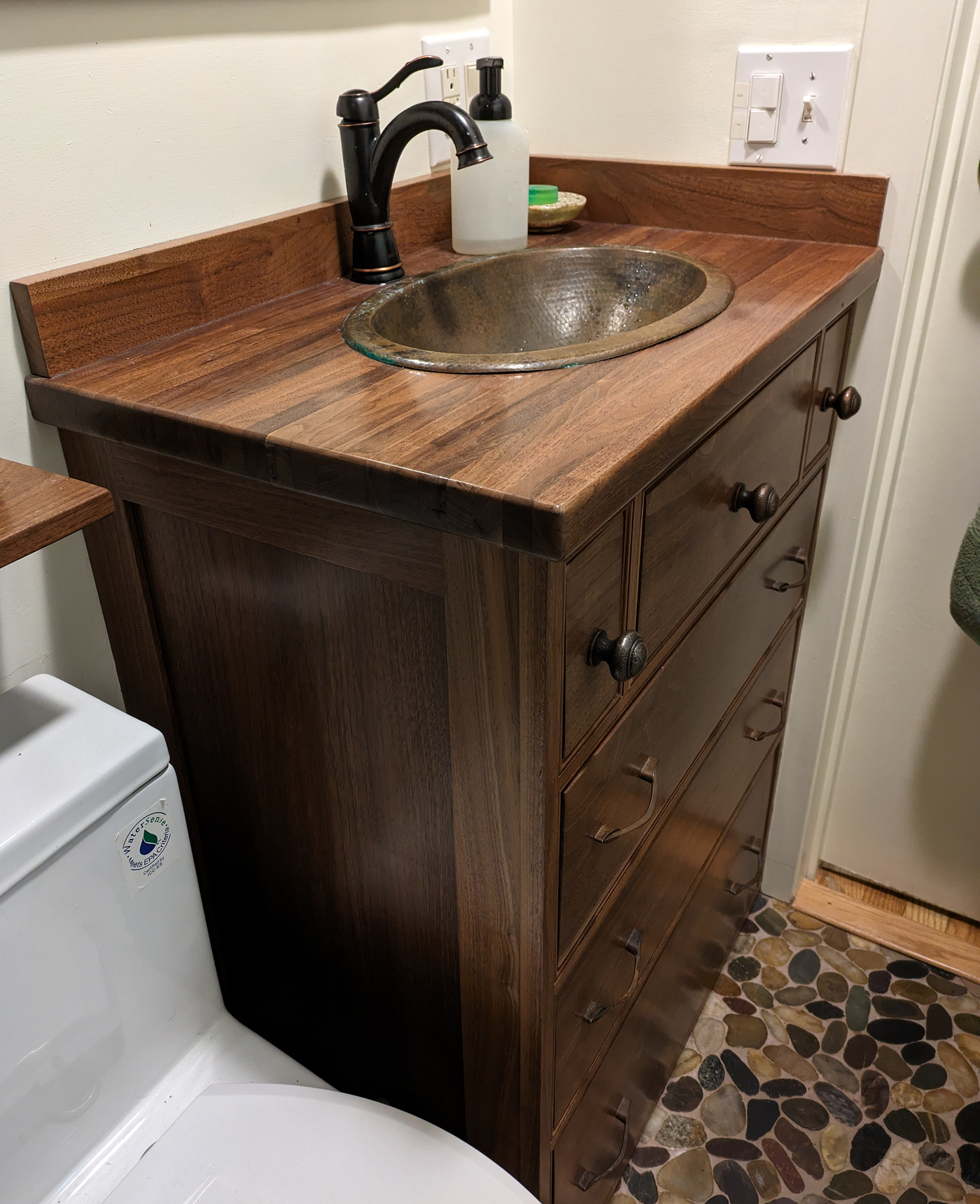
I recently built this custom vanity. I designed it to match the existing walnut built in bathroom cabinets that I had built a few years ago.
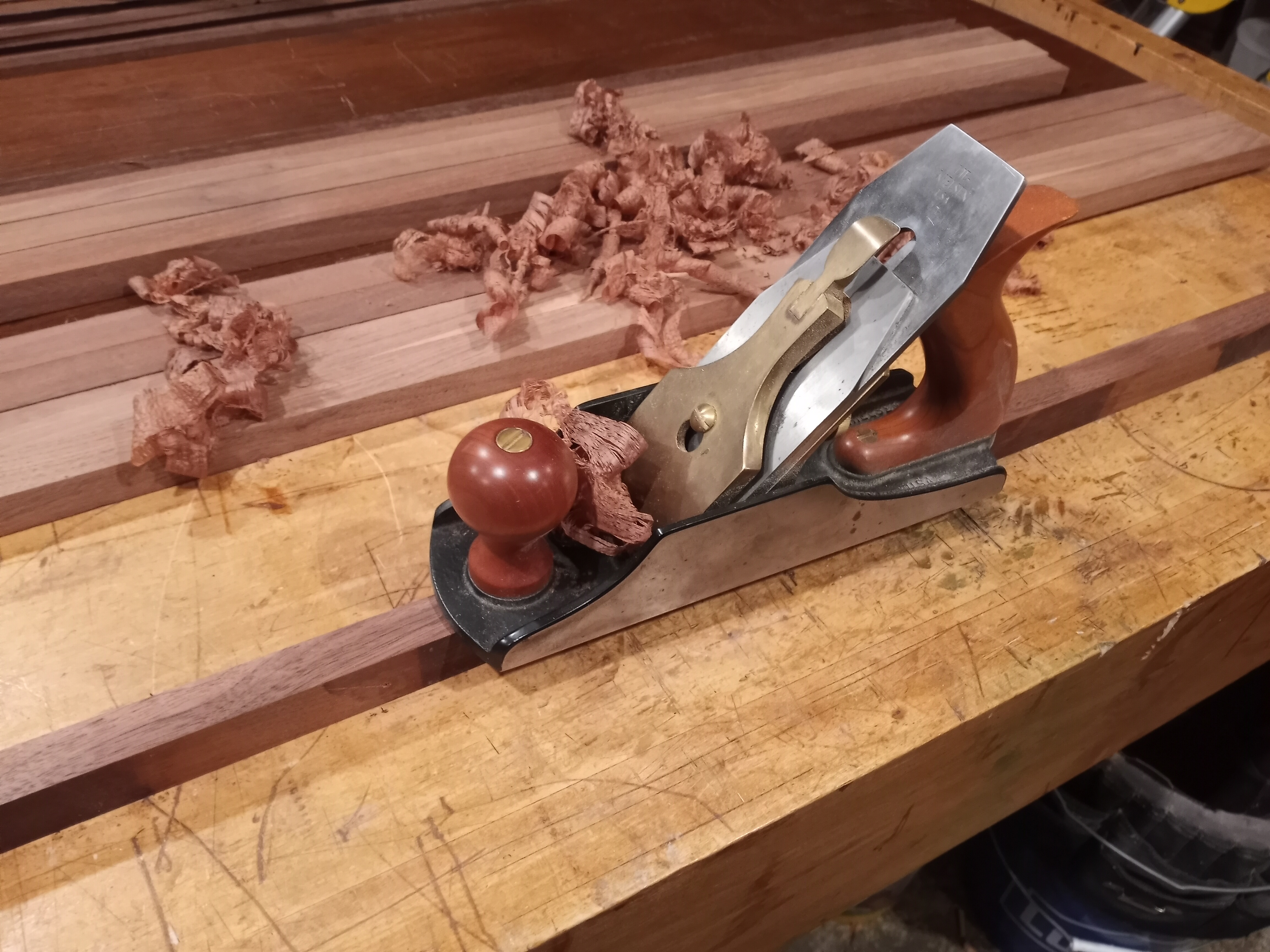
I began by cutting some walnut down to 1" wide by 3/4" thick strips for the face frame. A quick pass with a hand plane cleans up the table saw marks.
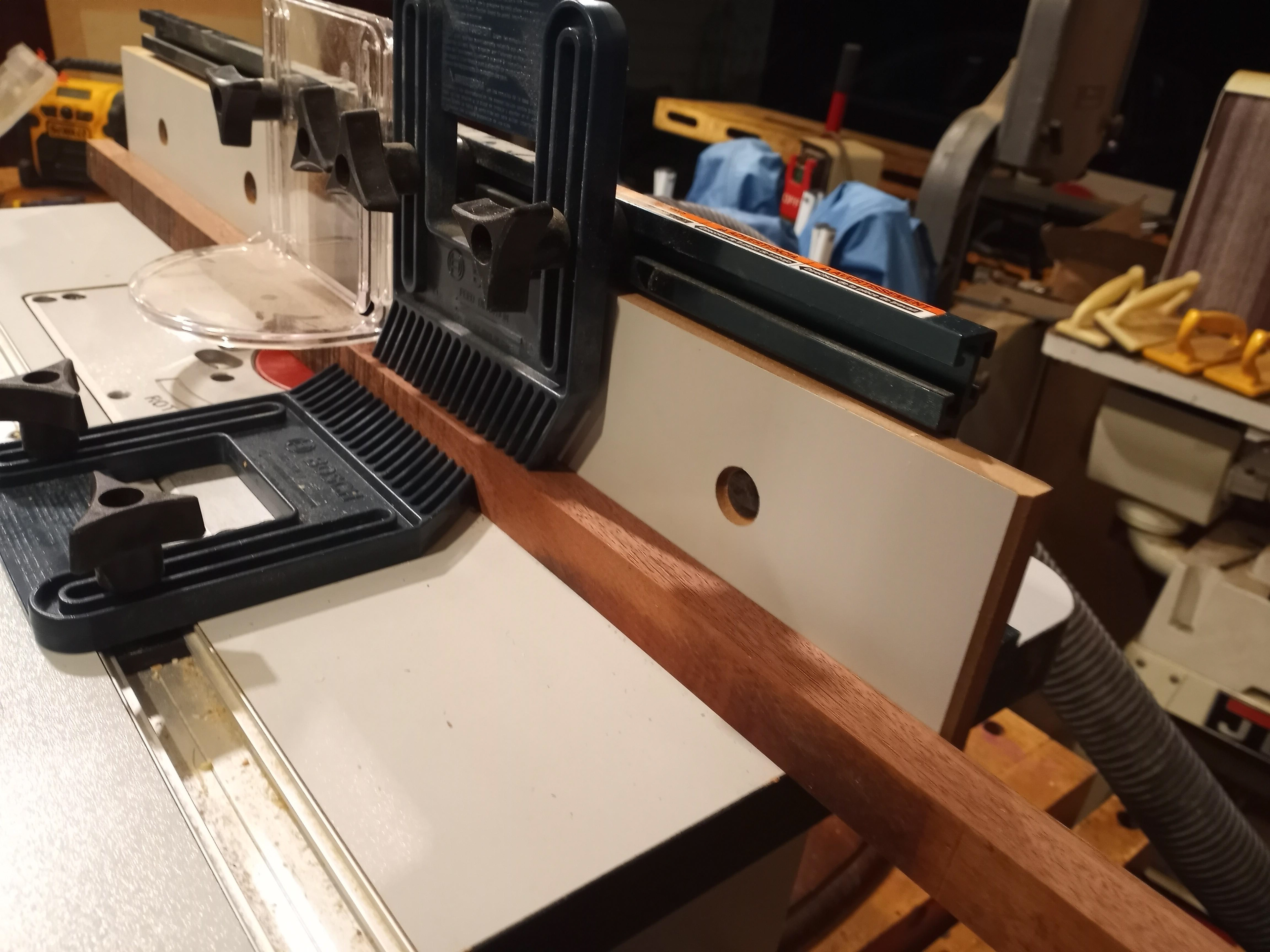
The existing cabinets have beaded face frames. So I'll use my router table to add a bead detail to the new cabinet's face frames too. The feather boards bold the walnut down to the table and against the fence for accurate routing.
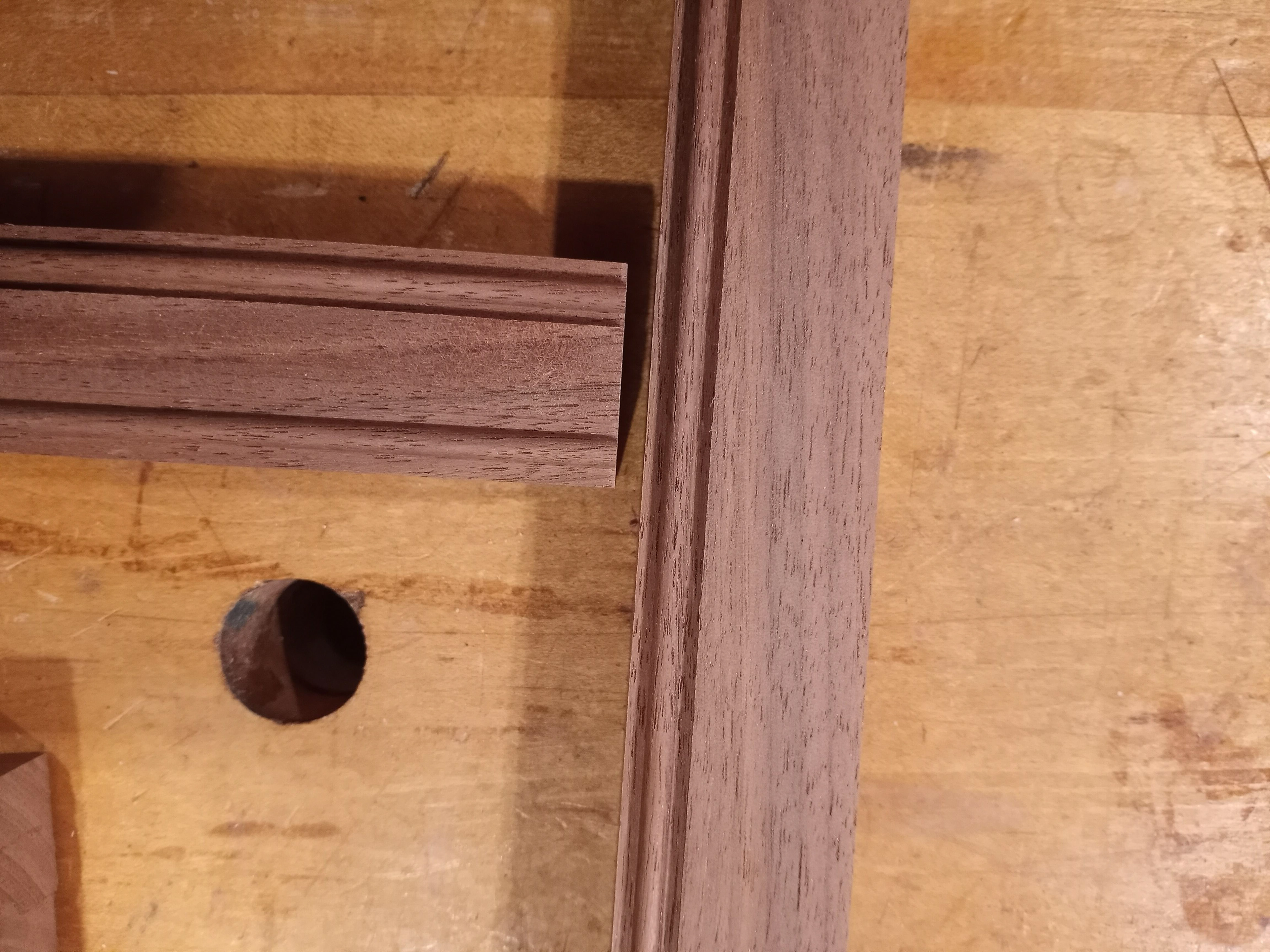
The rails are the horizontal part of the face frame. The rails between the drawers have a bead detail on both sides of their face. I'll cut jack miters, also called haunched miters so the bead travels continuously around the drawer openings.
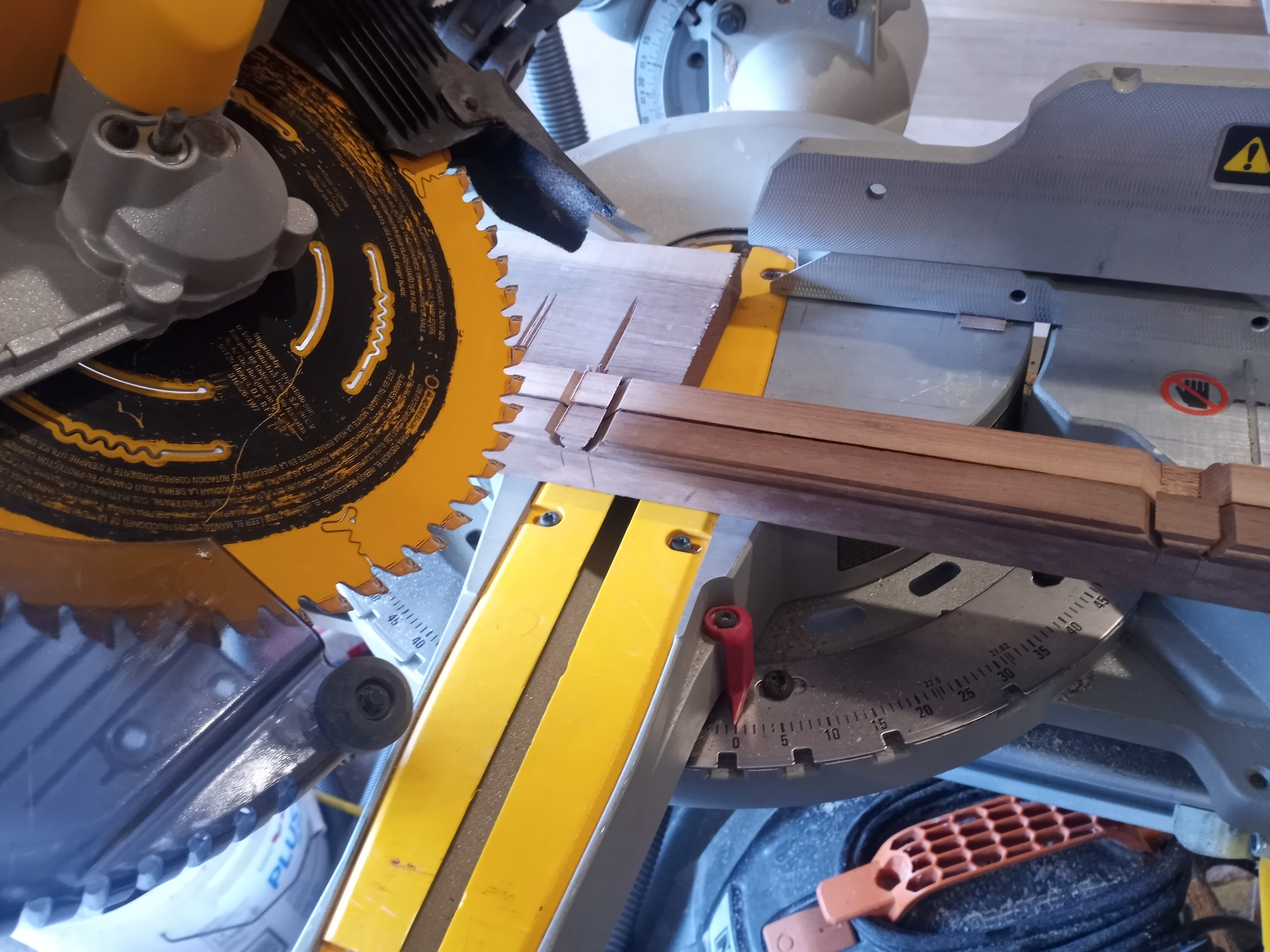
After a little bit of set up, I adjusted the compound miter saw to cut the haunches into the stiles. A spacer block keeps the stiles away from the fence so that the apex of the saw blade will cut through them completely at the set depth. I'm mitering both of the outer stiles at the same time.
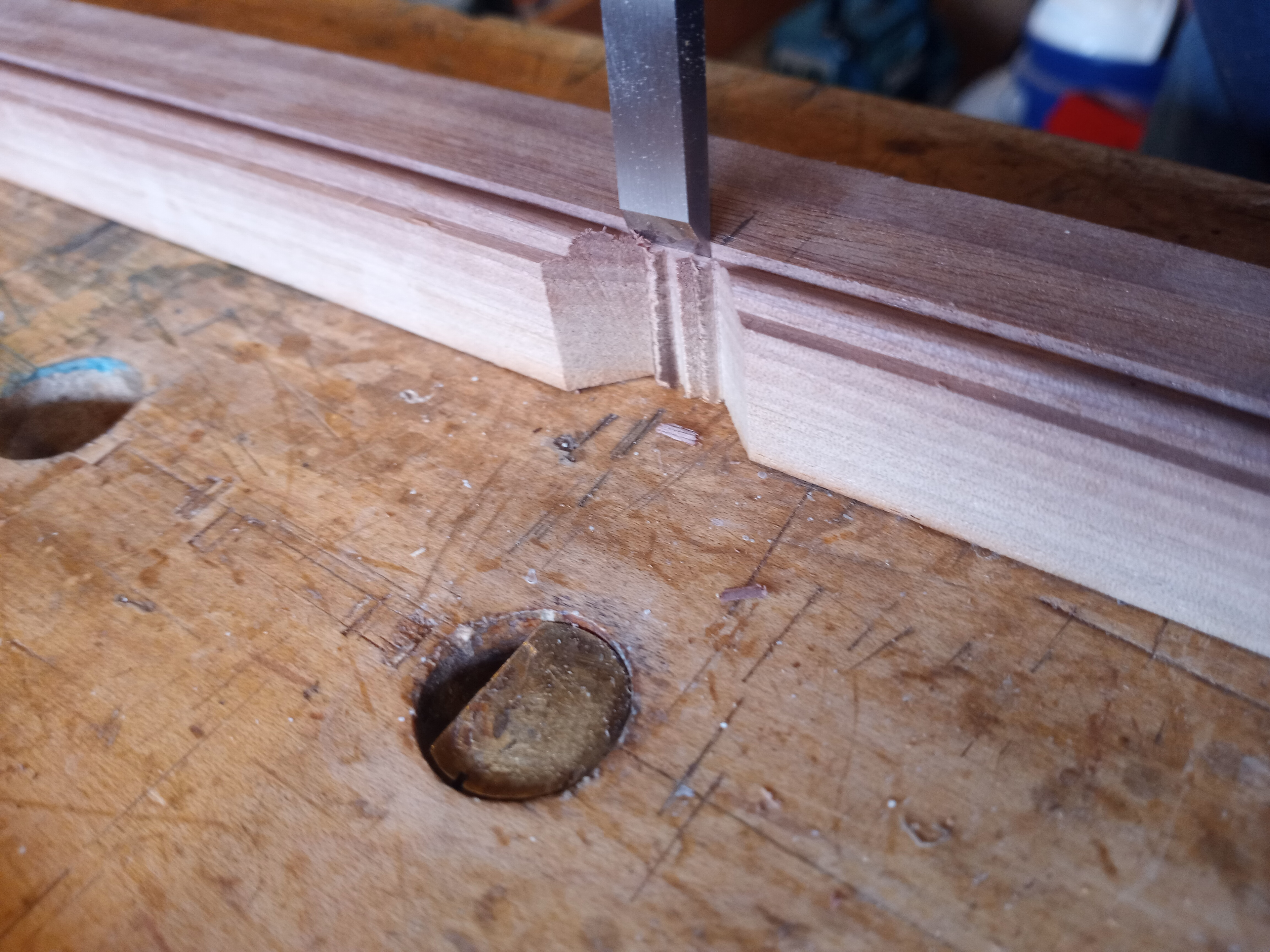
I'm cleaning out the remaining waste with a sharp chisel.
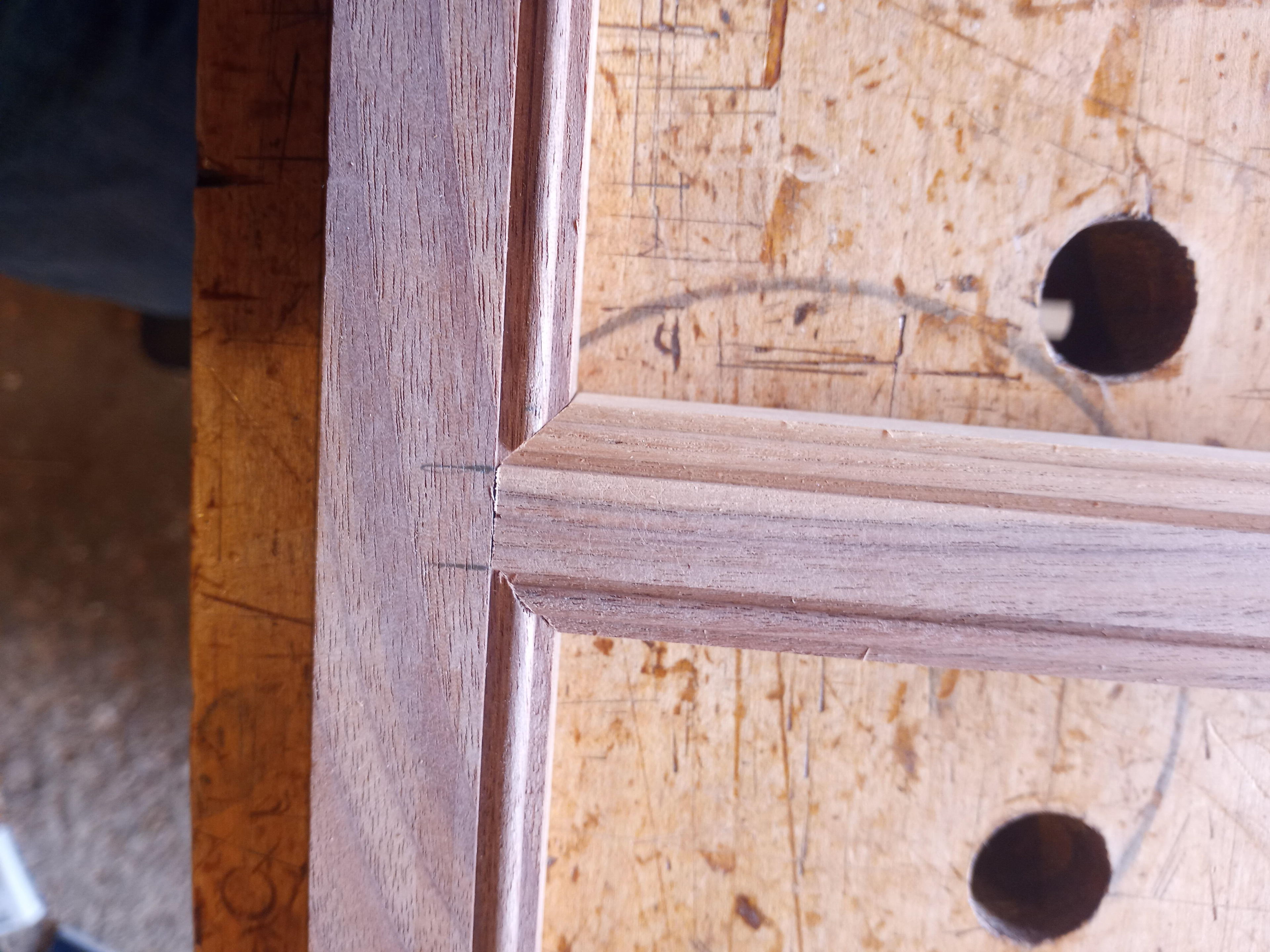
I cut the jack miter into the rails one at a time with the miter saw.
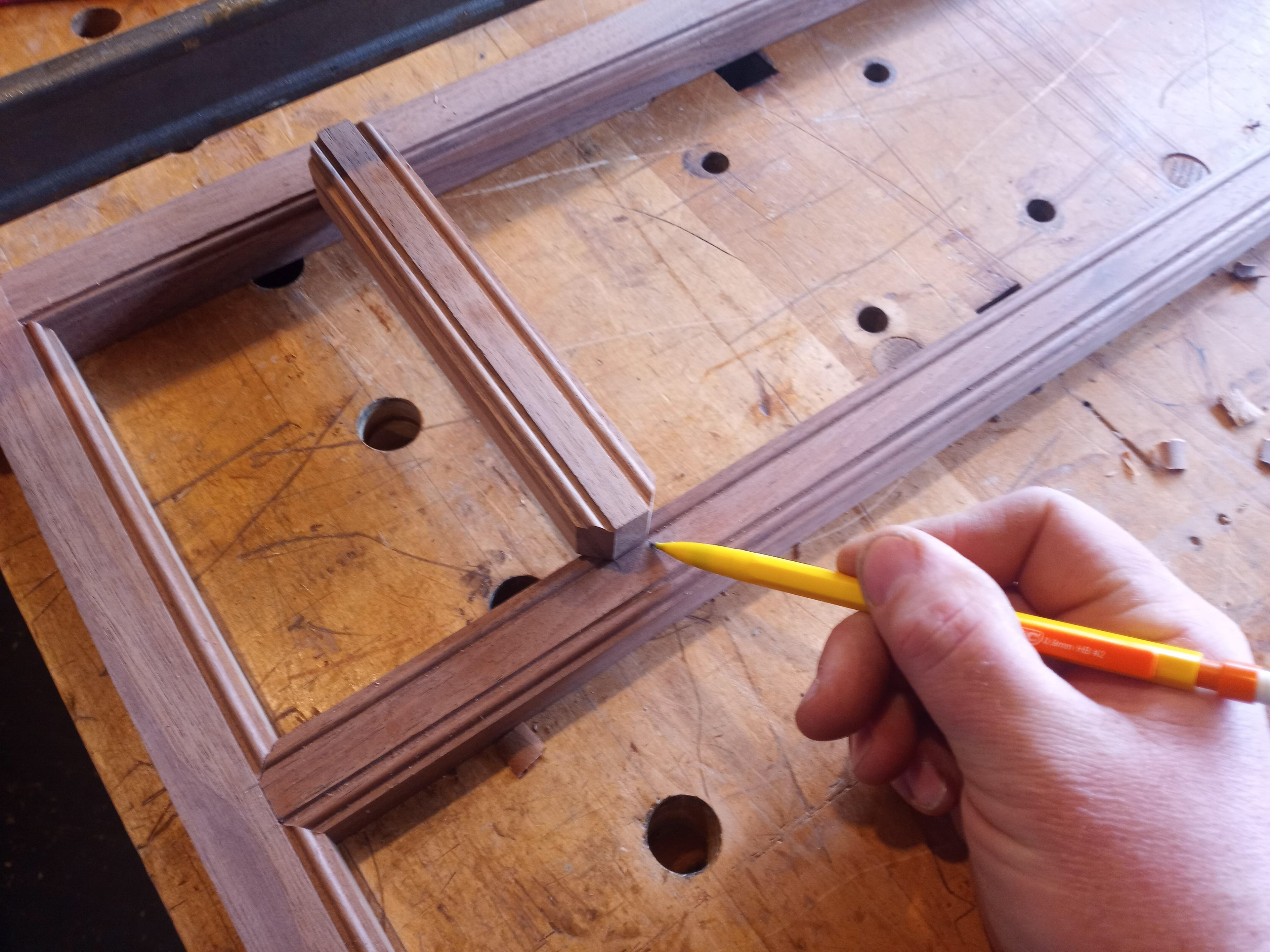
I've temporarily clamped together the outer stiles and the rails. Now I'm laying out the jack miter cuts in the rails to accommodate the small stiles that border the tiny drawers.
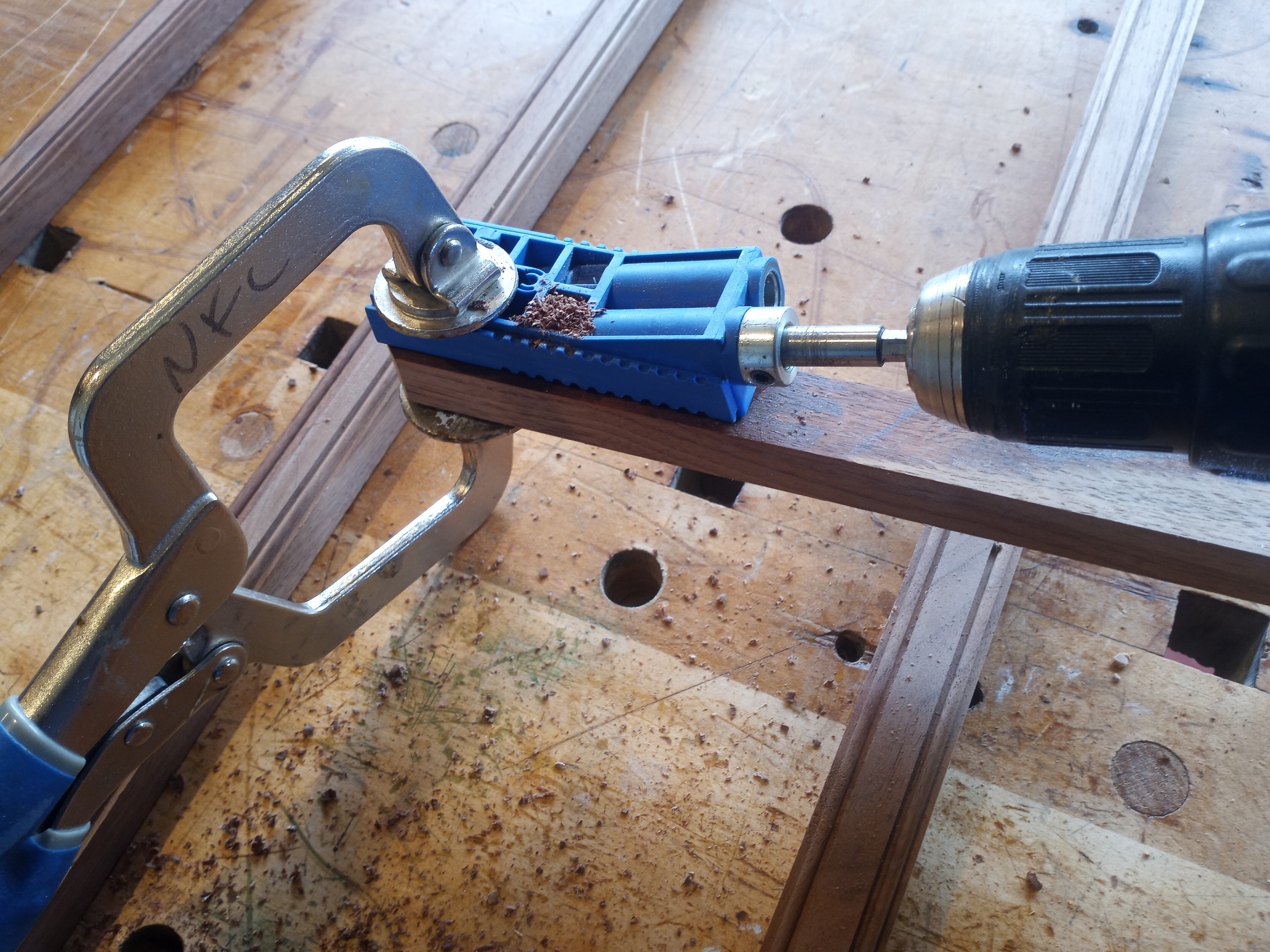
I'm going to assemble the face frame with pocket screws (toenailed, washer-head screws). Each rail and the two small stiles get pre drilled with the pocket hole jig.
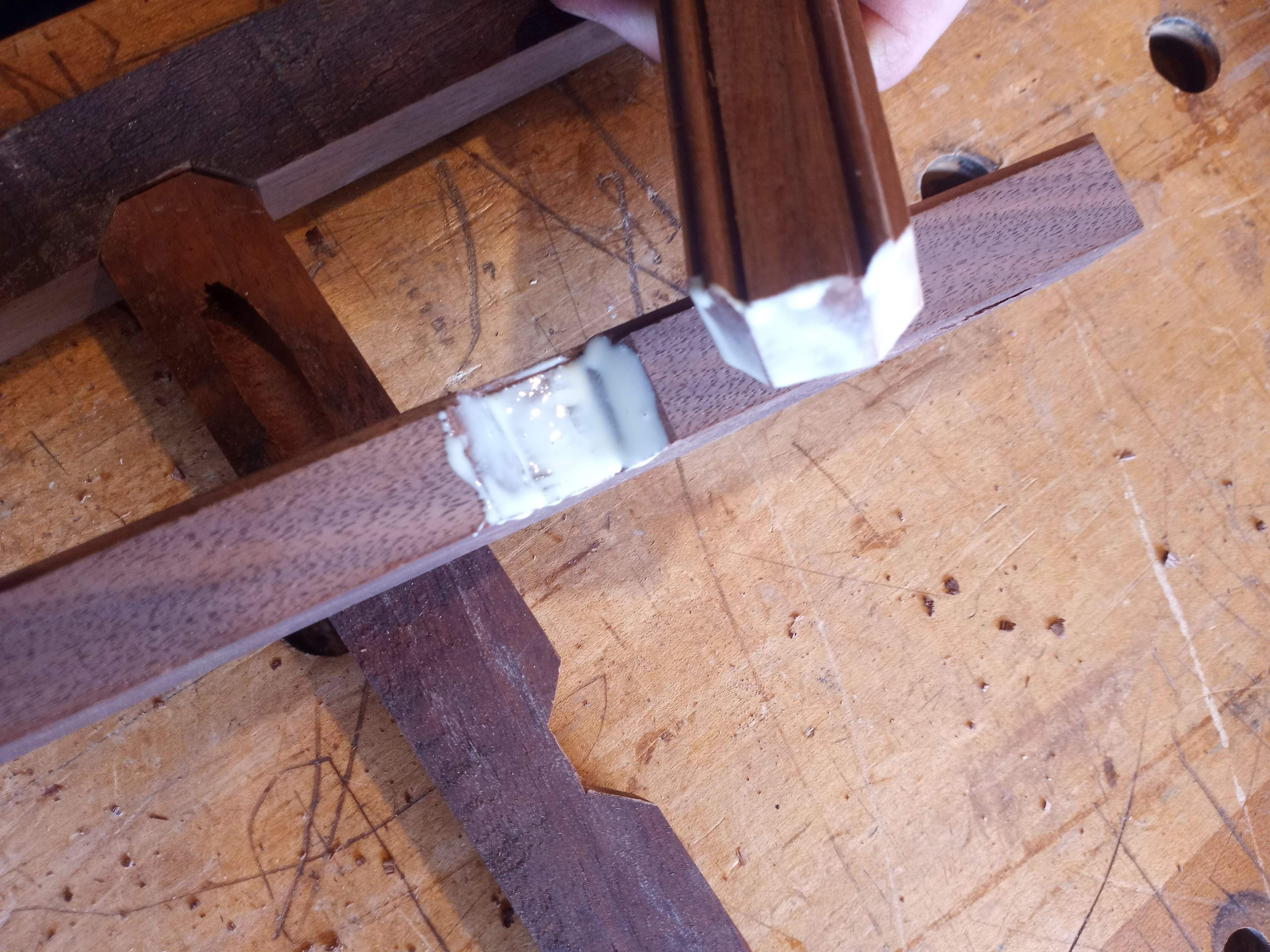
Wood glue will reinforce the fasteners.
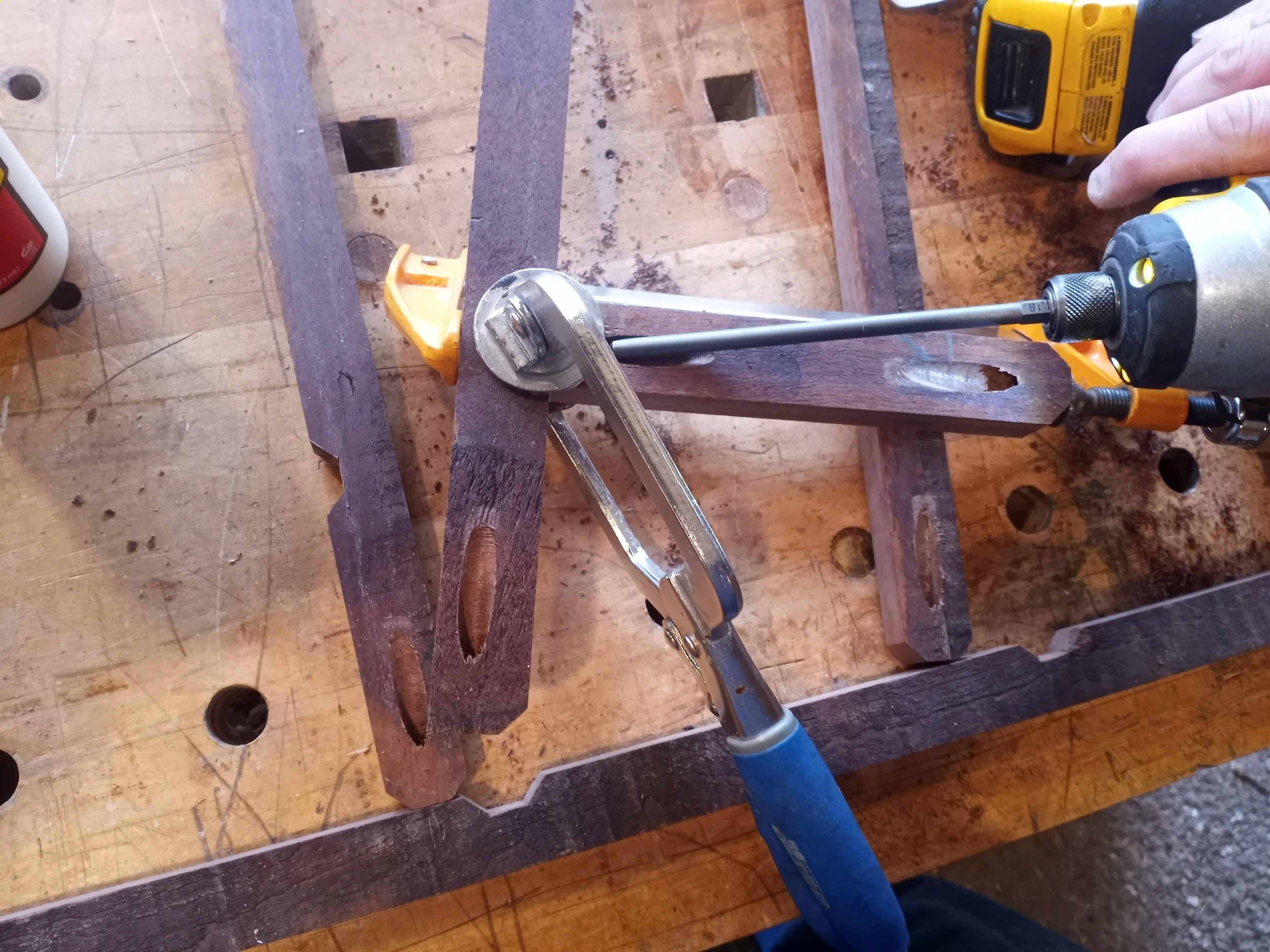
A clamp aligns the small stiles to the rails I drive the screws.
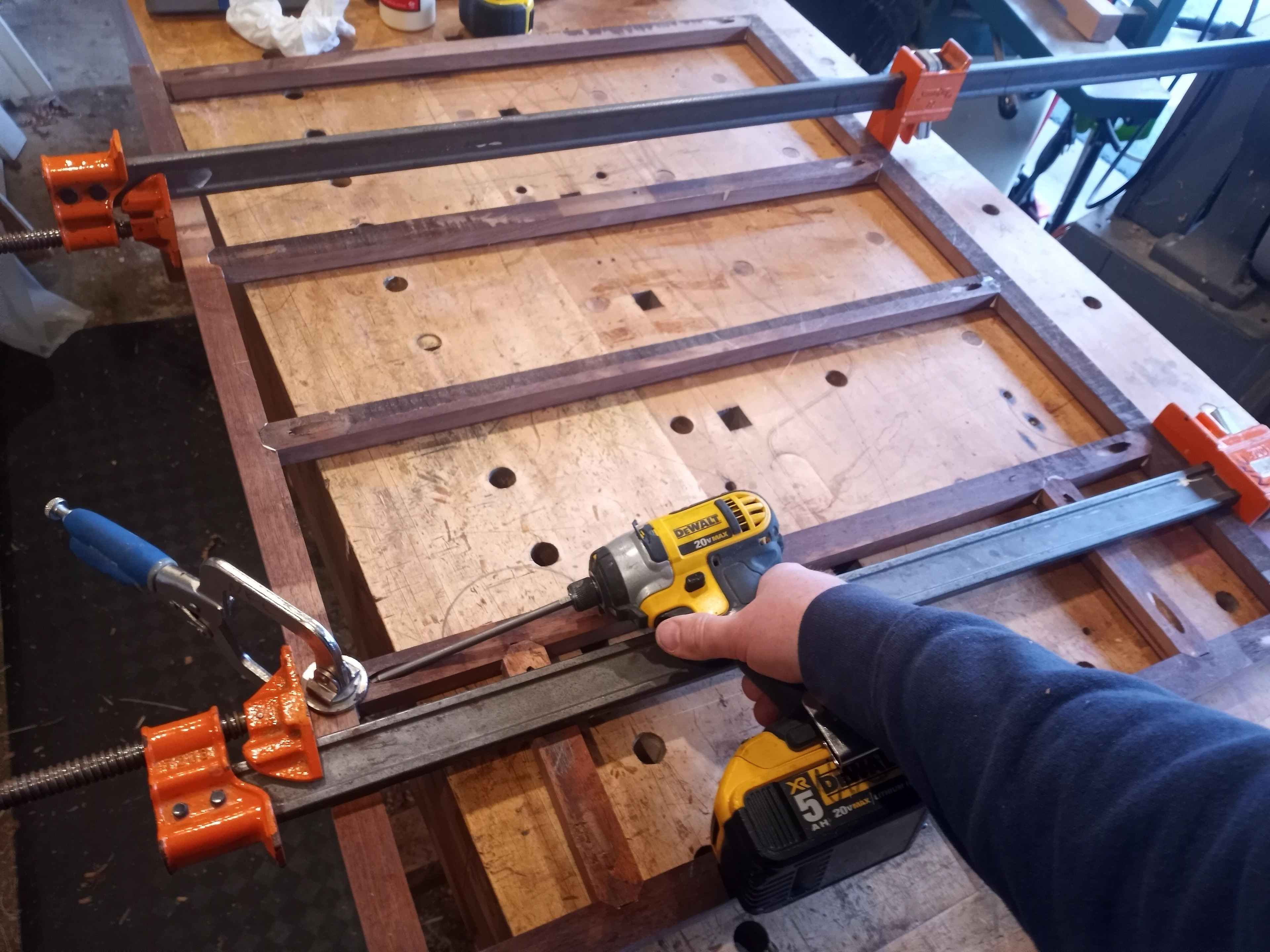
A bar clamp holds the outer stiles to the rails during assembly. The face frame is built from walnut that I salvaged from a discarded dining room table top.
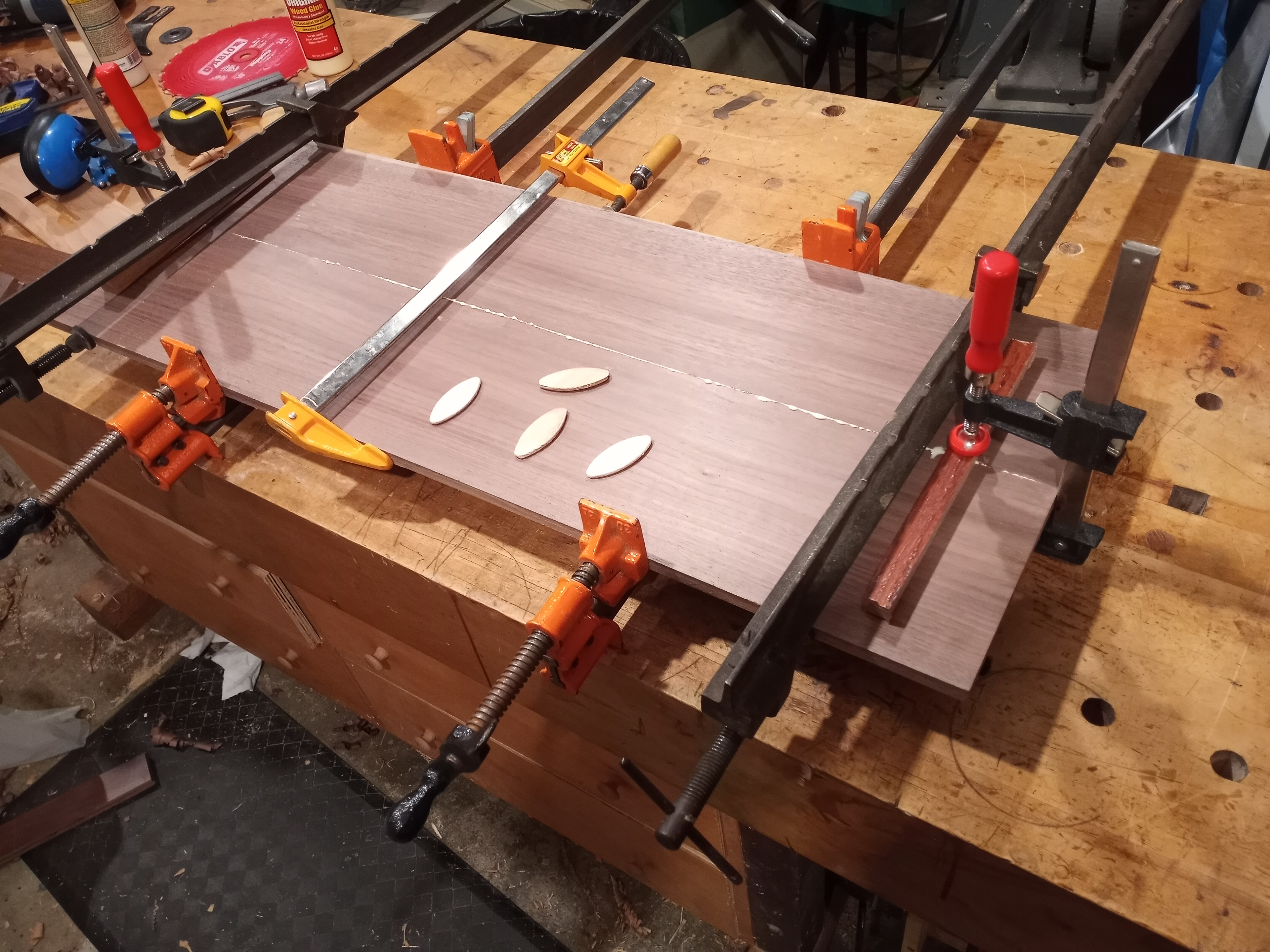
Gluing up the panel for the frame and panel side. The panel was actually a wide, rough sawn board that I had to rip in half to fit through my thickness planer. Now I'm gluing it back together with wood glue, some biscuits to help with alignment and clamps.
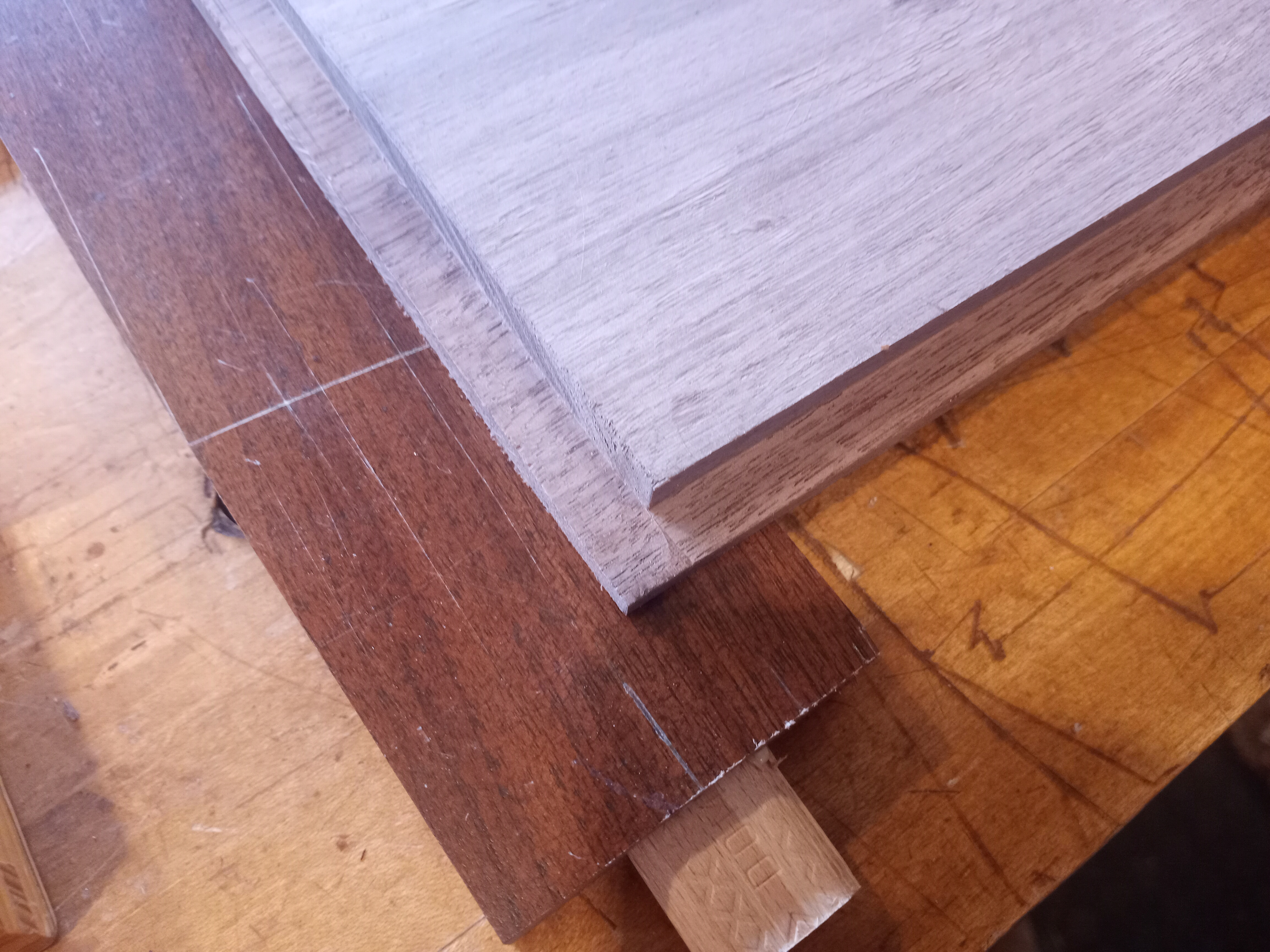
The frame and panel sides is built with loose mortise and tenon joints gluing together the rail and stiles. I plowed grooves into the sides of the stiles and rabbeted the backside of the panel to recess into the groove. I'll want the full 1/2" thickness of the panel in order to mount the drawer slide hardware later on.
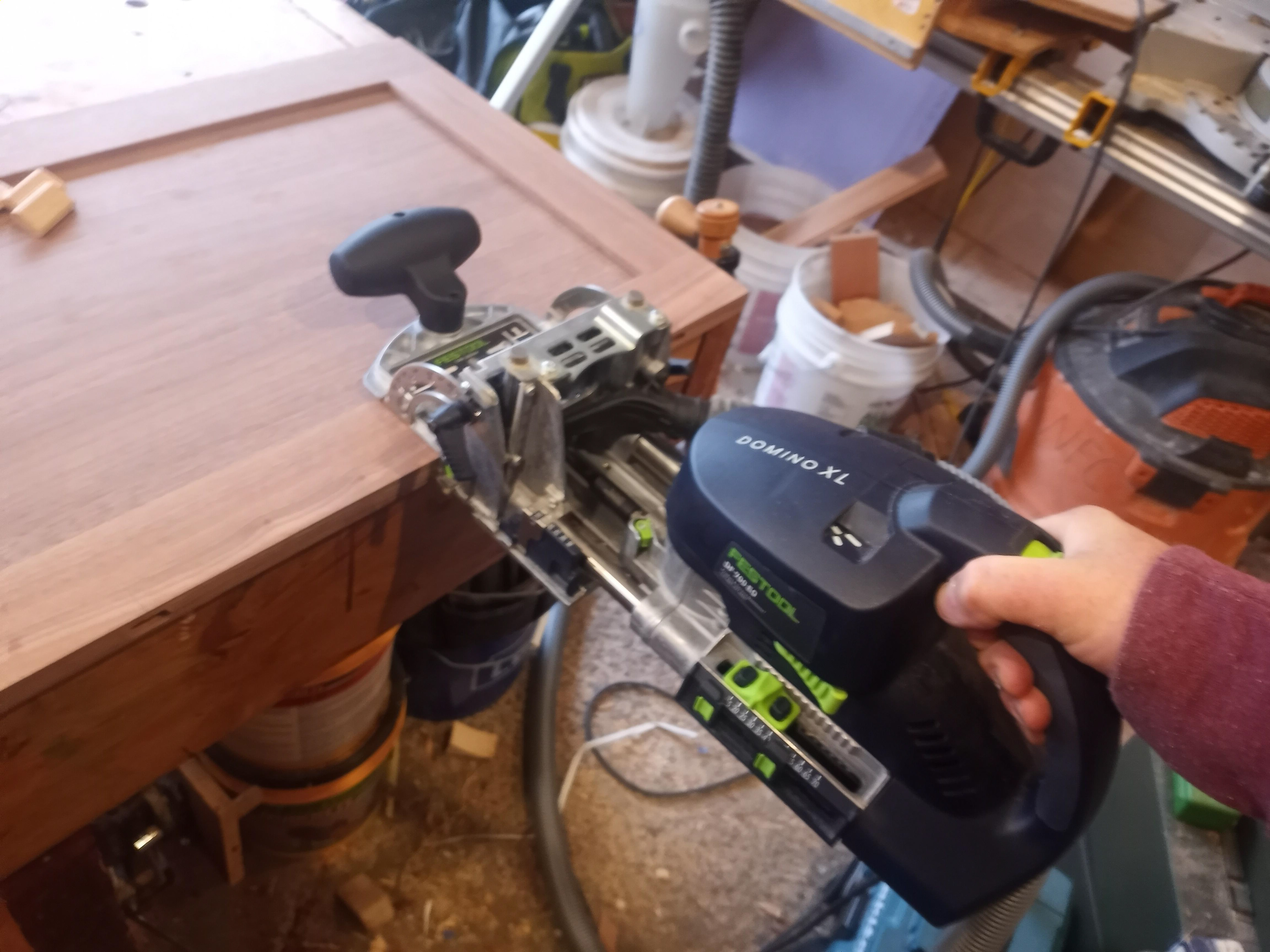
I'm using the domino machine to cut mortises for dominos (loose tenons) that will glue the frame and panel side to the face frame.
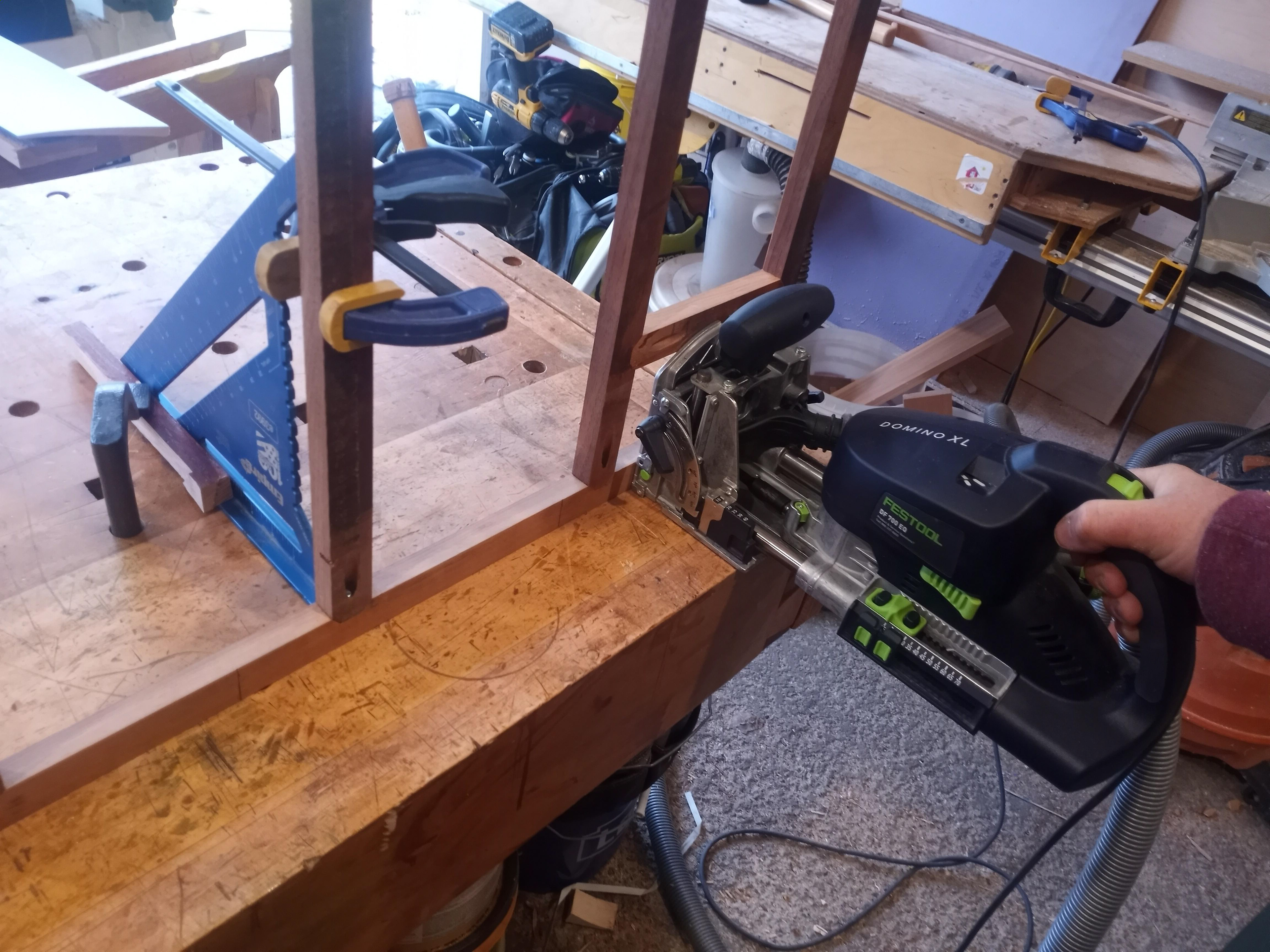
The domino machine cuts mortises into the backside of the face frame that correspond those in the frame and panel side.
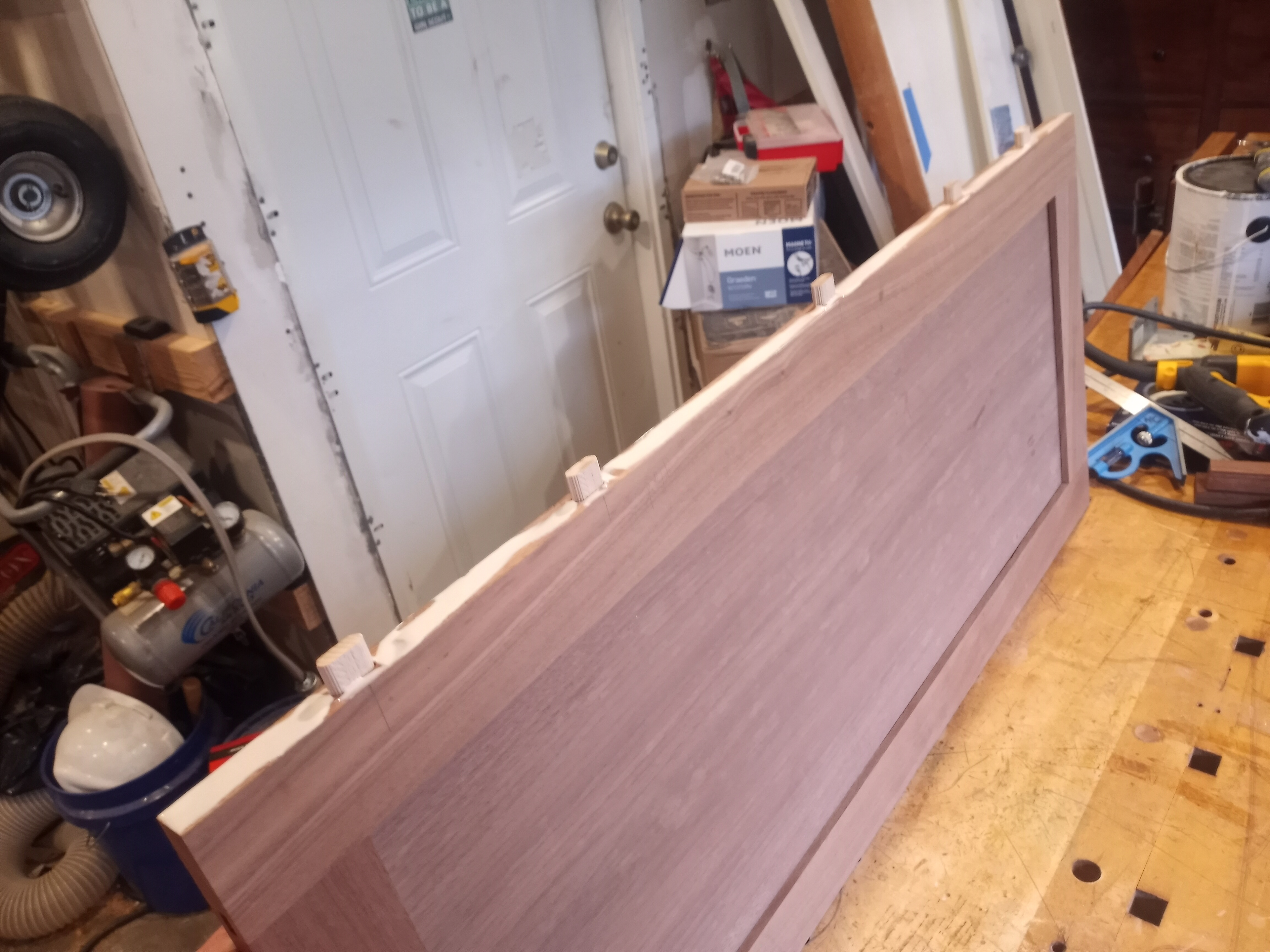
I'm preparing to glue and clamp the side to the faceframe.
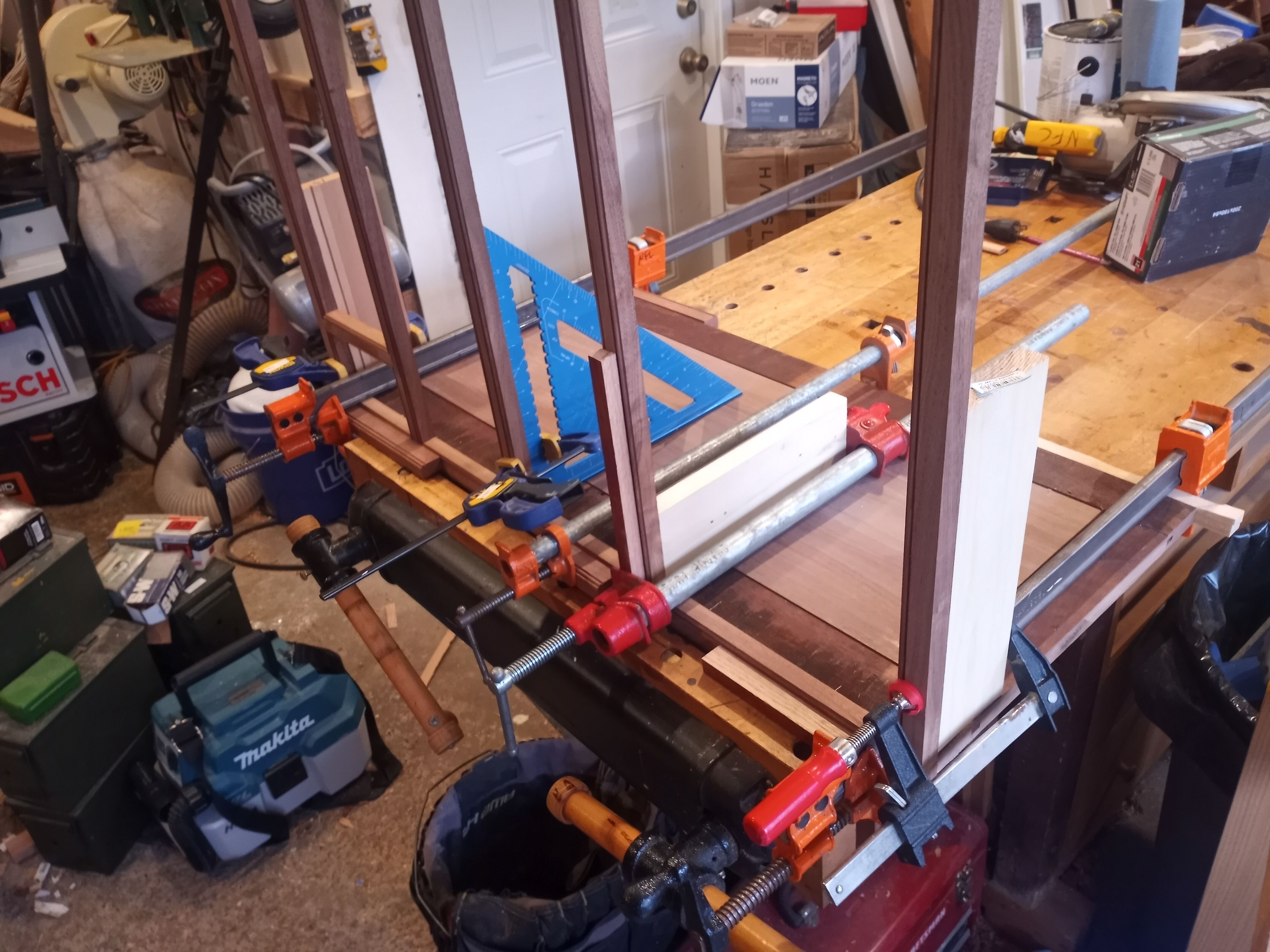
I've clamped some blocks of wood to the rails in order to keep the faceframe square to the side as I clamp the side in place.
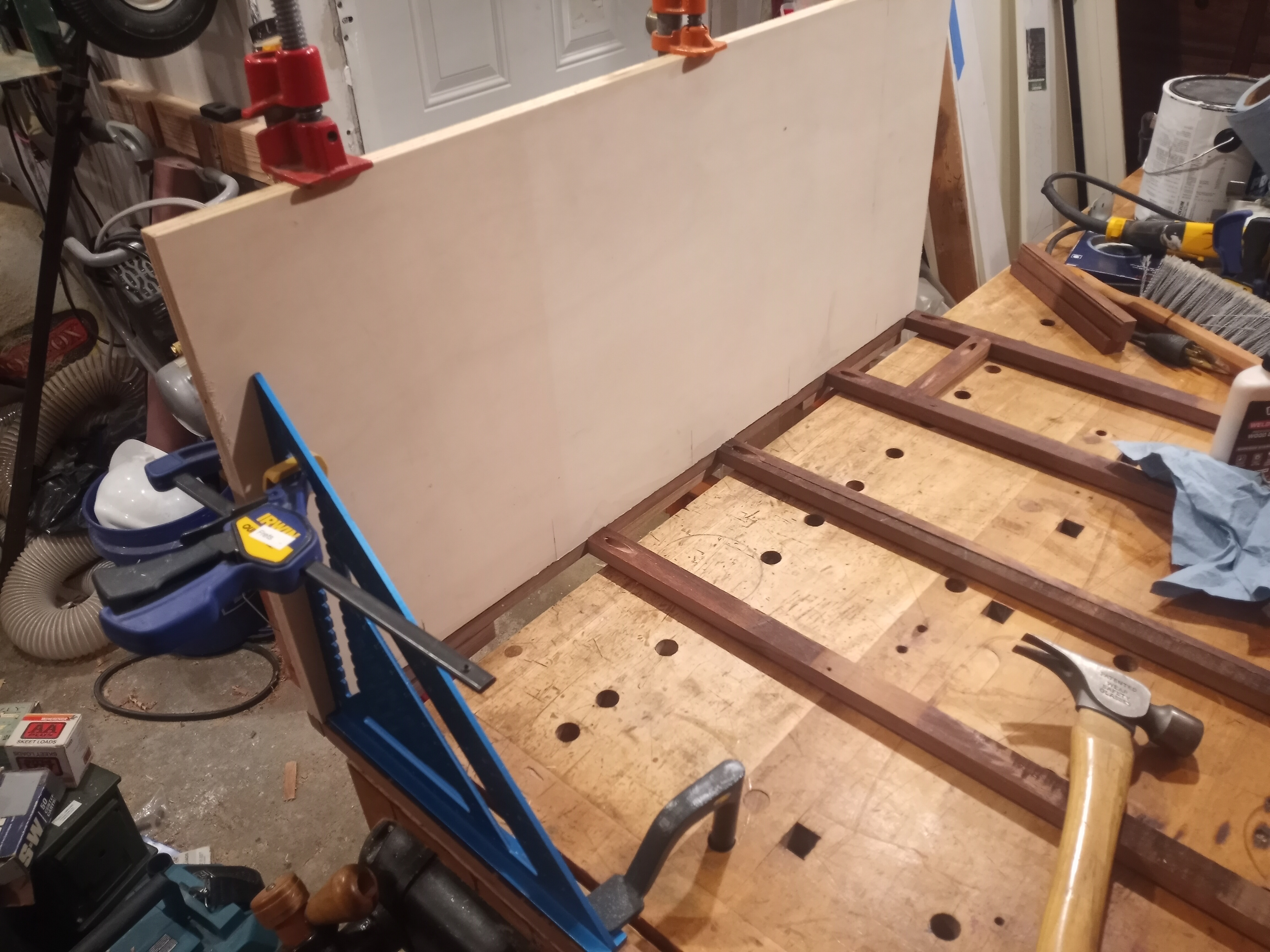
I'm repeating the same gluing and clamping routine with the hidden plywood side. This side won't be seen because it will be installed against a wall so I've saved time and money by using plywood here.
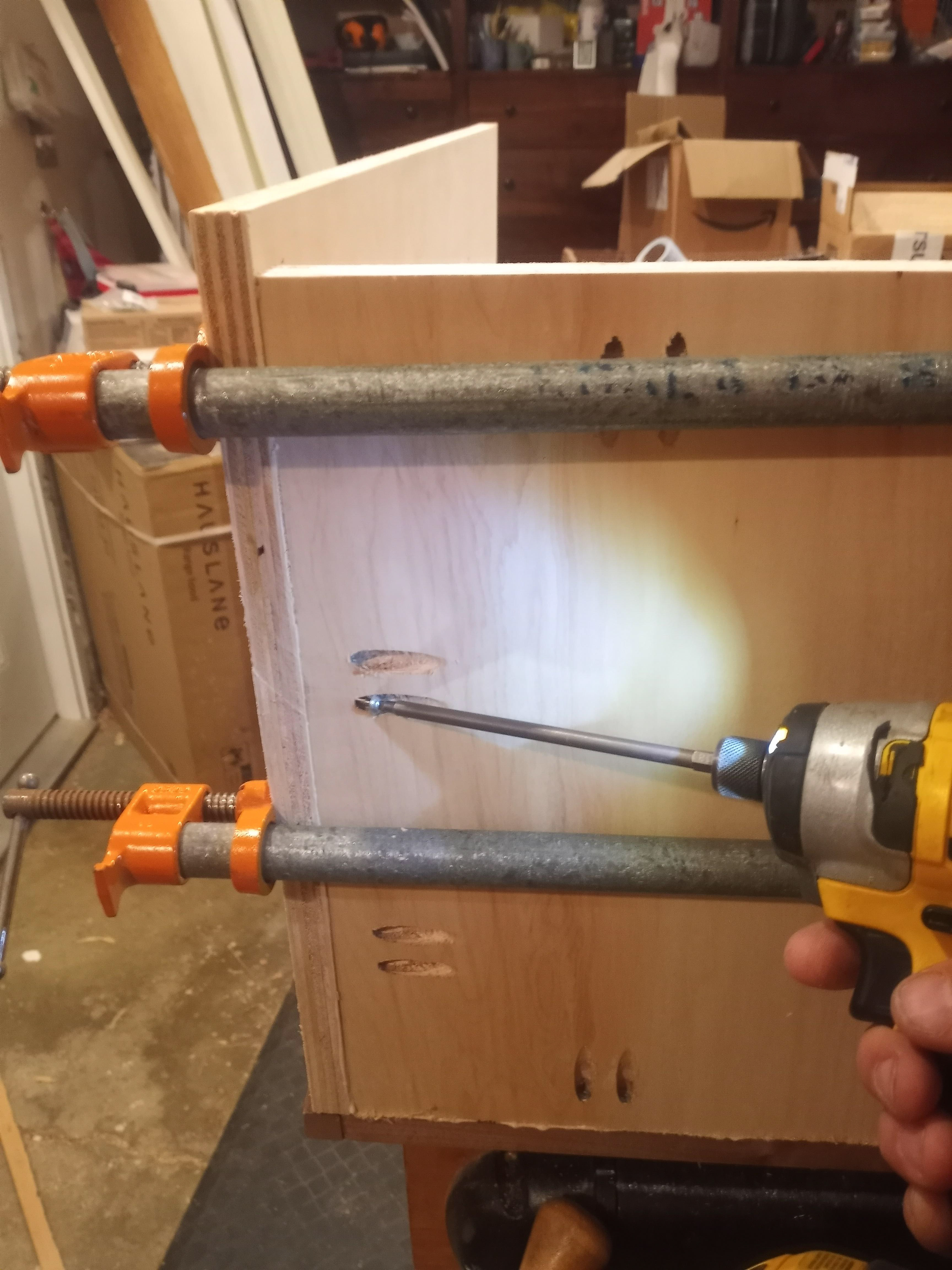
The back and bottom are attached to the faceframe and the sides with pocket screws and glue.
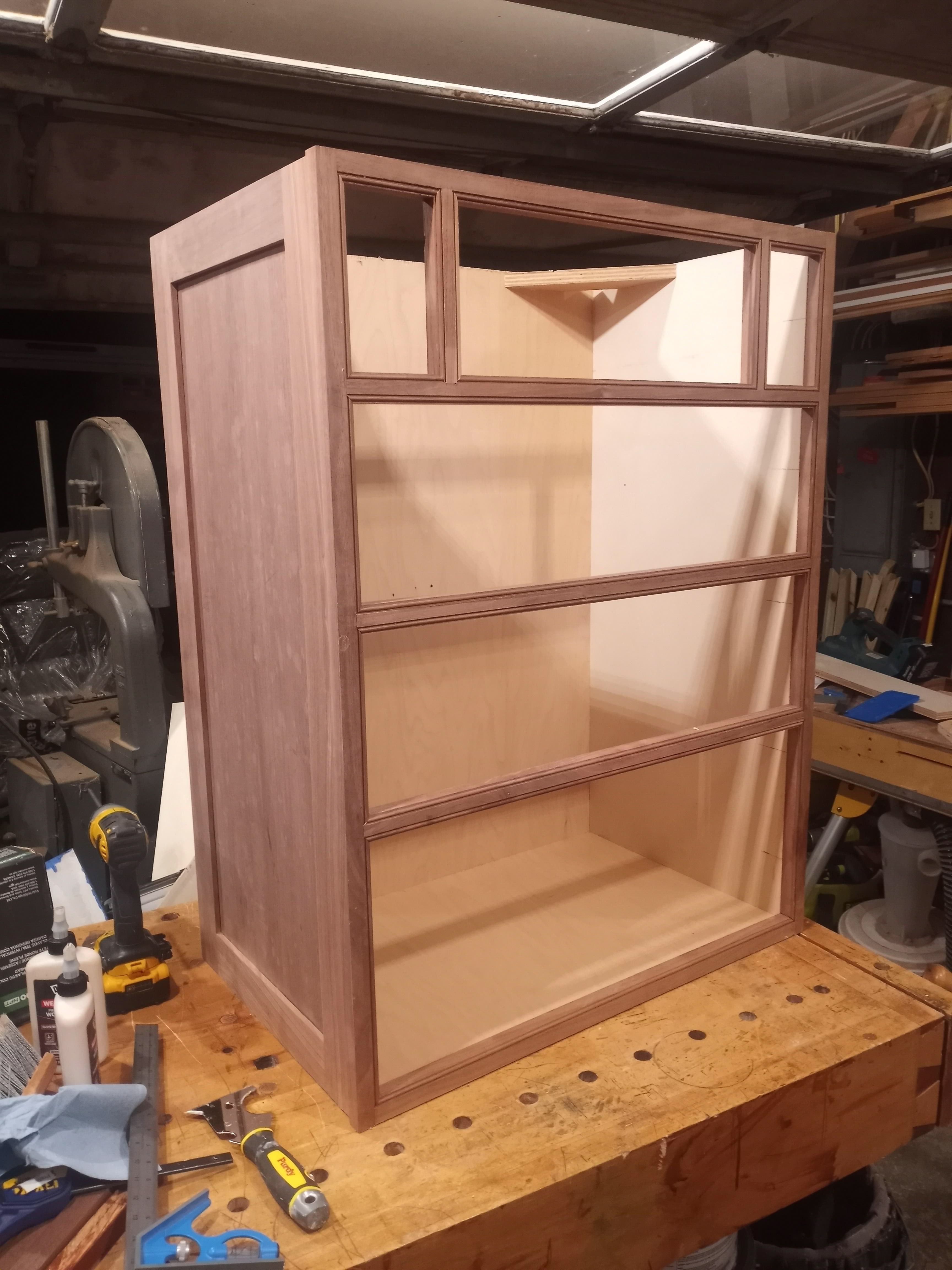
Here is the assembled carcass. My next step is to mill the drawer fronts and cut them to fit the openings in the faceframe.
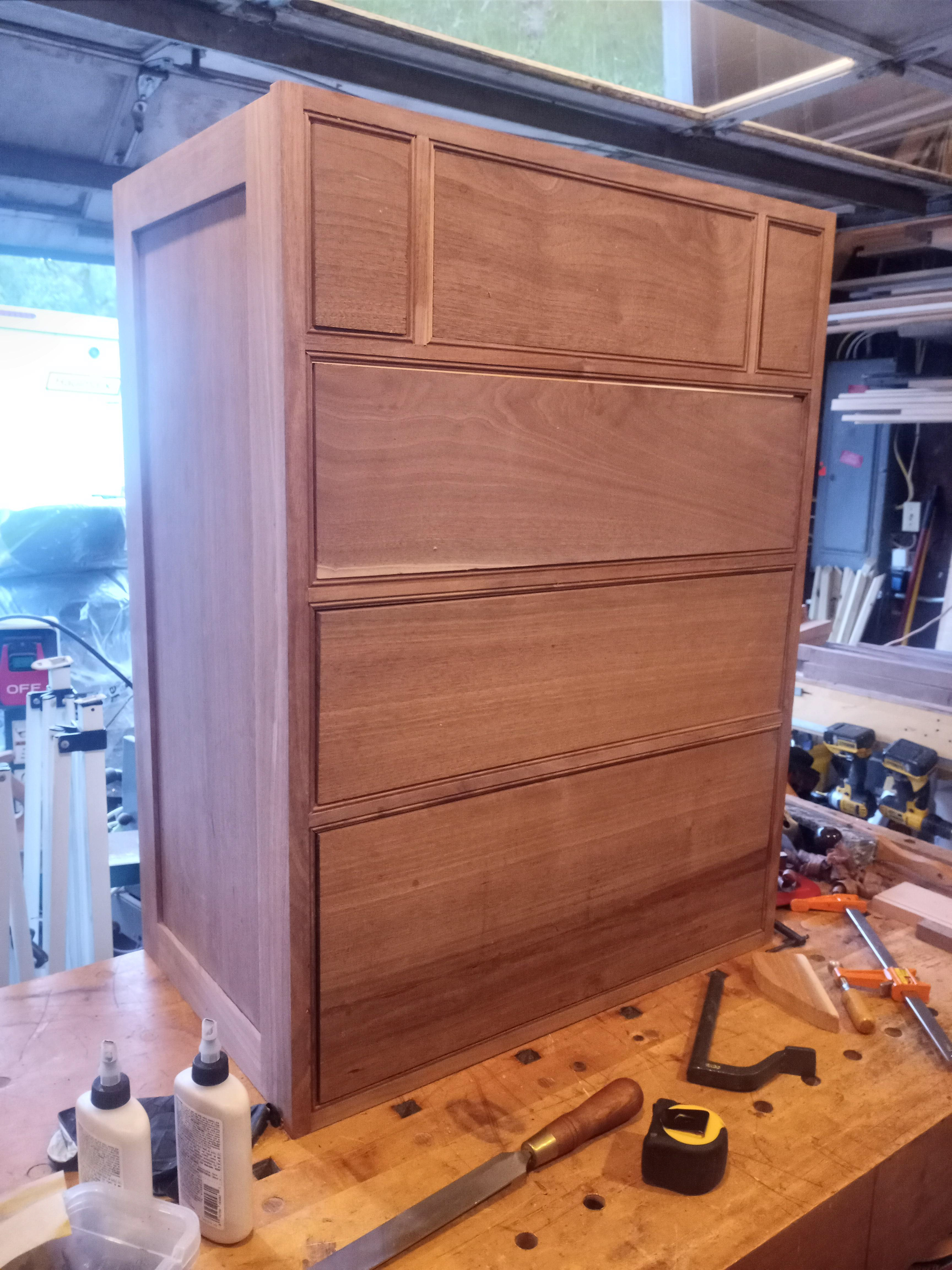
With the drawer fronts ready to go, I'll sand the walnut up to 220 grit and set it aside for varnishing later on.
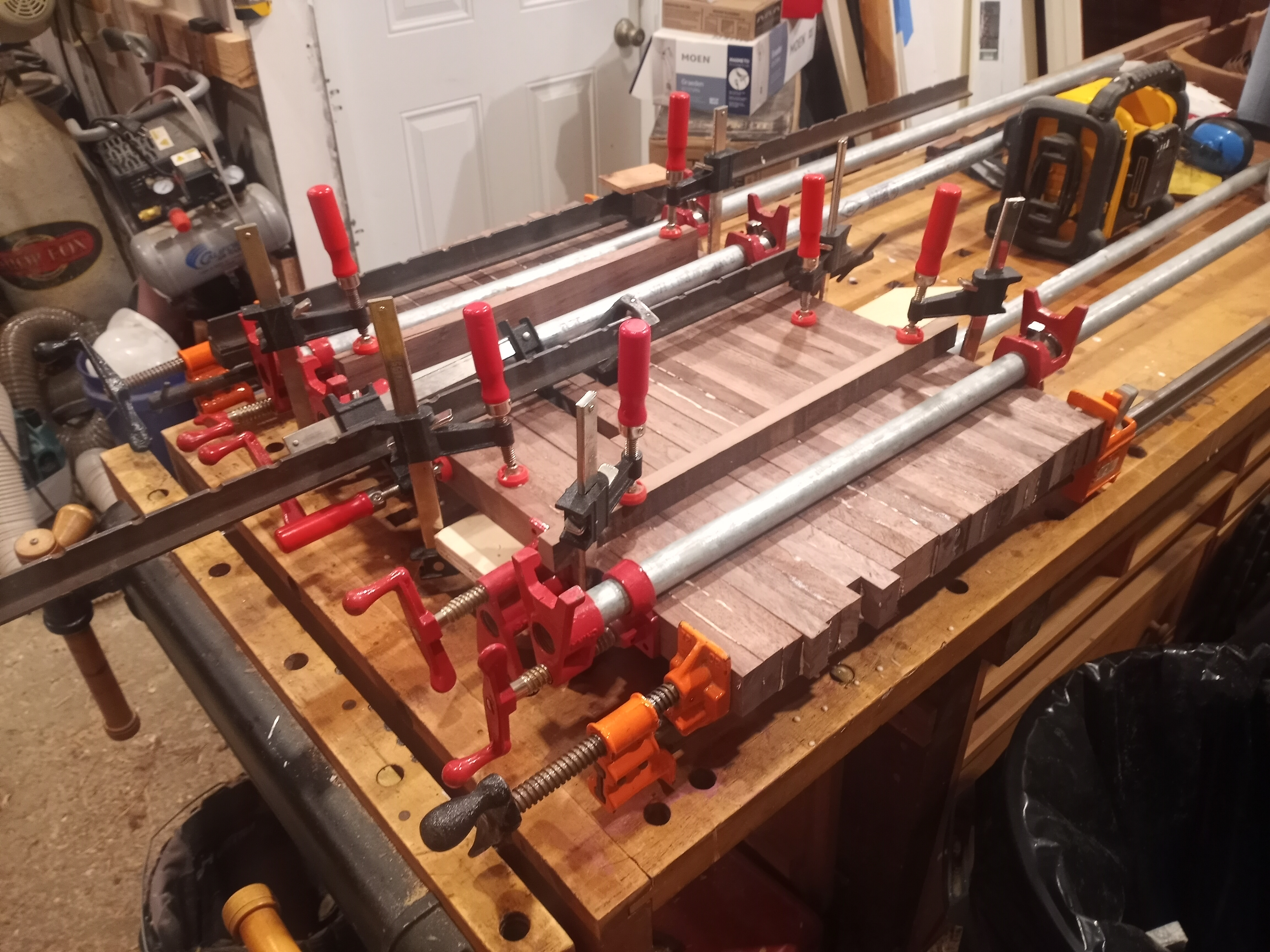
Building the countertop starts with milling and face gluing a bunch of strips of 3/4" flatsawn walnut. I used some shorter pieces to glue up at the edge of the sink leaving some gaps. This gap area will be cut out later for the sink.

A belt sander with a course grit sanding belt makes quick work of flattening the counter top.
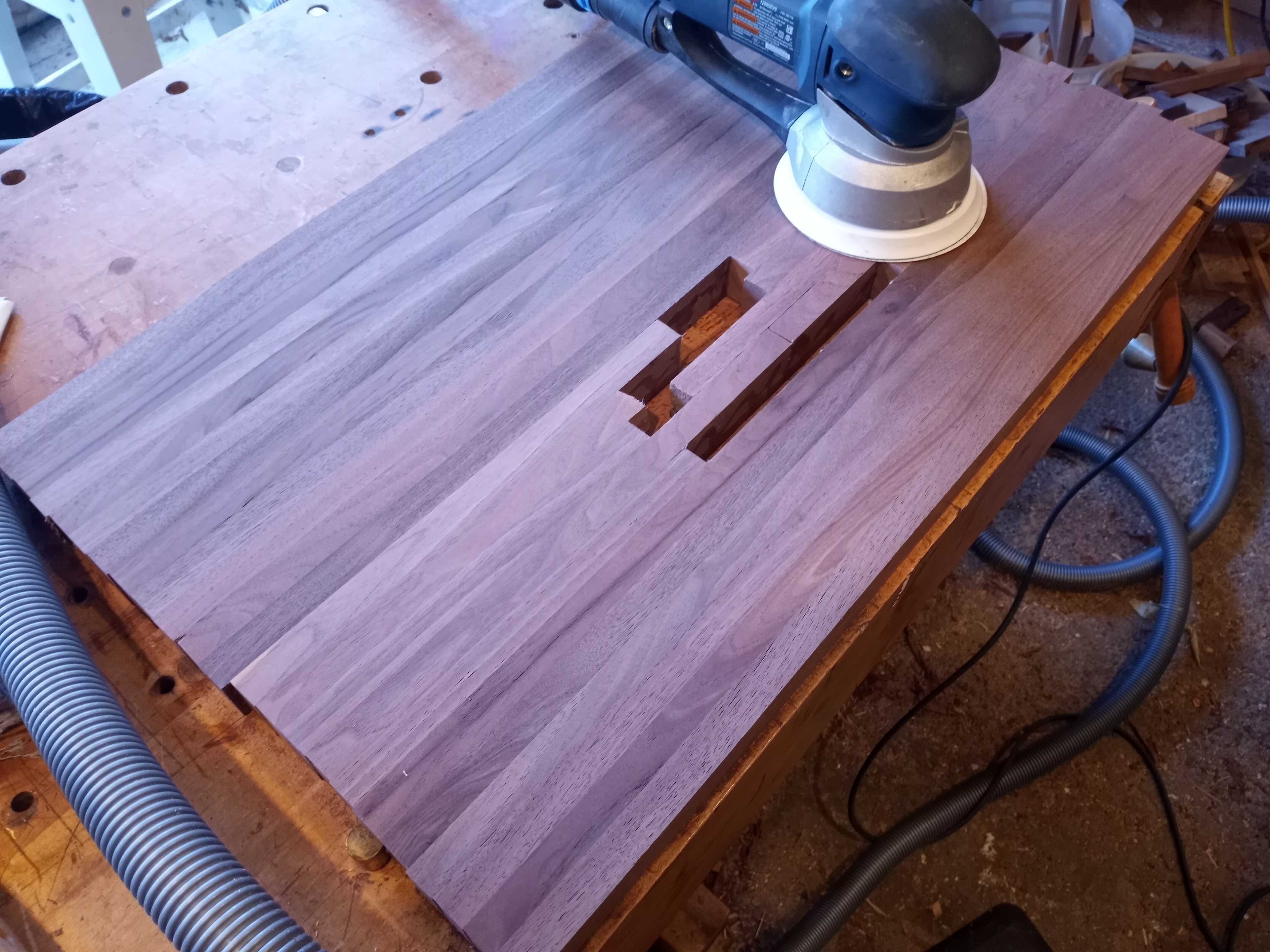
I'm machine sanding the counter top up to 150 grit. Next I'll use a circular saw to cross cut the slab to it's rough length.
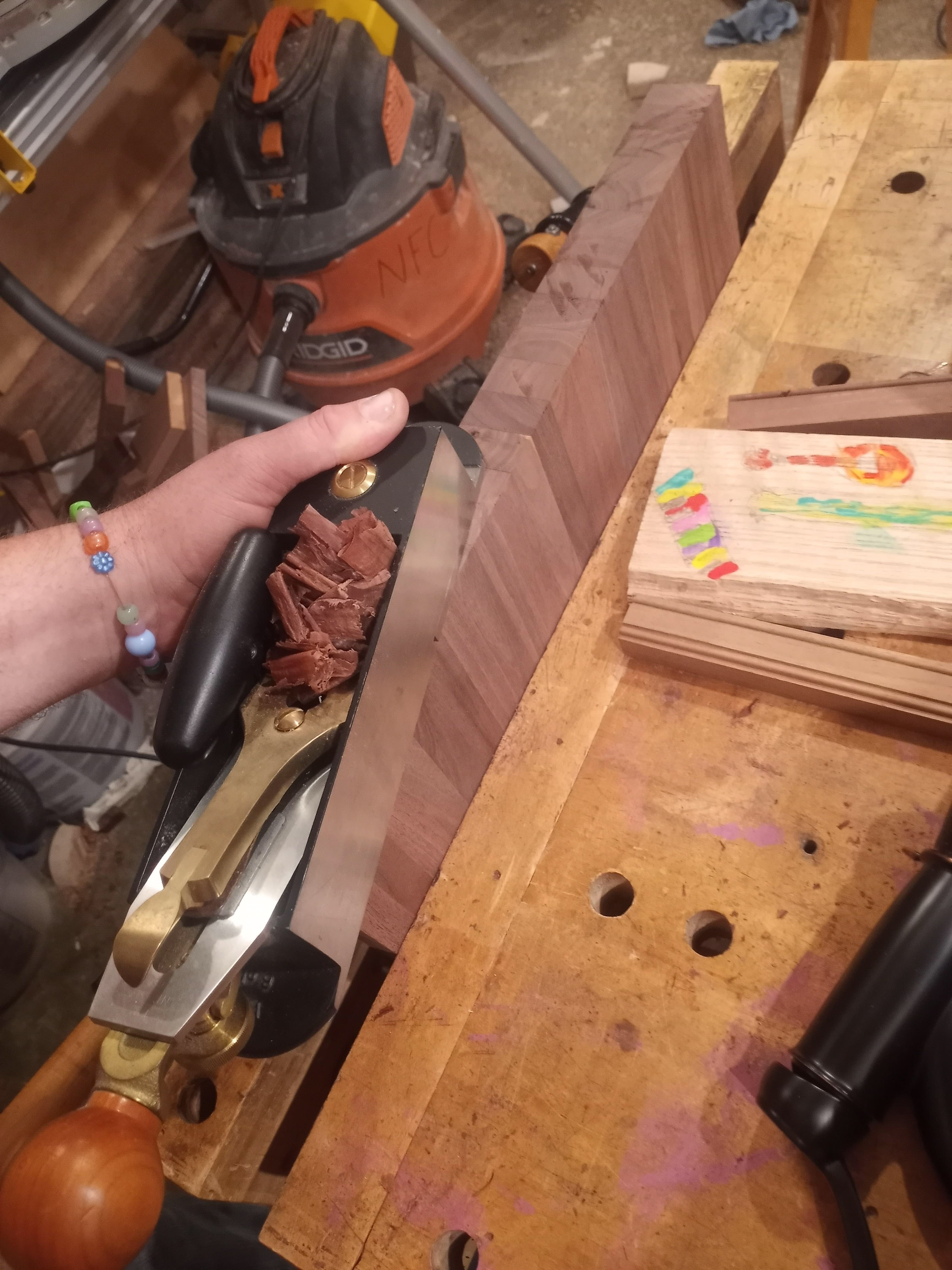
I'm cleaning up the circular saw marks with a miter plane on the edge of the countertop that will be exposed.
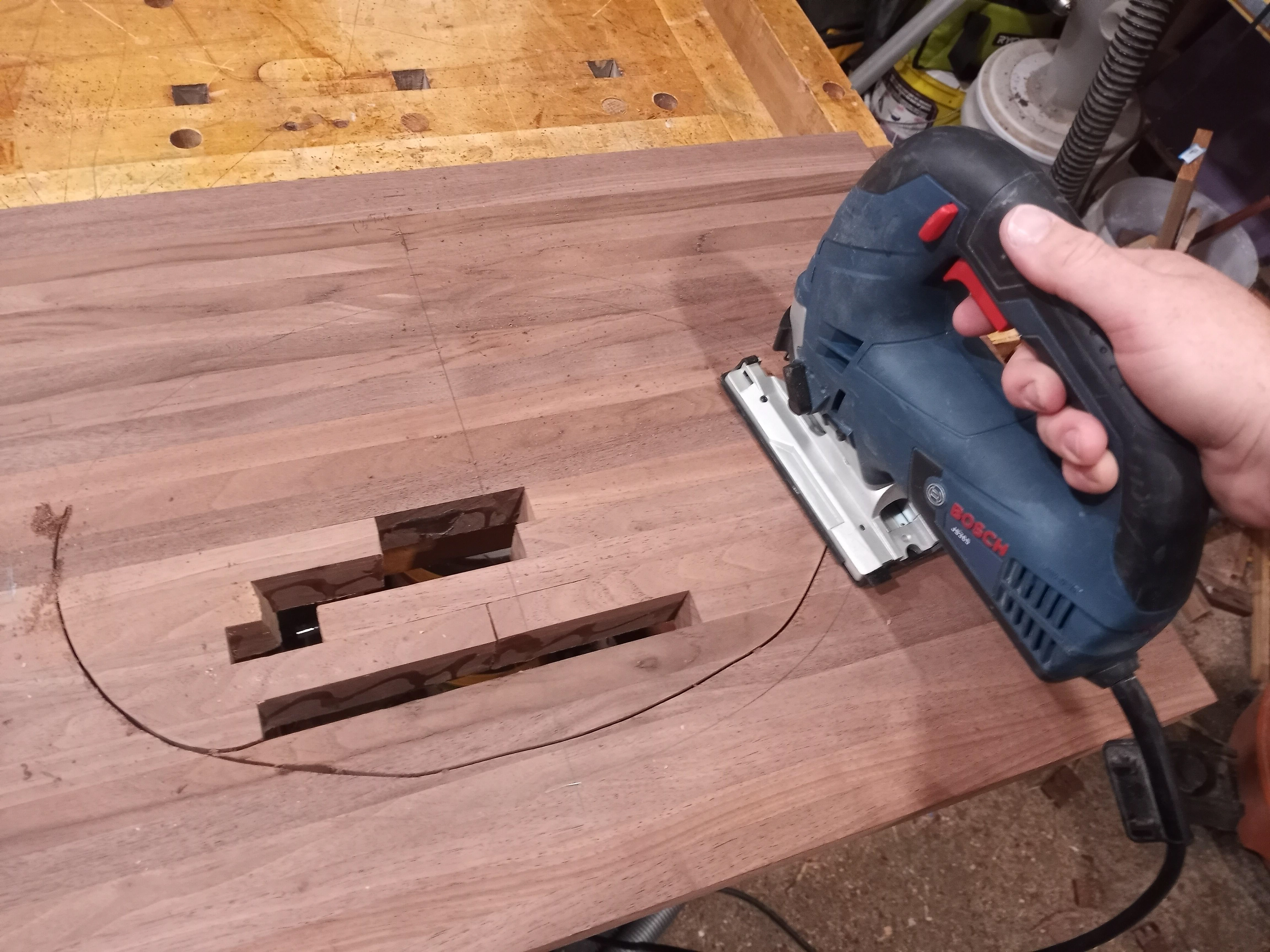
I'm cutting out the hole for the sink with a jigsaw.
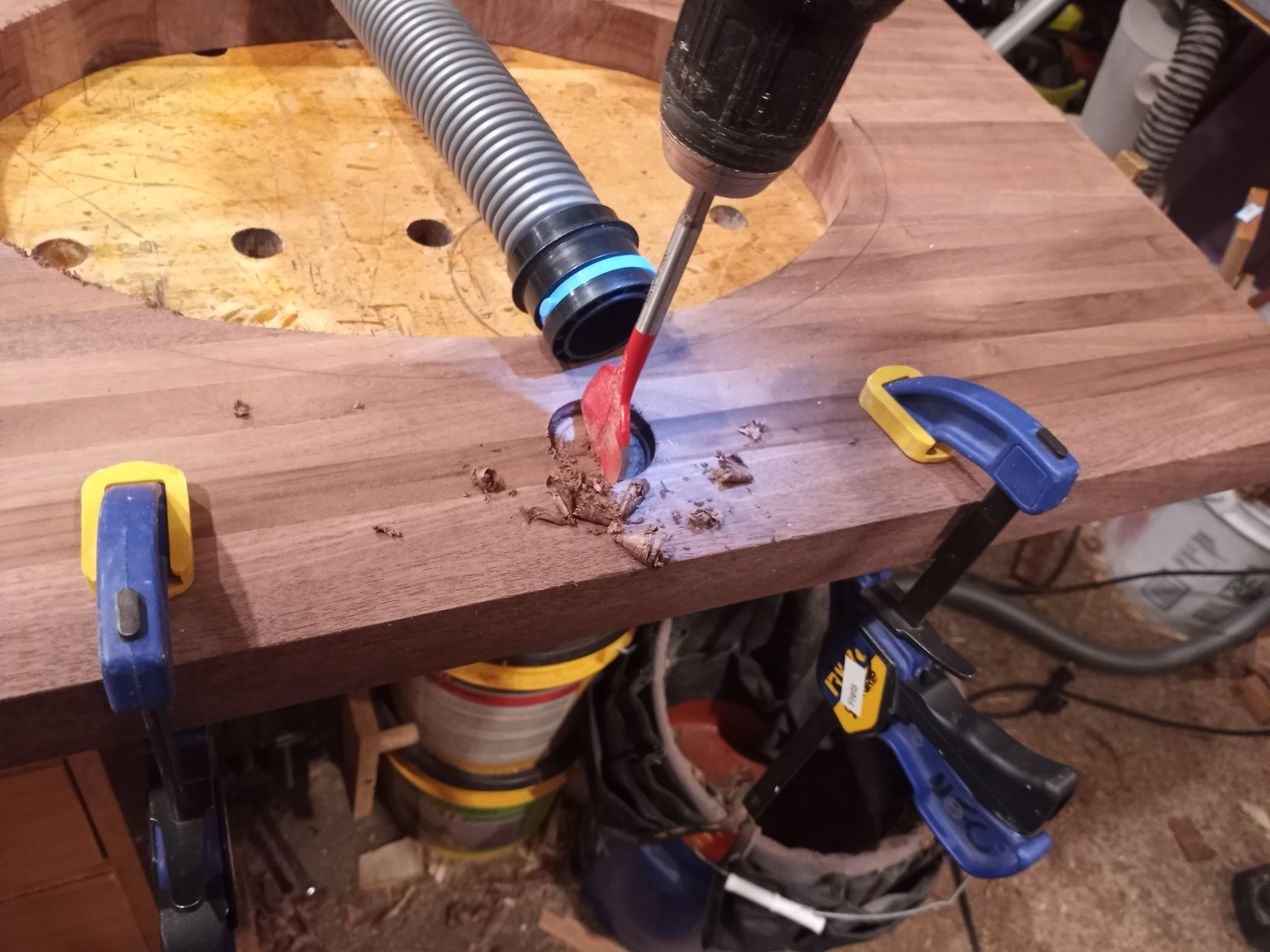
A spade bit drills the hole for the faucet.
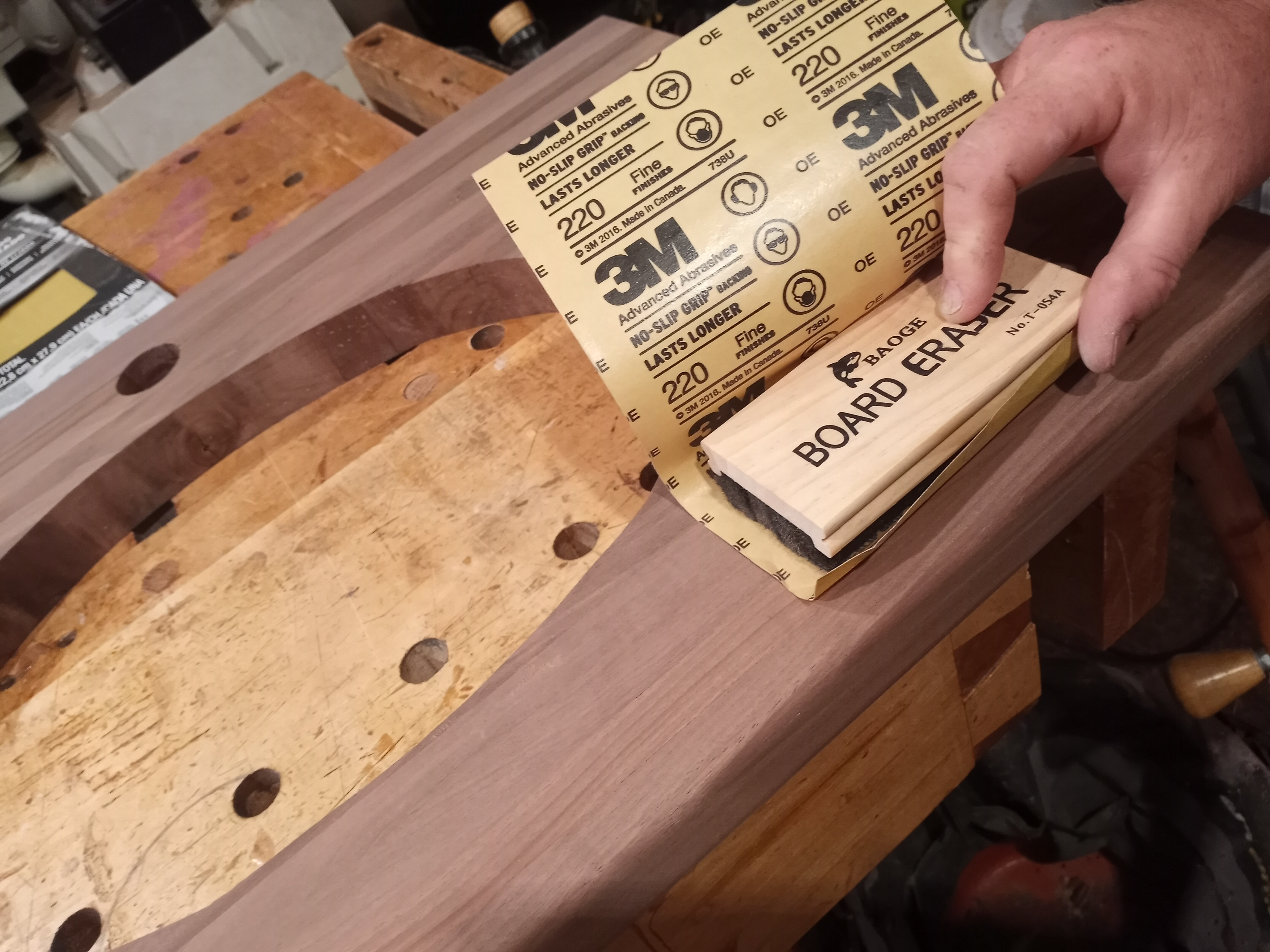
I cleaned up the saw marks on the front edge with a handplane then rounded over the front edge and left side of the countertop with a router. Now I'm hand sanding with the grain to 220 grit to prepare for varnishing.
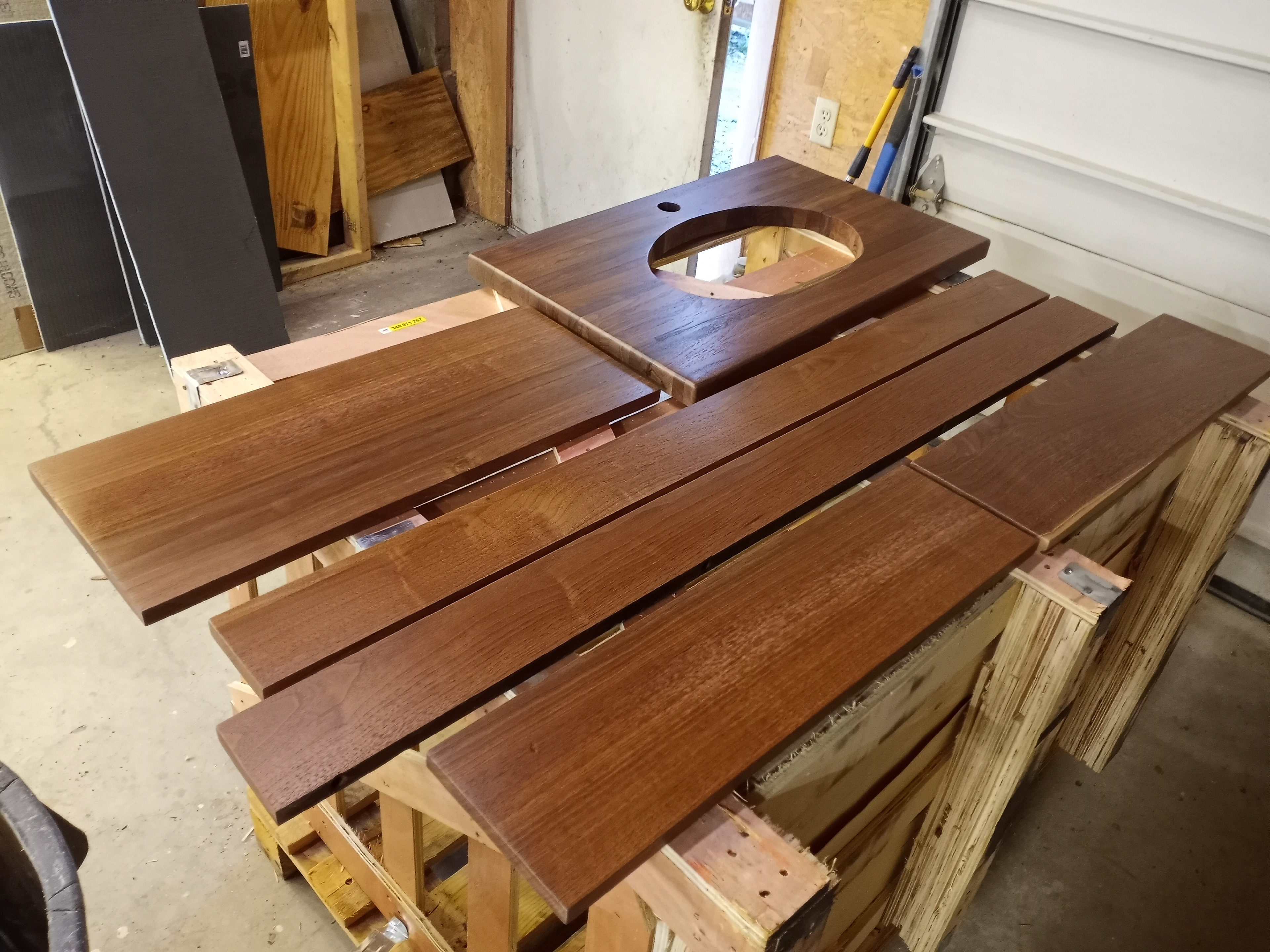
I'm spraying the cabinet with a two part conversion varnish which is an excellent finish for wood that's exposed to water.
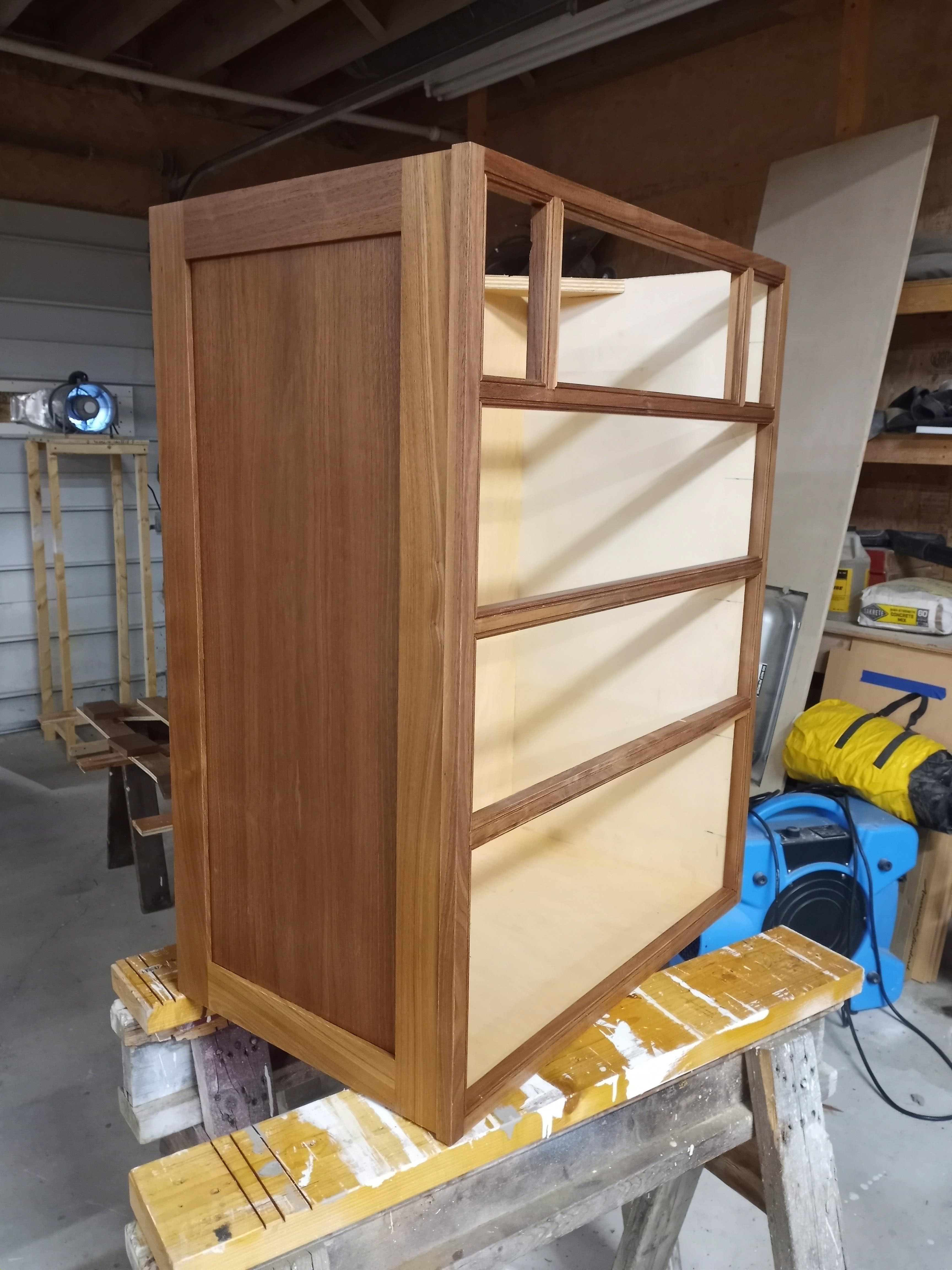
The spray gun allows me to quickly achieve an even coat of varnish. I'll spray a minimum of 3 coats.
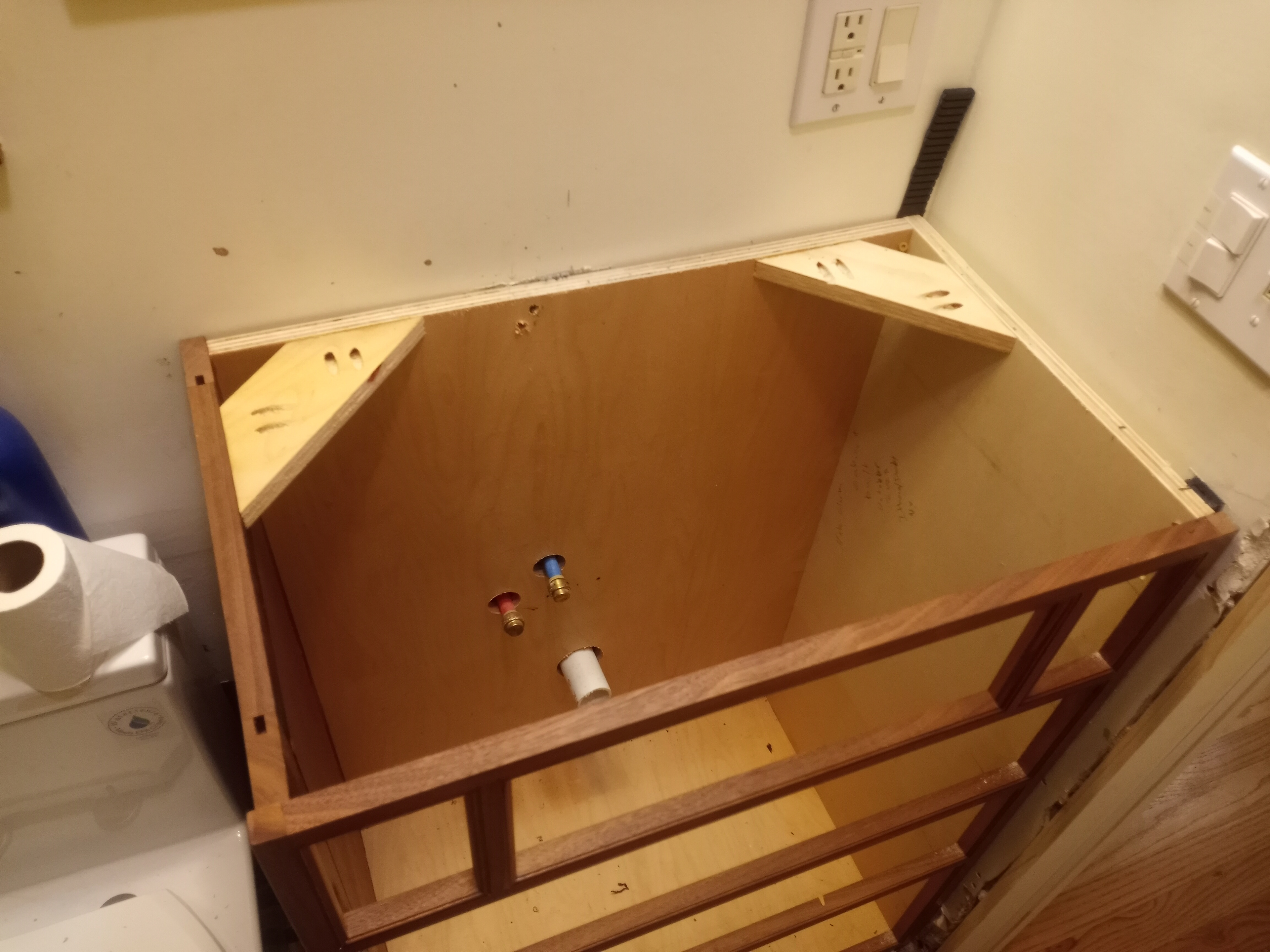
Installation day is here. Some shims and screws get the the cabinet screwed to the wall studs nice and level. After the plumber installs the finish plumbing, I'll build the drawers to tightly fit around the plumbing.
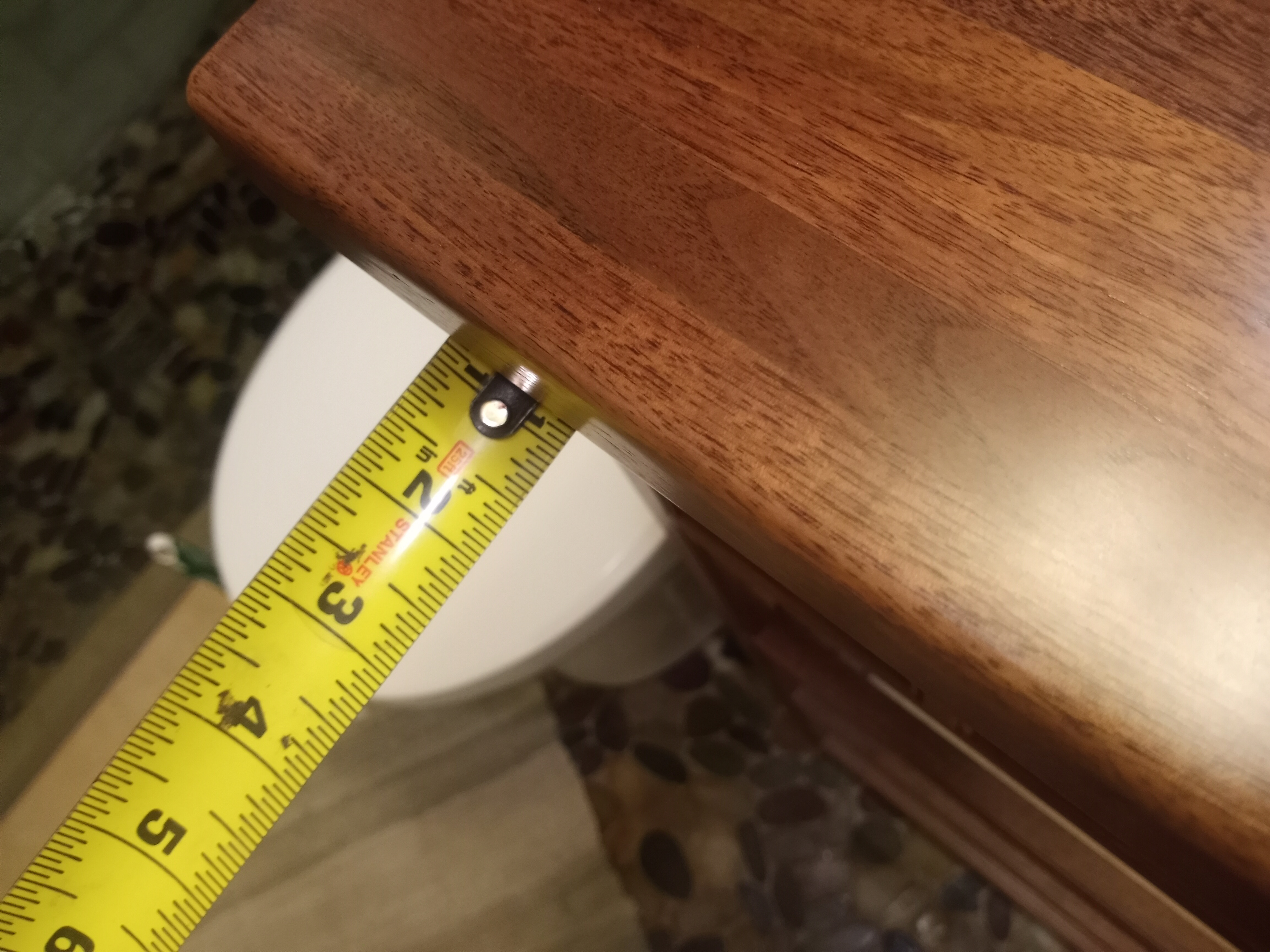
I've got the countertop overhanging by about 7/8" on the front and side.
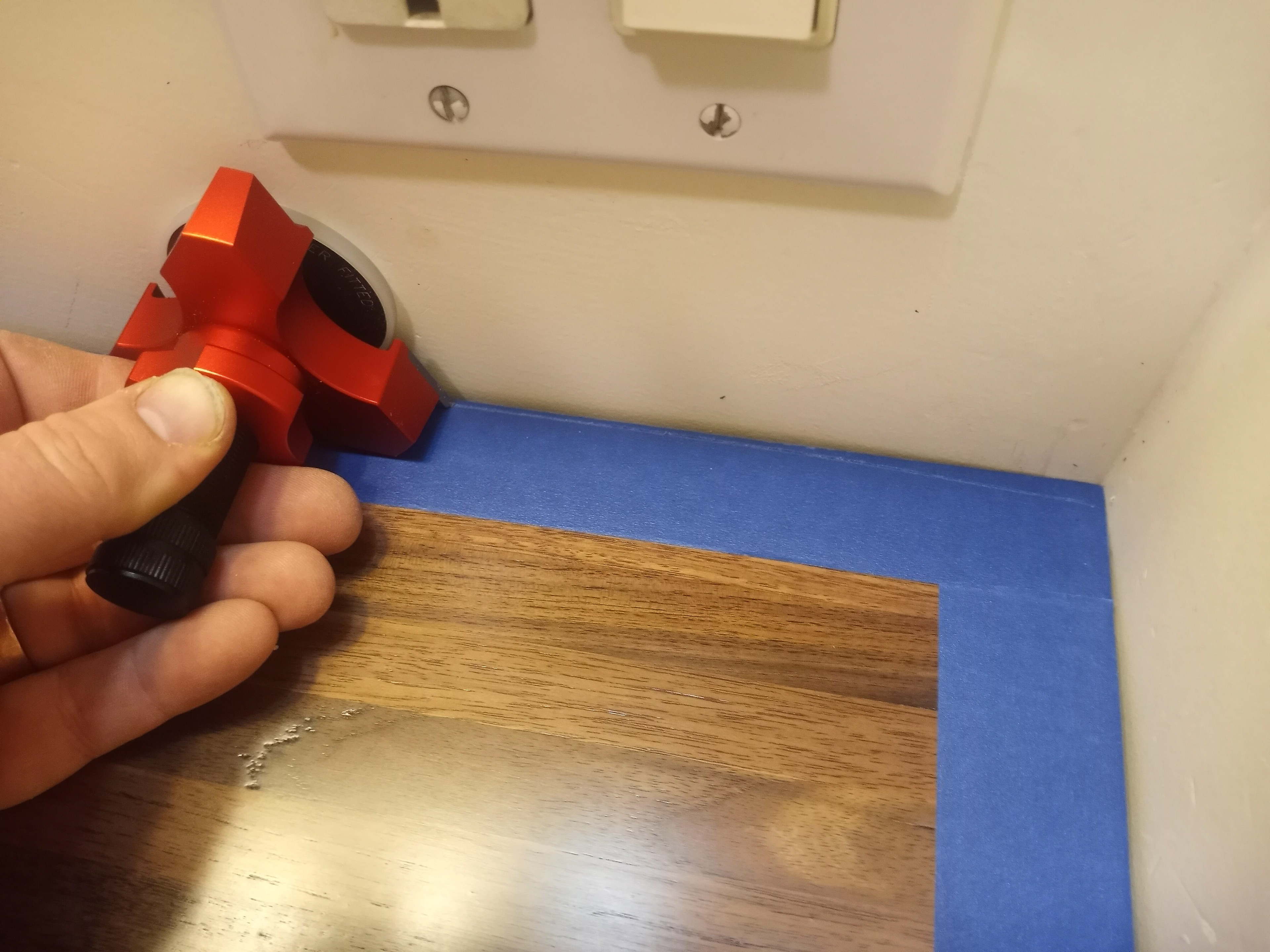
I'm scribing the countertop to the walls. Blue tape makes the razor knife scribe marks easier to see. I'll use a circular saw and hand plane to achieve a good fit to the wall. I'll attach the countertop to the cabinet with a couple of screws through the corner blocks into the underside of the countertop as well as a bead of silicone. I'll scribe the backsplash to the wall and glue it to the wall with some silicone. Silicone also seals the bottom of the backsplash to the countertop for a waterproof joint.
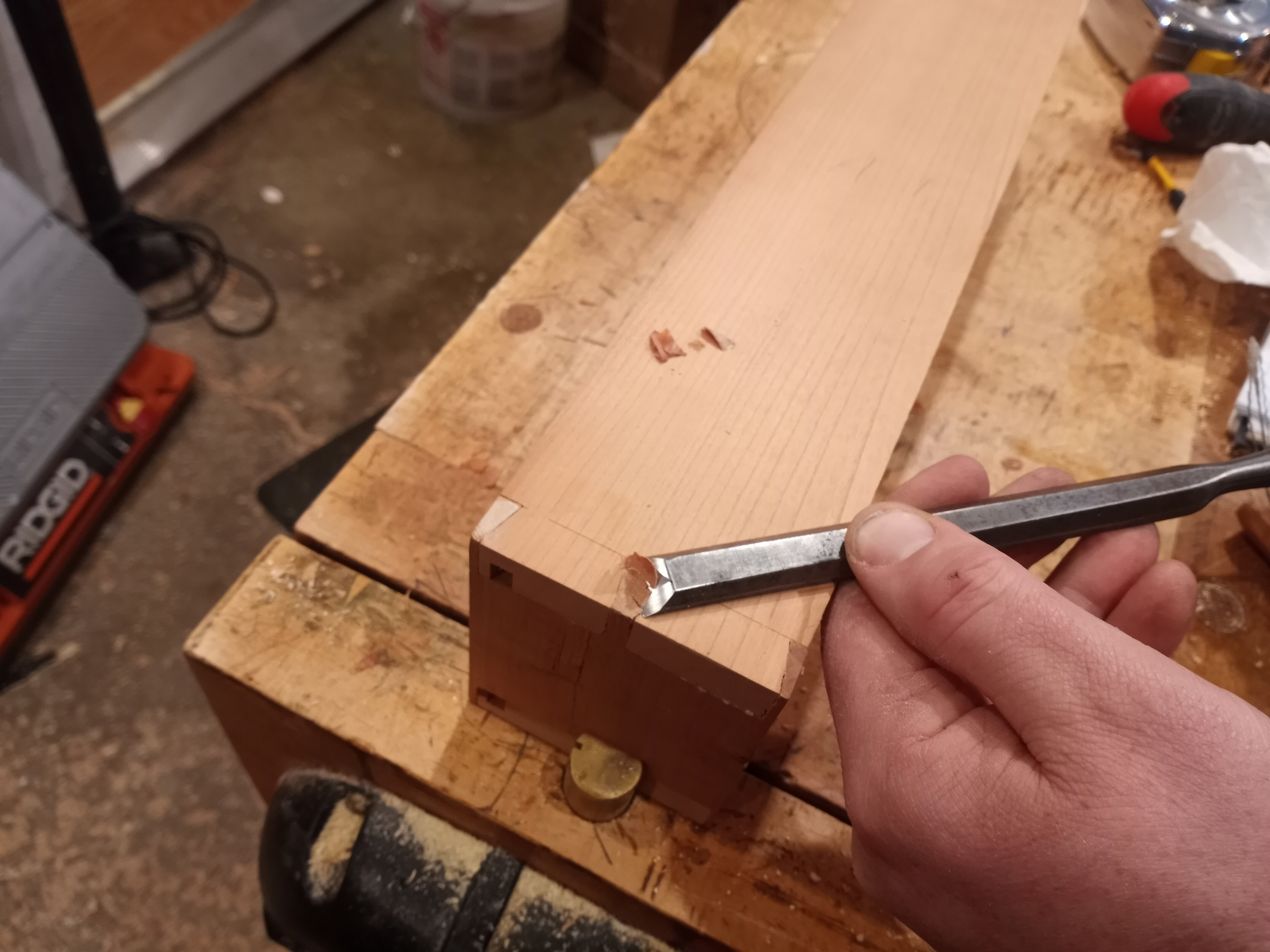
Building the drawers. I built the large drawer boxes from oak using the dovetailing router jig. Now I'm building the small drawers with handcut dovetails from 1/2" cherry. The drawers are a lot lower than the drawer fronts because they are so narrow. If they were any taller, they would be awkward to reach into.
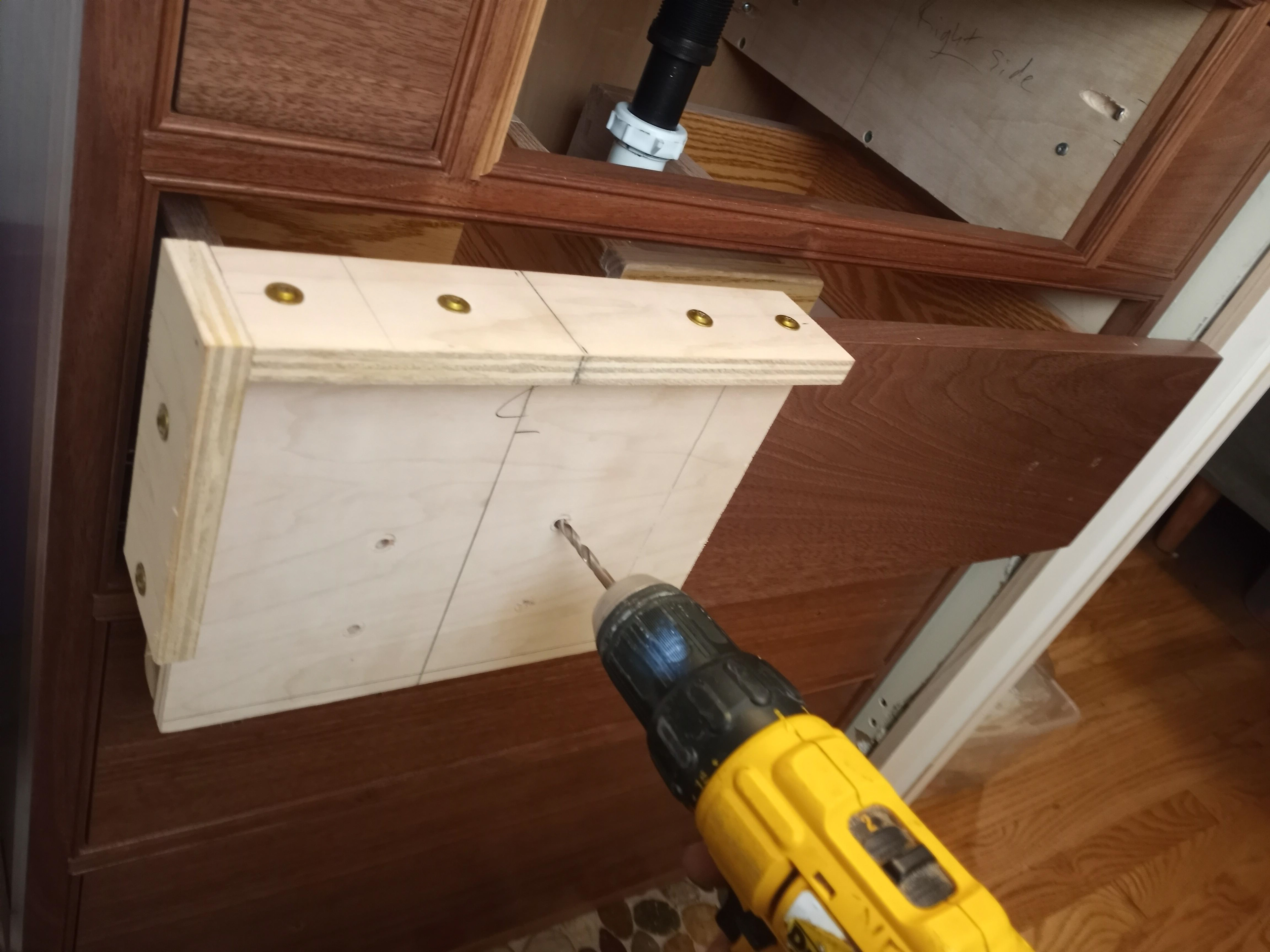
A shop-made jig allows me to accurately drill the drawer fronts for the drawer pulls.
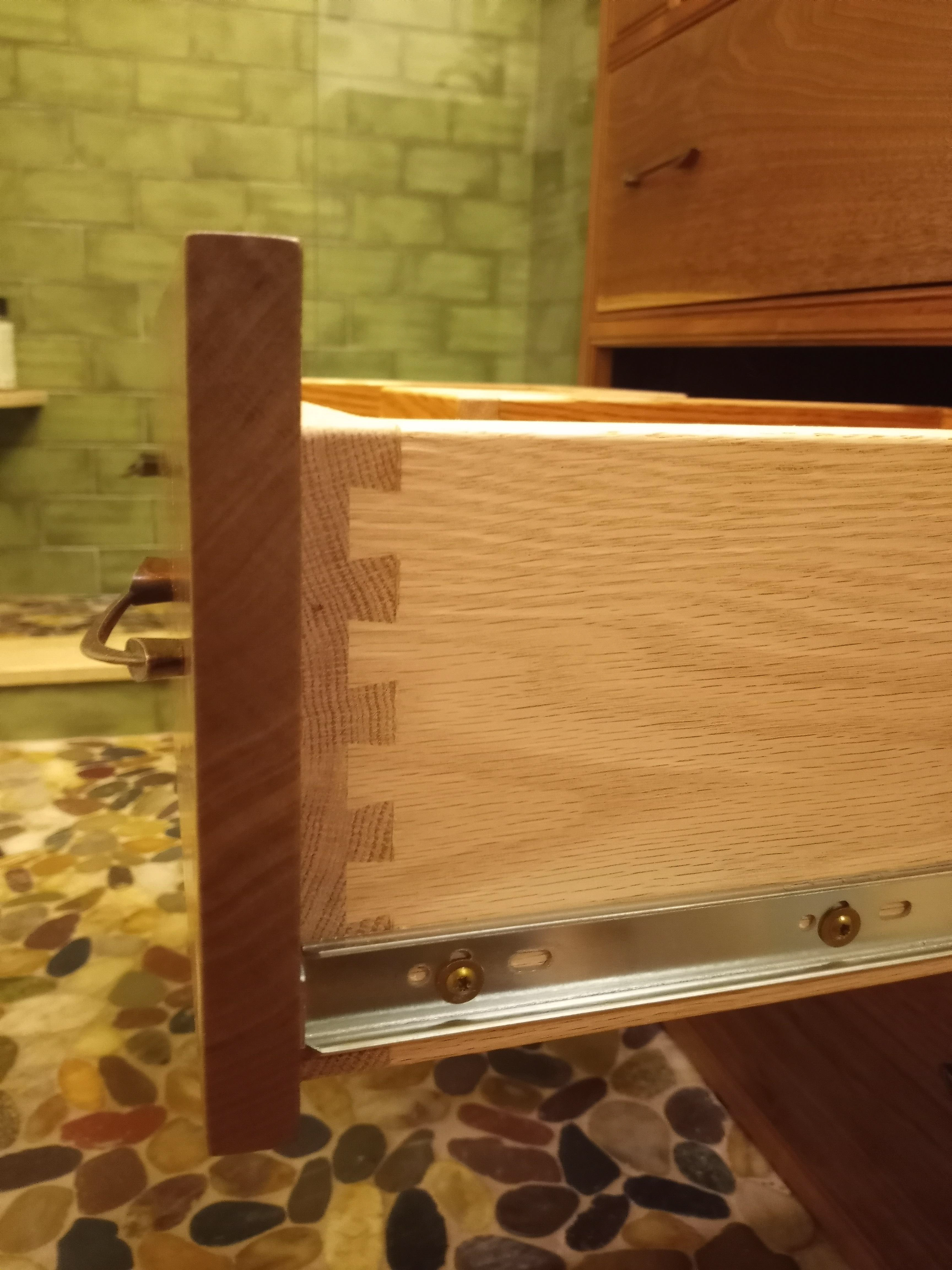
I've installed the drawer slides and applied the walnut fronts to the oak drawer boxes. The machined dovetails are quick to build once the jig is set up and they are very strong once they are glued together.
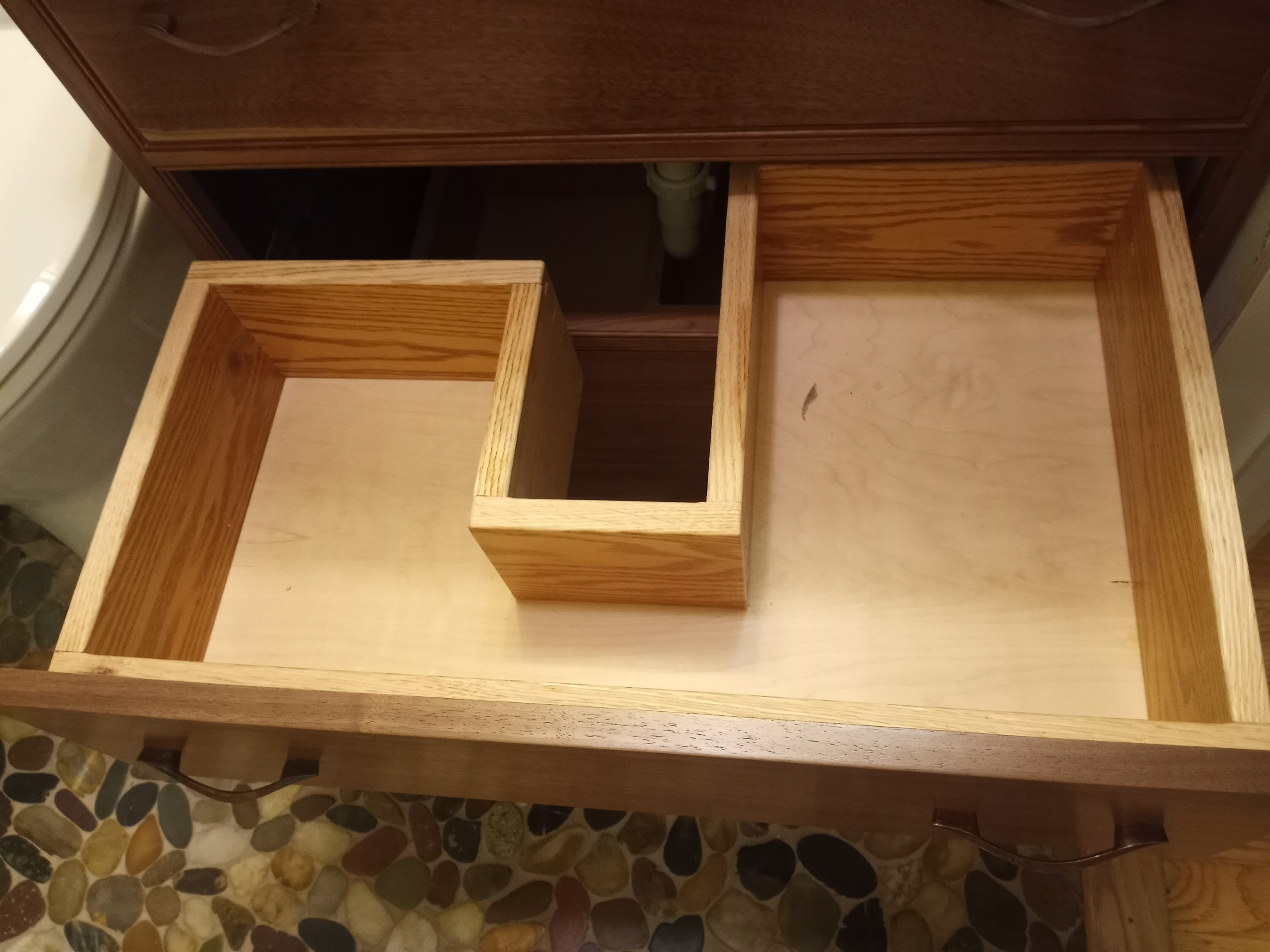
The 3 larger drawer boxes look a little odd but they are designed to maximize storage space around the water supply lines at the back left and the drain at the center.
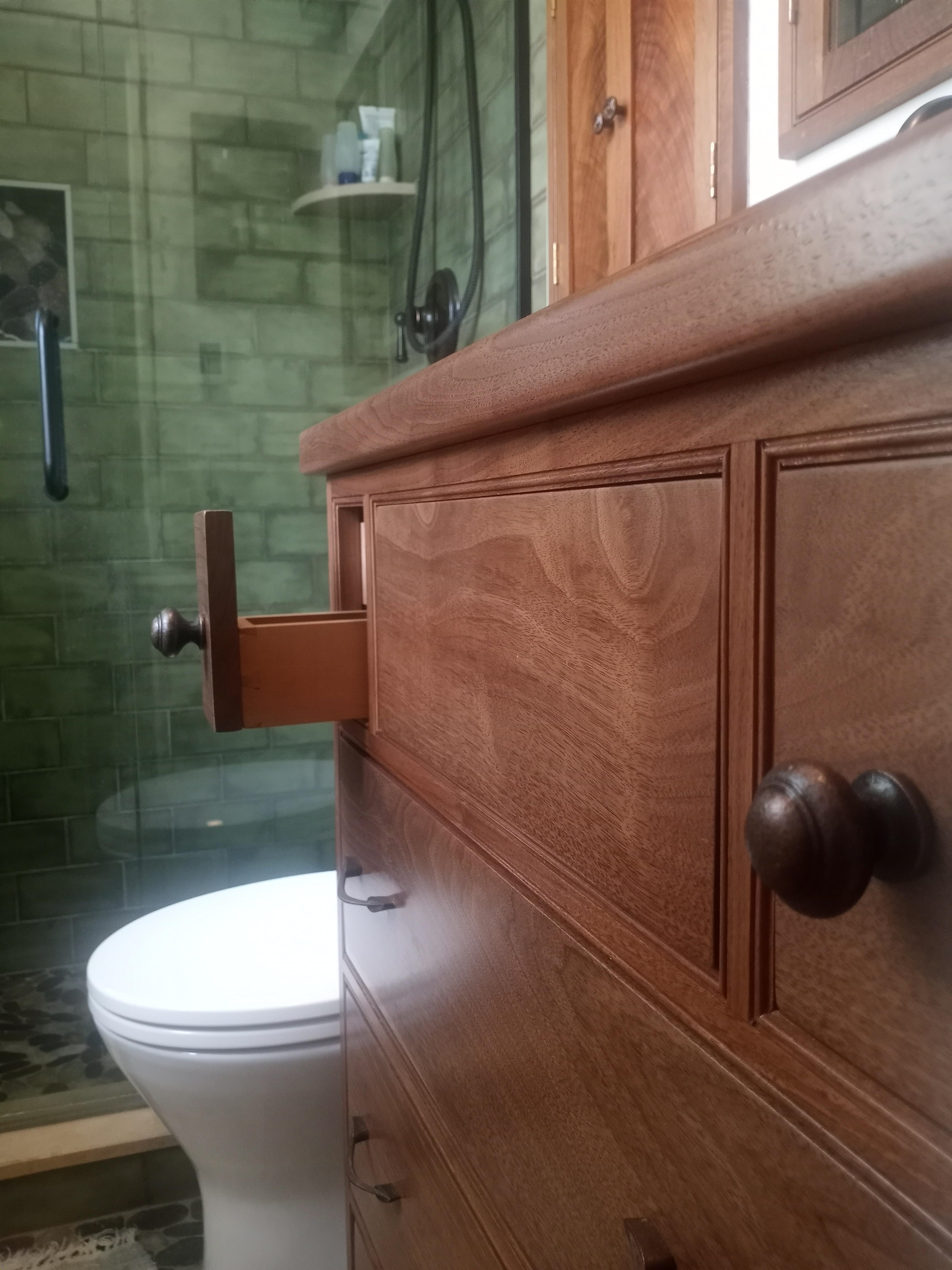
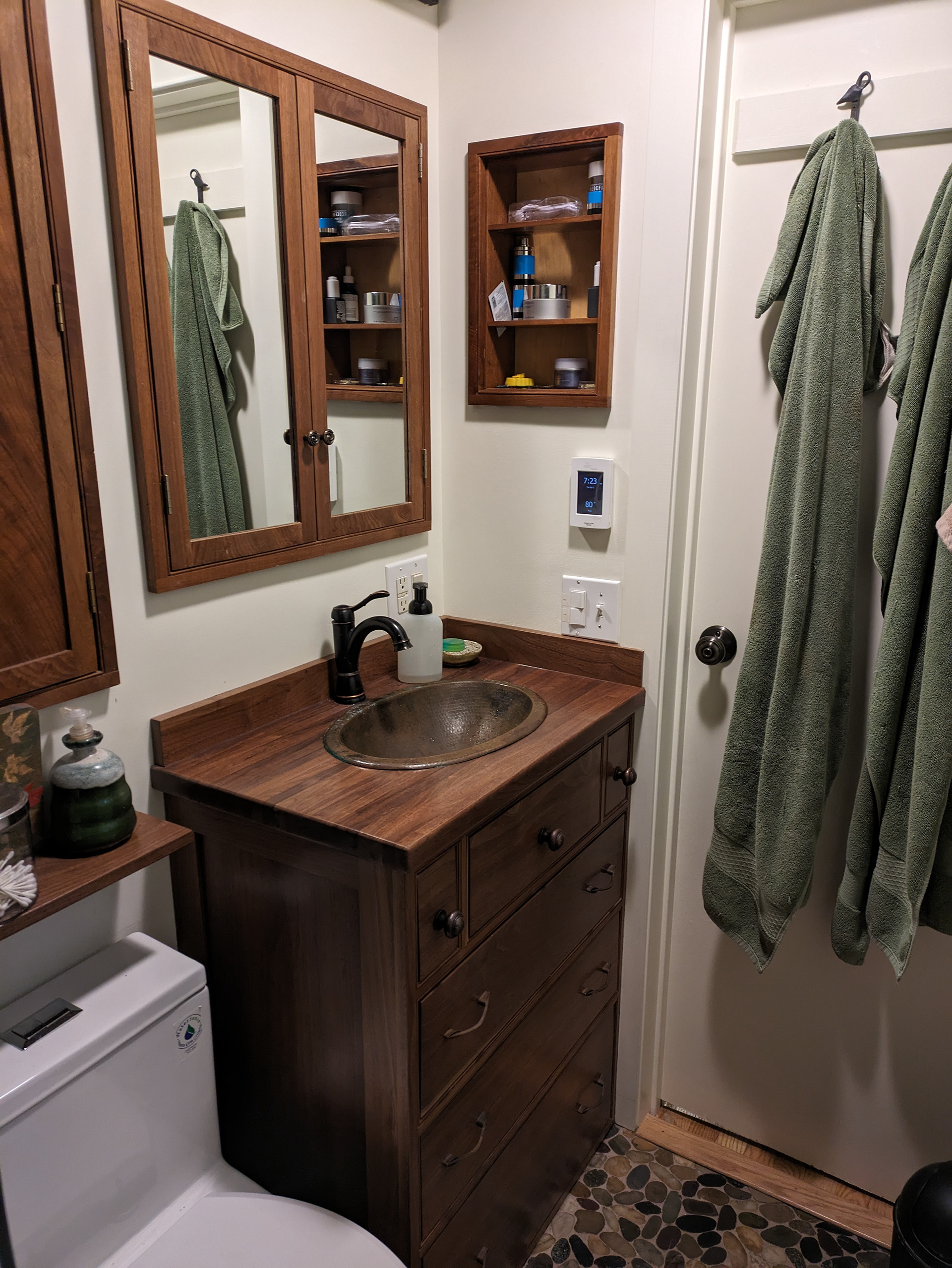
The copper sink basing and oil rubbed bronze faucet look really good with the walnut.
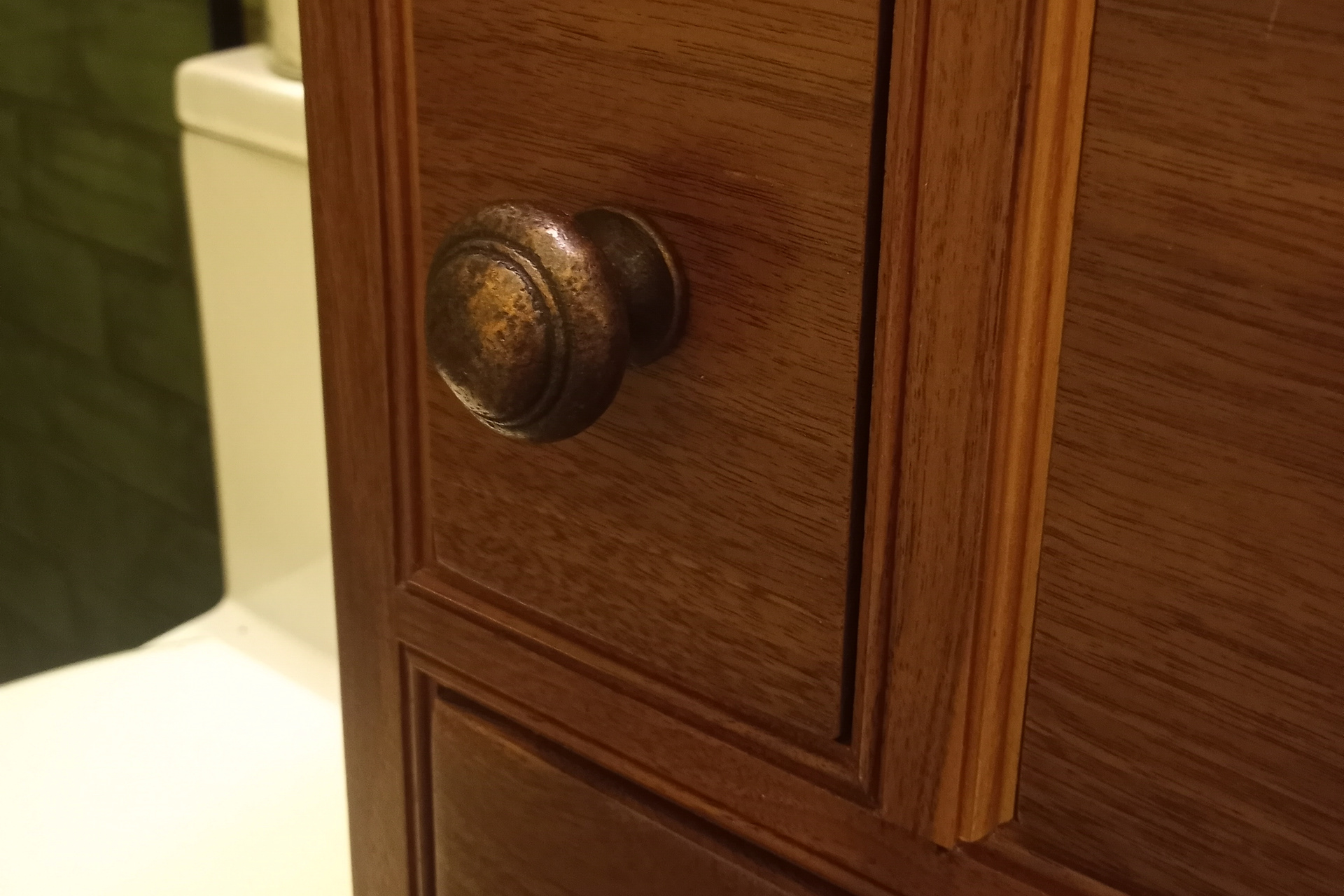
All of the drawer pulls are also copper.