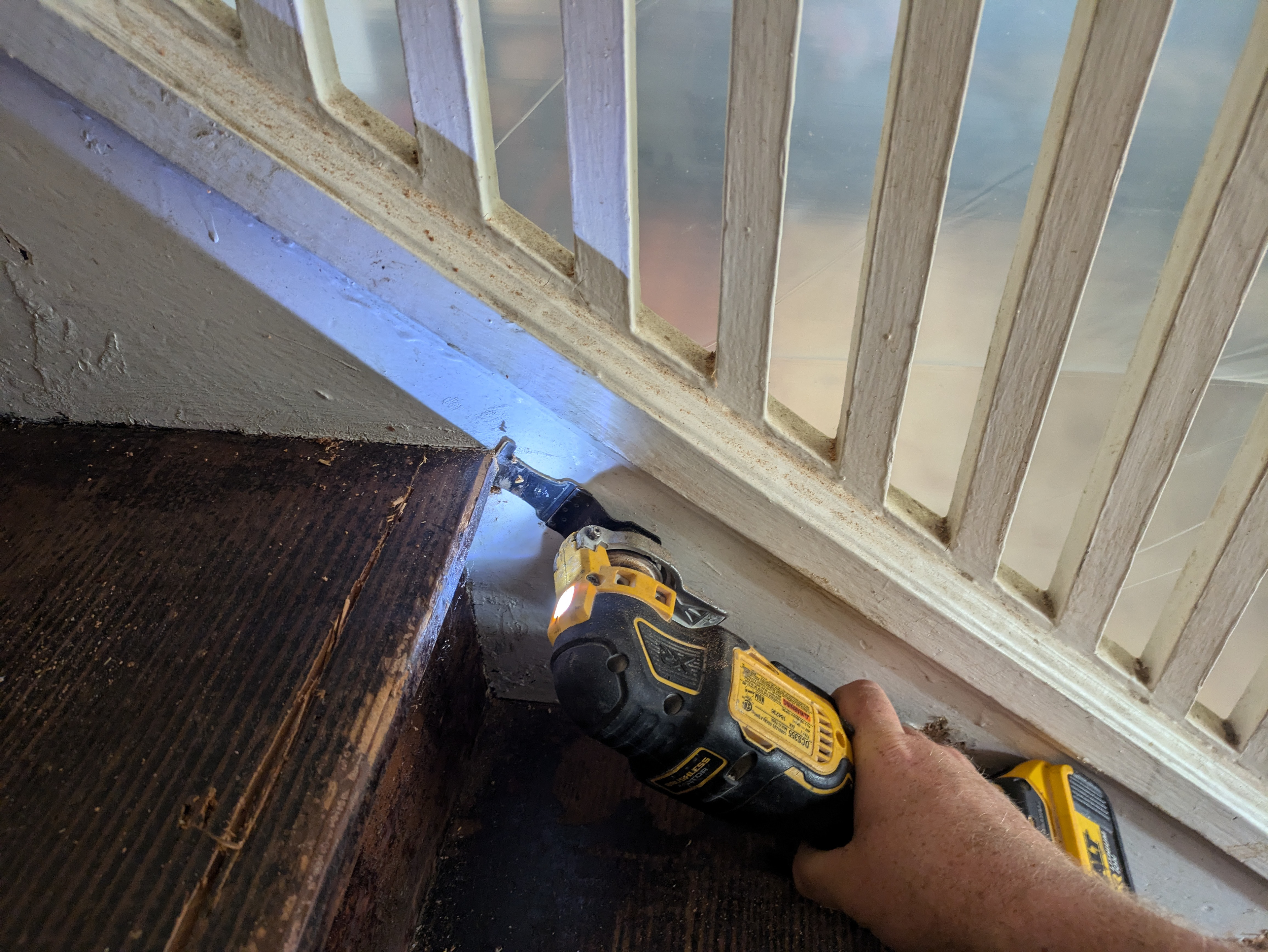
The buzzy saw flush cuts the nosing to the stringer on the balustrade side of the stairs.
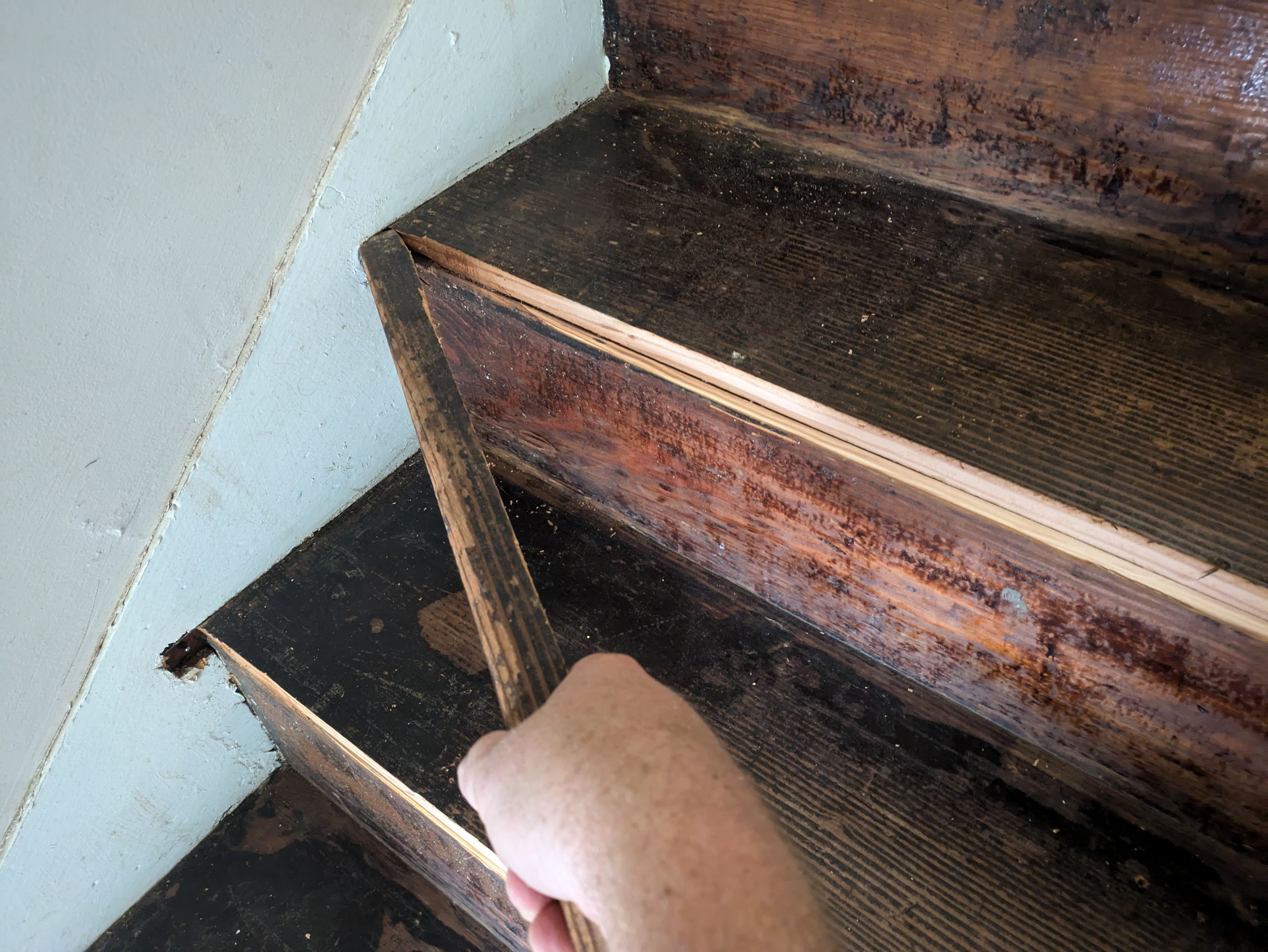
The nosing easily splits at the stringer. I'll pull the nosing all the way out of the stringer. These gaps will be hidden by the new skirtboard.
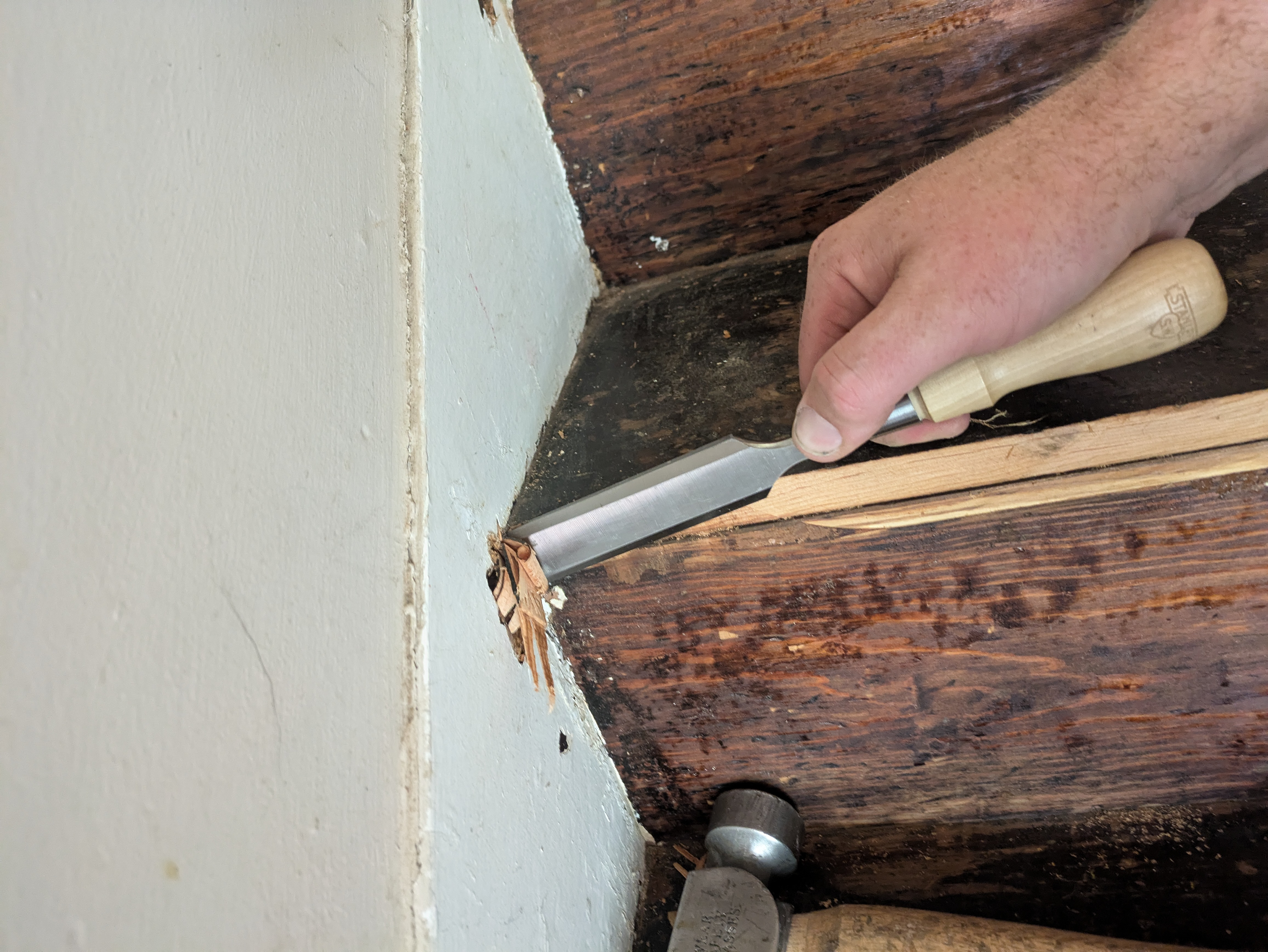
I'm trimming the treads flush to the risers when I had split them off earlier. A sharp chisel makes quick work of this.
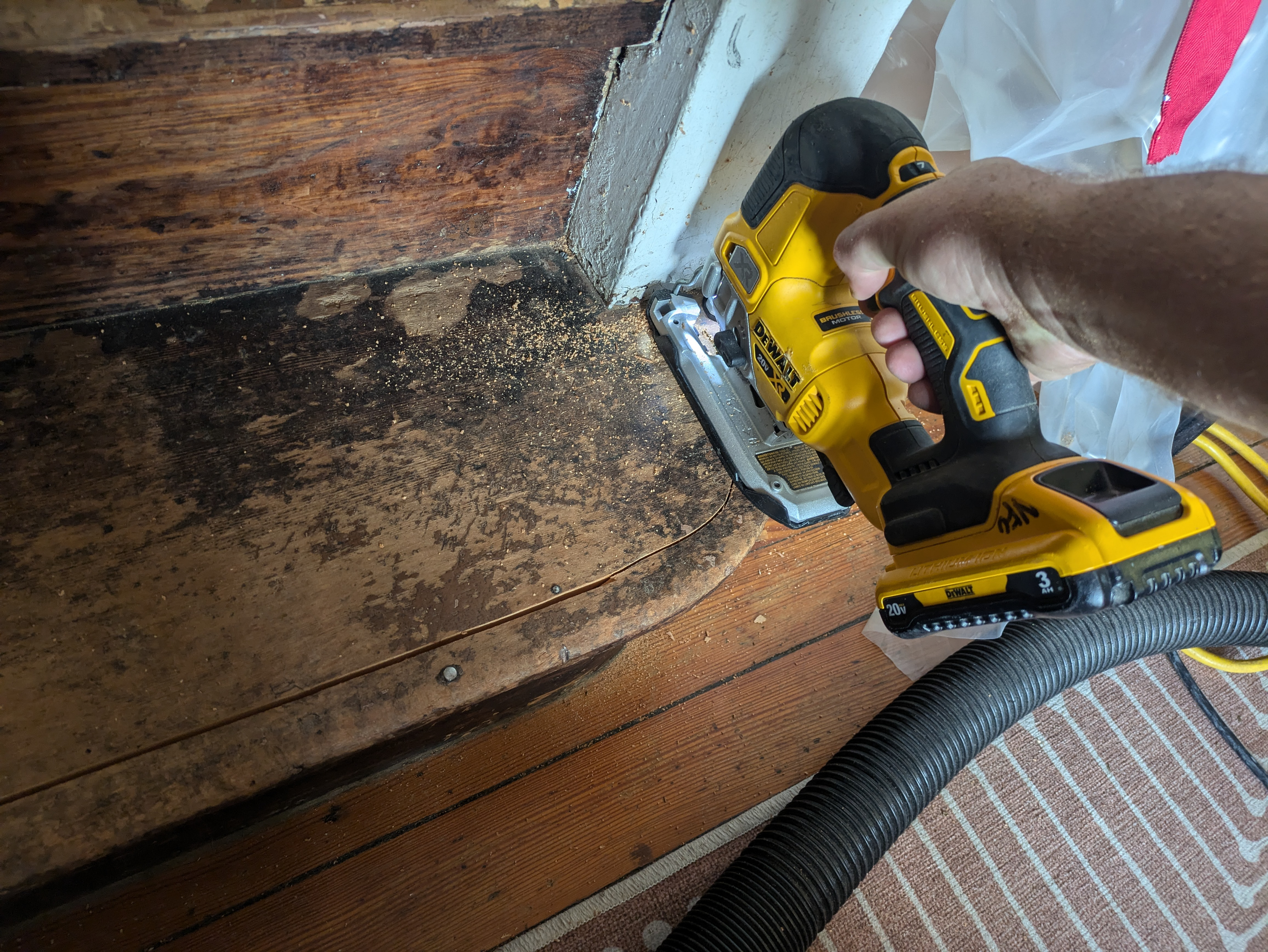
I'm using a jigsaw to remove the curved section of this tread's nosing.
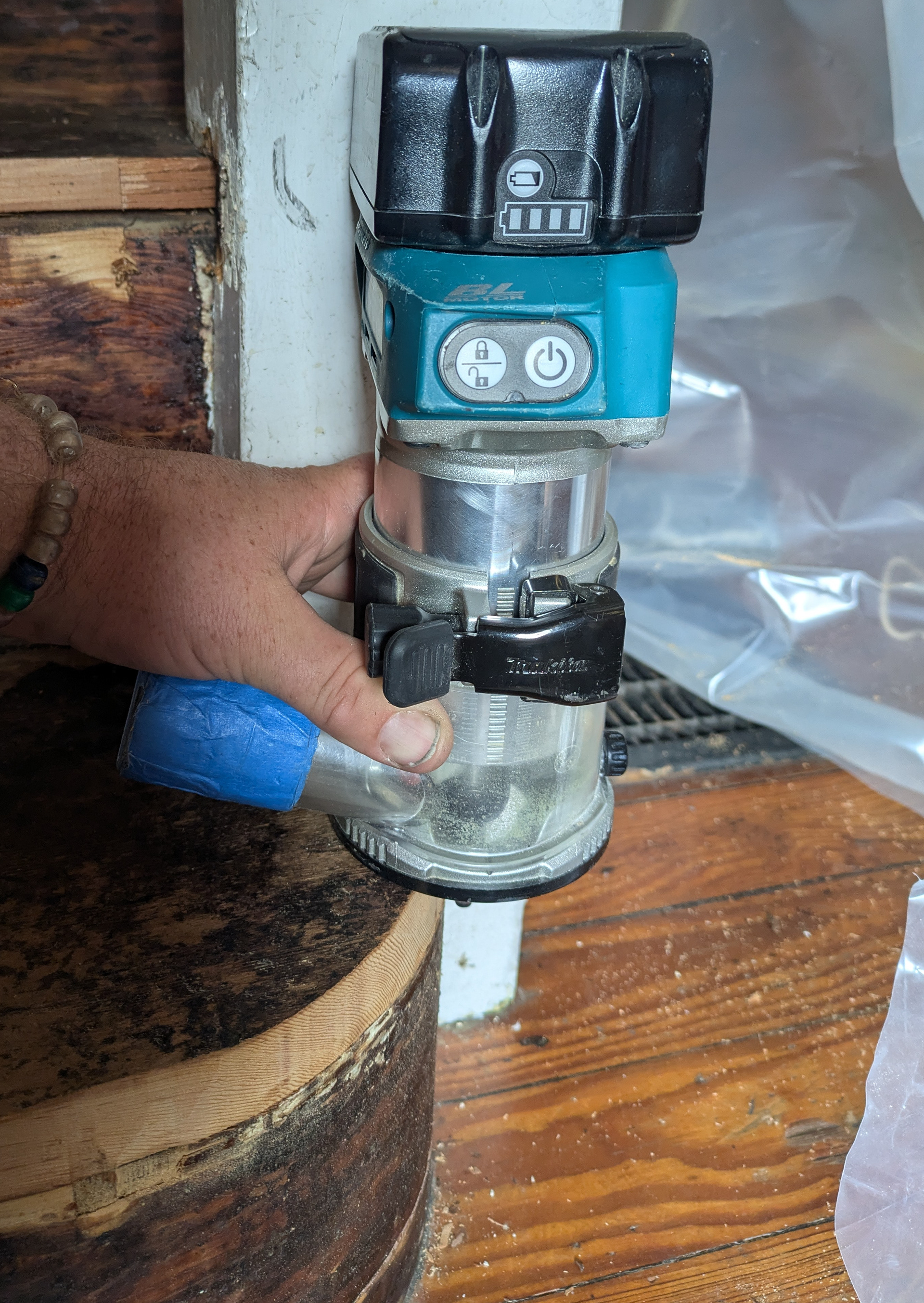
Cleaning things up with a router and flush cutting bit.
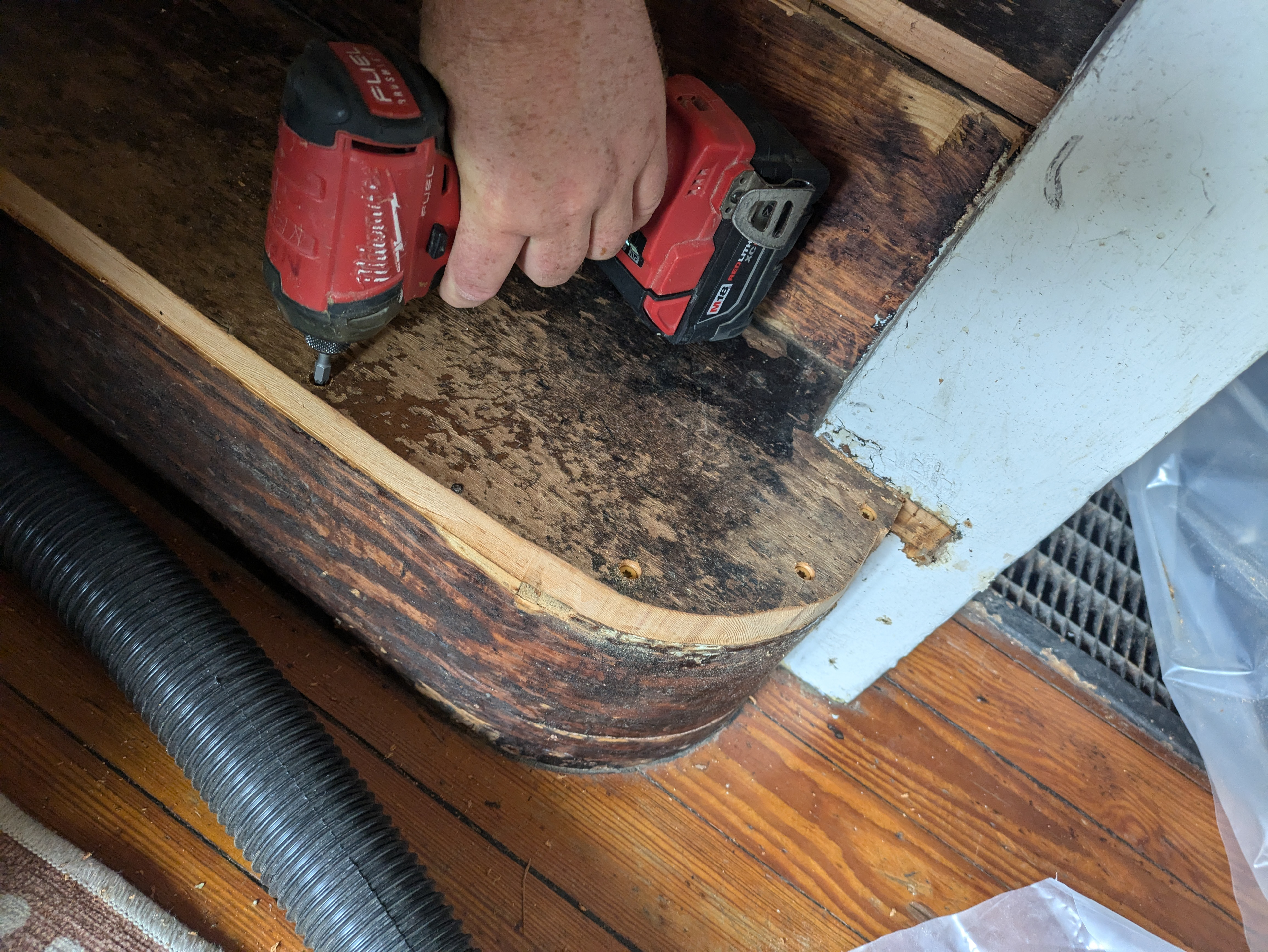
I pre-drilled and countersunk some pilot holes in the treads. Now I'm securing the treads to the risers below with some framing screws.
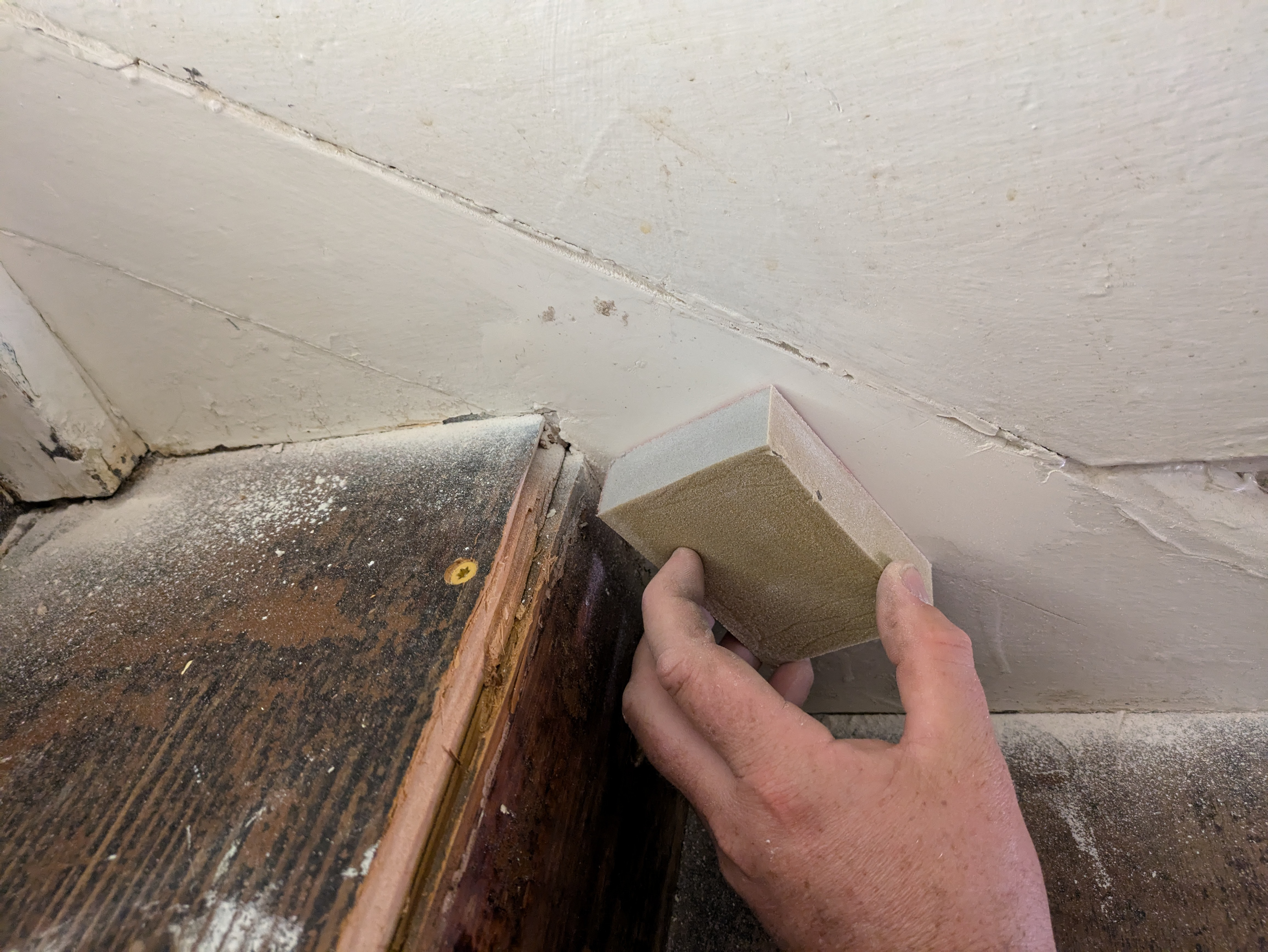
The balustrade-side stringer will remain visible when I'm done with the project so I've brad nailed the nub of nosing which remains in the housed stringer's dado in place. I filled the shallow void with m.h. ready patch, now I'm sanding the patches flush with the surrounding stringer surface. Next, I'll prime and paint the balustrade-side stringer.
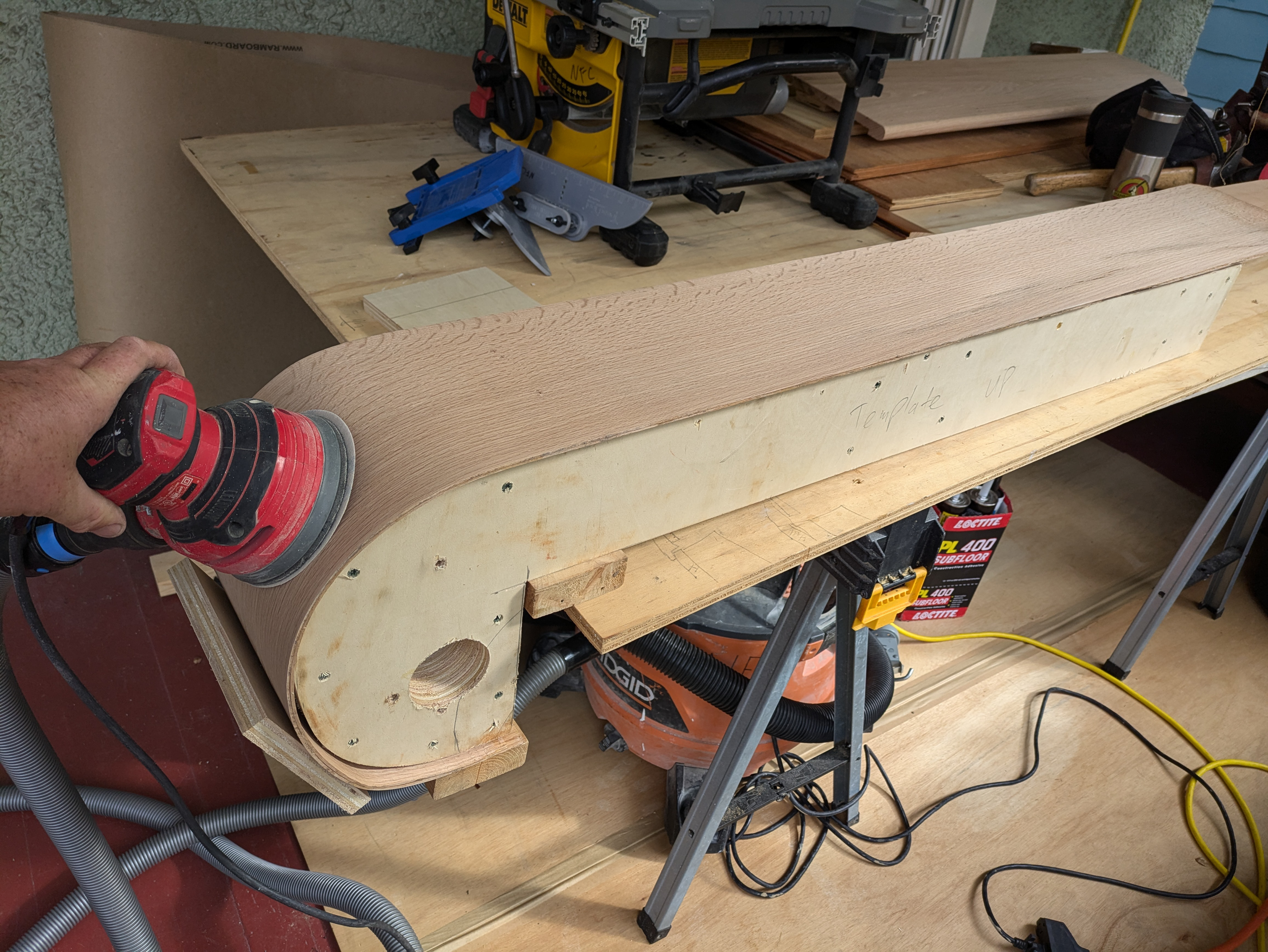
I'm machine sanding with 150 grit. Next I'll raise the grain with a damp rag. When the moisture evaporates I'll do a final hand sanding with 220 grit. This will reduce the grain-raise from the staining process.
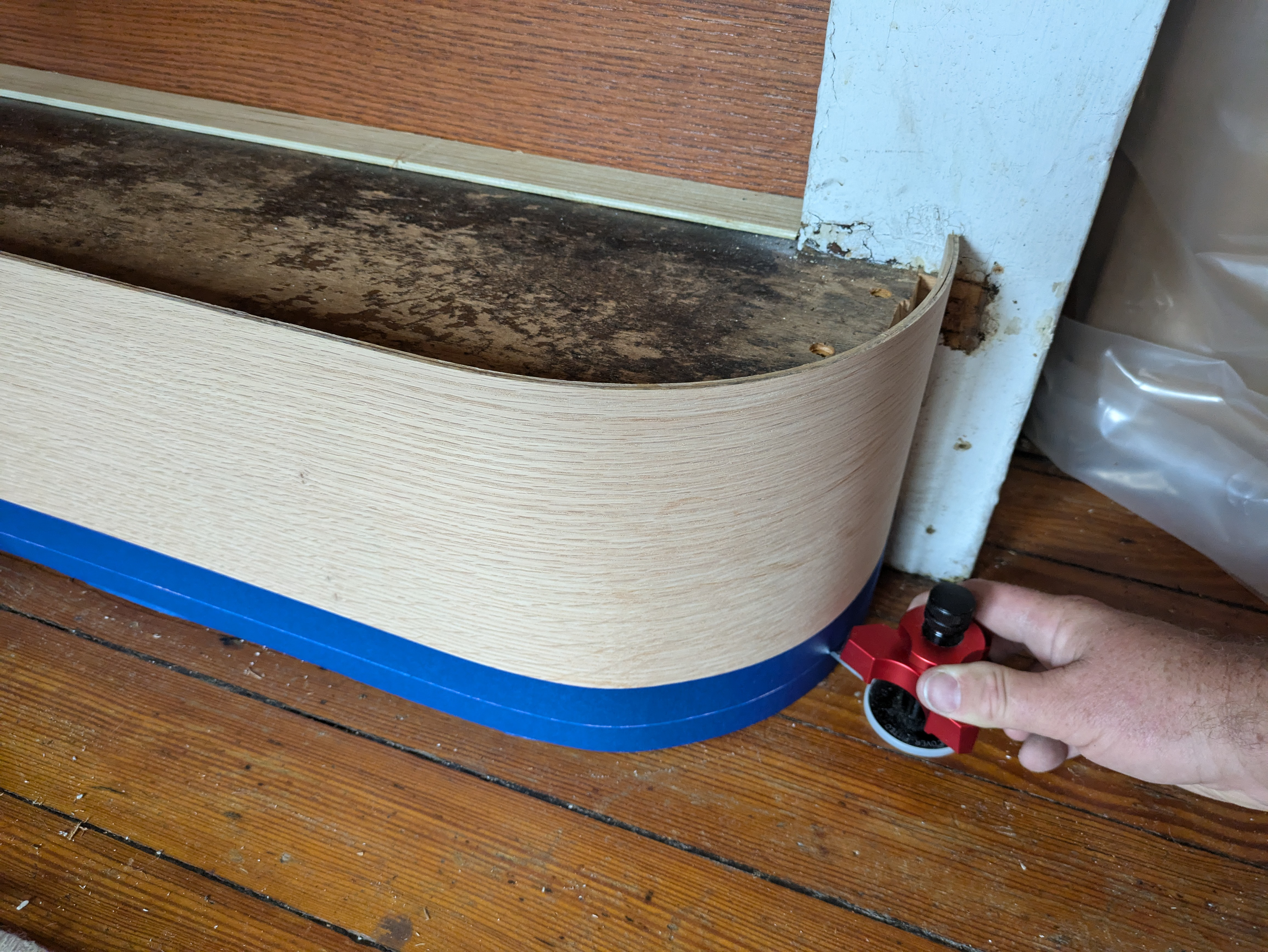
I'm scribing the riser to the floor. The tape makes it easier to see the scribed line.
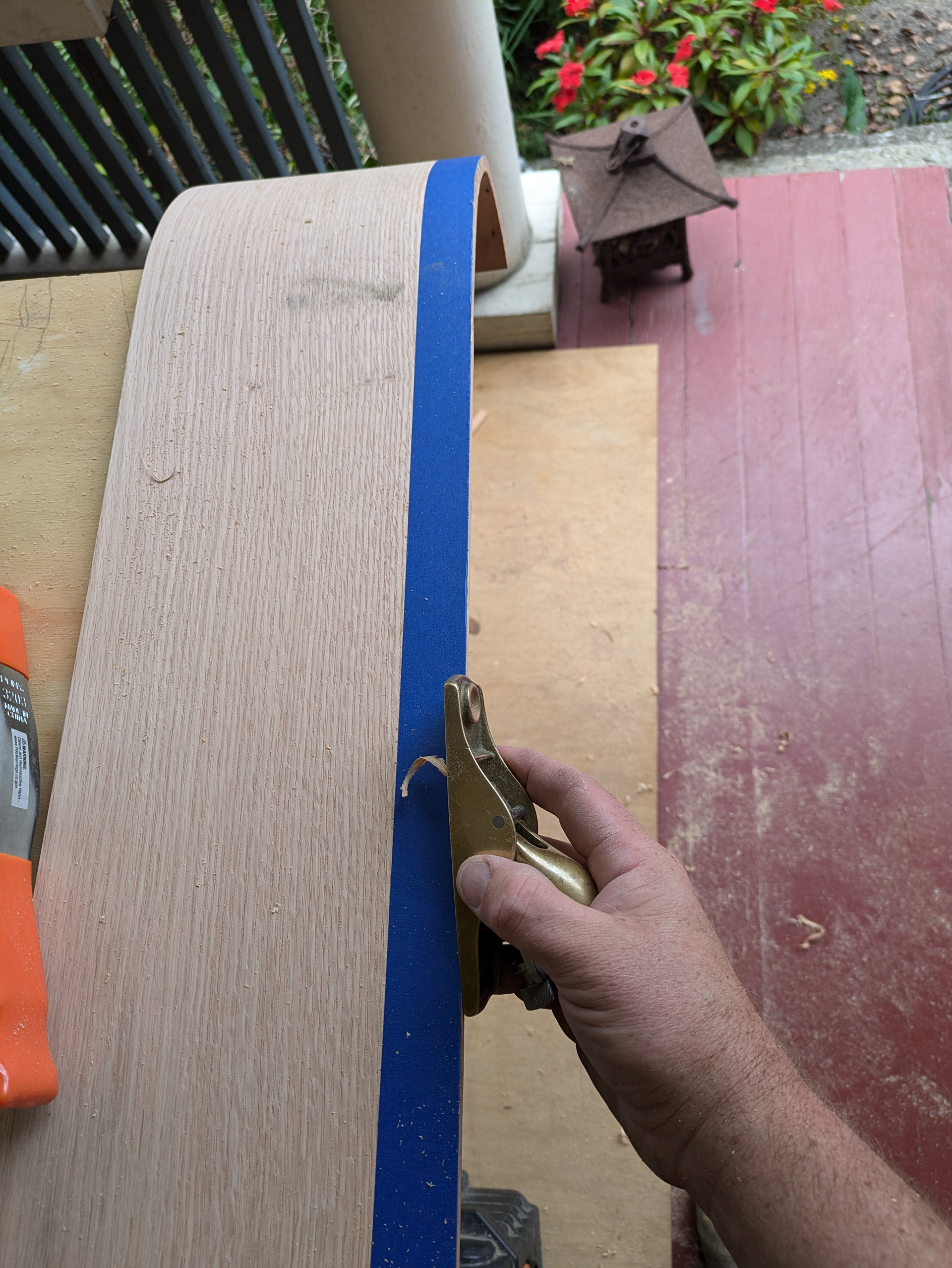
I rip cut the risers to the scribed line as closely as I dare. Now I'm cleaning up the saw marks and knocking down a couple of high spots with a block plane.
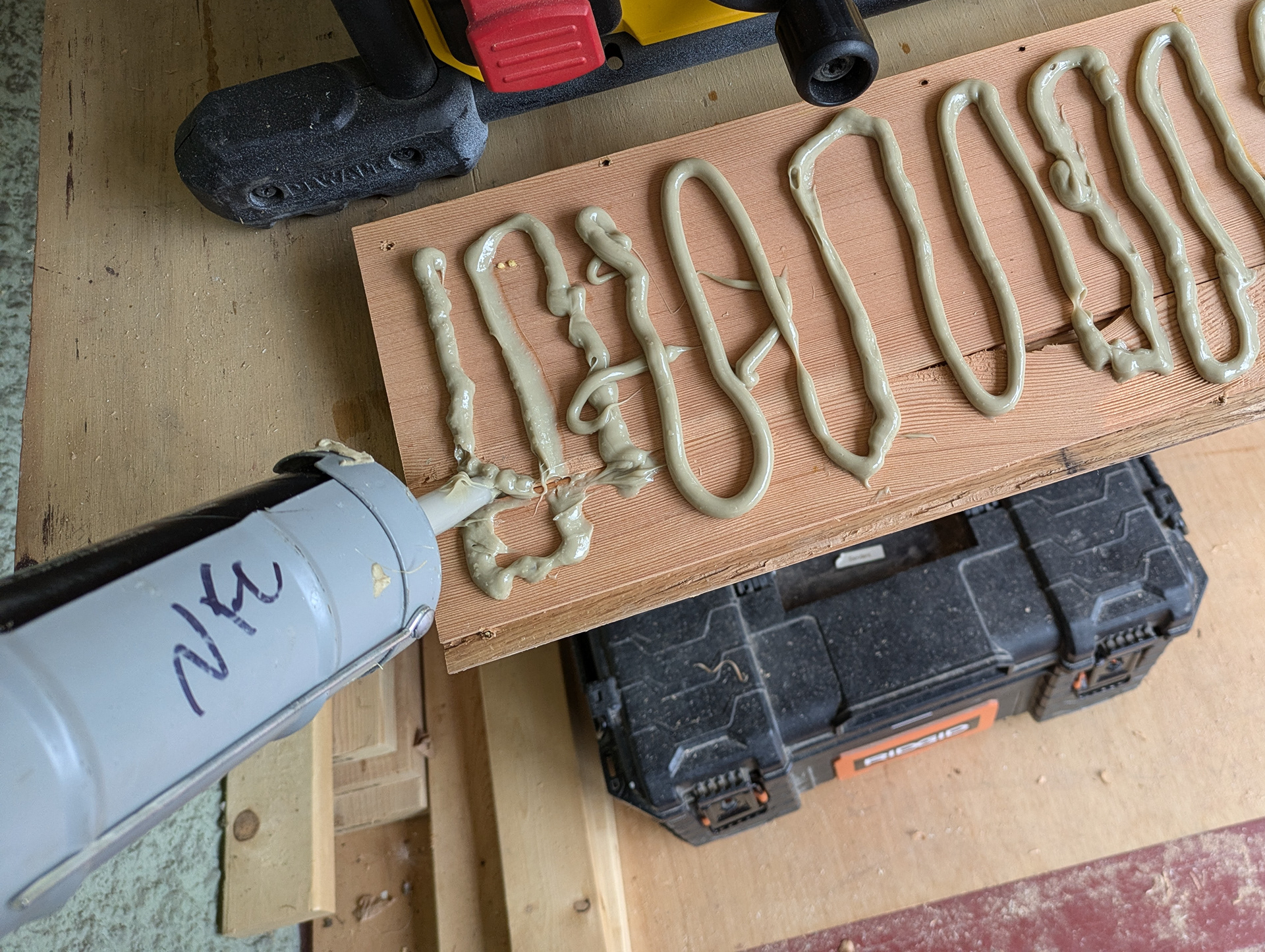
PL premium is a construction adhesive that has some elasticity once it cures. This makes it an excellent adhesive for stair parts. This is the backside of the curved riser that I'm gluing.
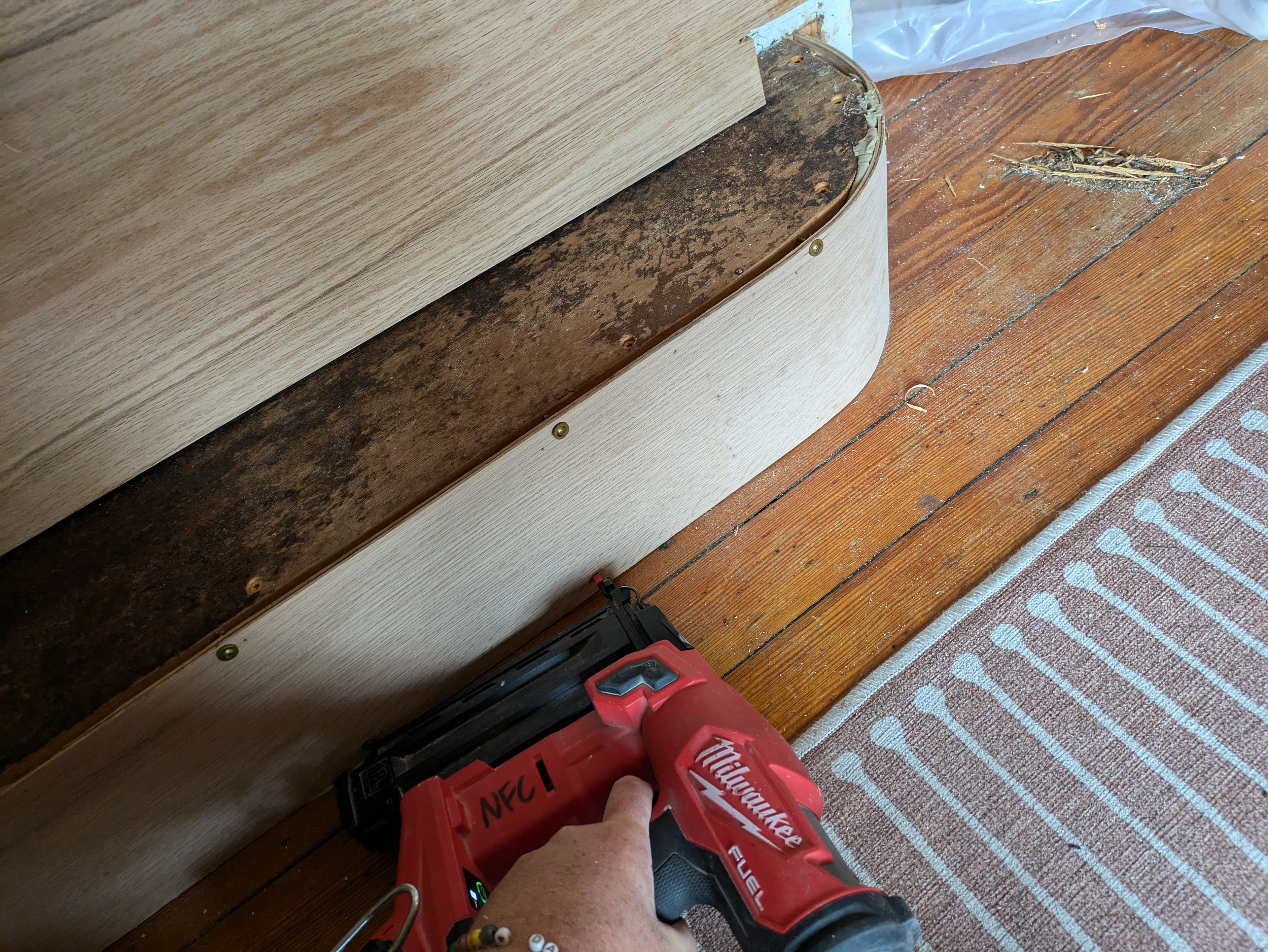
A few washer head screws and brad nails will hold the riser in place as the glue cures. Before setting the tread I'll pull the screws. The fastener holes along the top edge of the riser will be hidden by the tread nosing.
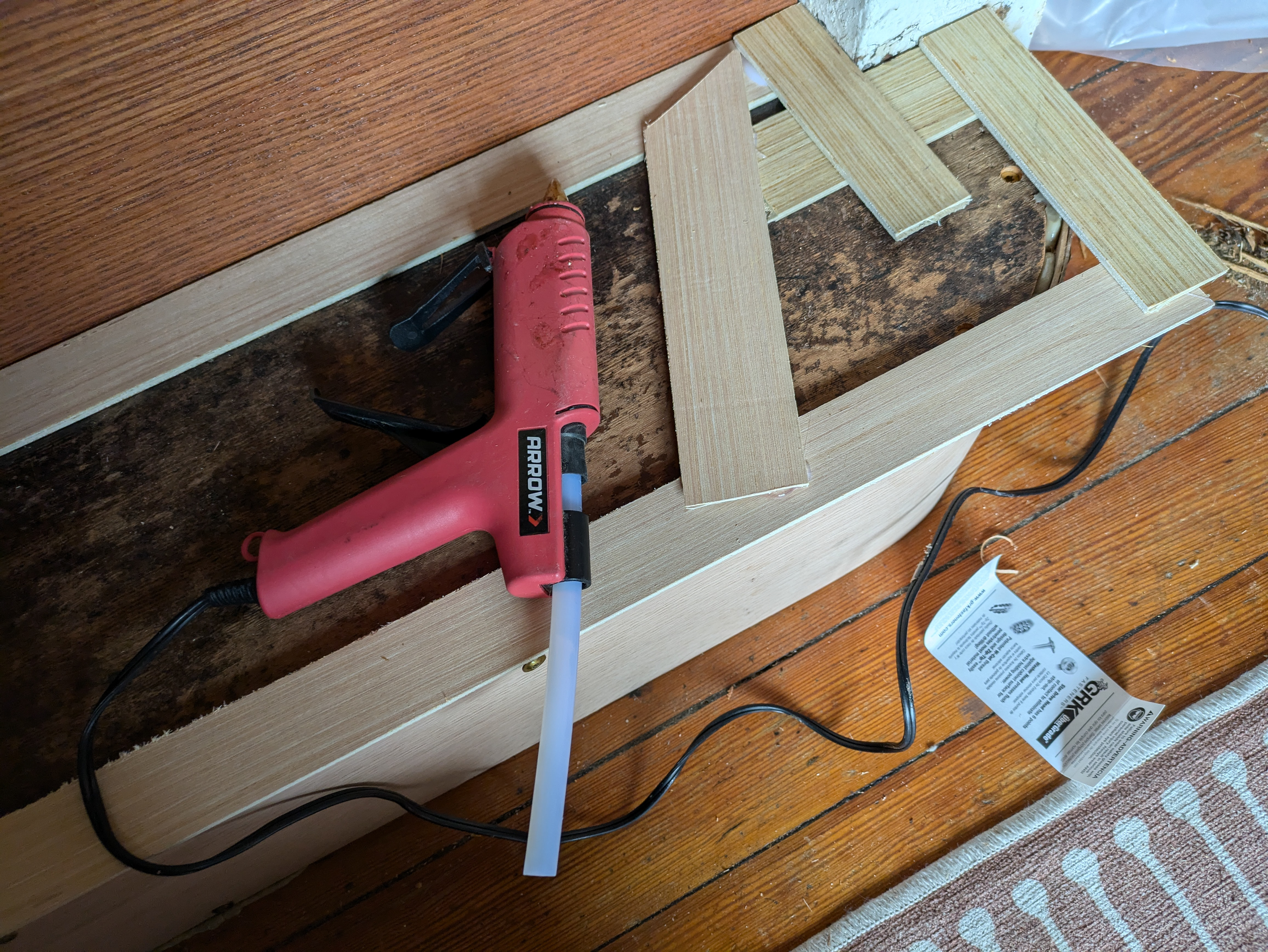
I'm building a template for the tread using strips of luan and a hot glue gun.
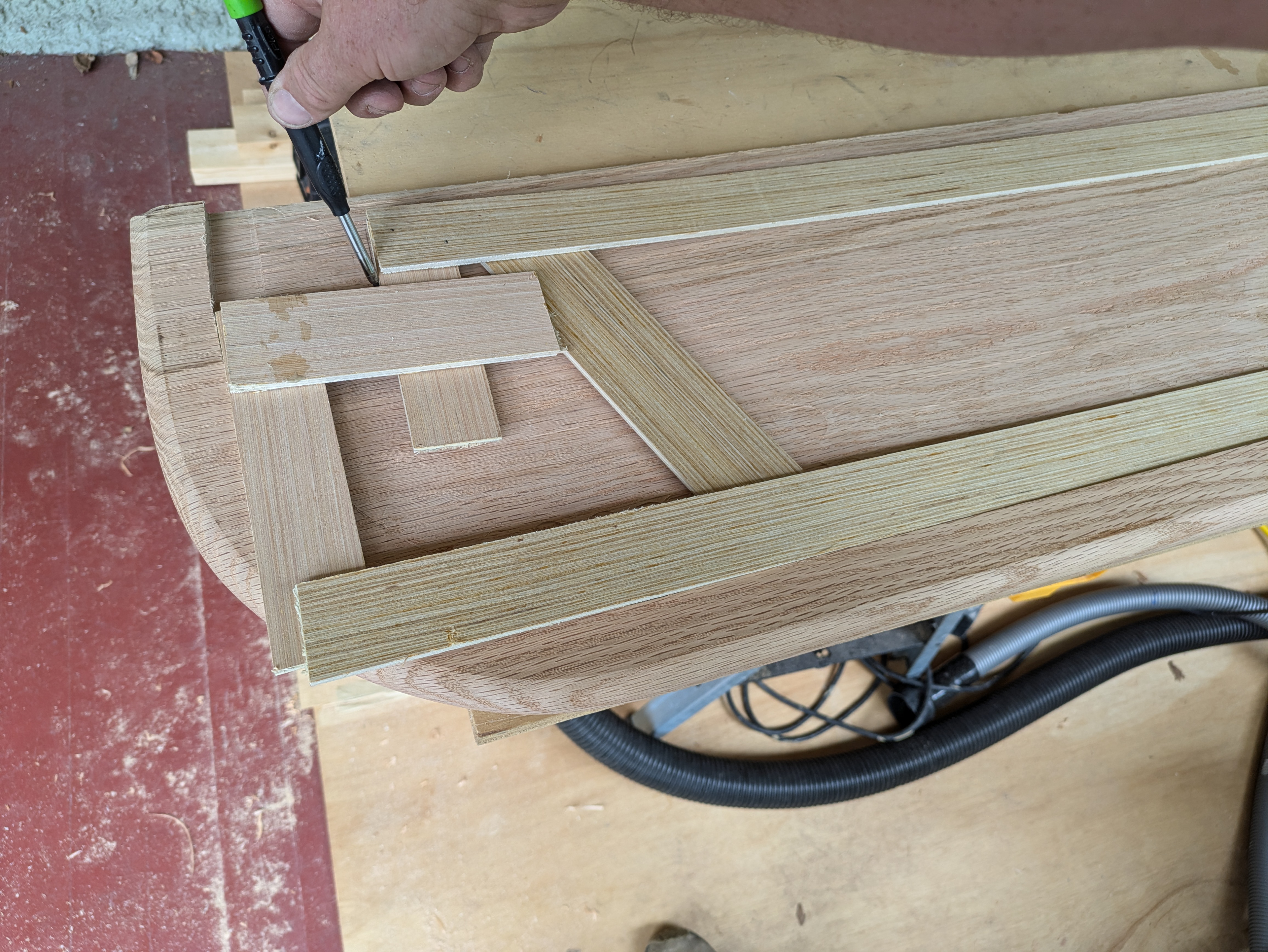
I'm tracing the rip cut-line and the newel post cut out onto the bottom of the tread.
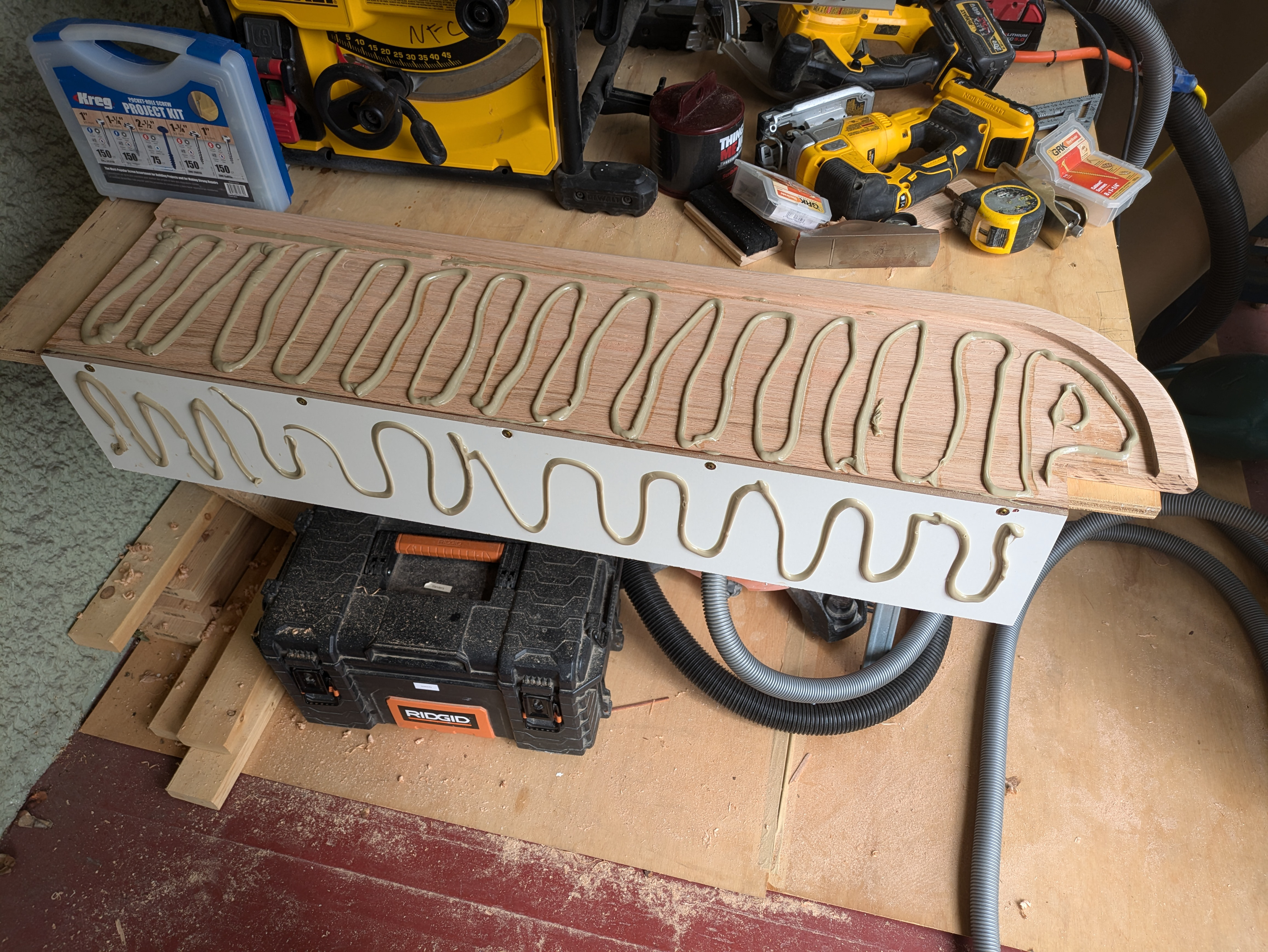
I've scribed the first straight riser to the right side stringer. I also glued and screwed the riser to the back edge of the tread. This sub assembly has a bunch of PL construction adhesive on it.
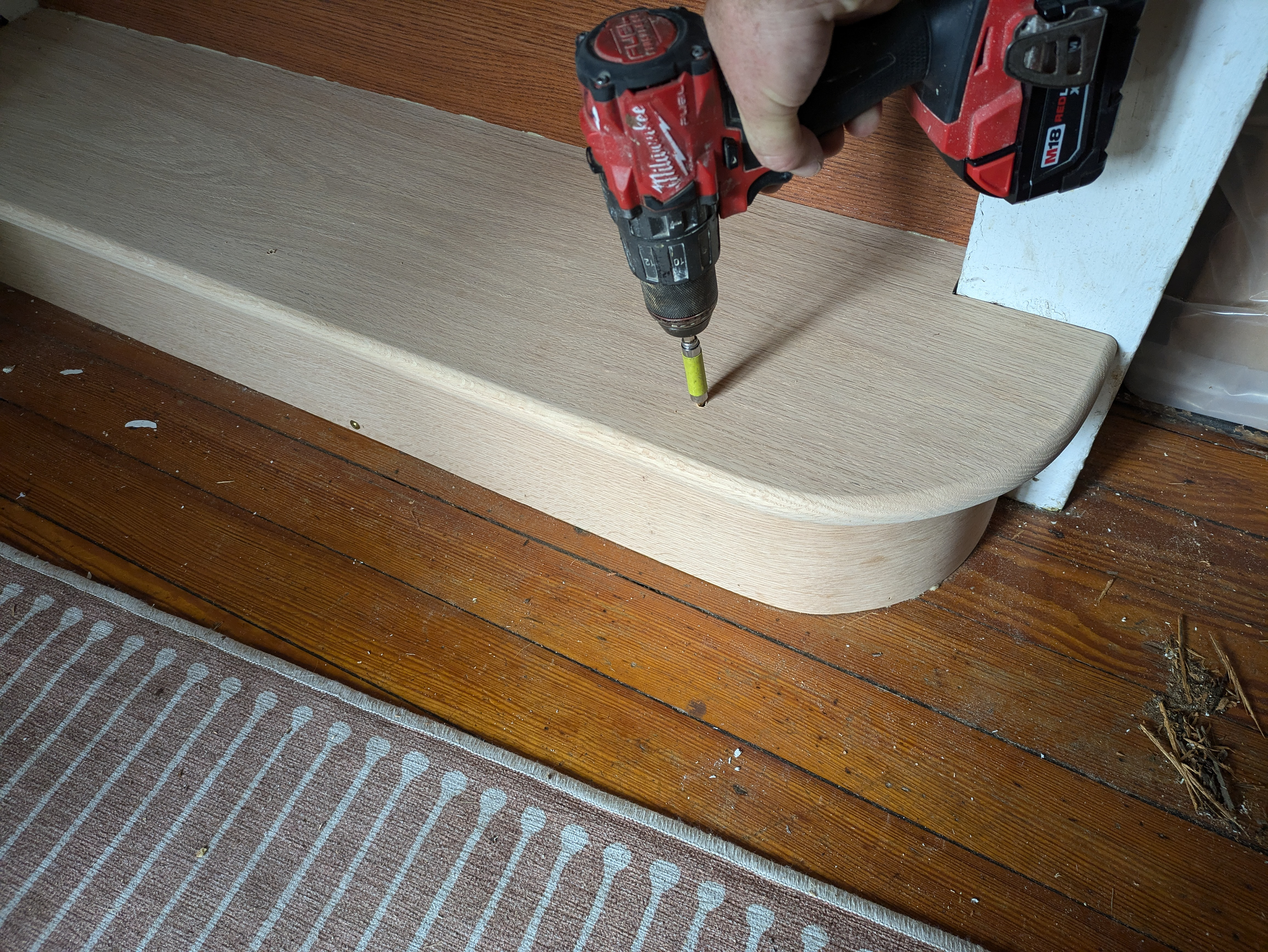
4 screws through the tread will hold it in place while the glue cures. I've brad-nailed the new riser to the old staircase up high where the next tread nosing will hide the nail holes.
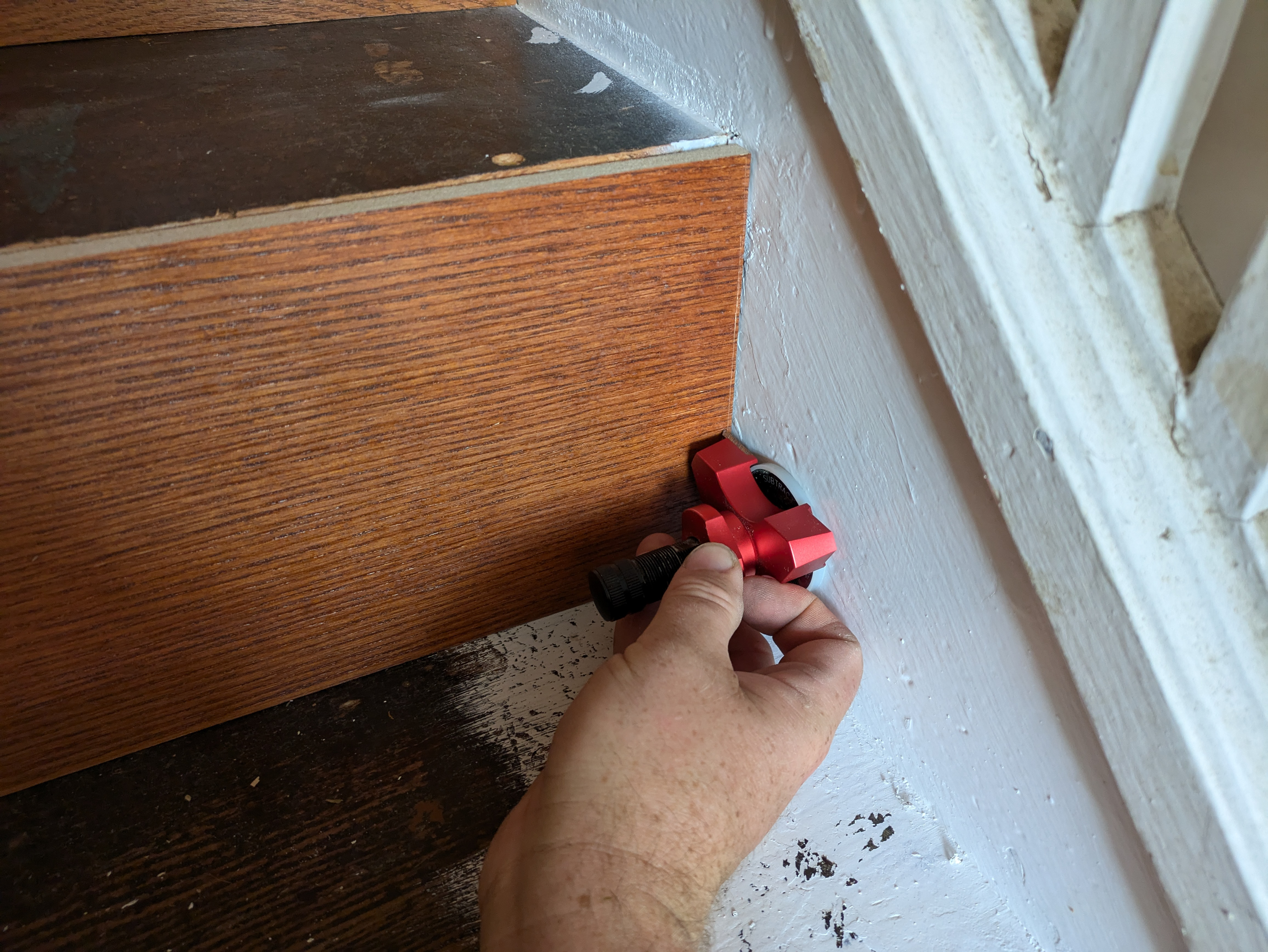
I'm scribing each riser to the balustrade-side stringer.
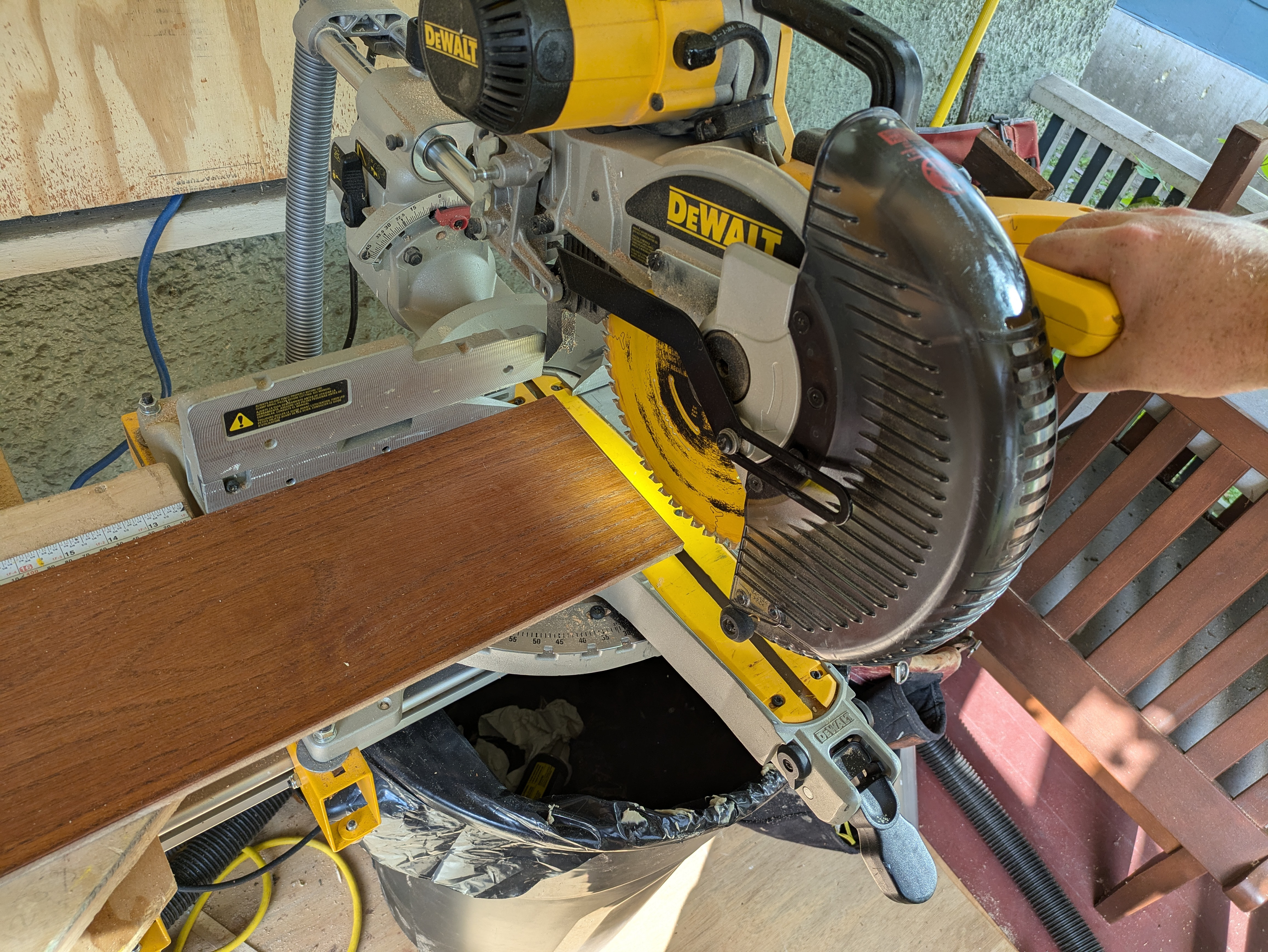
Cross cutting the risers with a miter saw can chip the oak veneer of these MDF core risers. I've depend the scribe mark with a sharp utility blade to prevent chipping. I'll also scribe and cut each tread in the same fashion
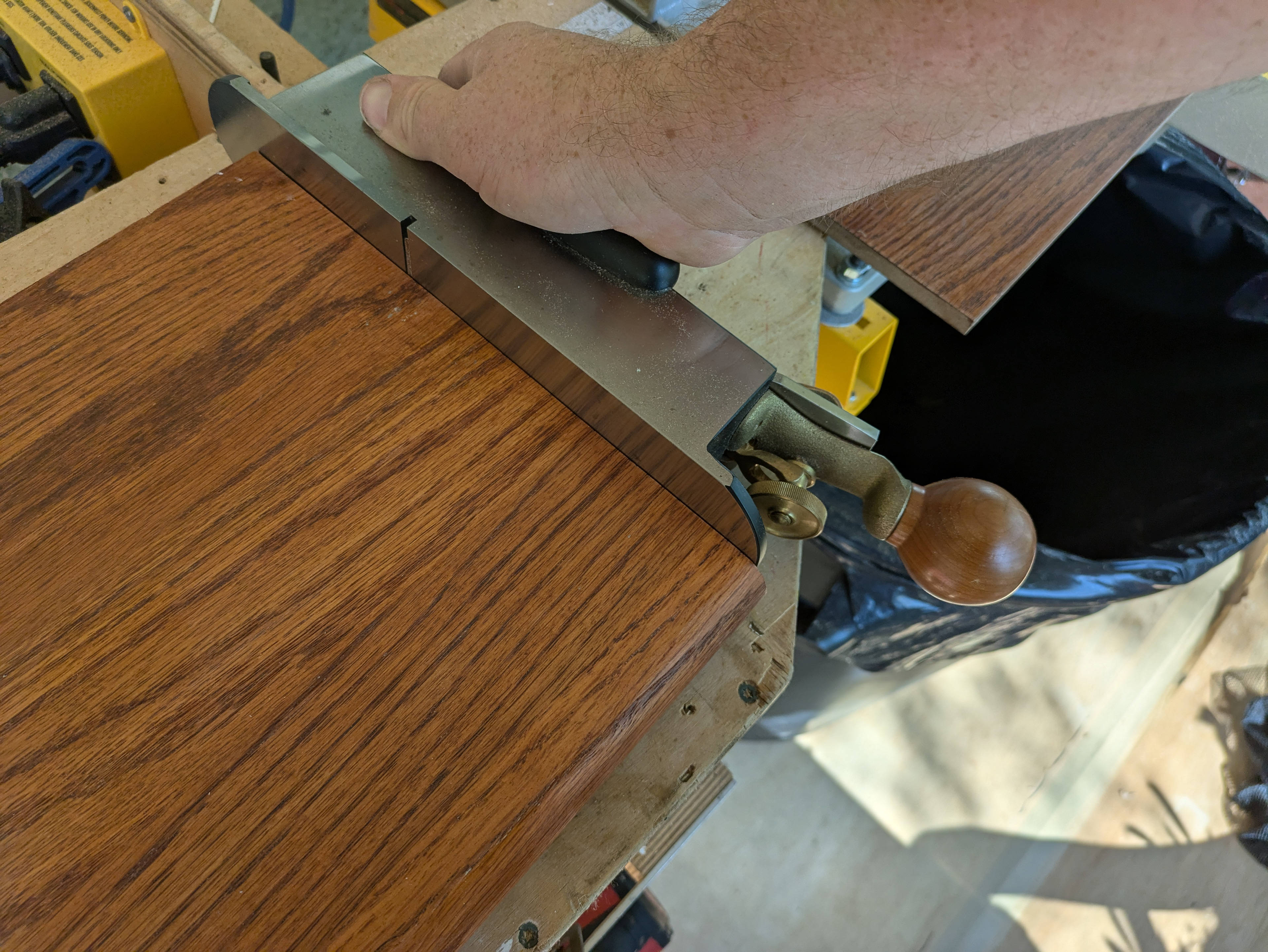
A miter plane cleans up the saw marks and helps me dial in the fit. If the scribed line isn't straight I'll dial in the straight miter saw cut by skewing the plane so I can get after the low spots.
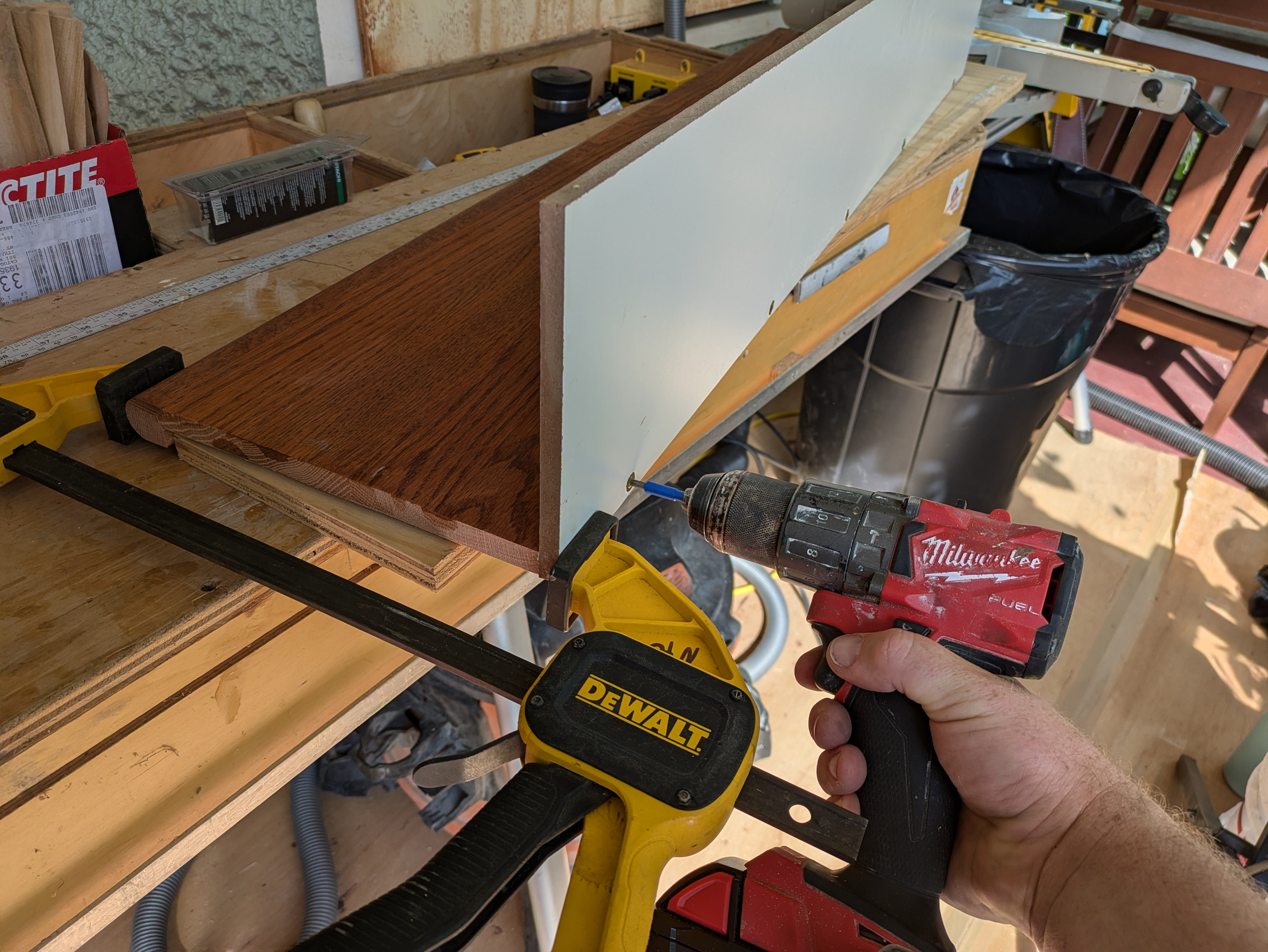
I'm pre-assembling each tread to the riser above with PL premium and some cabinet screws. I'll let any PL squeeze out start to set up before I scrape it away with a sharp chisel or putty knife.
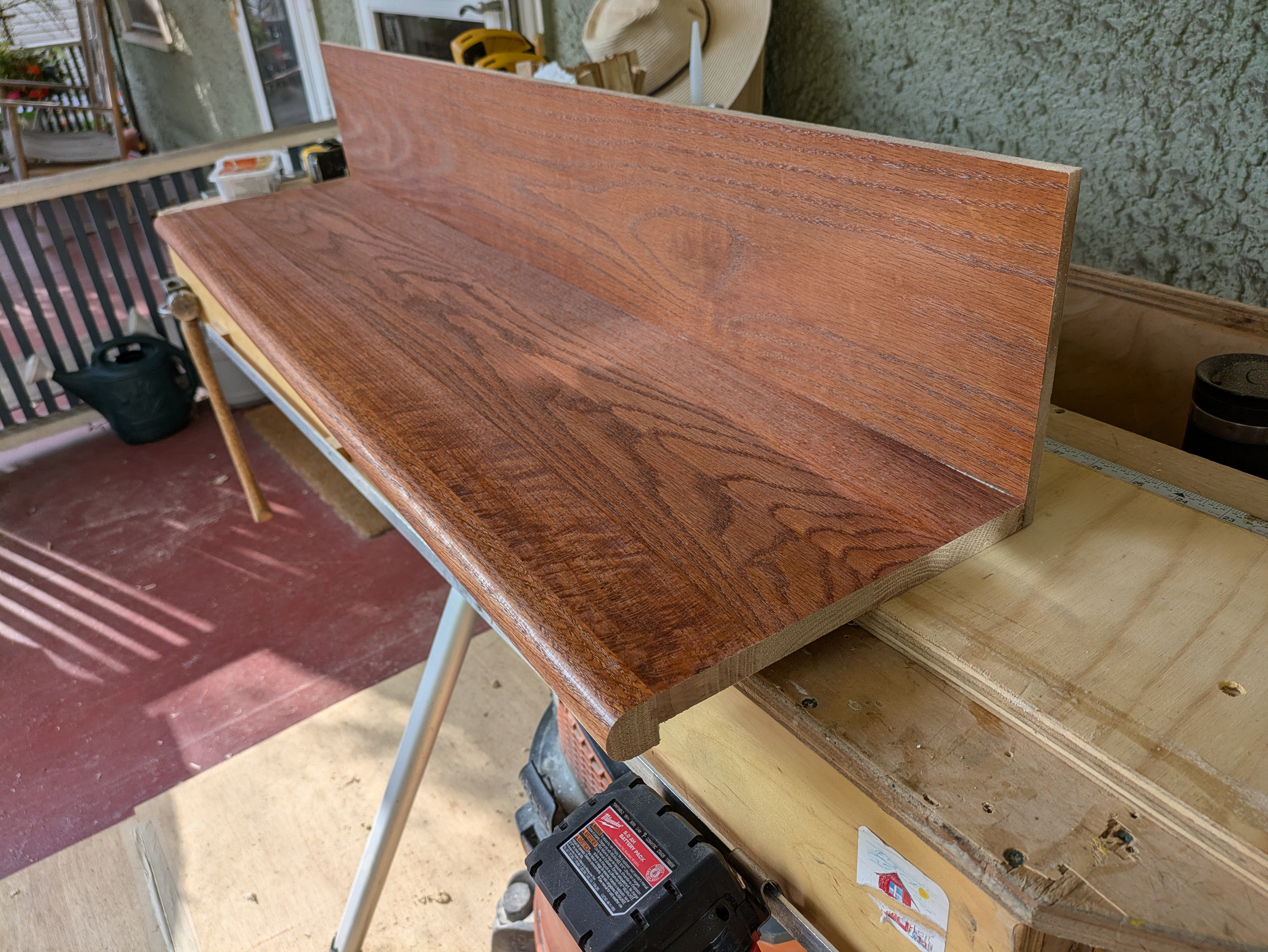
This sub assembly is ready for installation.
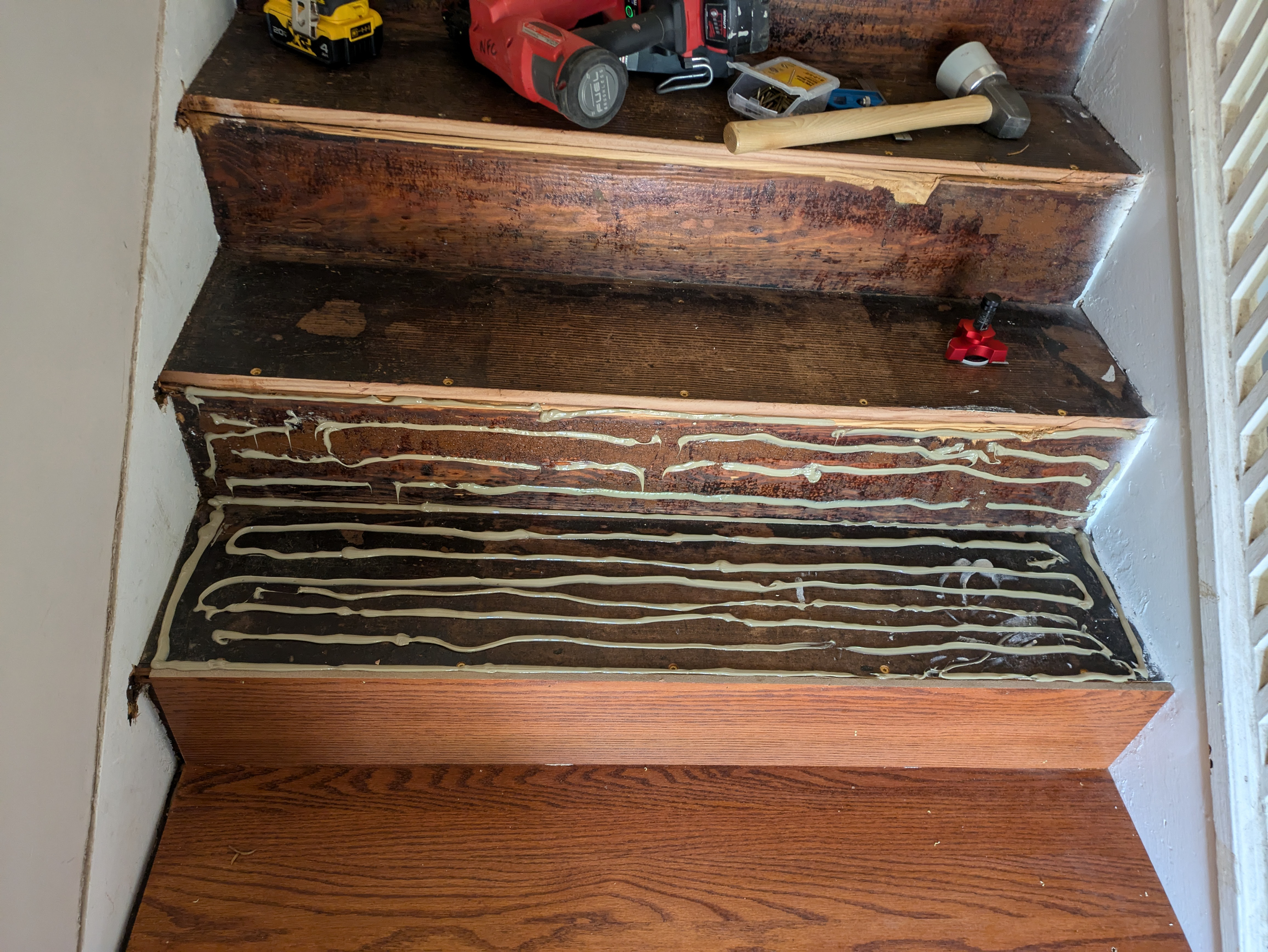
Construction adhesive on the old treads and risers will make for a stiffer, squeek free set of new stairs.
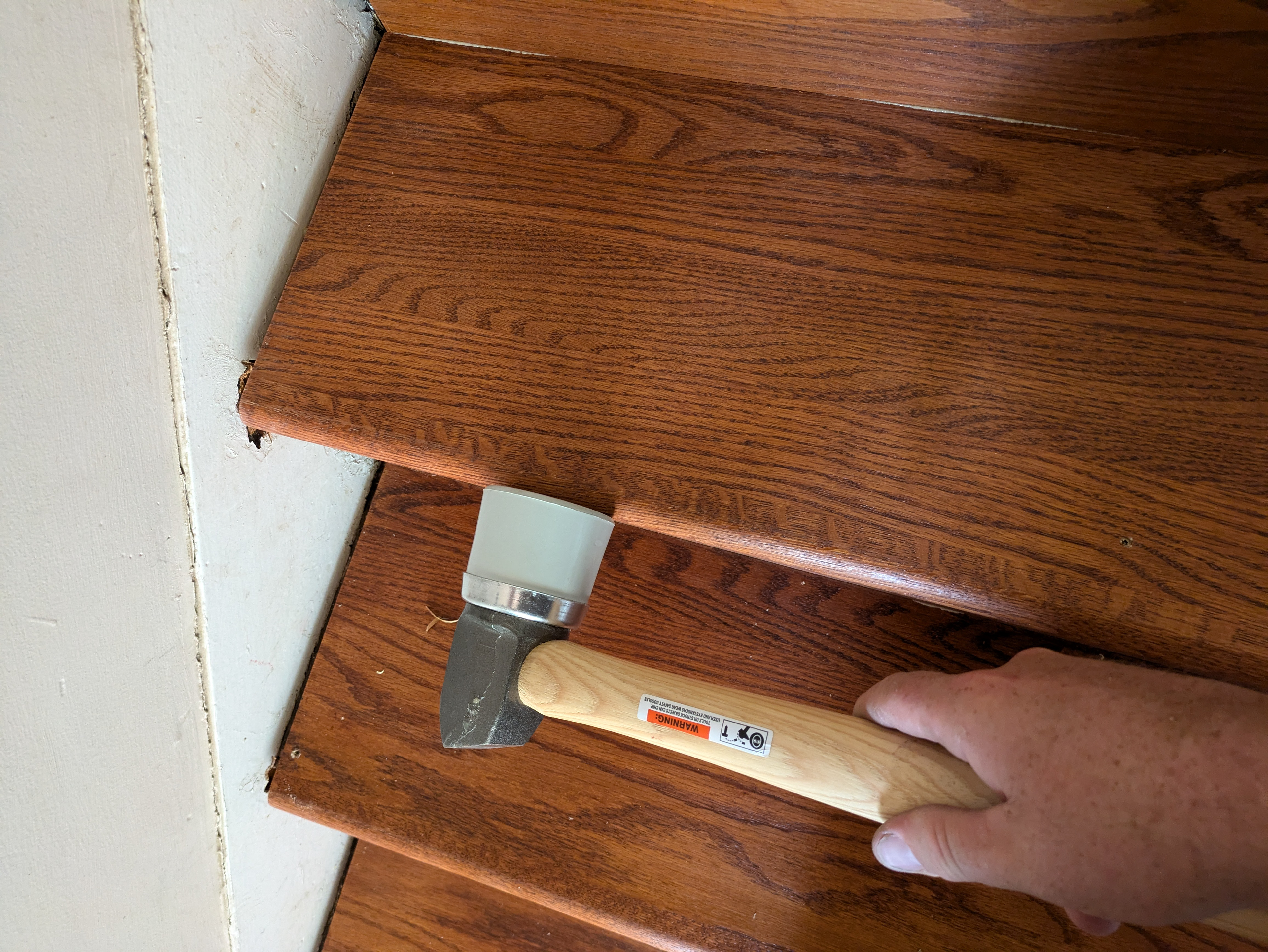
A rubber mallet pushes the assembly all the way back to the original riser and down onto the original tread.

A prybar holds the assembly tight to the stringer on the balustrade side as I set a couple of screws through the tread.
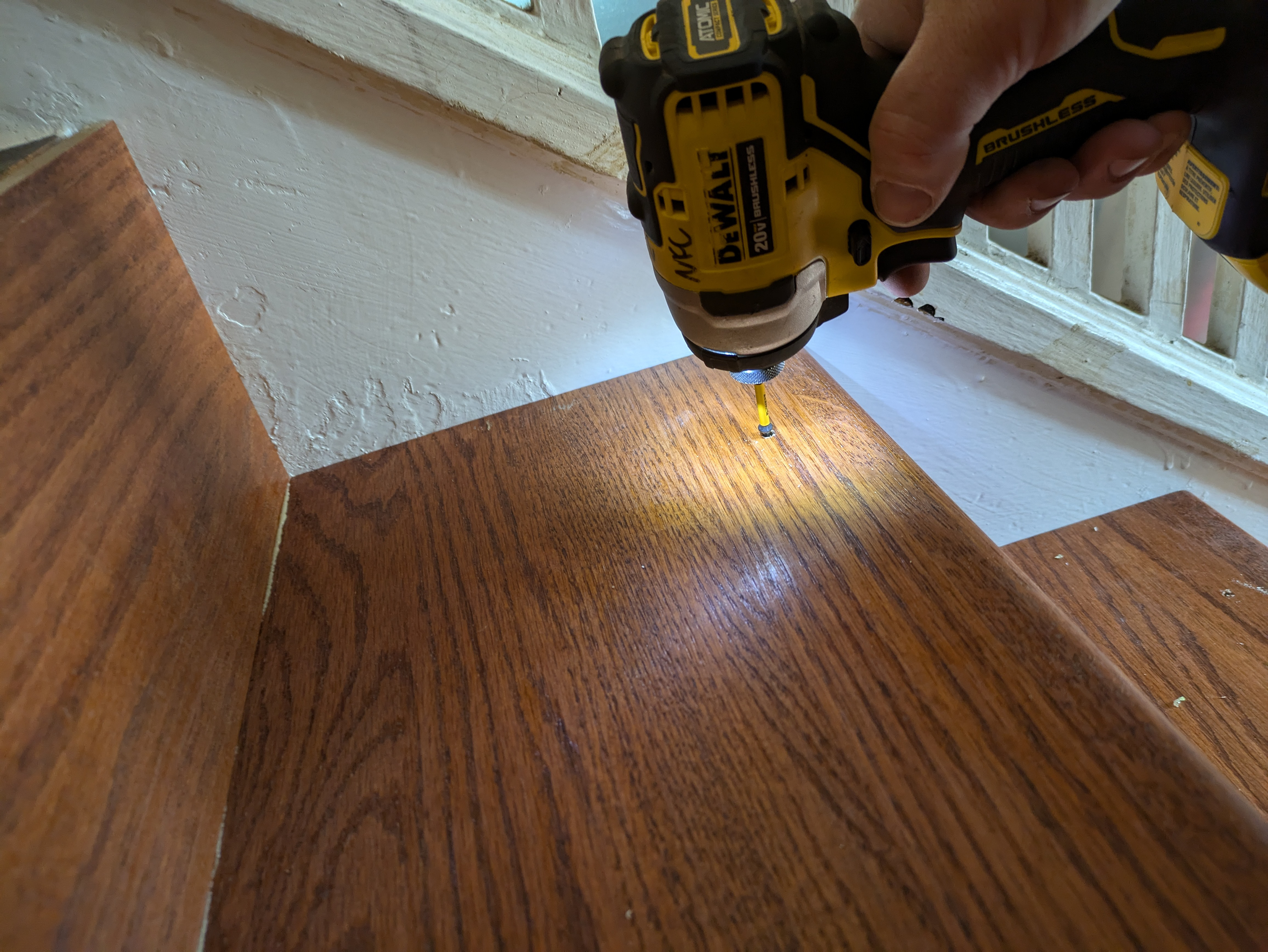
Three trim screws across the front of the tread hold the tread down as the glue cures.
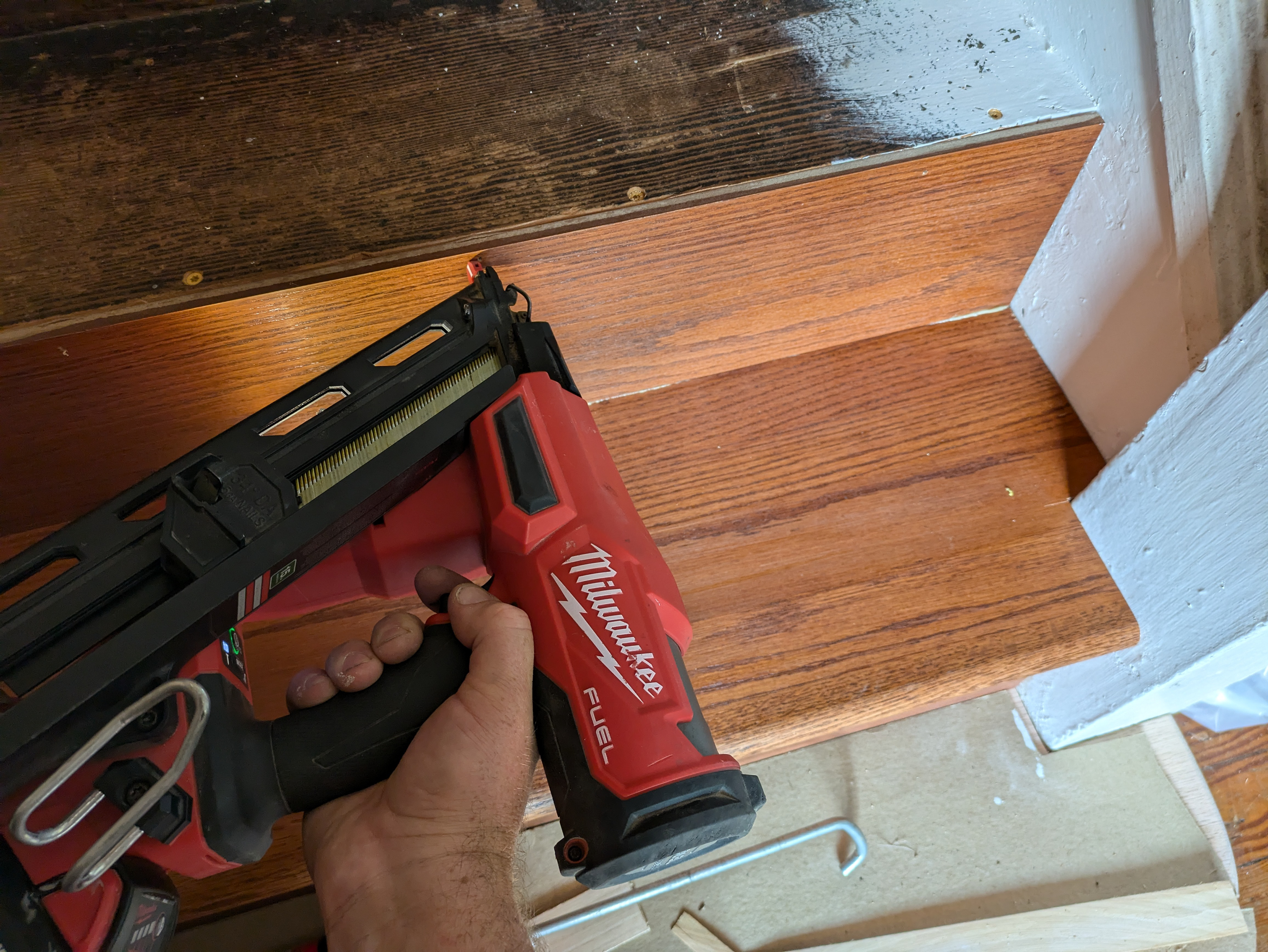
15 gauge nails hold the riser in place.
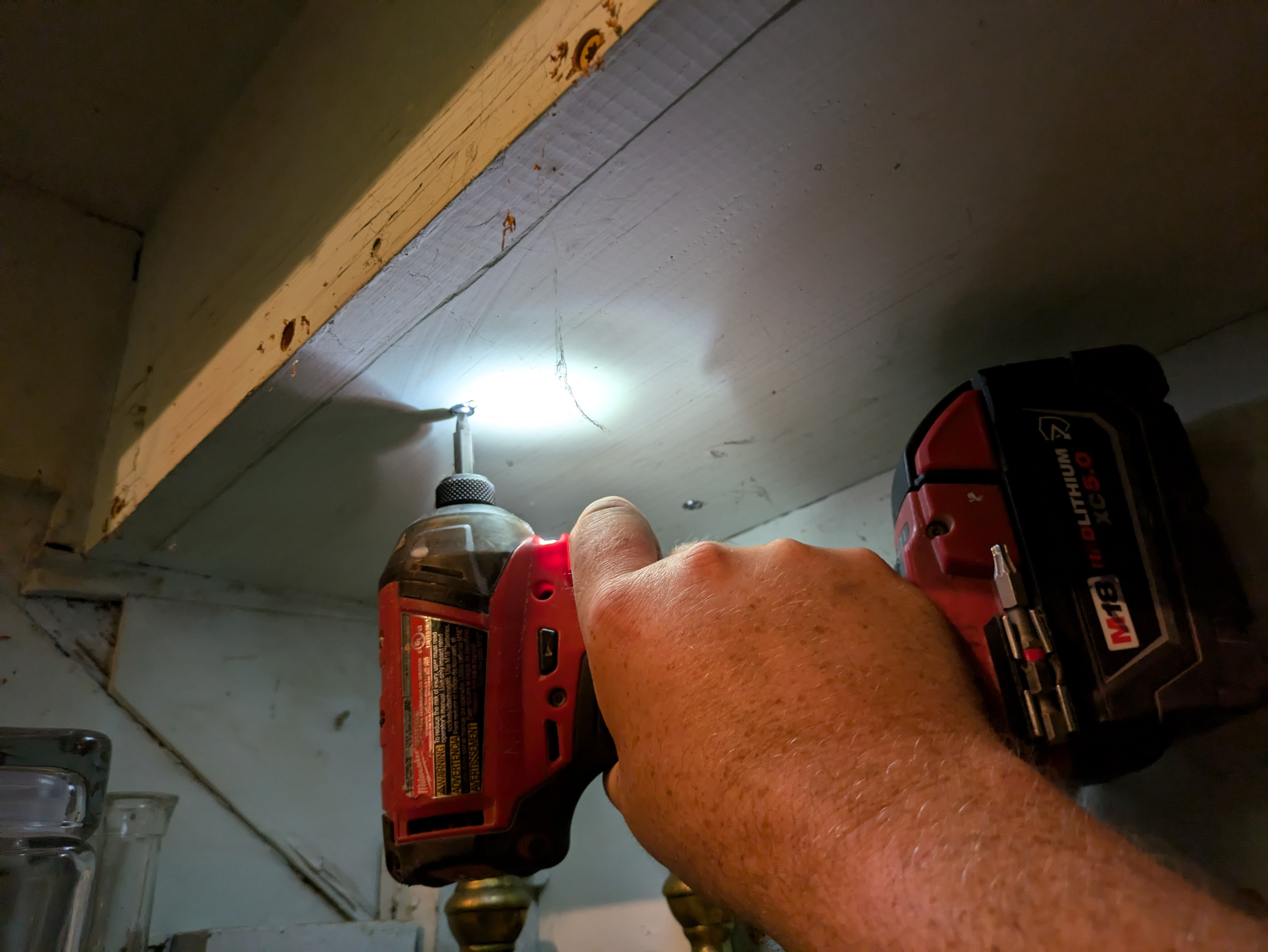
Washer-head course-thread screws screwed up into the retro treads from below will secure the old treads to the new treads with minimal visible fasteners appearing above.
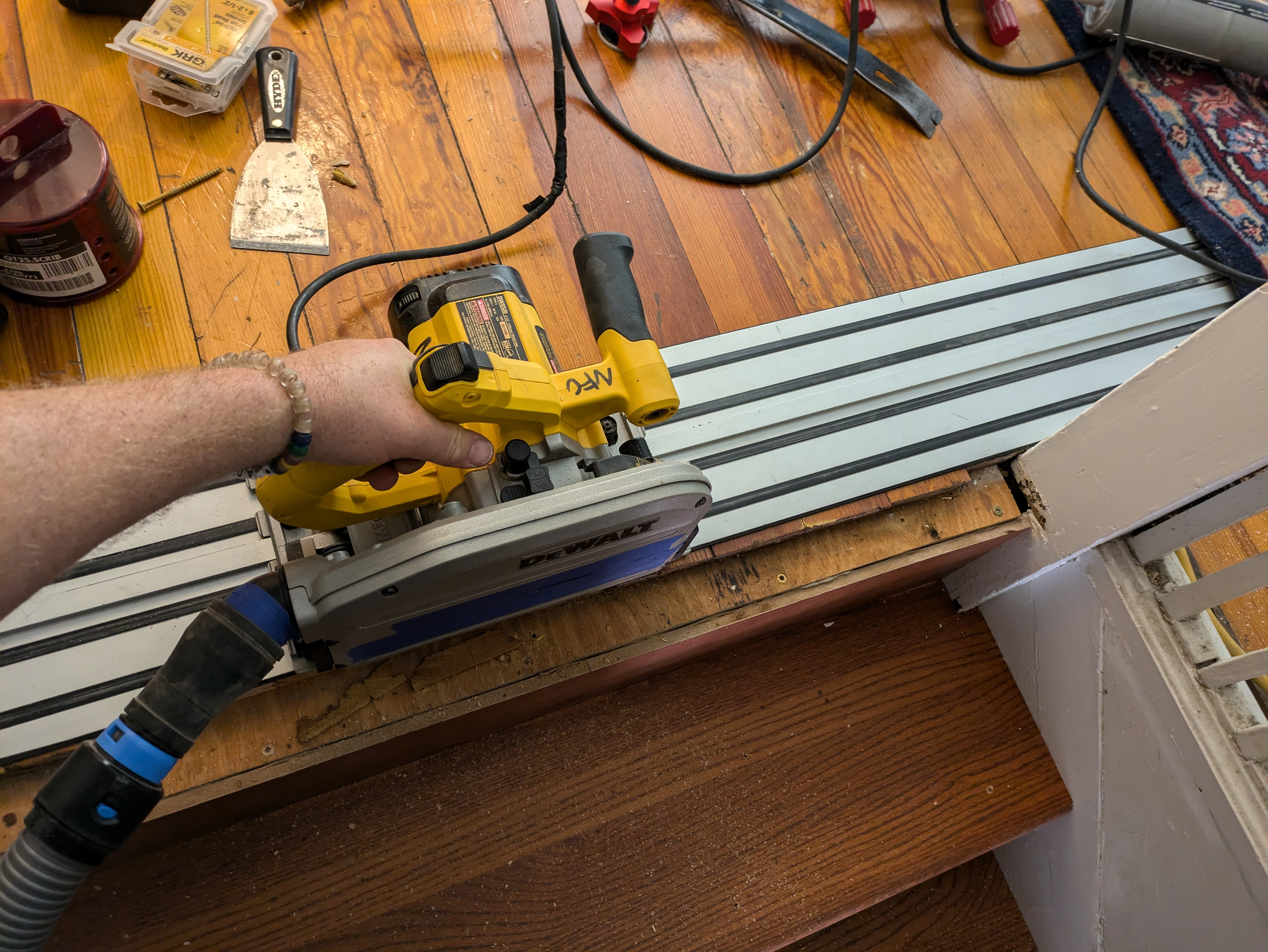
Preparing the 2nd floor for the landing tread. A track saw followed up with a buzzy saw cut at each end provides a nice looking straight line to which I can attach the landing tread with a spline.
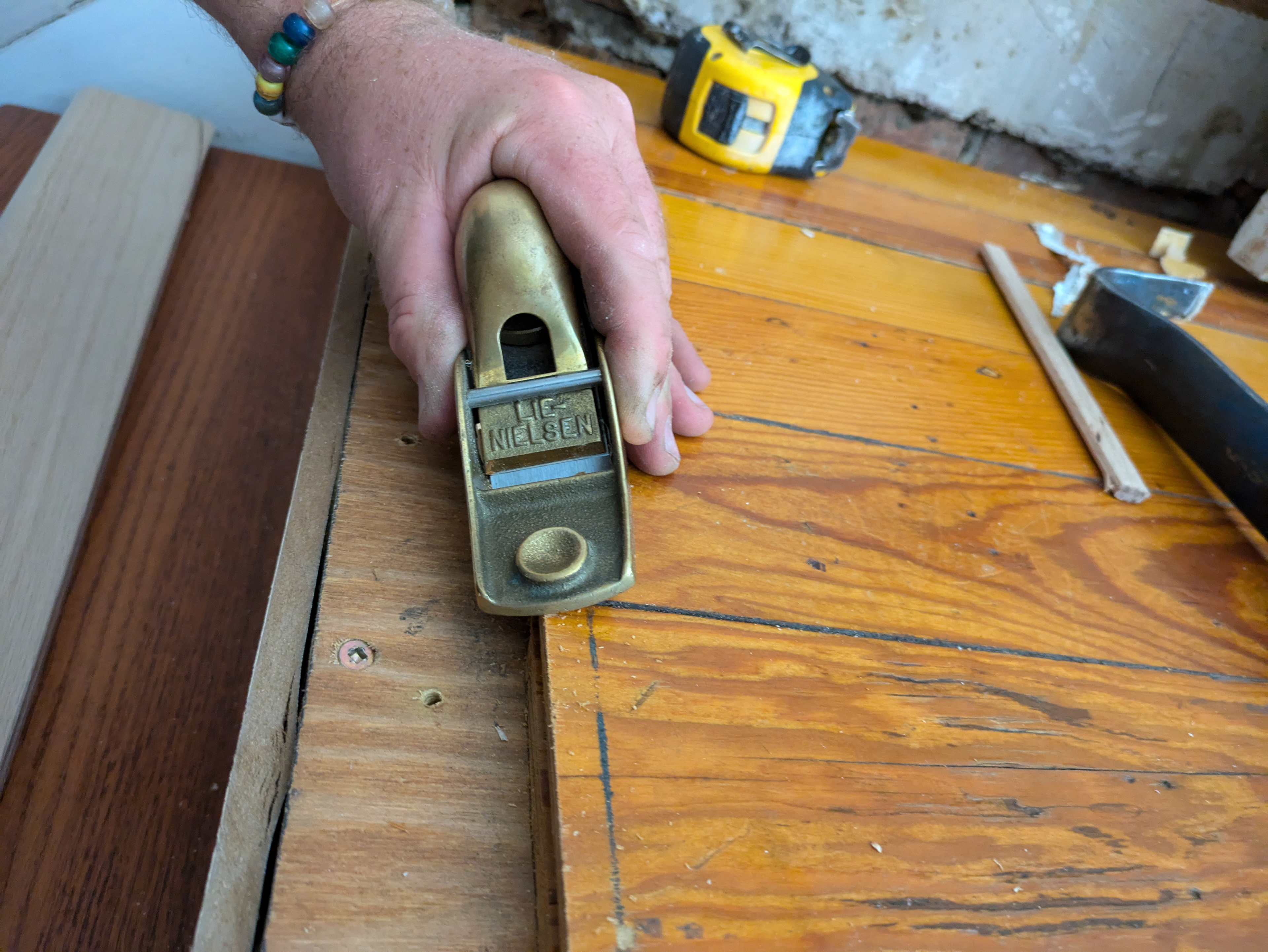
I'm slightly easing the leading edge of the flooring for a smooth transition to the new landing tread.
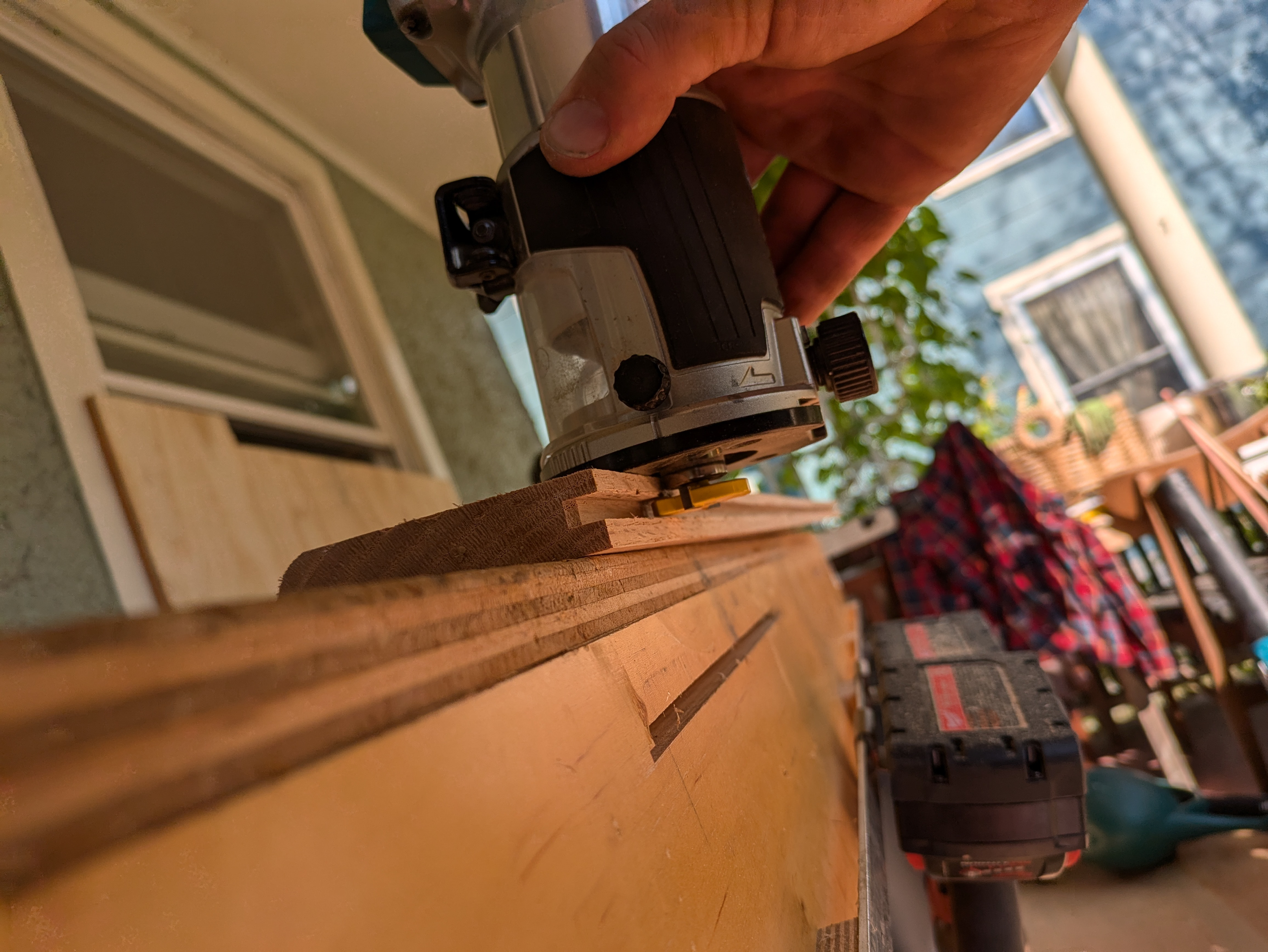
I am cutting a groove into the backside of the landing tread with a router bit. This groove will allow me to attach the landing tread to the flooring with a spline.
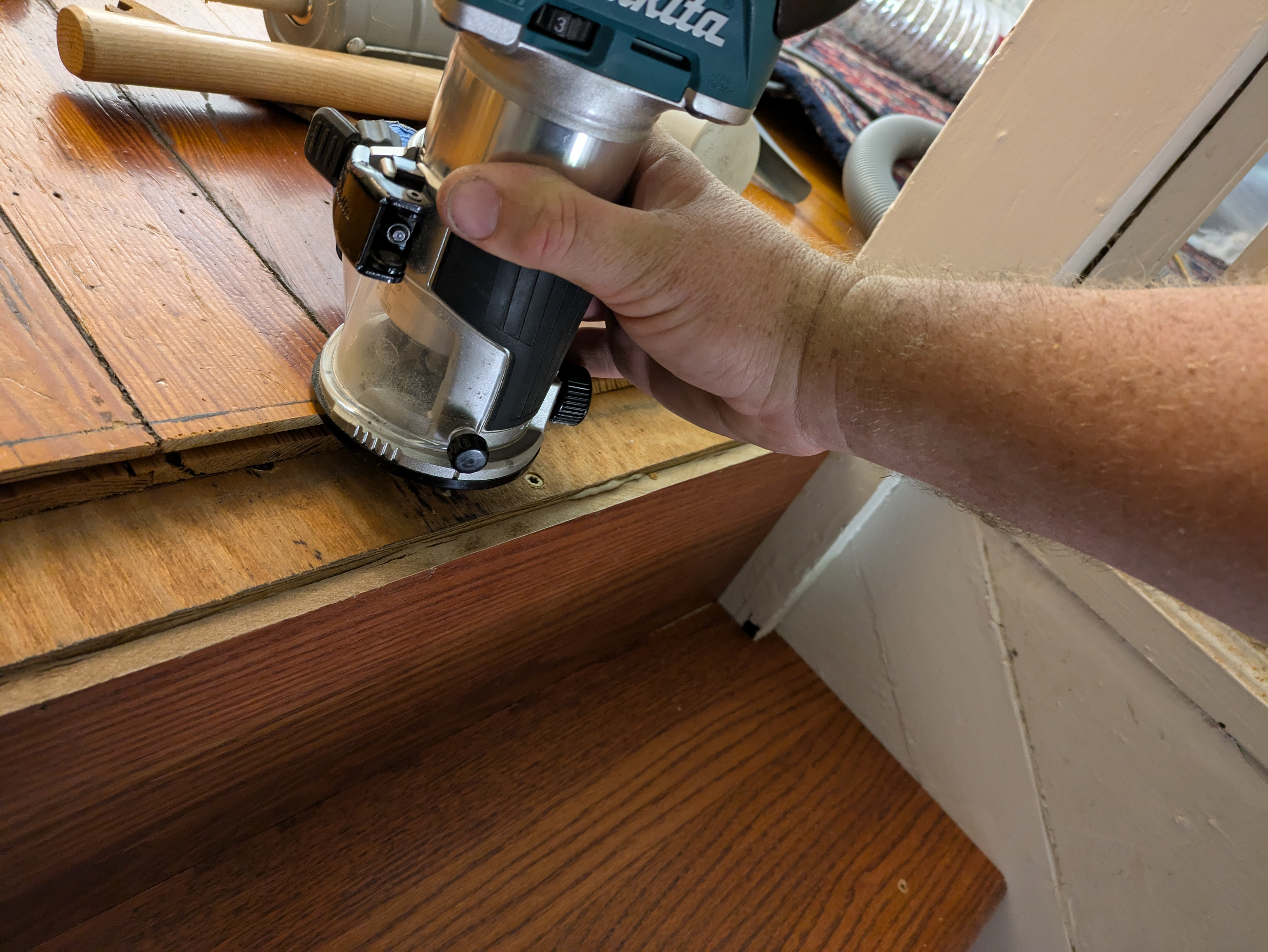
Grooving the flooring in preparation for the spline.
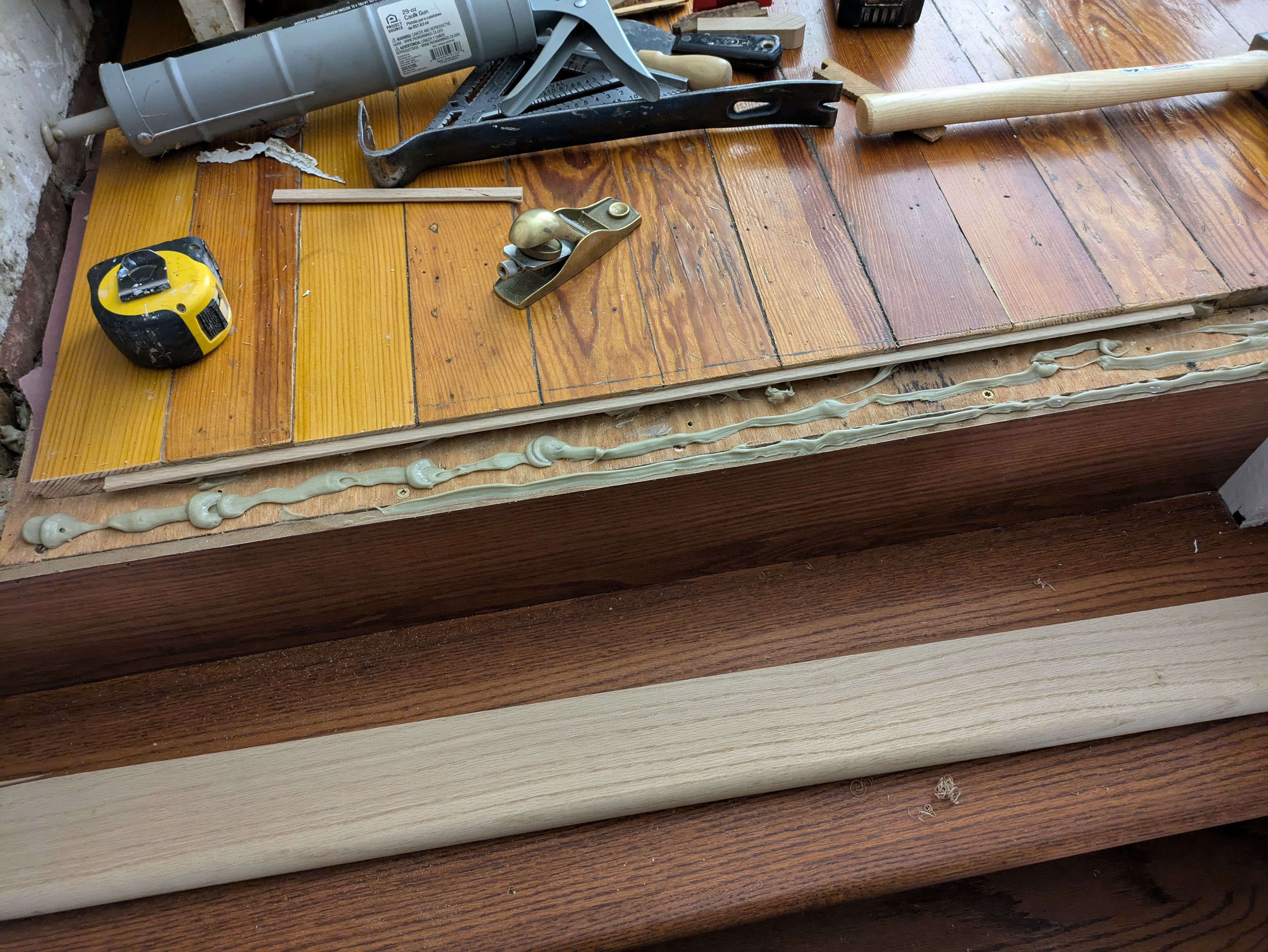
PL holds the landing tread down to the subfloor and holds the spline in place.
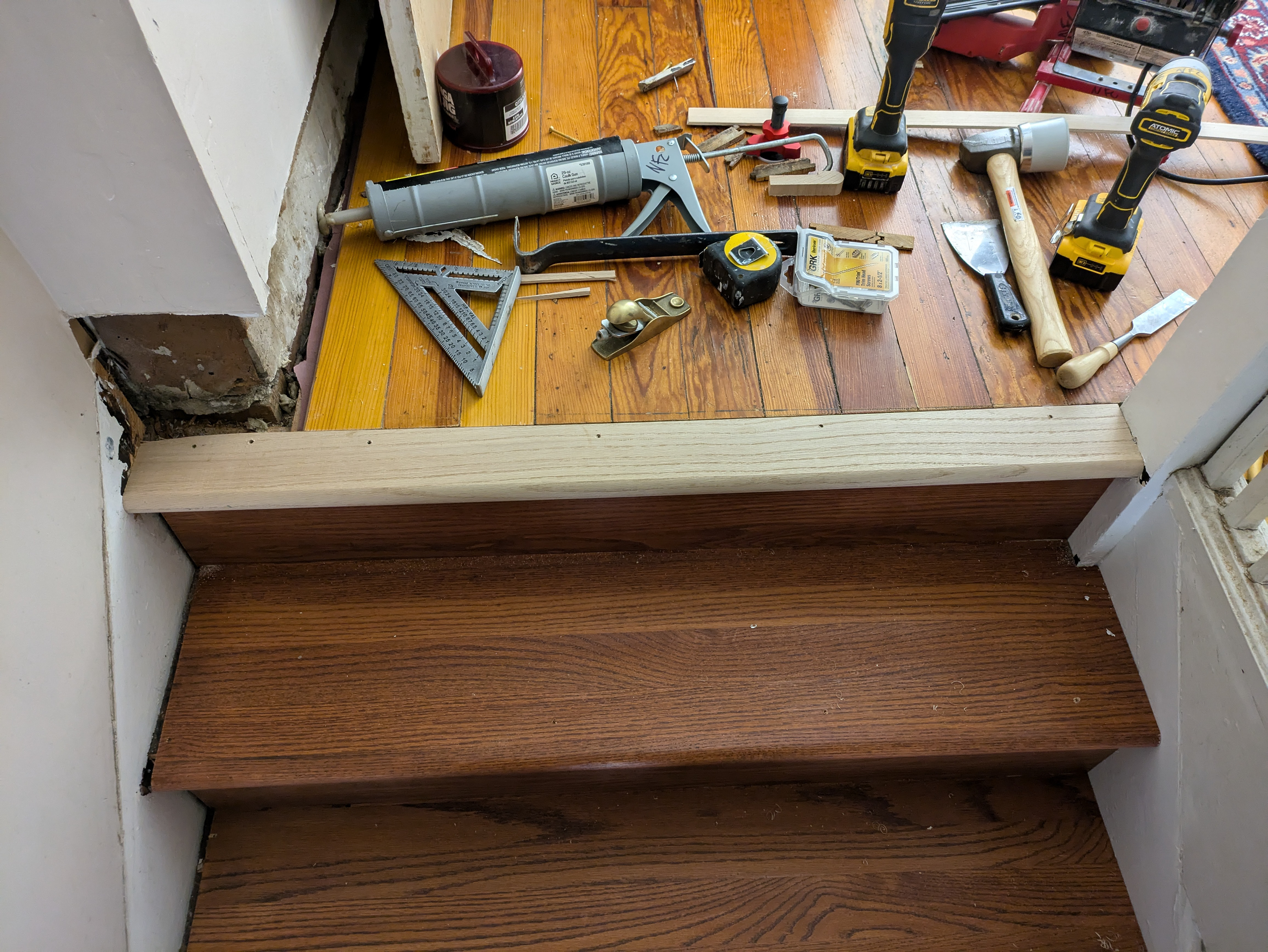
Six screws hold the landing tread in place.
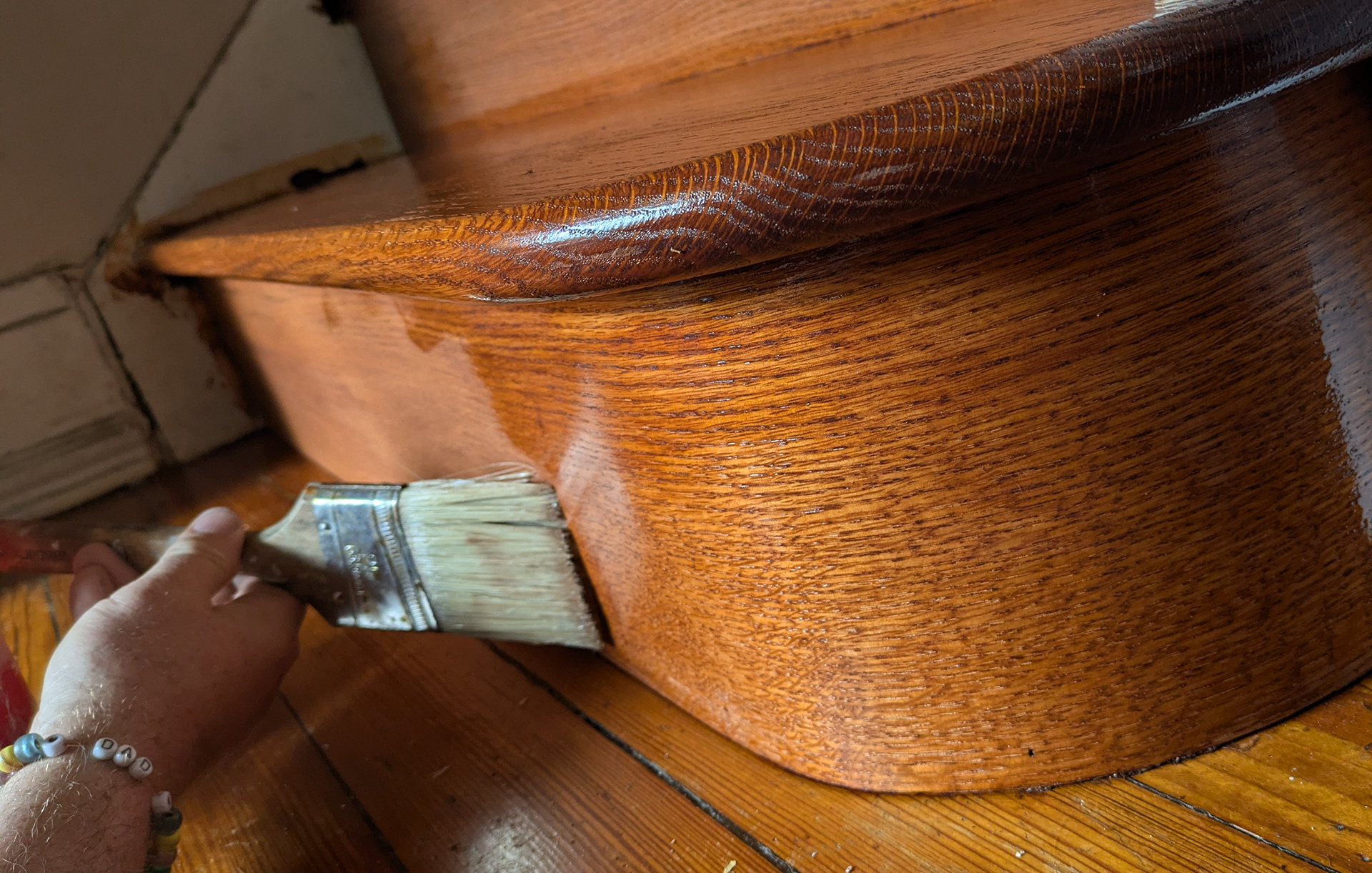
I've stained the curved riser, the curved tread and the landing tread. Now I'm going to apply 3 coats of polyurethane. Once the finish has cured over night, I'll scuff sand these components with 220 grit.
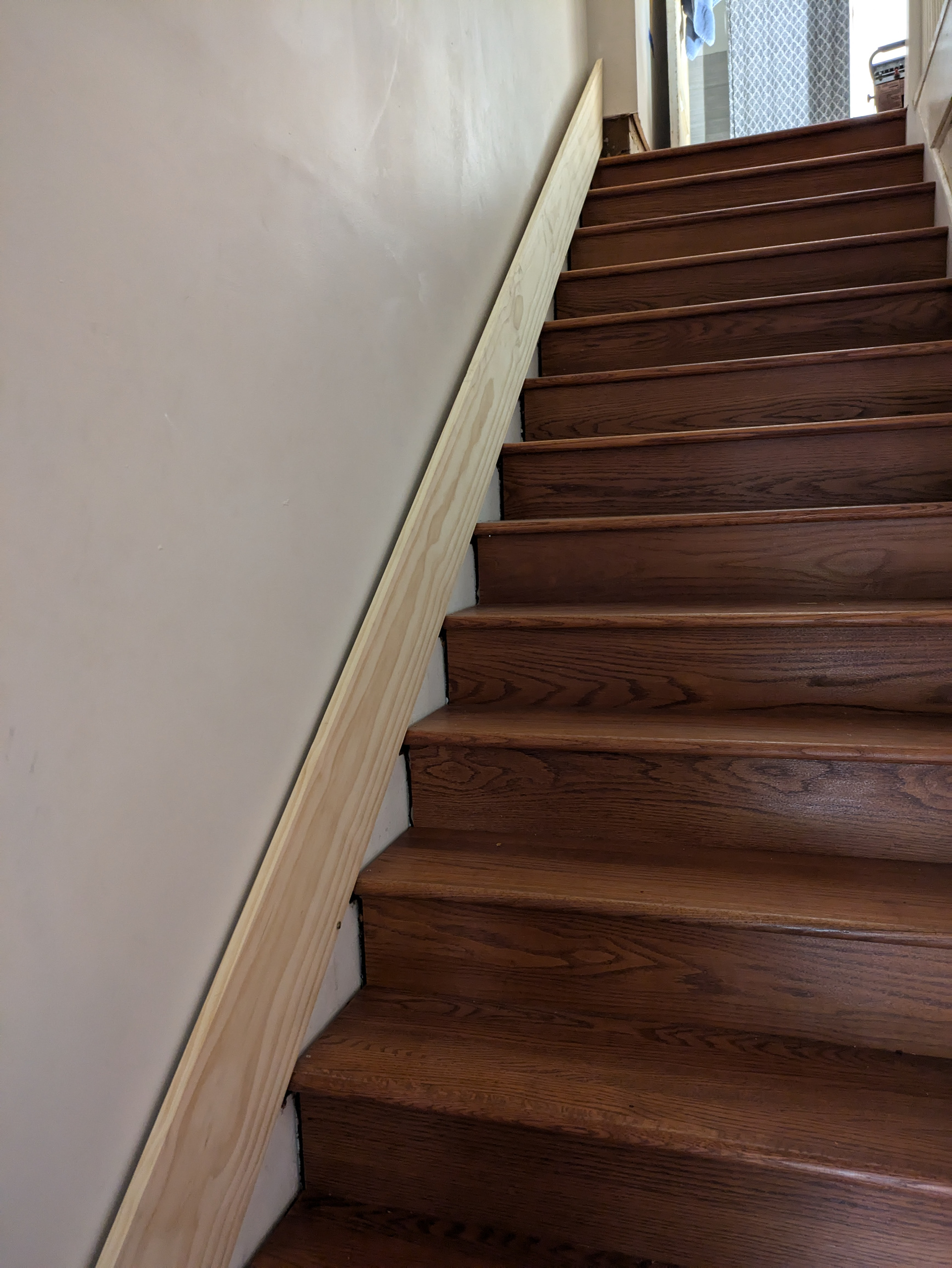
A new skirtboard will go on the wall-side stringer. Scribing a skirtboard to the treads looks better and less gappy over the years as the components of the staircase expand and contract than scribing the treads and risers to a skirtboard.
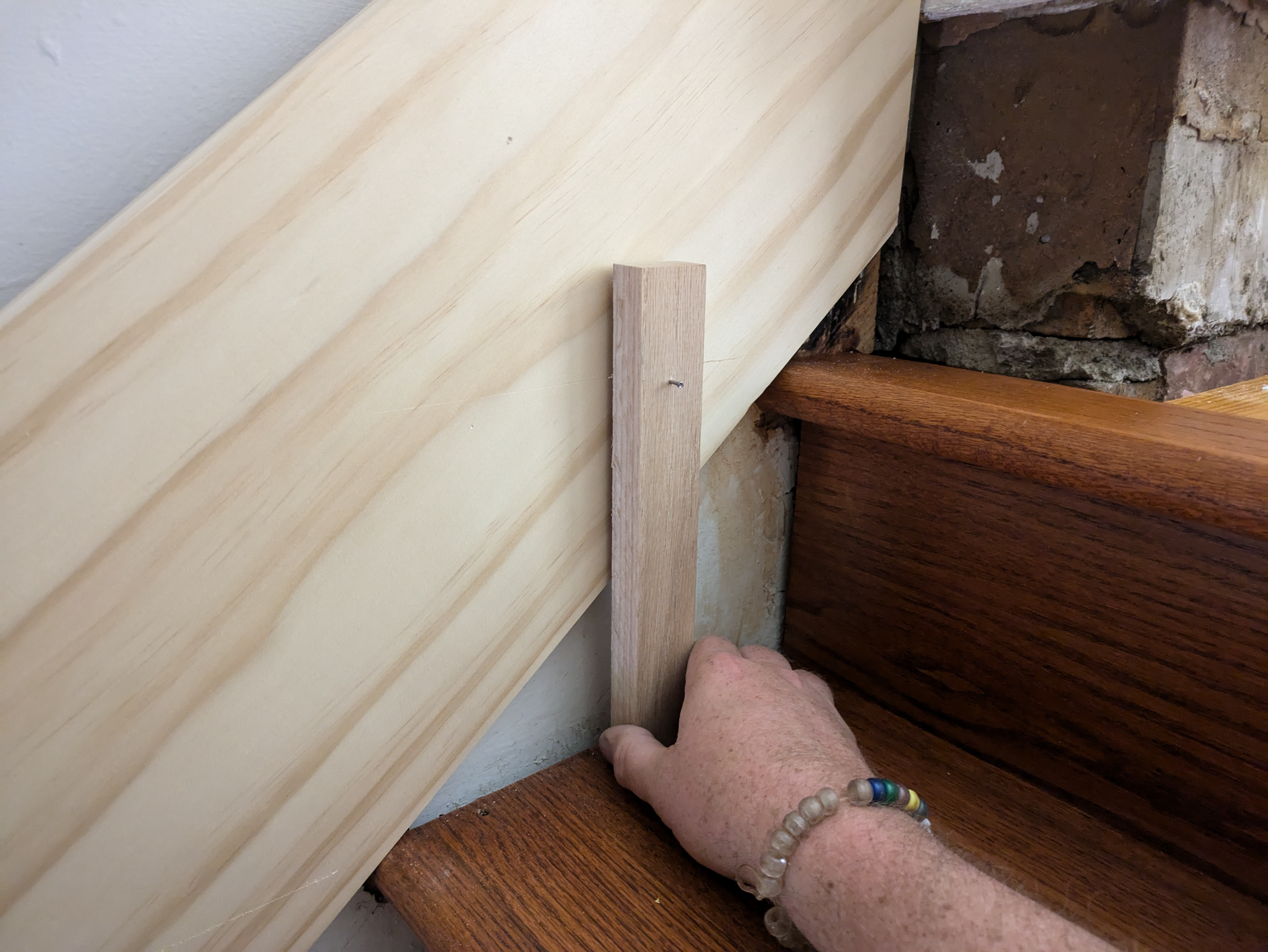
First I scribe the treads. I'm using a sharpened nail and a piece of scrap wood. Next I'll level cut the bottom of the skirtboard then scribe the risers.
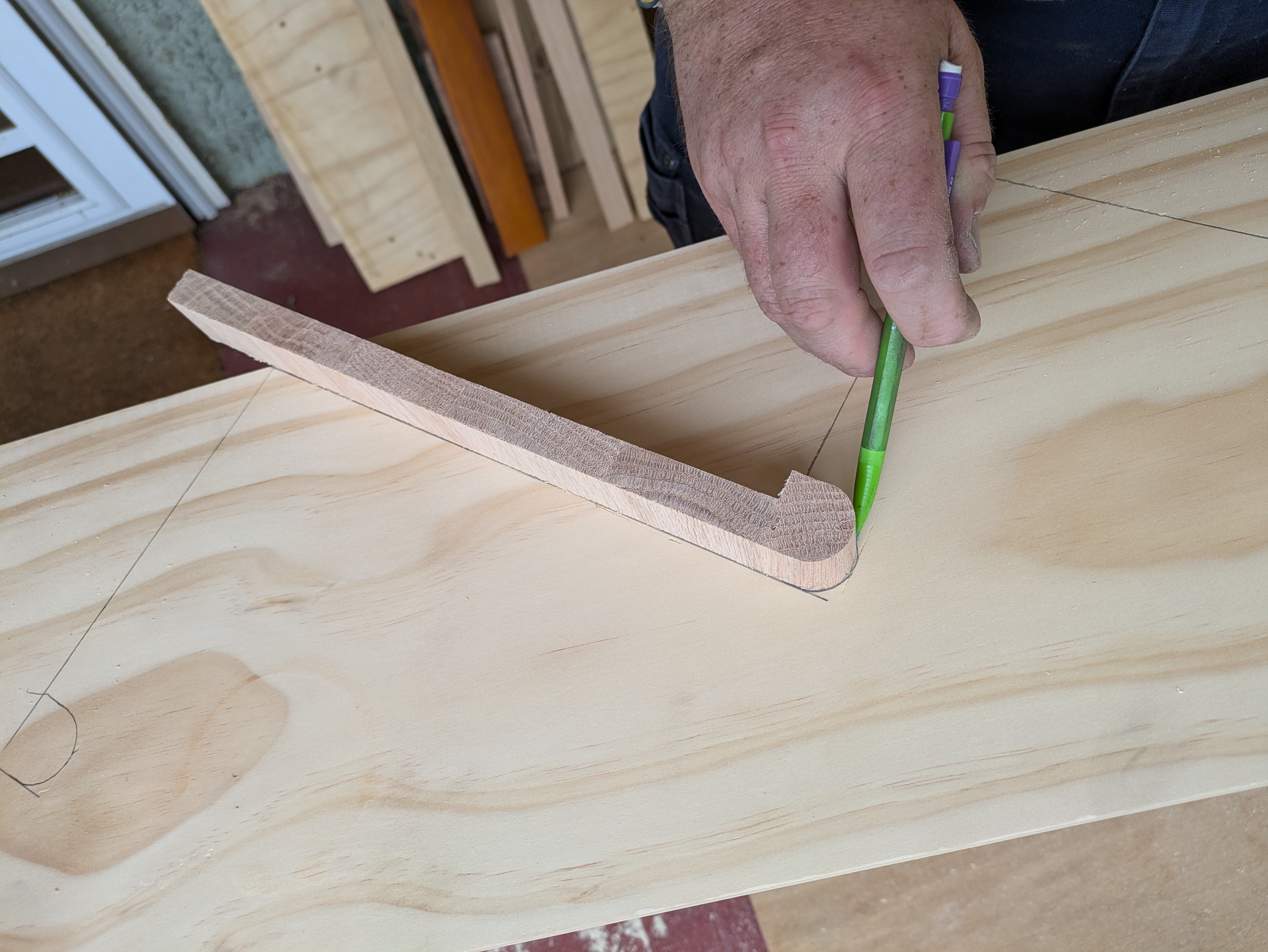
A scrap cut off of tread nosing is usefull for tracing the nosing onto the skirtboard. Next I'll use a circular saw, jigsaw and block plane to cut to the scribed lines.
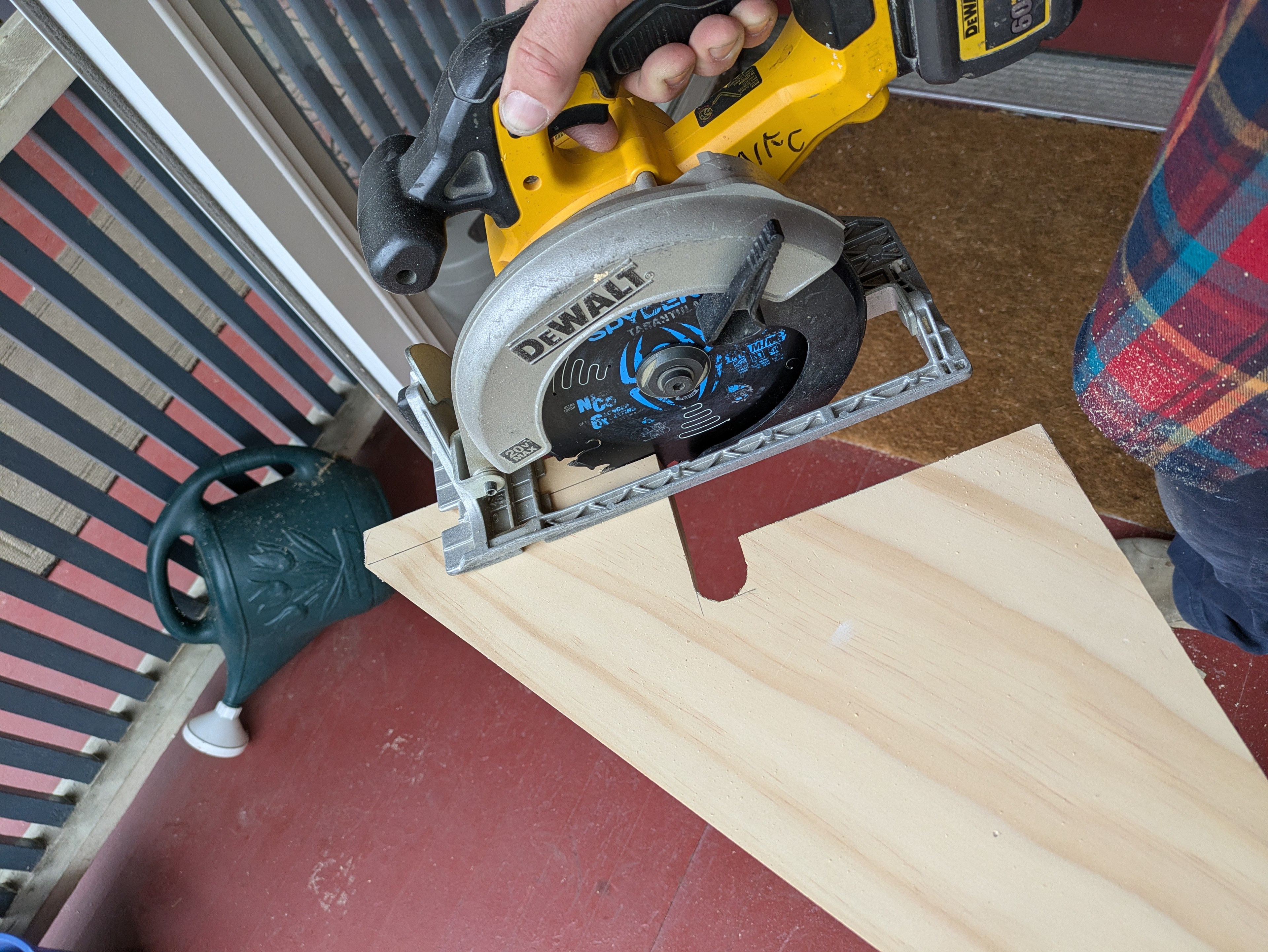
The circular saw makes the plumb cut on the skirtboard at the top of the stairs.
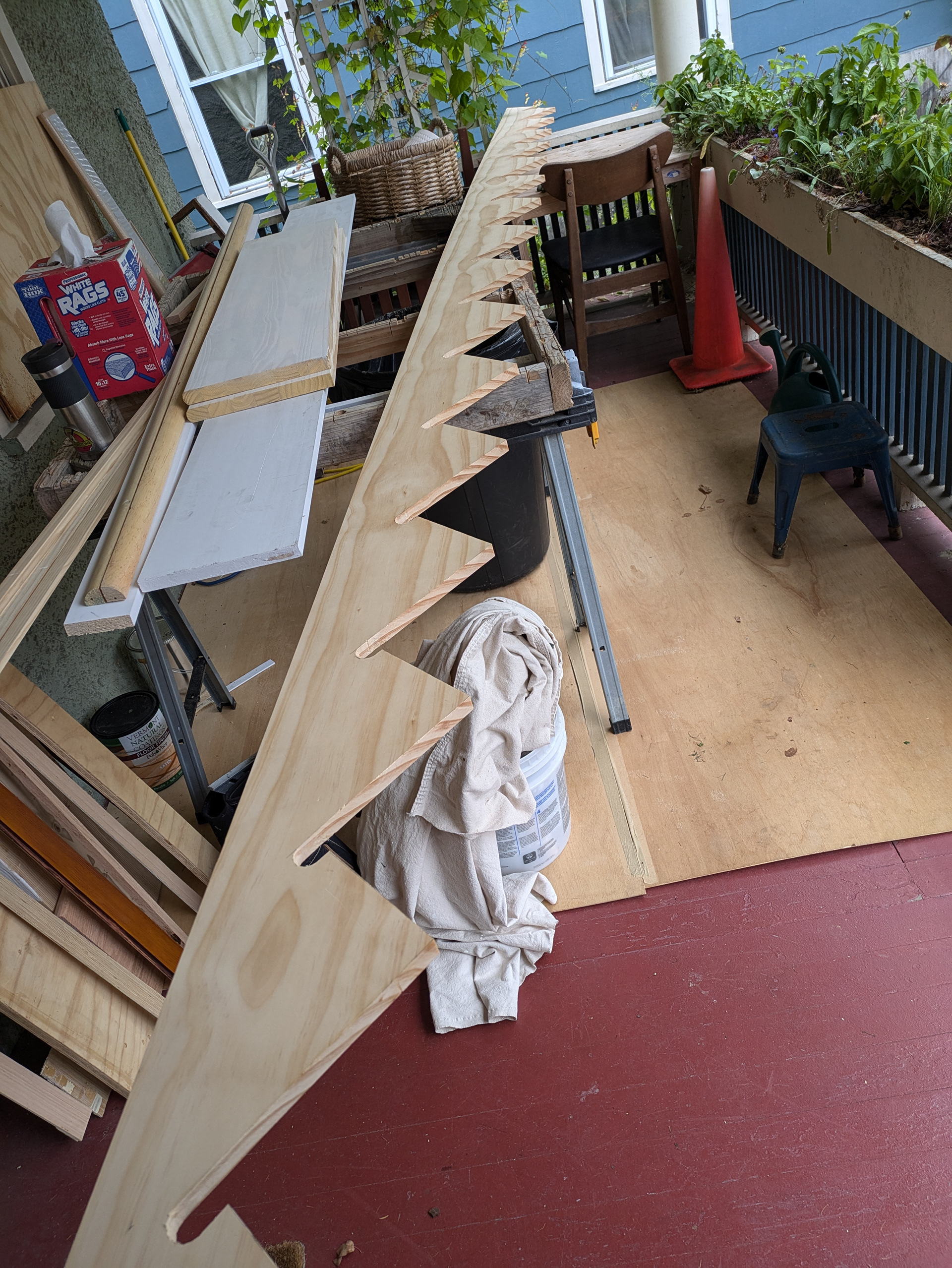
The scribed skirtboard will need to be dry fit and potentially whittled a bit to achieve a tight fit.
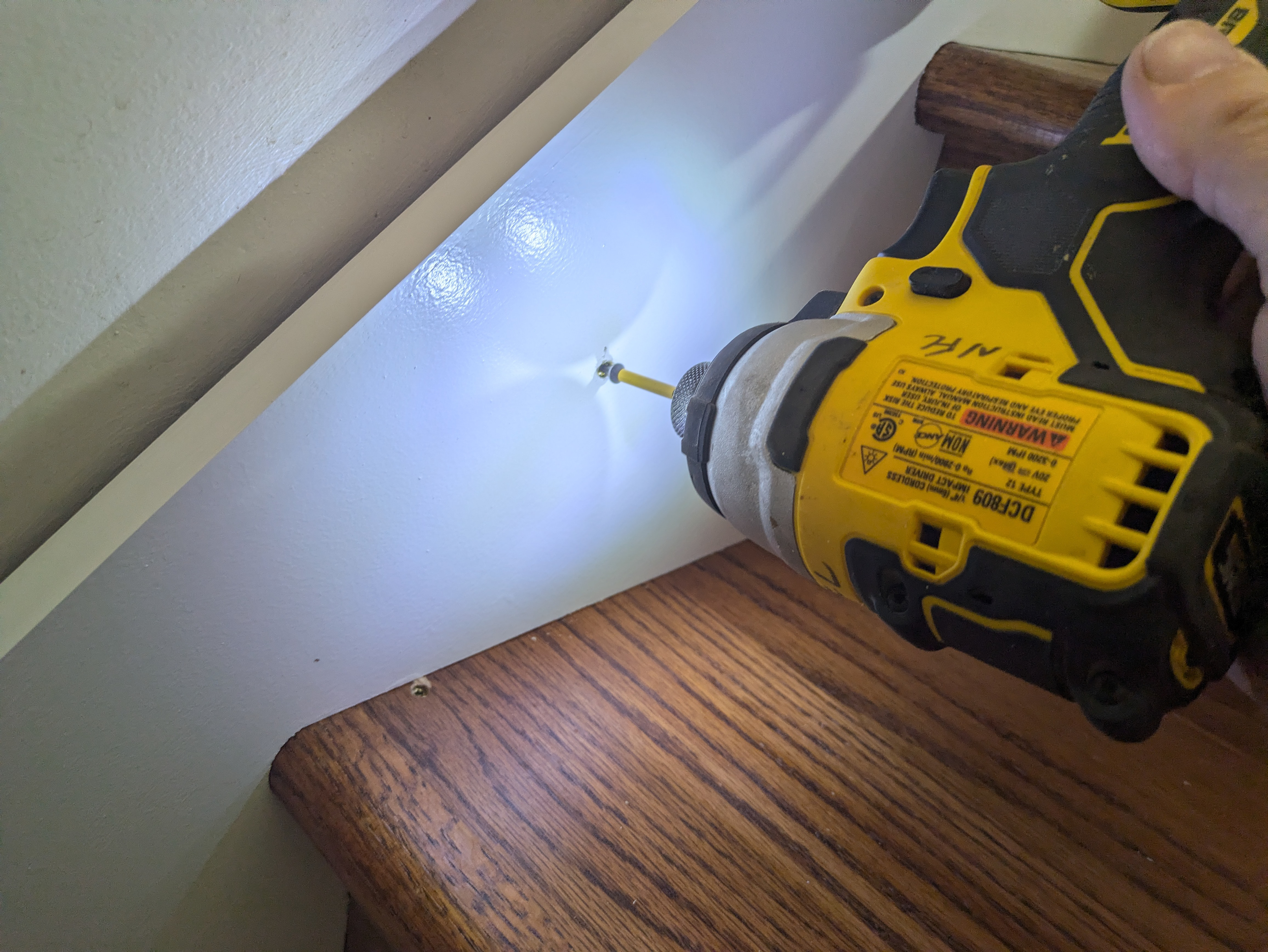
I'm fastening the skirtboard to the old stringer with 2 screws at each tread. Next I'll tie the baseboard into the skirtboard and add basecap molding to the skirtboard.
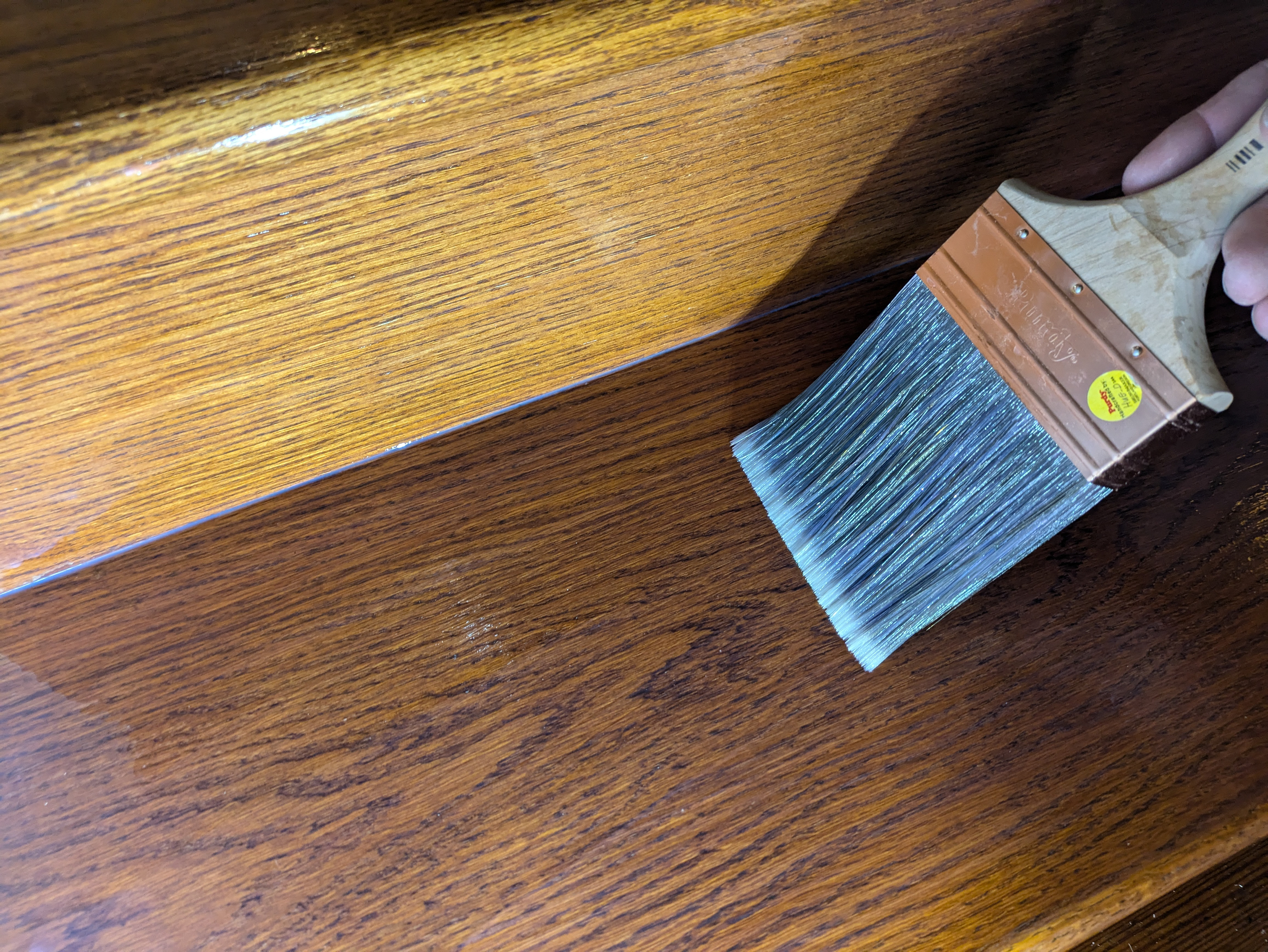
I filled the fastener holes in the treads with wood filler and stained them with the same stain I used on the raw oak. A fourth and final coat of polyurethane will protect these stairs for years to come. I'm using polywhey floor polyurethane in satin.
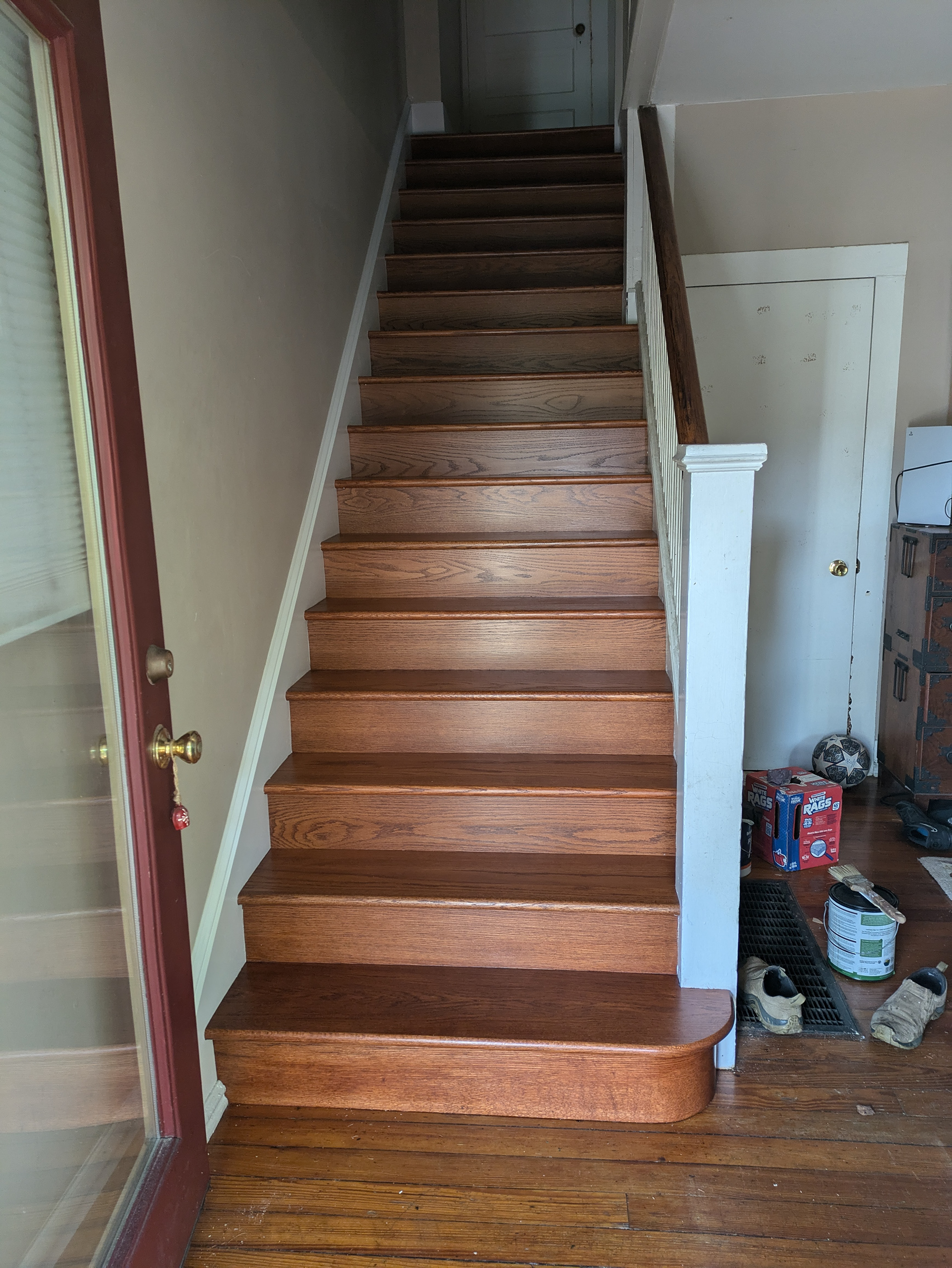
The project is done. These new stairs look good and are nice and stiff to walk on.
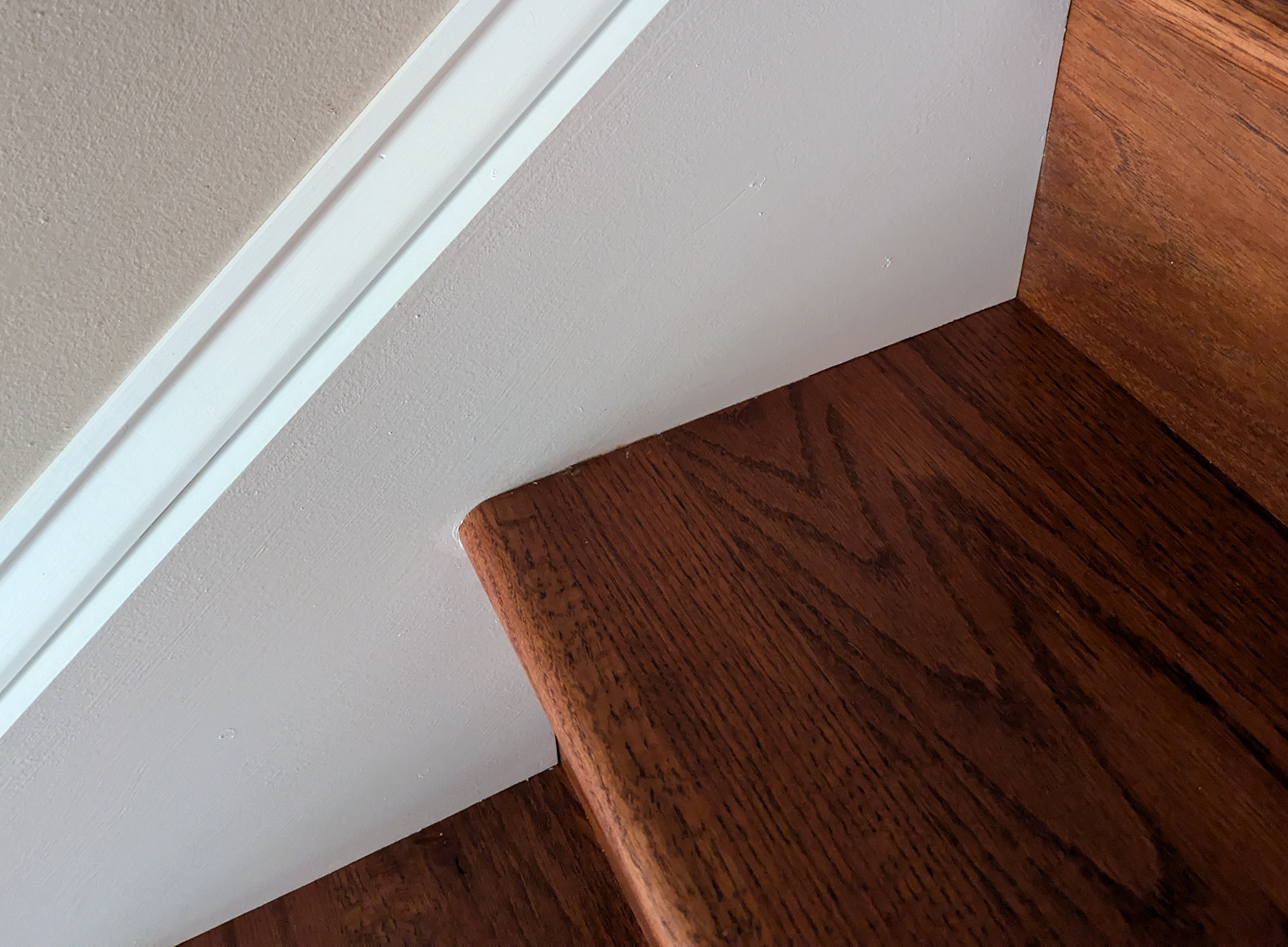
The skirtboard and basecap came out well.
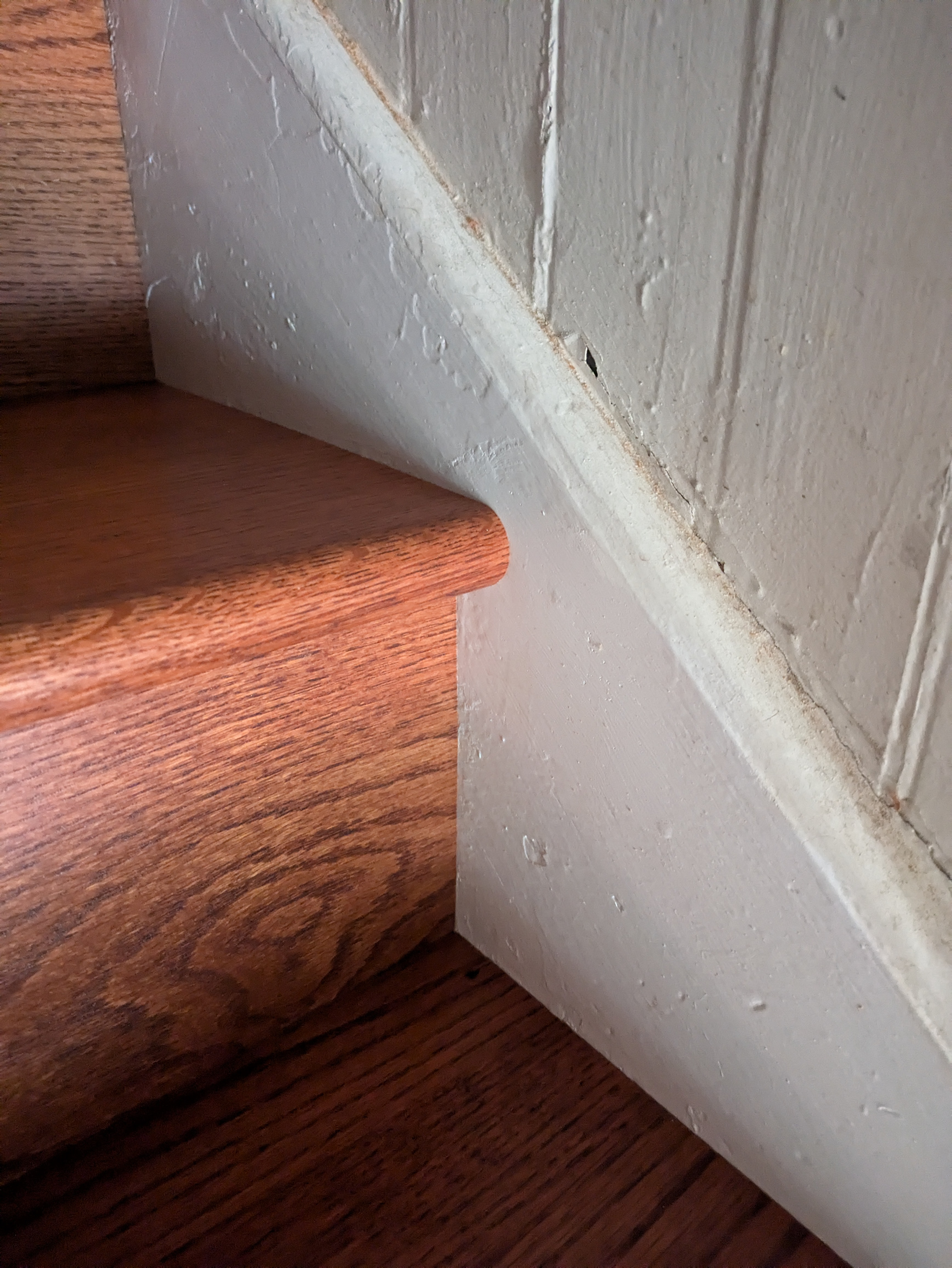
The new treads and risers fit tightly against the original stringer on the balustrade side.
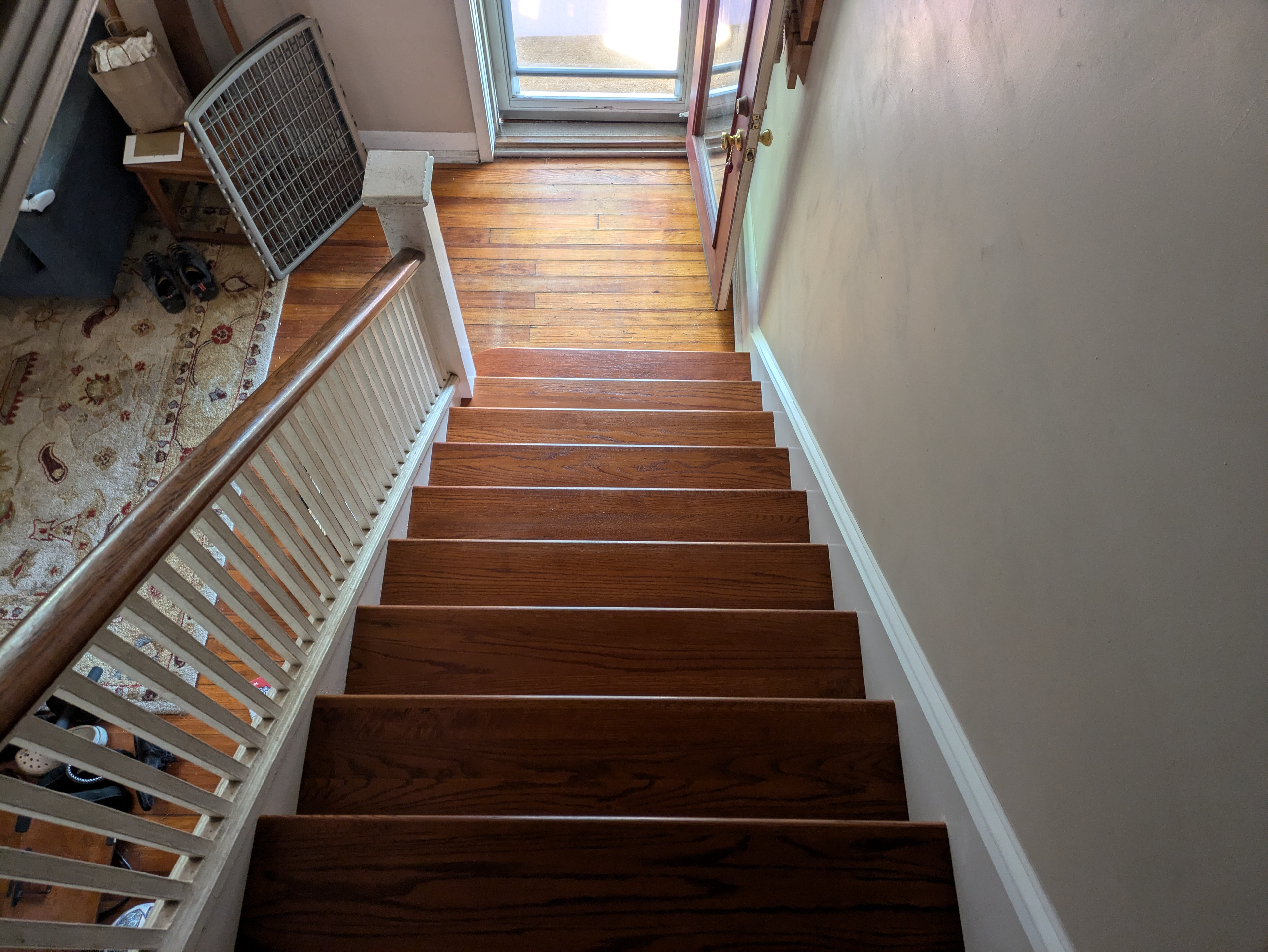
By repairing the original stairs and using them as sub treads and risers for the new oak treads and risers I was able to leave the old paint undisturbed and limit the scope of the project by keeping the balustrade in tact. I also didn't have to subsequently damage and repair the plaster walls.
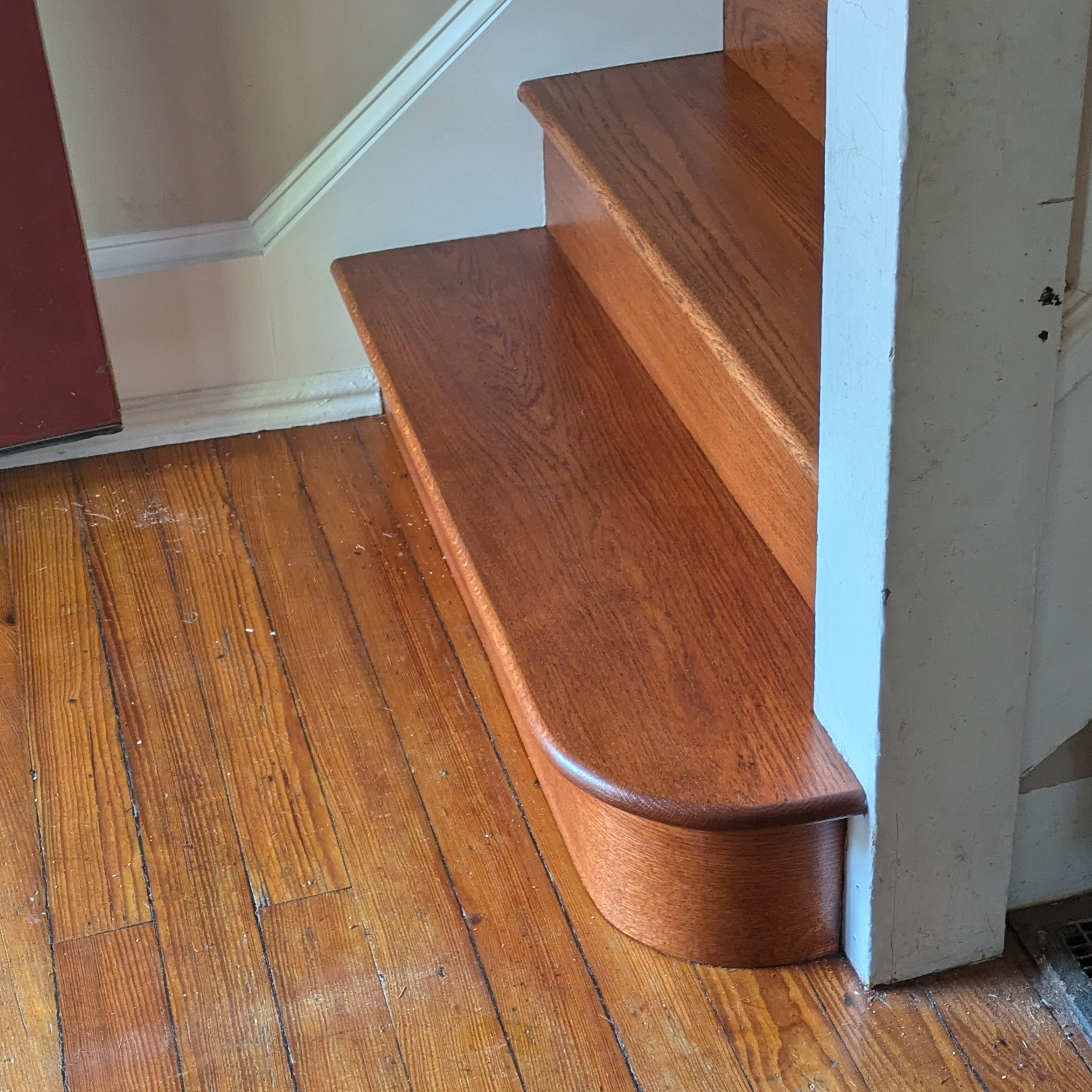
This was a fun project!